Procurement Glossary
Total cost accounting: definition & important aspects for buyers
Total cost accounting provides companies with a holistic view of all relevant costs of a procurement decision and prevents expensive misjudgements due to hidden follow-up costs. This structured overview shows you as a buyer how you can systematically determine the total cost of ownership and thus make better procurement decisions.
Total cost accounting in a nutshell:
Total cost accounting systematically records all direct and indirect costs associated with the procurement, use and disposal of a product or service. For Procurement , it is an essential tool for supplier selection and cost transparency, as it reveals hidden follow-up costs and enables genuine comparisons of profitability.
Example: When purchasing a production system for 250,000 euros, installation (15,000 euros), maintenance (8,000 euros/year), energy (12,000 euros/year) and disposal costs (20,000 euros) are taken into account in addition to the purchase price over the planned useful life of 10 years, resulting in total costs of 450,000 euros.
Total cost accounting in purchasing controlling
Total cost accounting is a fundamental instrument of corporate accounting and cost accounting. It provides companies with a comprehensive overview of all costs incurred within an accounting period. Unlike cost of sales accounting, it records all costs according to their nature and therefore represents an important basis for business decisions. In this introduction, we will highlight the key aspects of total cost accounting, explain its importance for corporate management and show how it can be used successfully in practice. Both the theoretical principles and practical application examples will be covered.
What is total cost accounting?
Total cost accounting is a business management method for recording and evaluating all costs incurred by a company over a certain period of time. It takes into account both fixed and variable costs and provides a comprehensive overview of the cost structure. The aim is to analyze the profitability of processes and products and make well-founded decisions to reduce costs and increase efficiency.
Core elements of total cost accounting
Relevance of total cost accounting in Procurement
In Procurement total cost accounting plays a decisive role in the evaluation of procurement decisions. By analyzing all costs incurred, buyers can identify hidden costs and reduce the TCO into account. This enables a holistic view of supplier selection and supports strategic decisions regarding supplier selection, price negotiations and long-term cooperation.
Total cost accounting: From pure acquisition costs to total cost of ownership (TCO)
Total cost accounting plays a decisive role in modern procurement. Whereas in the past the focus was primarily on the purchase price, today's complex business world requires a more holistic view of all costs incurred. Building on the theoretical basis outlined in the previous section, it is clear that a pure price orientation can lead to long-term disadvantages. The approach has therefore shifted from a traditional understanding of costs to a consideration of the total cost of ownership (TCO).
Old: Focus on acquisition costs
Traditional approach: In practice, the focus was on Procurement has long focused on minimizing immediate acquisition costs. Companies selected suppliers and products mainly on the basis of the lowest price in order to achieve short-term savings. Tools such as simple price comparisons and tenders were used to find the cheapest offer. However, this approach often neglected hidden costs such as maintenance, energy consumption or downtime. The lack of consideration of these factors often led to higher total cost of ownership and affected long-term profitability.
New: Total Cost of Ownership (TCO)
Total Cost of Ownership (TCO): The modern approach to total cost accounting goes beyond the purchase price and takes into account all costs incurred during the entire life cycle of a product or service. In practice, this means that companies use methods and tools to record and analyze costs for operation, maintenance, training, downtime and disposal. By using software solutions for cost-benefit analysis, detailed cost forecasts can be created. This provides companies with a sound basis for decision-making, leading to more sustainable procurement strategies and long-term cost savings.
Practical example: Implementation of TCO in the automotive industry
A leading automotive manufacturer was faced with the decision to purchase new industrial robots for its production line. While one supplier offered a lower purchase price, the company used TCO analysis to consider additional factors such as energy consumption, maintenance intervals and potential downtime. The analysis showed that the initially more expensive robot would reduce overall costs by 15% over a five-year period due to more efficient energy consumption and lower maintenance costs. By taking this comprehensive view, the manufacturer was able to significantly reduce its production costs and increase operational efficiency.
Conclusion on total cost accounting
Total cost accounting is an indispensable tool for strategic purchasing decisions. By taking into account all direct and indirect costs, it enables a holistic evaluation of procurement options. Despite initial challenges during implementation, it leads to optimized supplier relationships and sustainable cost savings. With increasing digitalization and the integration of sustainability aspects, its importance for successful supply chain management will continue to grow.
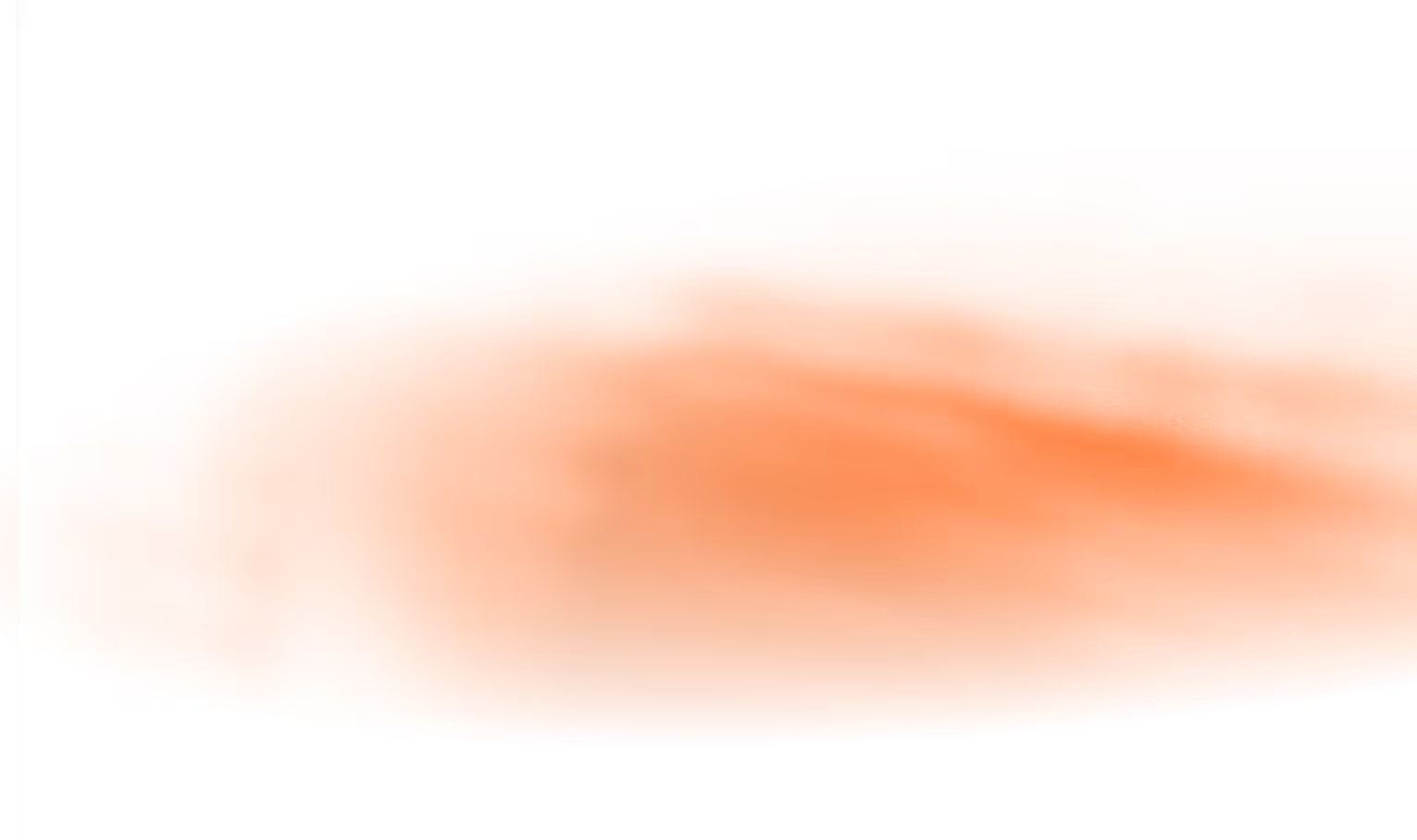