Procurement Glossary
Outsourcing analysis in strategic Procurement
The outsourcing analysis forms the decisive foundation for successful outsourcing decisions in Procurement and can generate considerable competitive advantages if carried out systematically. The methodical evaluation of in-house production versus outsourcing requires a structured approach that goes far beyond simple cost comparisons and integrates strategic, operational and risk-related factors.
What is an outsourcing analysis?
The outsourcing analysis is a systematic evaluation process for deciding whether company tasks or processes should be carried out internally or outsourced to external service providers. It includes a holistic view of strategic, operational, financial and risk-related factors and forms the basis for well-founded make-or-buy decisions in procurement. Essentially, this involves the following aspects:
- Evaluation of the economic efficiency of in-house versus external services
- Examination of the strategic relevance of the services under consideration
- Analysis of potential risks and dependencies
- Assessment of long-term effects on corporate competencies
Strategic importance of outsourcing analysis
The outsourcing analysis has developed from a purely cost-related instrument into a strategic tool in modern Procurement . It helps companies to optimize their vertical integration and focus on core competencies. By systematically analyzing outsourcing options, companies can not only realize cost advantages, but also increase their flexibility, promote innovation and achieve competitive advantages.
In the context of increasing market complexity and globalization, a well-founded outsourcing analysis ensures that strategic aspects are adequately taken into account. The decision to outsource certain services has far-reaching effects on the corporate structure, cost structure and long-term competitiveness. A detailed and methodical analysis is therefore essential in order to avoid wrong decisions and to support the company's strategic goals.
Evolution of the outsourcing analysis
The consideration of in-house production versus outsourcing has evolved over time and reflects changing economic conditions and company requirements.
Traditional approach vs. strategic approach
The traditional approach to outsourcing analysis primarily focused on short-term cost savings. Companies mainly outsourced peripheral, non-strategic tasks in order to conserve internal resources. This was characterized by simple contracts with clearly defined services, but without long-term commitment or strategic partnership. The main challenges were a lack of flexibility, low innovative strength and inadequate management of hidden costs.
The modern strategic approach, on the other hand, views outsourcing as part of the corporate strategy. Here, external service providers are deeply integrated into the company's value chain. The focus is not only on cost savings, but also on the joint achievement of corporate goals. Innovations such as agile contract management, joint development projects and the use of modern technologies enable more efficient processes and sustainable competitive advantages.
Phase model of the outsourcing analysis
A structured outsourcing analysis typically follows a multi-stage process that enables systematic decision-making. The following phase model provides a proven framework for conducting a comprehensive analysis:
- Phase 1: Identification of the need for action - strategic classification of the services to be analyzed, derivation of requirements and identification of the need for action
- Phase 2: Basic strategic decision - evaluation of strategic relevance, analysis of own competencies and identification of services that can in principle be outsourced
- Phase 3: Development of scenarios - process analysis, definition of performance parameters, review of in-house service alternatives and definition of possible outsourcing scopes
- Phase 4: Decision preparation - calls for tenders, obtaining offers, reference visits, development of cooperation scenarios and pre-selection
- Phase 5: Decision - cost-benefit analysis, profitability calculations, final decision and contractual arrangements
- Phase 6: Implementation and controlling - implementation, continuous monitoring and further development
This structured approach ensures that all relevant aspects are included in the decision-making process and enables an objective evaluation of the alternatives. It serves as a filter system to adequately take strategic aspects into account and to achieve clarity regarding the scope of outsourcing, the performance requirements and the possible design options.
Evaluation criteria in the outsourcing analysis
A comprehensive outsourcing analysis takes into account various dimensions that go far beyond a pure cost analysis. The following criteria should be included in the analysis:
Economic criteria
The economic evaluation is often the starting point for an outsourcing analysis, but should not be the sole criterion for the decision:
- Full cost accounting of internal service provision: Variable production costs, fixed cost allocation, capacity costs and opportunity costs
- Costs of external procurement: direct procurement costs, transaction costs (partner search, contract design, monitoring), interface costs
- Dynamic cost effects: One-off costs of the changeover (e.g. social plan costs), future ongoing costs, variabilization of fixed costs
- Volume-dependent cost degression effects: Optimal company size, capacity utilization effects, economies of scale through bundling with service providers
A common mistake in practice is the inadequate consideration of hidden costs and long-term cost effects. A reliable profitability calculation must compare all costs incurred by outsourcing with the costs actually incurred, whereby the time dimension (short, medium and long-term effects) must also be taken into account.
Strategic factors
The strategic dimension of the outsourcing analysis is crucial for the long-term competitiveness of the company:
- Core competence analysis: Analysis of whether the services in question belong to the company's core competencies or support them
- Strategic relevance: Evaluation of the contribution to competitive differentiation and the generation of customer benefits
- Innovation potential: assessment of whether higher innovation rates can be achieved through in-house or external services
- Market access: Improving market access through strategic partnerships with service providers
Focusing on core competencies is a key strategic argument for outsourcing. Companies should concentrate on activities that represent special competencies, offer differentiation potential and create special customer benefits. Services that do not meet these criteria are potential candidates for outsourcing from a strategic perspective.
Risk factors
Systematic risk analysis is an indispensable part of every outsourcing decision:
- Dependency risks: Evaluation of supplier power, risk of price increases, alternatives on the market
- Know-how risks: Risk of knowledge drain, long-term loss of core competencies
- Quality risks: Ensuring quality standards, rework costs
- Supply risks: Delivery reliability, flexibility in the event of fluctuations in demand, response time
- Reputational risks: Effects on the corporate image, especially in customer-related processes
A well-known example of supply risks is the production stoppage at Ford in 1998 due to a lack of door locks. This event illustrates the potential risks of excessive dependence on external suppliers and underlines the importance of comprehensive risk management as part of the outsourcing analysis.
Operational factors
The operational aspects influence day-to-day collaboration and the efficiency of processes:
- Flexibility: adaptability to fluctuations in demand, responsiveness to market changes
- Delivery times: Time-adequate availability of the required services
- Interface management: integration of external services into in-house processes
- Controllability: possibilities of influence and control
Taking dynamic market developments into account is particularly important here. For example, increasing demand can lead to longer delivery times for external service providers, which can have a negative impact on the availability of the required services. These factors must be compared with the capacity utilization situation of the company's own production.
Implementation of a make-or-buy mechanism
The establishment of a structured make-or-buy mechanism enables systematic and consistent decision-making regarding in-house services or external procurement. Such a mechanism ensures that decisions are made on the basis of objective criteria and are not influenced by subjective assessments or prejudices.
Implementation typically involves the following steps:
- Definition of relevant evaluation criteria: Determination of the relevant factors for the company, taking into account economic, strategic, operational and risk-related aspects
- Weighting of the criteria: Prioritization of the factors according to their importance for the company
- Development of an evaluation scheme: creation of a scoring model for the systematic evaluation of alternatives
- Institutionalization of the process: Anchoring the make-or-buy mechanism in the company processes, ideally in controlling
- Regular review and adjustment: Continuous evaluation and further development of the mechanism
The institutional anchoring of the make-or-buy mechanism in controlling ensures acceptance by all parties involved and guarantees consistent application across different areas and time periods.
Case study: outsourcing analysis in the manufacturing industry
A medium-sized manufacturing company was faced with the decision to outsource the production of certain components. The systematic outsourcing analysis comprised the following steps:
Initial situation and objectives
The company had previously produced all components itself, but was faced with rising costs and capacity bottlenecks. The aim was to improve profitability and free up resources for more strategically important tasks by potentially outsourcing certain non-core components.
Procedure and analysis
First, Controlling determined a comparative hourly rate that compared the internal production costs (variable production costs plus fixed cost allocation) with the external procurement costs (variable production costs of the supplier, its overhead cost allocation and transaction costs).
Further criteria were then included in the analysis:
- Strategic relevance: Evaluation of the contribution of the components to value creation and differentiation
- Flexibility: Evaluation of delivery times and responsiveness to fluctuations in demand
- Dependency risk: analysis of supplier power and alternative sources of supply
- Quality aspects: Assessment of the expected quality of externally sourced components
Results and implementation
Based on the comprehensive analysis, the company decided to outsource certain standardized components with low strategic relevance. In-house production was retained for components with high strategic importance or critical quality requirements.
The results were reflected in particular in optimized coordination and cooperation between the Procurement and Production departments. By taking a wide range of criteria into account, risks were minimized and greater planning reliability was achieved. After one year, costs for outsourced components were reduced by 15% and productivity in the strategic production areas increased by 20%.
Case study: Strategic outsourcing in IT infrastructure
A multinational company carried out an outsourcing analysis for its IT infrastructure in order to modernize and optimize its systems.
Initial situation and objectives
The company had been operating its IT infrastructure internally for years, but was faced with rising costs, outdated technology and an increasing shortage of skilled workers. The aim of the outsourcing analysis was to improve efficiency, secure access to innovative technologies and relieve the IT department of routine tasks.
Procedure and analysis
The following aspects were examined in detail as part of the outsourcing analysis:
- Profitability analysis: comparison of internal operating costs (hardware, software, personnel, energy) with the costs of various cloud solutions and managed services
- Strategic assessment: Analysis of the extent to which IT operations are part of the company's core competencies
- Technological perspective: Evaluation of access to innovative technologies and expert knowledge by external service providers
- Risk assessment: analysis of data protection and security risks, dependency risks and possible effects on existing processes
Results and implementation
Based on the comprehensive analysis, the company decided to strategically outsource its IT infrastructure to a leading technology provider. The strategic partnership enabled the company to migrate its systems to the cloud within six months. This led to a cost reduction of 25% and an increase in system availability to 99.9%. In addition, access to innovative technologies enabled a faster response to market requirements and significantly improved global communication processes.
The release of internal IT resources for strategic projects and innovations was particularly valuable, which strengthened the company's competitiveness in the long term. The systematic outsourcing analysis ensured that all relevant factors were taken into account and a well-founded decision could be made.
Digitization of the outsourcing analysis
Digitalization opens up new possibilities for more efficient and precise implementation of outsourcing analyses. Modern SRM systems and specialized analysis tools support the decision-making process and improve data quality and availability.
Digital tools to support the outsourcing analysis
The following digital solutions can significantly improve the analysis process:
- Data analysis tools: Enable the evaluation of large amounts of data to identify cost structures and optimization potentials
- Simulation tools: Allow the modeling of different scenarios and the evaluation of their impact
- Market analysis platforms: Provide insights into market developments, supplier landscapes and pricing structures
- Collaborative sourcing platforms: Support collaboration between internal stakeholders and external partners
- AI-based decision support: analyzes complex correlations and provides data-based recommendations
Integration into SRM systems
The integration of outsourcing analysis into existing SRM systems offers considerable advantages:
- Data consistency: use of a uniform database for all decisions
- Process integration: Seamless integration of the analysis into the procurement process
- Automation: Reduction of manual activities and sources of error
- Transparency: Improved overview of decisions and their basis
- Compliance: Ensuring adherence to defined processes and criteria
By digitally transforming outsourcing analysis, companies can not only increase the efficiency of the process, but also improve the quality of decisions. The automated collection and analysis of relevant data enables a more objective evaluation of alternatives and reduces subjective influences.
Challenges and best practices
Conducting an effective outsourcing analysis is associated with various challenges for which there are proven solutions:
Typical challenges
- Insufficient data basis: Missing or inaccurate cost information makes a well-founded assessment difficult
- Short-term thinking: focus on short-term cost savings without considering long-term effects
- Resistance within the organization: concerns about job security and loss of control
- Complexity of the assessment: difficulty in adequately considering qualitative factors
- Interface problems: challenges when integrating external services into existing processes
Best practices for successful outsourcing analyses
- Holistic approach: consideration of all relevant dimensions (economic, strategic, operational)
- Long-term perspective: inclusion of medium and long-term effects in the assessment
- Stakeholder involvement: Early involvement of all affected areas
- Transparent criteria: Clear definition and communication of the evaluation criteria
- Continuous review: regular evaluation of decisions made
- Pilot projects: Test implementation for selected services before large-scale implementation
The successful implementation of an outsourcing analysis requires a structured approach and the consideration of all relevant factors. It is particularly important to involve all affected stakeholders in order to utilize their expertise and address resistance at an early stage.
Conclusion and recommendations for action
The outsourcing analysis is an essential tool in strategic Procurement that goes far beyond a simple cost comparison. A well-founded analysis takes into account economic, strategic, operational and risk-related factors and enables a holistic evaluation of the alternatives. The implementation of a structured make-or-buy mechanism supports systematic decision-making and ensures that all relevant aspects are taken into account. Increasing digitalization is opening up new opportunities to improve the efficiency and quality of outsourcing analysis.
We recommend the following measures for the successful implementation of a systematic outsourcing analysis:
- Establish a structured decision-making process with clearly defined phases and responsibilities
- Develop a comprehensive catalog of criteria that covers all relevant dimensions and is adapted to the specific requirements of your company
- Integrate outsourcing analysis into your digital procurement processes to ensure efficiency, transparency and consistency
- Train your employees in the application of the analysis methods and the interpretation of the results
- Establish a monitoring process that continuously checks the results of decisions made and enables adjustments to be made
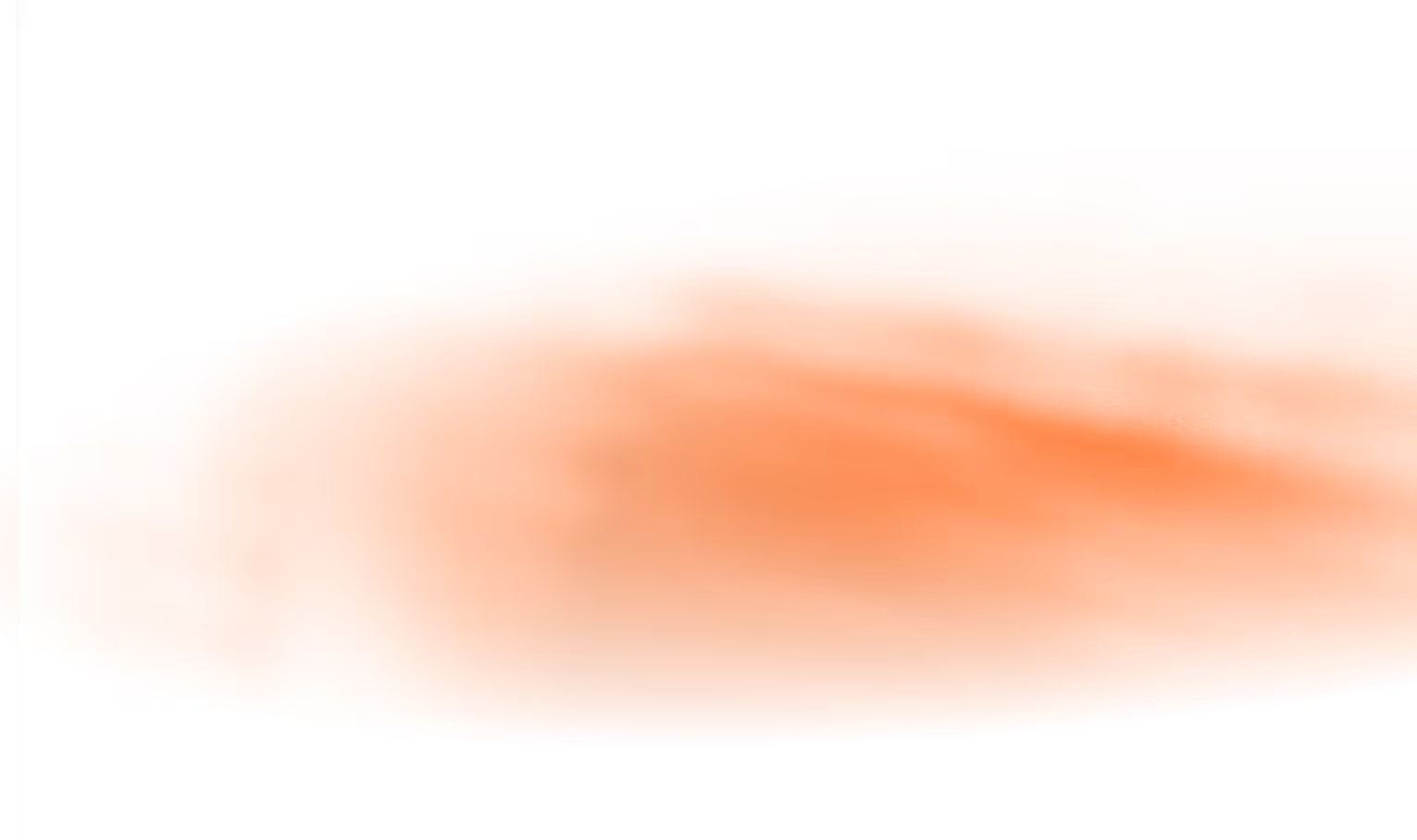
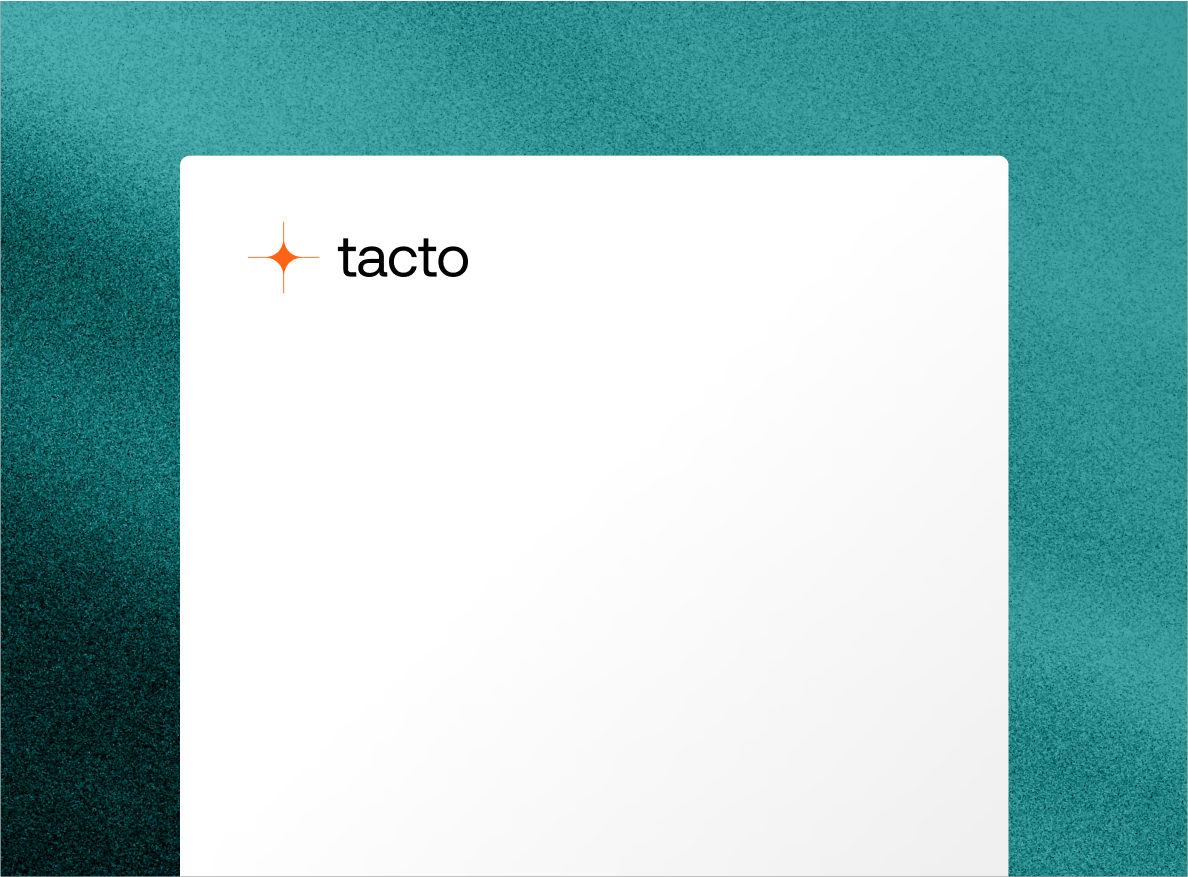