Procurement Glossary
Stockpiling strategy: definition and important aspects for buyers
In a world where supply chains are becoming increasingly complex and prone to disruption, the right stockpiling strategy can make the difference between a company's success and failure. The trick is to have neither too much nor too little in stock - because both can be expensive. Today, modern technologies and intelligent planning make it possible to master this balancing act and even save costs in the process.
What is a stockpiling strategy?
A stockpiling strategy is a systematic approach to planning and managing stock levels in companies. It aims to find the optimum balance between security of supply and storage costs. Factors such as demand, costs and availability are taken into account.
Stockpiling strategy: Efficient warehouse management for business success
In Procurement , the stockpiling strategy plays a central role in ensuring the supply of materials. It helps companies to avoid production downtime while keeping storage costs low. A good stockpiling strategy allows buyers to benefit from volume discounts and optimize relationships with suppliers. The integration of modern technologies such as Demand Driven MRP enables much more precise inventory control than traditional methods. Another advantage is the improved coordination between Procurement, production and sales.
Key problems when implementing a stockpiling strategy
- Fluctuating demand makes precise demand forecasts difficult
- High capital commitment due to excessive safety stocks
- Complex coordination between different departments
- Resistance to change when switching from old to new systems
- Technical challenges when integrating new tools
Implementation plan for a stockpiling strategy
1. analysis of the current situation
- Inventory of previous warehousing
- Identification of weak points
- Recording the most important key figures
2. strategy development
- Definition of clear goals
- Determination of safety stocks
- Selection of suitable tools and systems
3. preparation of the organization
- Employee training
- Adaptation of processes
- Building up the necessary know-how
4. step-by-step implementation
- Start with pilot project
- Continuous monitoring
- Customization if required
5. control and optimization
- Regular review of key figures
- Collection of feedback
- Continuous improvement
Stockpiling strategy: from safety stocks to demand-driven MRP
Building on the theoretical basis of the stockpiling strategy, effective inventory management in Procurement enables the continuous supply of materials and goods. In practice, it is crucial to find the balance between sufficient availability and minimal storage costs in order to avoid both supply bottlenecks and excessive inventories. In view of increasing market dynamics and the growing complexity of supply chains, there is a need to transform traditional approaches and integrate innovative methods.
Traditional approach: safety stocks and manual scheduling
The traditional stockpiling strategy was based on high safety stocks and manual planning. Companies kept considerable buffer stocks to compensate for uncertainties in demand and delivery times. The order quantity and timing were often determined on the basis of historical data and fixed minimum stock levels. Although this approach led to basic security in the supply of materials, it also resulted in high capital commitment, increased storage costs and the risk of obsolete stocks. In addition, the approach did not respond adequately to short-term market changes and fluctuations in demand.
New: Demand Driven MRP
The modern approach to stockpiling strategy is based on Demand Driven Material Requirements Planning (DDMRP). This method focuses on actual market analysis and dynamically manages stocks according to current requirements. By integrating real-time data, forecasting models and adaptive buffer stocks, companies can increase their responsiveness. The implementation of DDMRP makes it possible to reduce stock levels by up to 50%, minimize delivery times and increase service levels. At the same time, the digitalization and automation of inventory planning reduces manual errors and makes more efficient use of resources.
Conclusion on the stockpiling strategy
Today, a well-thought-out stockpiling strategy is essential for a company's success. It makes it possible to reduce costs and increase security of supply at the same time. The key to success lies in careful planning, the use of modern technologies and continuous adaptation to changing market conditions. Despite initial challenges during implementation, the long-term benefits clearly outweigh the costs.
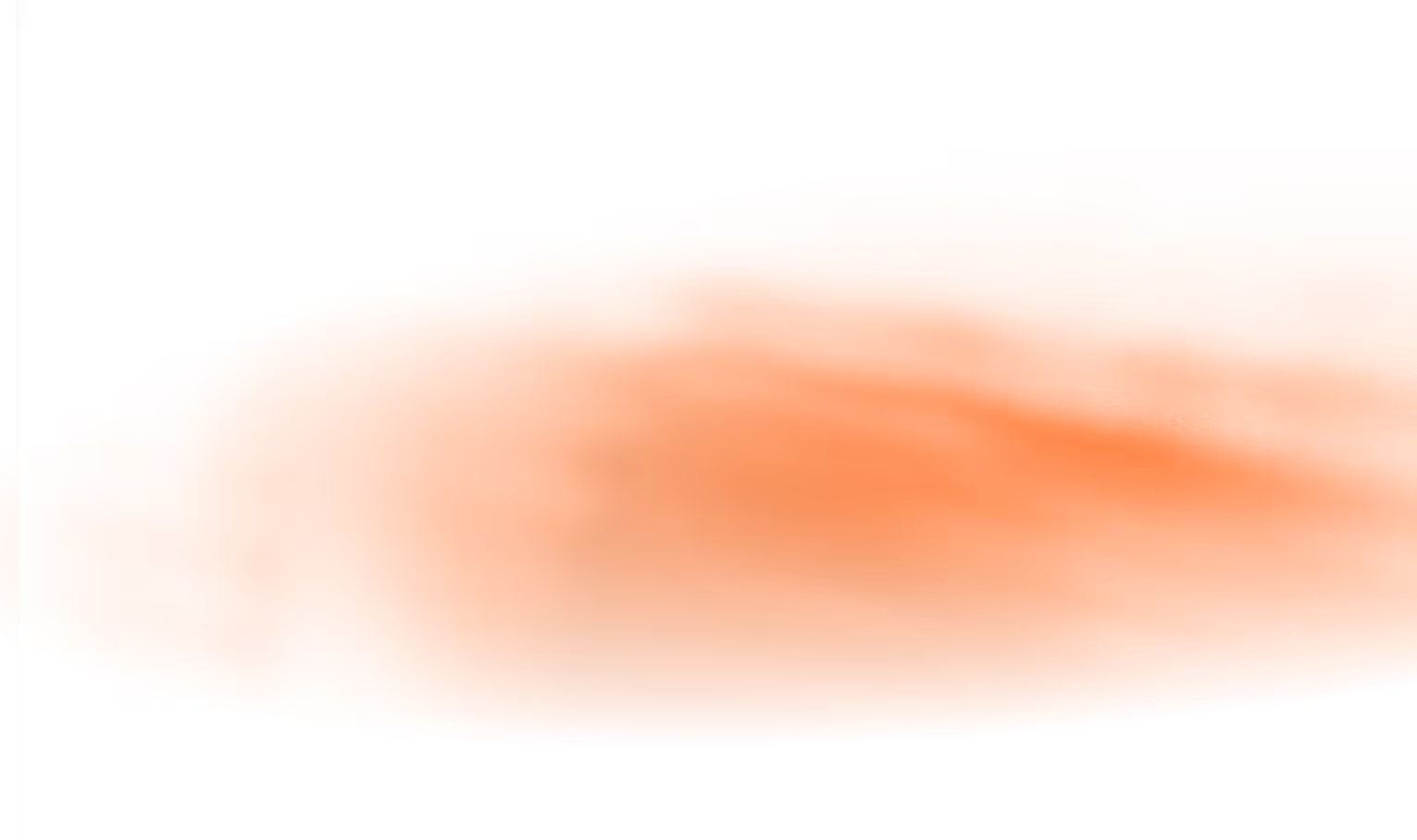
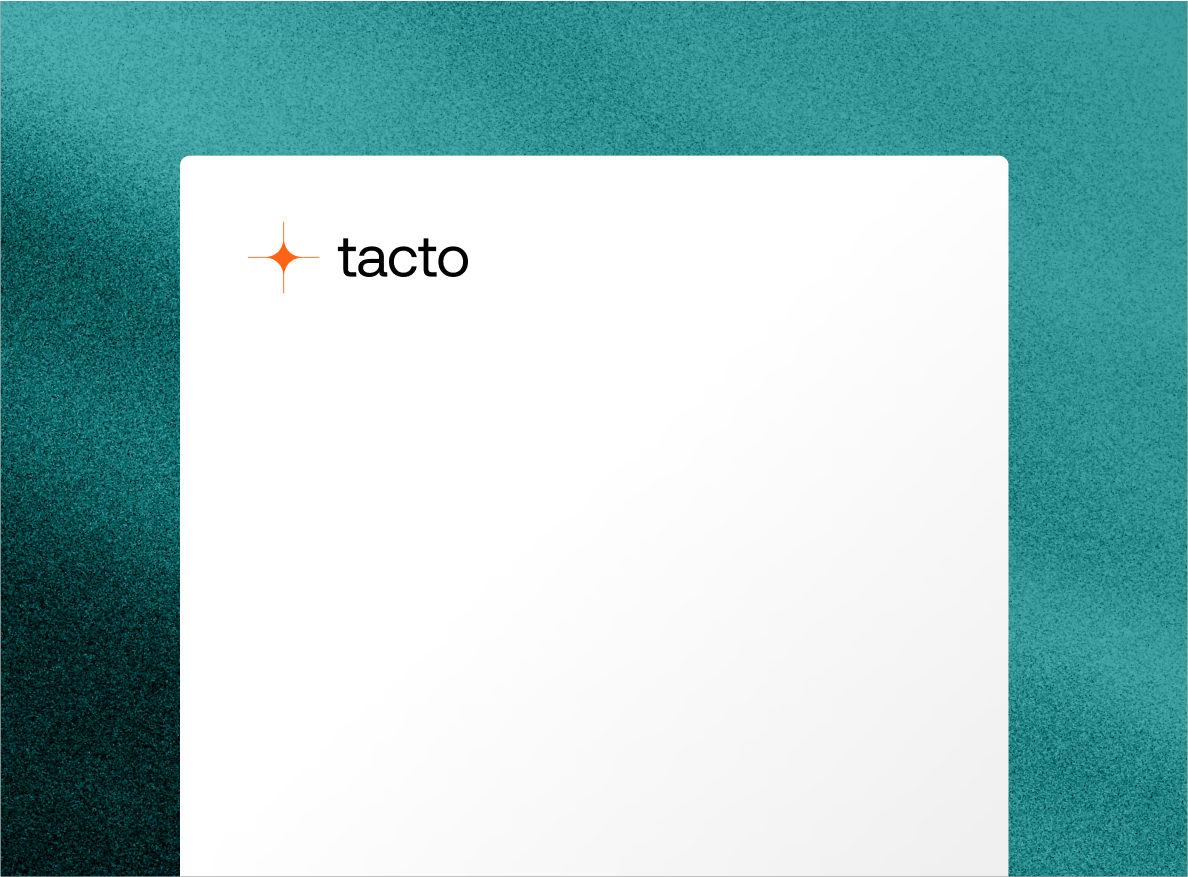