Procurement Glossary
Container sizes: Definition & important aspects for buyers
The right choice of container sizes has a decisive impact on storage costs, ordering costs and efficiency in Procurement. This structured overview shows you the most important decision criteria and helps you to find the optimum balance between costs and handling.
Container sizes in a nutshell:
Package sizes refer to the smallest packaging or order unit of a product offered by the supplier. For Procurement , the knowledge and optimization of container sizes is essential for efficient warehousing, cost minimization and needs-based procurement.
Example: A chemical company purchases a solvent in 200-liter drums as standard, but can negotiate with the supplier to agree a smaller container size of 50-liter canisters, thereby reducing storage costs by 30% while improving handling at the same time.
Container sizes in purchasing controlling
In modern logistics and retail, pack sizes play an important role in the efficient design of packaging and transportation processes. They describe the quantity or number of individual products that are combined in a packaging unit. The right choice of pack size has a decisive influence on costs, storage and distribution of goods. In this guide, you will learn which factors need to be taken into account when determining pack sizes and how you can optimize them for your company. Both economic and practical aspects that are relevant for an efficient supply chain are highlighted.
What are container sizes?
Pack sizes refer to the defined packaging units or quantities in which goods are delivered, stored and sold. They determine how many individual items are contained in a packaging unit and play a decisive role in procurement logistics and inventory management. Typical examples are pallets, boxes, sacks or bottles, each of which contains a certain number or quantity of a product.
Core elements of container sizes
Importance of container sizes in Procurement
In the procurement process, container sizes play a key role in the efficiency of the supply chain. By selecting suitable container sizes, buyers can reduce storage costs, optimize transport routes and improve the flow of materials. Container sizes also influence pricing, as larger quantities often lead to lower unit costs. Strategic planning of container sizes therefore makes a significant contribution to saving costs and increasing competitiveness.
Package sizes: From standard packaging to flexible packaging solutions
Based on the theoretical importance of container sizes in the procurement process, it becomes clear how crucial the right packaging unit is for the efficiency of the supply chain. Traditionally, companies have relied on standardized containers, which has often led to inefficiencies and increased costs. The increasing demand for flexibility and cost savings requires a transformation towards customized packaging solutions that adapt to individual needs.
Old: Standardized container sizes
Traditional approach: In traditional practice, goods were packaged and transported in fixed, standardized container sizes. Although this simplified production and logistics costs, it often meant that the packaging units were not optimally matched to actual requirements. Companies had to hold larger stocks to compensate for fluctuations, which led to increased storage costs and capital commitment. In addition, transport capacities could not be used efficiently as the fixed container sizes did not always allow for optimal capacity utilization. The inability to adapt to specific customer requirements was another obstacle, particularly in sectors with volatile demand.
New: Flexible packaging units
Customized packaging: Modern approaches focus on flexible and individually adapted pack sizes. By using advanced technologies and data analysis, packaging units can now be tailored precisely to requirements. This enables companies to optimize their stock levels and use means of transport more efficiently. The introduction of variable pack sizes not only reduces storage costs by up to 25%, but also improves responsiveness to market changes. In addition, these customized solutions contribute to sustainability by reducing packaging material and the ecological footprint.
Practical example: Automotive supplier relies on flexibility
A leading automotive supplier was faced with the challenge of reducing its storage costs and capital commitment. By switching from standardized pallets to flexible container sizes that were precisely tailored to the car manufacturer's production schedule, the company was able to reduce its stock levels by 30%. The optimized use of transport vehicles led to a 15% reduction in freight costs. In addition, the ability to adapt to short-term fluctuations in demand increased customer satisfaction and gave the supplier a competitive advantage.
Conclusion on container sizes
Packaging sizes are a key lever for cost savings and increased efficiency in Procurement. The optimal choice of packaging units not only enables direct cost savings through volume discounts, but also improves the entire supply chain through more efficient storage and transportation processes. Digital solutions and close supplier cooperation enable companies to continuously adapt their packaging sizes to changing requirements, taking into account both economic and sustainable aspects.
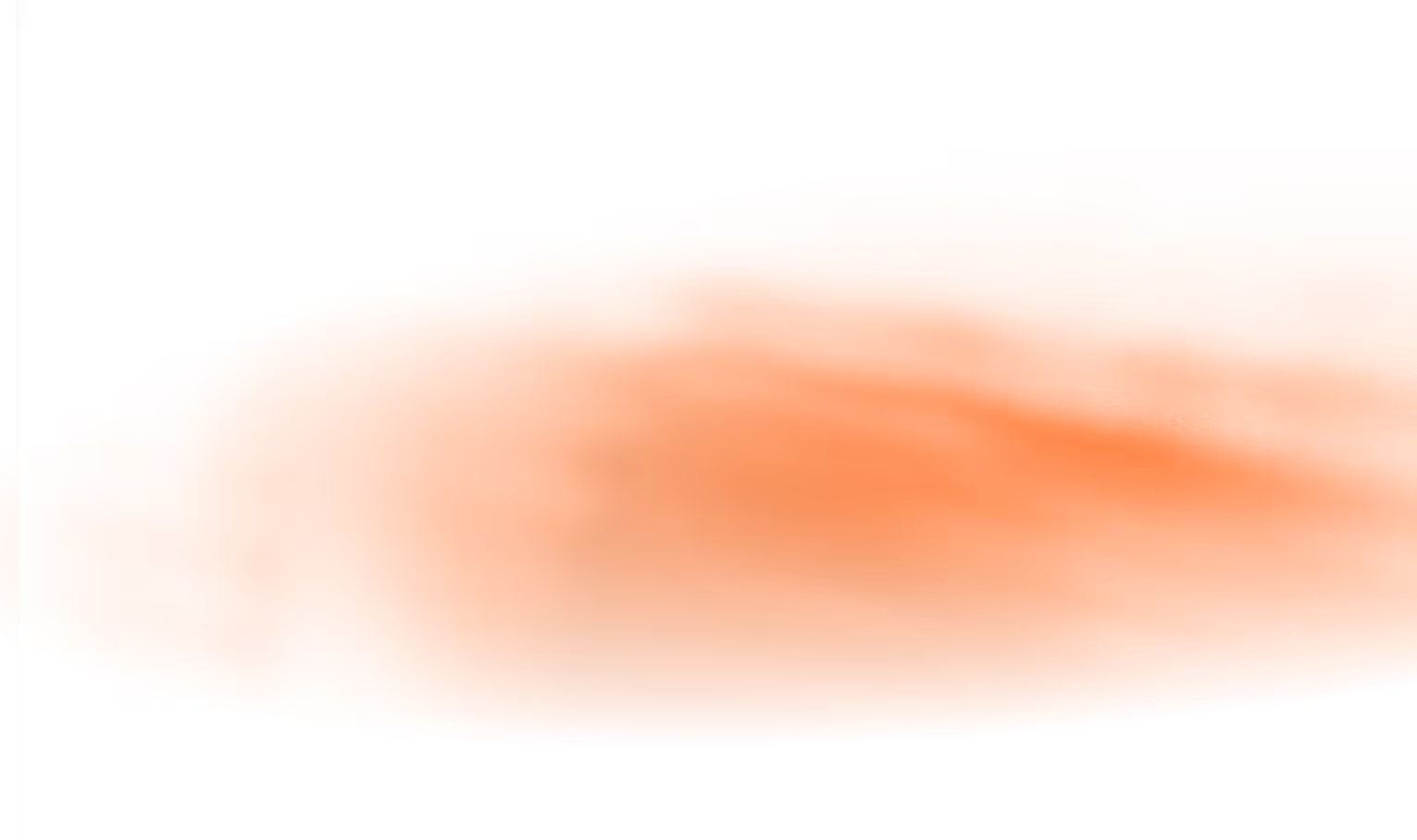
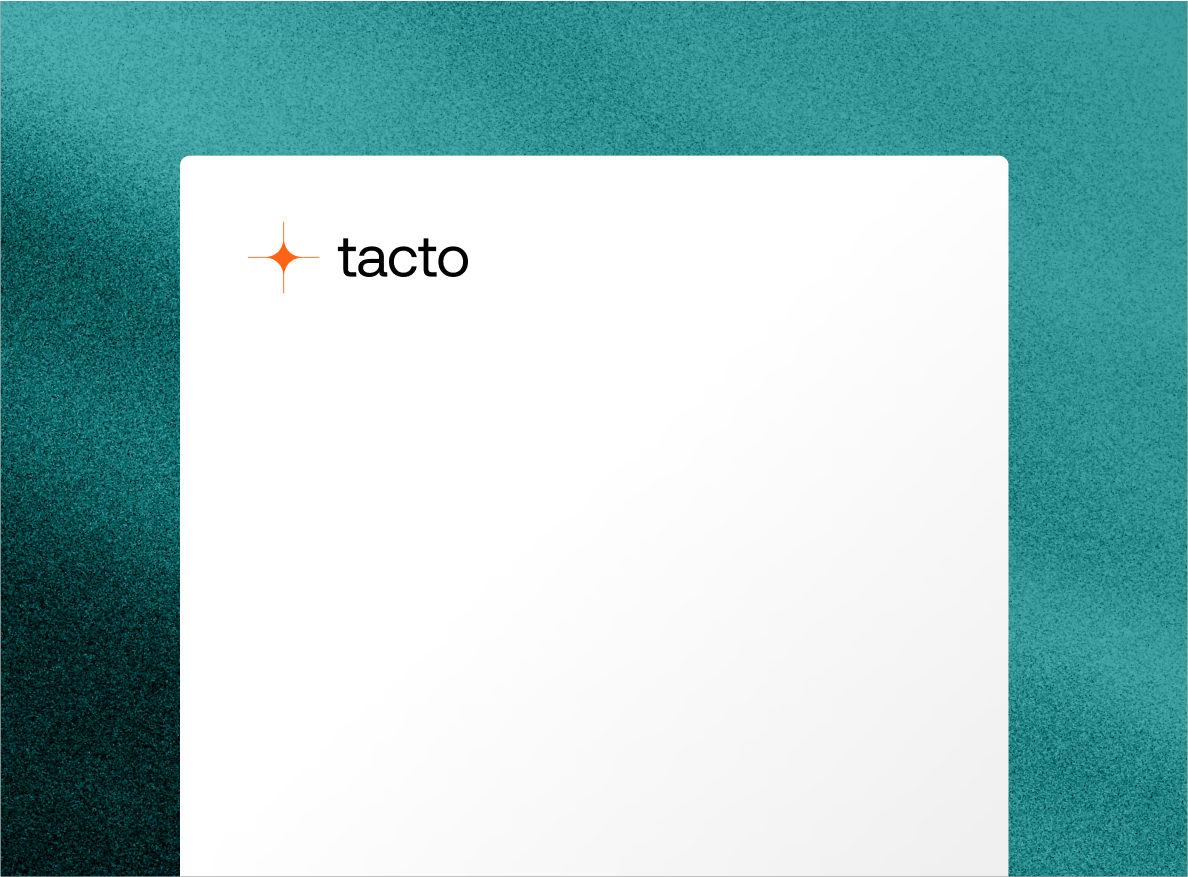