Procurement Glossary
ABC analysis: definition & important aspects
The ABC analysis helps companies to use their resources efficiently and focus on the essentials. In this structured overview, you will learn how you can use this proven method to optimize your purchasing processes and achieve measurable cost savings.
ABC analysis in a nutshell:
The ABC analysis is a method for classifying articles or suppliers according to their economic importance in the categories A (very important), B (important) and C (less important). It enables Procurement to systematically prioritize resources and measures for optimal management of the procurement portfolio.
Example: An automotive supplier categorizes 1,000 items, with 20% of the items (A parts) accounting for 80% of the purchasing volume of EUR 10 million, 30% (B parts) a further 15% and the remaining 50% (C parts) representing only 5% of the volume.
Introduction to ABC analysis
ABC analysis is a key tool in the field of purchasing and materials management. It enables companies to systematically classify their products and services in order to develop an effective and efficient procurement strategy. By classifying products into categories A, B and C according to value and importance, purchasers can take targeted measures to optimize the supply chain, reduce costs and improve inventory management. This guide explains the basics of ABC analysis, presents practical application examples and discusses proven methods and supporting tools for successful implementation.
Definition and meaning of ABC analysis
ABC analysis is a method of classifying inventory management and services according to their value and importance to the company. It is based on the Pareto principle, which states that around 80% of the value comes from 20% of the items. In the ABC analysis, items are divided into three categories:
- Category A: High-value items that have the greatest impact on sales and profitability. They usually make up a small part of the total inventory, but require intensive management.
- Category B: Medium-value items that have a moderate impact. They lie between categories A and C in terms of value and importance.
- Category C: Low-value items that have the smallest impact. They make up the largest part of the inventory, but are less critical to the success of the business.
Key aspects of the ABC analysis:
- Value-based classification: Evaluation of items based on their turnover, profit or another relevant value measure.
- Cumulative distribution: Analysis of the cumulative values to determine the percentage distribution of the categories.
- Regular updating: Adjustment of the classification at regular intervals to take account of changes in the market and in the company.
- Integration into purchasing processes: Integration of the ABC analysis into the purchasing strategy and operational management of purchasing.
- Data quality: Ensuring the accuracy and timeliness of the underlying data for reliable classification.
Importance for Procurement:
ABC analysis enables buyers to use their resources efficiently by focusing on the most important items. By prioritizing, companies can ensure that the most valuable items are always available and optimally managed. At the same time, the analysis helps to store and procure less important items cost-effectively, which can reduce procurement costs. In addition, ABC analysis promotes a better overview and control of the entire inventory, which leads to improved decision-making and greater competitiveness.
ABC analysis: from classic classification to data-driven optimization
ABC analysis has long been a key tool for classifying materials and goods according to their economic importance for a company. It makes it possible to use resources efficiently and focus on the most important products. In today's dynamic business world with increasing complexity, however, the traditional method is reaching its limits. As a result, there is a growing need for modern approaches that take more comprehensive data into account and can react more flexibly to market analysis.
Old: Classic ABC analysis
Traditional approach:
In practice, the classic ABC analysis is often carried out by manually evaluating annual consumption values. Companies use simple spreadsheets or ERP reports to sort items according to their value share and classify them into A, B and C categories. The main features of this approach are its simplicity and focus on monetary value. However, this method does not take into account other relevant factors such as fluctuations in demand, delivery times or logistics costs. Manual processing is also time-consuming and prone to errors, which can lead to inaccurate classifications.
New: Data-Driven Inventory Optimization
Data-Driven Inventory Optimization:
The modern approach to inventory management uses advanced data analysis and technologies to enable a more comprehensive evaluation of materials. By incorporating real-time data, forecasted demand trends and supplier performance, products are dynamically classified. Machine learning and artificial intelligence identify patterns and trends that remain undetected in traditional ABC analysis. This data-driven process enables companies to optimize inventory levels, reduce excess stock and ensure the availability of critical items. Automated systems minimize manual effort and increase the accuracy of decisions.
Practical example: Increasing efficiency in retail through AI
A leading retailer implemented a data-driven inventory optimization solution to manage its stock levels more efficiently. By integrating real-time sales data, weather forecasts and social media, the company was able to forecast demand more accurately. Within six months, stock levels were reduced by 15%, while product availability increased by 10%. The automated analysis also identified slow-moving items, resulting in a 25% reduction in write-offs.
Conclusion: More efficient purchasing processes with the ABC analysis
The ABC analysis is an effective tool for strategically aligning Procurement and optimally utilizing resources. By prioritizing the most important goods, companies can reduce costs, increase efficiency and improve their competitiveness. Implement ABC analysis in your Procurement to make informed decisions and ensure sustainable success.
Summary of the ABC analysis
- A-goods: High value, low volume share
- B goods: medium value, medium volume share
- C-goods: Low value, high volume share
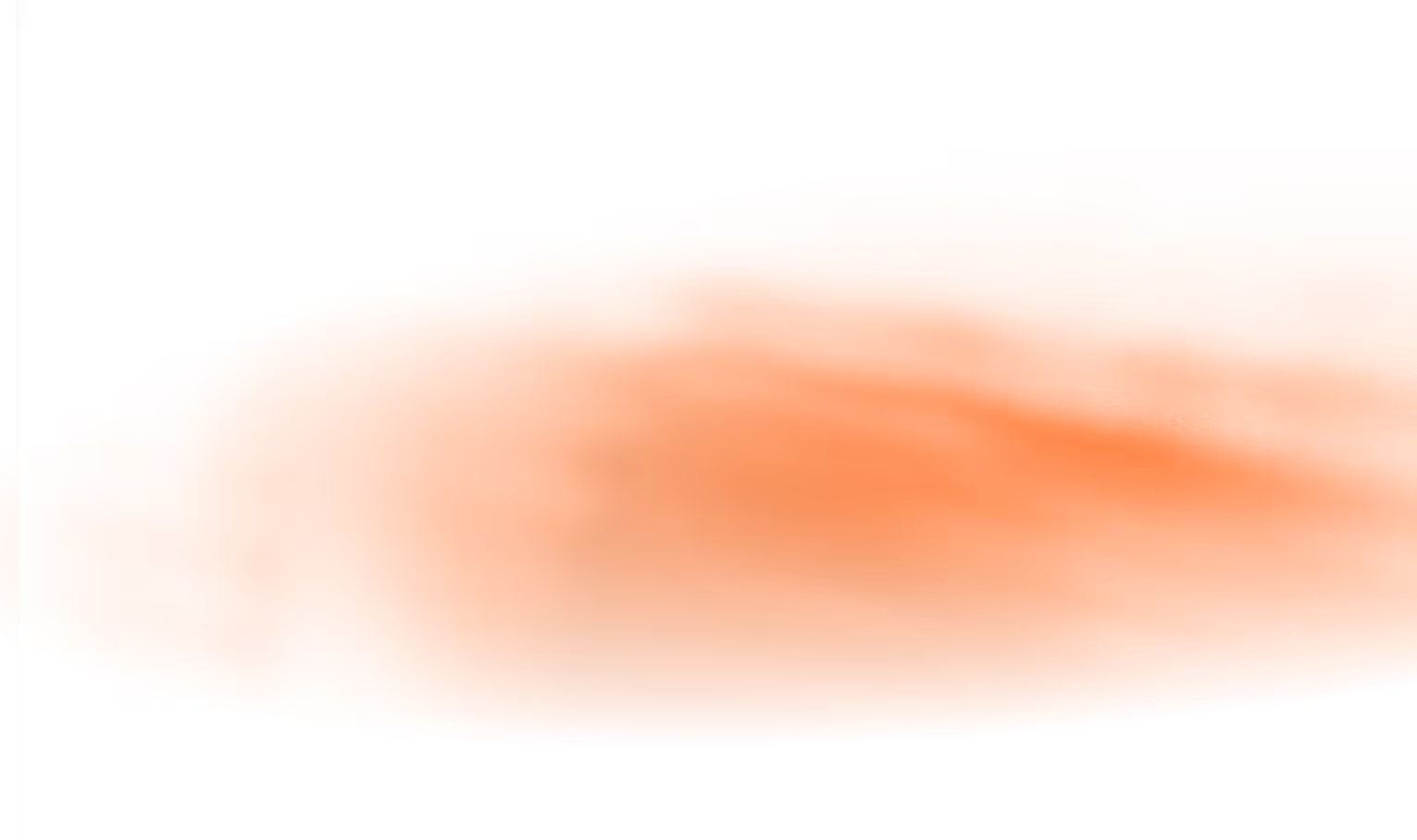
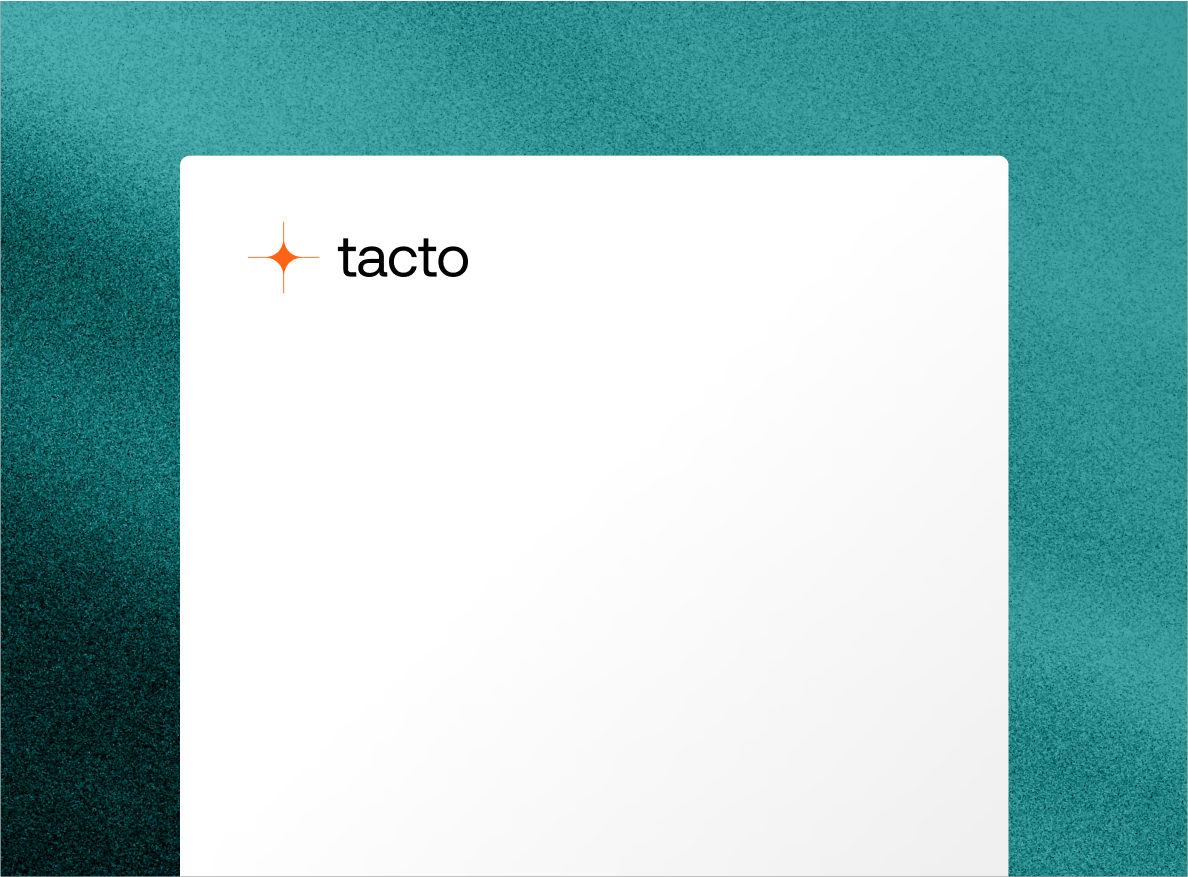