Procurement Glossary
Acceptance criteria: Definition and important aspects for buyers
Acceptance criteria create clarity and commitment between Procurement and suppliers and are therefore an indispensable tool for successful procurement projects. This structured overview shows you how you can ensure quality and avoid conflicts by using precise acceptance criteria.
Acceptance criteria in a nutshell:
Acceptance criteria are predefined, measurable quality characteristics and performance requirements that a product or service must fulfill in order to be accepted by the client. For Procurement , they form the contractual basis for the objective evaluation of supplier performance and protect against inferior or non-compliant deliveries.
Example: When procuring aluminum parts, an automotive supplier specifies the following acceptance criteria: material hardness 150±5 HB, surface roughness Ra ≤ 1.6 µm, dimensional accuracy ±0.02 mm and delivery reliability of at least 98% within a 3-day time window.
Acceptance criteria for {{name}}
Acceptance criteria are an essential part of quality management and project execution. They define measurable and verifiable conditions that must be met in order for a product, service or project result to be accepted by the client. These criteria form the basis for successful cooperation between client and contractor and ensure that the agreed requirements and quality standards are met. In this guide, you will learn how acceptance criteria can be effectively defined, documented and applied to ensure a smooth project flow and avoid potential conflicts.
What are acceptance criteria?
Acceptance criteria are specific requirements and conditions that a product or service must fulfill in order to be officially accepted and approved by the purchaser. They serve as binding guidelines for quality management in Procurement, functionality and performance of the procured goods. By clearly defining these criteria, it is ensured that both the supplier management and the buyer have a common understanding of the expected results.
Core elements of the acceptance criteria
- Technical specifications: Detailed description of the desired features and functions.
- Quality standards: Definition of standards and tolerances for product or service quality.
- Delivery conditions: Time frame, delivery locations and special delivery requirements.
- Test and inspection criteria: Methods for checking and validating the services provided.
Importance in Procurement
Acceptance criteria are crucial in the fulfillment process as they form the basis for the evaluation and acceptance of deliveries. They enable buyers to objectively measure supplier performance and ensure that the goods or services procured fulfill their intended purpose. Clearly defined acceptance criteria can minimize risks, reduce rework costs and increase internal stakeholder satisfaction.
- Quality assurance: Ensuring that products and services meet company standards.
- Contractual clarity: Avoidance of conflicts through clear expectations and obligations.
- Efficient processes: Acceleration of acceptance procedures through predefined criteria.
Acceptance criteria: From manual testing processes to Agile Acceptance Criteria
Based on the importance of acceptance criteria as an essential tool for quality assurance and compliance with contractual agreements, their practical implementation is of central importance for companies. Traditional methods are increasingly reaching their limits in the face of increasing demands for efficiency and flexibility. In order to meet the growing challenges, a transformation towards agile and digital approaches that enable faster and more precise acceptance is required.
Old: Manual acceptance criteria
Traditional approach:In traditional practice, acceptance criteria were often manual and paper-based. Quality checkswere carried out through physical inspections and the results were documented in the form of checklists and reports. Communication with supplier management was mainly via phone calls or emails, which could lead to delays and loss of information. The process was also time-consuming and resource-intensive, as each step had to be carried out and monitored manually by employees. This approach was prone to errors and offered little flexibility to respond to last-minute changes or problems.
New: Agile Acceptance Criteria
Agile Acceptance Criteria:The modern approach relies on agile methods and digital technologies to make the acceptance process more efficient. By using specialized software solutions, acceptance criteria can be defined centrally and made available to all parties involved in real time. Automated test procedures and data analyses enable continuous quality monitoring and an immediate response to deviations. Integrating suppliers into digital platforms improves communication and cooperation. Innovation-driven tools such as AI in Procurement support the prediction of potential problems and the optimization of processes. This leads to increased transparency, faster decision-making processes and an overall increase in product quality.
Practical example: Digital acceptance in mechanical engineering
A leading mechanical engineering company has revolutionized its acceptance processes by introducing Agile Acceptance Criteria. Acceptance criteria were digitally recorded and shared with suppliers using a cloud-based platform. Automated quality checks reduced inspection time by 35%. Real-time monitoring made it possible to identify deviations immediately and develop solutions together with the supplier. Improved collaboration reduced the error rate by 20% and delivery times were shortened by an average of 25%. These efficiency gains led to significant cost savings and increased customer satisfaction.
Conclusion on supplier evaluation
Acceptance criteria are an indispensable tool in modern Procurement, ensuring quality, efficiency and transparency in the supplier relationship. The clear definition and consistent review of these criteria minimizes risks and creates a solid foundation for successful procurement processes. With increasing digitalization, verification methods are evolving, opening up new opportunities for even more precise and efficient acceptance processes. The balance between thorough inspection and economic feasibility remains crucial.
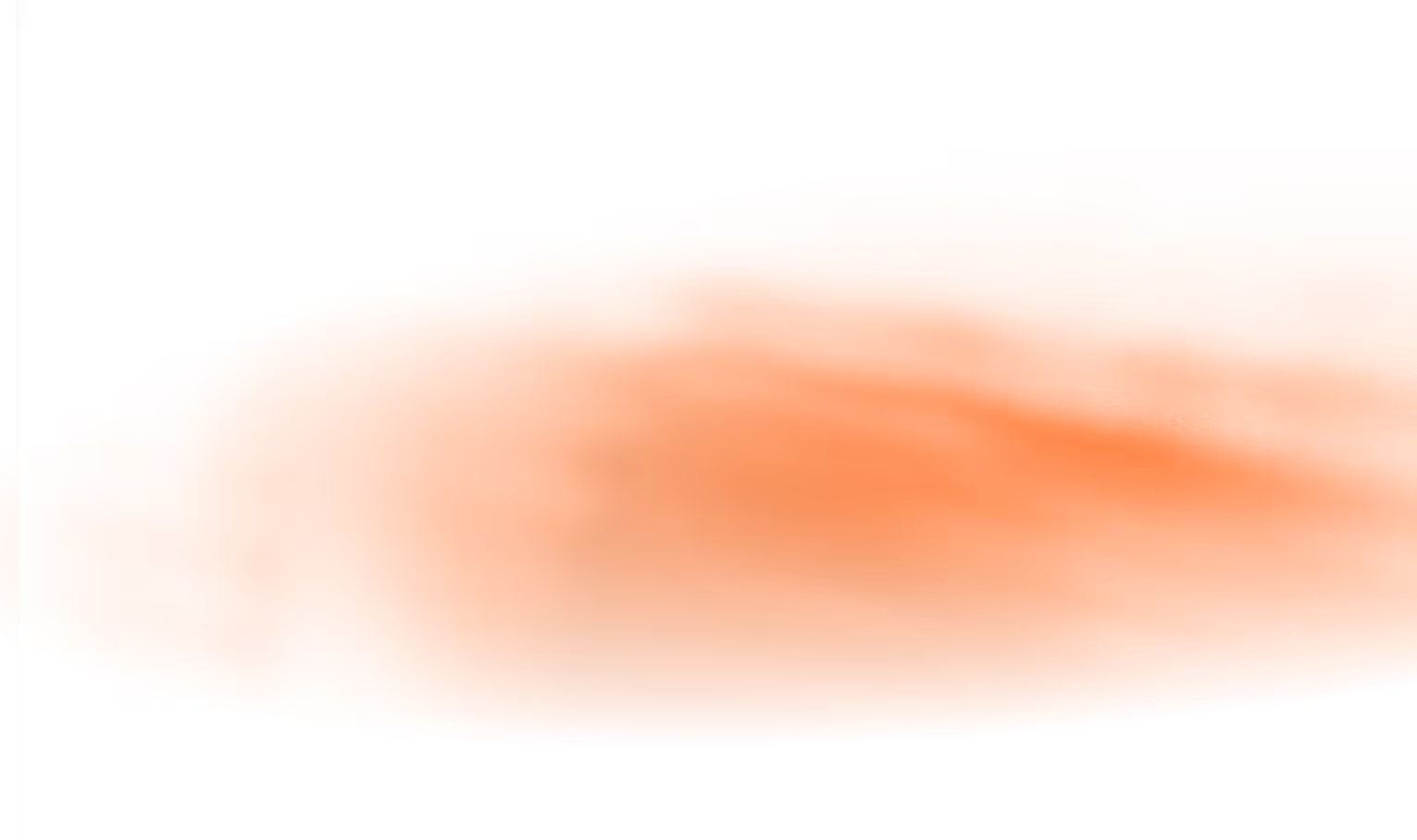
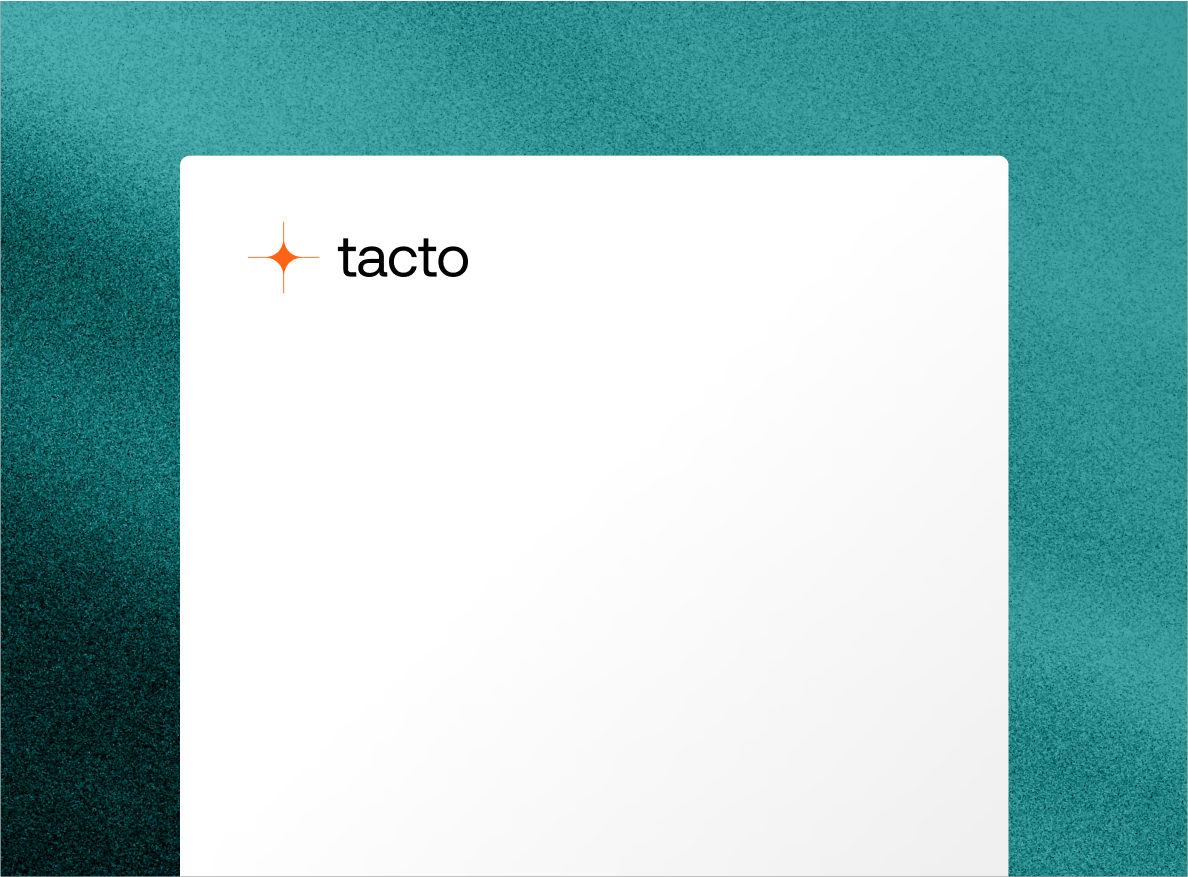