Procurement Glossary
Warehouse key figures: The key to optimizing purchasing processes
Warehouse KPIs are decisive control instruments in Procurement that not only make the profitability of warehousing measurable, but also enable strategic decisions to be made on cost reduction and inventory optimization; by systematically monitoring these KPIs, companies can reduce their capital commitment and at the same time ensure delivery readiness, as demonstrated by a medium-sized automotive supplier that was able to save over 400,000 euros annually through targeted optimization of its warehouse KPIs.
What are inventory ratios?
Warehouse key performance indicators, also known as warehouse KPIs, are business indicators that companies can use to monitor, evaluate and control the profitability of their warehousing. They quantify various aspects of warehouse performance, such as stock levels, inventory turnover, storage duration and service level, which means they serve as a basis for decision-making when optimizing procurement processes and the strategic orientation of purchasing.
- Stock-related key figures (e.g. average stock level, stock range)
- Process-related key figures (e.g. inventory turnover rate, picking performance)
- Cost-related key figures (e.g. storage costs per unit, capital commitment costs)
- Performance-related key figures (e.g. service level, readiness to deliver)
Importance of warehouse key figures in strategic Procurement
For buyers and procurement managers, inventory key figures are of central importance for managing and optimizing the entire supply chain. They provide an important decision-making basis for the design of procurement strategies and enable evidence-based supplier selection and negotiations.
In strategic Procurement , inventory ratios are used in particular to find the optimum balance between security of supply and capital commitment. While excessively high stock levels cause unnecessary costs, excessively low stock levels can lead to supply bottlenecks and production downtime. Procurement can make a significant contribution to a company's competitiveness by continuously analyzing and managing relevant inventory indicators.
Purchasing departments also use inventory key figures as a basis for make-or-buy decisions, for evaluating various procurement concepts such as just-in-time or consignment stock and for developing needs-based ordering cycles. They are therefore an indispensable tool for procurement controlling as a whole.
Classification and systematics of warehouse key figures
For effective warehouse controlling, it is important to systematically record and evaluate warehouse KPIs. Depending on the perspective and analysis objective, warehouse KPIs can be divided into different categories that shed light on different aspects of warehousing.
Categorization according to viewing perspective
- Absolute key figures: Directly quantifiable statuses such as total stock in euros or units, which serve as the basis for further calculations
- Relative key figures: Ratios with higher strategic expressiveness, such as inventory turnover rate or inventory range
- Time-related key figures: Metrics that measure time-related aspects of warehousing, such as storage duration or throughput times
- Key performance indicators: Indicators for the performance of warehouse processes, for example picking performance or picking error rate
ABC analysis as the basis for differentiated key figure management
An important basis for efficient work with warehouse KPIs is the ABC analysis, which classifies warehouse items according to their economic importance. This method helps to prioritize the effort for KPI management according to the relevance of the items:
- A-items: High-value, high-turnover products (approx. 20% of items, 80% of value) that require intensive and high-frequency monitoring using warehouse indicators
- B articles: Articles of medium importance (approx. 30% of the articles, 15% of the value) that require regular but less intensive key figure analysis
- C-articles: Low-value, low-turnover products (approx. 50% of items, 5% of value) for which a simplified key figure survey is sufficient
This differentiated view enables buyers to deploy their resources in a targeted manner and adapt the controlling effort to the actual economic benefit. For example, daily key figure analyses can be useful for A-items, while monthly or quarterly evaluations are sufficient for C-items.
The most important warehouse key figures for Procurement in detail
Certain warehouse KPIs are particularly relevant for purchasing professionals, as they allow direct conclusions to be drawn about the efficiency of procurement processes and reveal specific optimization potential. The key performance indicators that should not be missing from any purchasing controlling system are presented below.
Inventory-related key figures
- Average stock level: Indicates the average stock level within a defined period and forms the basis for many other calculations. The formula is: (opening stock + closing stock) / 2 for a rough calculation or (opening stock + sum of all monthly stocks) / (number of measurement times + 1) for a more precise calculation.
- Stock range: Shows how long the current stock would last if consumption remained constant. It is calculated as: (average stock level / average consumption per time unit). For example, a range of 30 days means that the current stock is sufficient for one month.
- Safety stock: The minimum stock held to protect against delays in delivery or unexpected peaks in demand. It is calculated based on factors such as delivery time, delivery reliability and fluctuations in demand.
Dynamic warehouse key figures
- Inventory turnover rate: Measures how often the average inventory is turned over within a period of time (usually one year). The formula is: cost of goods sold / average stock level. A higher inventory turnover rate indicates more efficient warehousing, as the tied-up capital is released more quickly.
- Storage duration: Indicates how long items remain in the warehouse on average before they are further processed or sold. It is calculated as: 365 days / inventory turnover rate. A short storage period is generally desirable, but must always be considered in the context of security of supply.
- Cost of goods sold: Shows the quantity of goods actually consumed or sold in a specific period. The calculation is based on the formula: (opening stock + receipts) - closing stock.
Cost and performance indicators
- Storage costs per unit: Determines the average costs per stored unit and includes space, personnel, energy and insurance costs as well as costs for storage technology. It is calculated as: Total storage costs / number of units stored.
- Capital commitment costs: Quantifies the opportunity costs of the capital tied up in inventory. The formula is: average inventory in euros × discount rate. A company with an average inventory of 1 million euros and an interest rate of 8% has annual capital commitment costs of 80,000 euros.
- Service level: Measures the warehouse's ability to serve customer orders or internal requirements on time and in full. It is calculated as: (number of orders fulfilled on time and in full / total number of orders) × 100%.
Process-related key figures
- Picking performance: Indicates the number of items or units picked per time unit (usually per hour) and is an important indicator of the efficiency of warehouse processes.
- Picking error rate: Measures the proportion of incorrect picks in the total number of picking processes. A low error rate is a sign of high-quality warehouse processes.
- Loading dock occupancy: Calculates the utilization of incoming and outgoing goods capacities and helps to identify bottlenecks or inefficient processes.
Key stock figures in the procurement strategy
The systematic analysis of inventory key figures provides valuable insights for the development and optimization of the procurement strategy. Buyers can use this data to make informed decisions about supplier selection, ordering cycles and stock levels.
Optimization of the procurement policy
By analyzing key figures such as inventory turnover, stock range and service level, buyers can continuously improve their procurement policy. For example, if the analysis shows that the inventory turnover rate is too low while the service level is high, this indicates excessive safety stocks. In this case, order quantities could be reduced or delivery intervals shortened in order to reduce capital commitment without jeopardizing security of supply.
Conversely, a high inventory turnover rate combined with a low service level may indicate that stocks have been calculated too tightly. In this case, it would be advisable to adjust the safety stocks or improve the accuracy of the forecast in order to increase delivery readiness.
Integration into supplier management
Key stock figures also play an important role in supplier management. For example, buyers can compare the average delivery time and reliability of different suppliers and make decisions about supplier selection or development on this basis.
The analysis of inventory development in relation to suppliers can also provide information about the quality of the collaboration. If higher safety stocks have to be maintained for certain suppliers than for others, this can be an indicator of optimization potential in the supplier relationship.
Demand forecasts and procurement planning
The historical development of inventory figures forms an important basis for demand forecasts and the procurement planning based on them. By analyzing consumption patterns, seasonal fluctuations and inventory trends, buyers can predict future requirements more accurately and align their procurement activities accordingly.
Modern forecasting methods combine historical warehouse data with current market information and thus enable forward-looking inventory optimization. This is particularly important for products with long procurement times or strong fluctuations in demand.
Practical example: Optimization of warehouse key figures in an industrial company
A medium-sized automotive supplier with an annual turnover of 150 million euros was faced with the challenge of making its warehousing more efficient and reducing its tied-up financial resources. The company was able to achieve significant improvements by systematically analyzing and optimizing its key warehouse figures.
Initial situation and problem analysis
The analysis of the current situation revealed the following key figures:
- Average stock level: 12 million euros
- Stock turnover rate: 6 per year
- Average storage time: 60 days
- Service level: 98.5%
- Capital commitment costs (at 8% interest rate): 960,000 euros per year
A detailed inventory analysis revealed that excessive safety stocks were being held, particularly for B and C items, while supply bottlenecks were repeatedly occurring for some A items. In addition, the ordering processes were not optimally adapted to actual demand patterns.
Measures implemented
The following measures were implemented based on the analysis:
- Introduction of differentiated inventory management: Close monitoring with daily inventory monitoring was established for A items, while B and C items were checked at longer intervals.
- Optimization of safety stocks: Based on a statistical analysis of delivery times and fluctuations in demand, safety stocks were recalculated - with an increase for critical A items and a significant reduction for B and C items.
- Adjustment of ordering cycles: Longer-term supply agreements with staggered call-off quantities were implemented for items with stable demand patterns, while items with volatile demand were switched to more flexible, demand-oriented procurement concepts.
- Intensification of supplier cooperation: Vendor Managed Inventory (VMI) and just-in-time concepts were agreed with key suppliers in order to reduce inventories and increase supply security at the same time.
Results and performance measurement
After one year, the stock figures showed the following development:
- Average inventory: reduction to 9 million euros (-25%)
- Stock turnover rate: increase to 8 per year (+33%)
- Average storage period: reduced to 45 days (-25%)
- Service level: slight increase to 99.0% (+0.5 percentage points)
- Capital commitment costs: reduction to 720,000 euros per year (-240,000 euros)
Taking into account the reduced storage costs for space, personnel and handling as well as the improved process efficiency, this resulted in total annual cost savings of over 400,000 euros. At the same time, the more demand-oriented inventory management improved the security of supply, resulting in fewer production interruptions and greater customer satisfaction.
This example illustrates how a systematic analysis and optimization of warehouse key figures can lead to significant improvements in the entire supply chain. The decisive factor for success was the consistent alignment of the measures to the specific requirements of the different article groups and the close integration of Procurement, logistics and production.
Digitalization in warehouse KPI management
Digitalization has revolutionized the management of warehouse KPIs and now offers purchasing departments completely new possibilities for data collection, analysis and visualization. Modern systems enable automated, near-real-time calculation of KPIs and support data-driven decision-making processes in Procurement.
Advantages of digital solutions over manual processes
- Higher data quality and timeliness: Digital systems record stock movements in real time and minimize manual errors in data collection. This leads to more precise and up-to-date warehouse KPIs.
- Faster evaluation and reaction: The automated calculation of key figures enables immediate analysis and faster reaction to changes in stock levels or the demand situation.
- More extensive analysis options: Modern software solutions offer advanced analysis functions such as trend and pattern recognition, multidimensional evaluations and predictive analyses.
- Better visualization and communication: Digital dashboards clearly visualize warehouse key figures and enable more effective communication between Procurement, logistics and other departments.
Integrated systems for warehouse KPI management
Various system categories are used for effective digital management of warehouse KPIs:
- Enterprise Resource Planning (ERP) systems: Form the basis for the integration of inventory and transaction data and enable a company-wide view of warehouse key figures.
- Warehouse Management Systems (WMS): Specialized solutions for the detailed control and monitoring of warehouse processes that provide precise operational key figures.
- Supplier Relationship Management (SRM) systems: Link supplier data with inventory information and enable an integrated view of procurement and warehouse key figures.
- Business Intelligence (BI) tools: Provide advanced analysis and visualization capabilities for warehouse KPIs and support management in strategic decision making.
Artificial intelligence and predictive analyses
The latest generation of solutions for warehouse KPI management uses artificial intelligence (AI) and machine learning to go beyond pure reporting and offer predictive functions:
- Demand forecasts: AI algorithms analyze historical inventory data, seasonality and external factors to make more accurate predictions about future demand.
- Automatic inventory optimization: self-learning systems continuously adjust order quantities and times in order to optimize the balance between capital commitment and security of supply.
- Early warning systems: AI-based analyses detect anomalies in stock movements or consumption patterns at an early stage and automatically generate warnings in the event of impending shortages or excess stock.
- Simulation models: Digital twins and simulation tools make it possible to predict the effects of changes in the procurement or warehouse strategy on relevant key figures.
Conclusion and recommendations for action
Warehouse KPIs are indispensable management tools for modern Procurement that go far beyond a mere control function. They form the basis for strategic decisions to optimize the entire supply chain and contribute significantly to the competitiveness of the company. By systematically recording, analyzing and interpreting relevant key figures, buyers can find and continuously improve the optimum balance between capital commitment and security of supply.
Increasing digitalization is opening up completely new possibilities for data-driven warehouse KPI management, which enables near-real-time insights into warehouse performance and can also anticipate future developments through predictive analyses. This results in the following specific recommendations for action for purchasing managers:
- Establish systematic KPI management: Define relevant KPIs for your specific purchasing and warehouse situation and implement routine recording and evaluation processes.
- Use differentiated approaches: Adapt your KPI management to the different requirements of different article groups and prioritize your activities according to their economic importance.
- Invest in digital solutions: Rely on modern systems for automated data collection and analysis to improve the quality and timeliness of your warehouse KPIs.
- Integrate your KPI systems: Link your warehouse KPIs with other relevant data from Procurement, production and sales to obtain a holistic picture of the supply chain.
- Think predictively: Use advanced analysis tools to not only evaluate the current situation, but also to predict and proactively manage future developments.
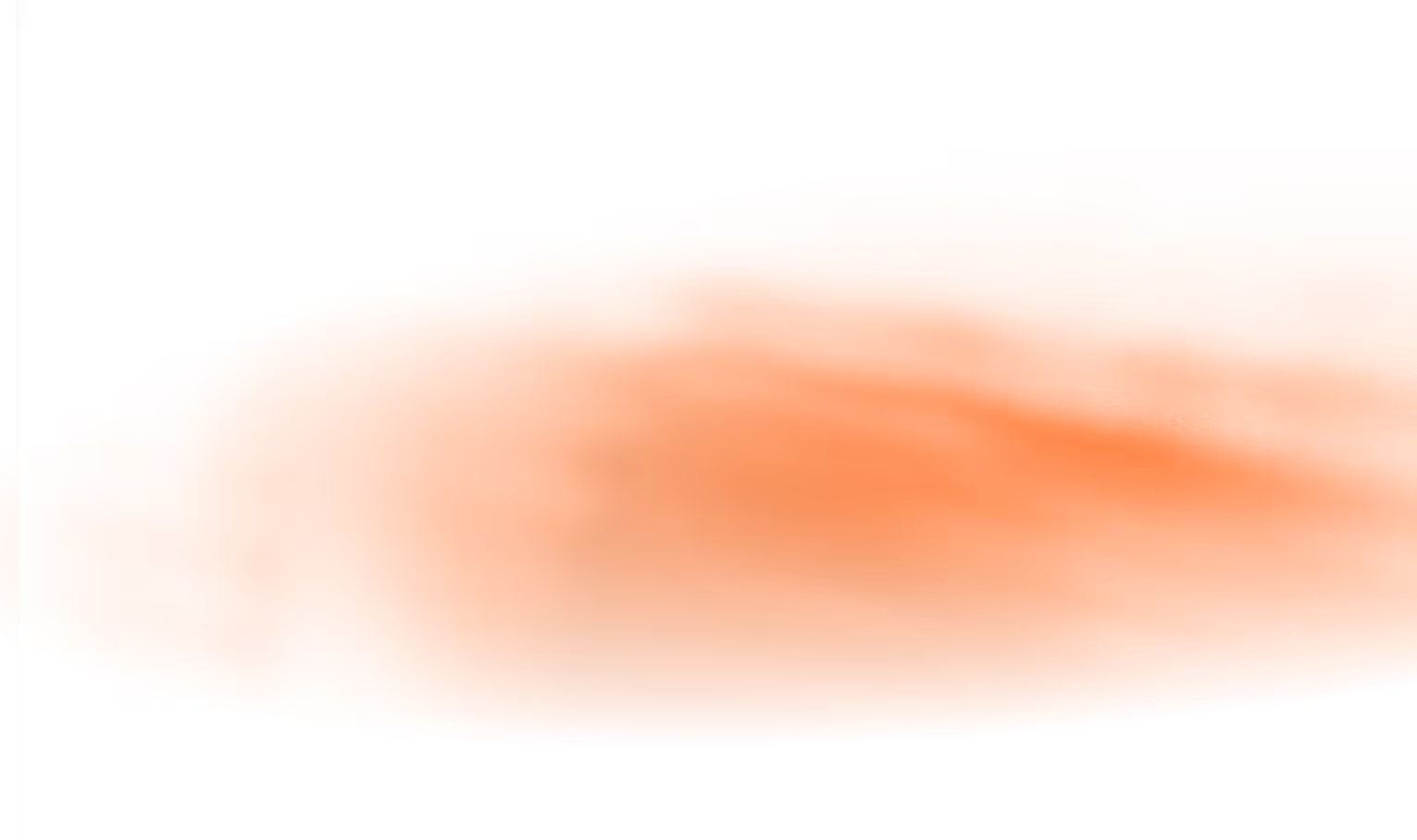
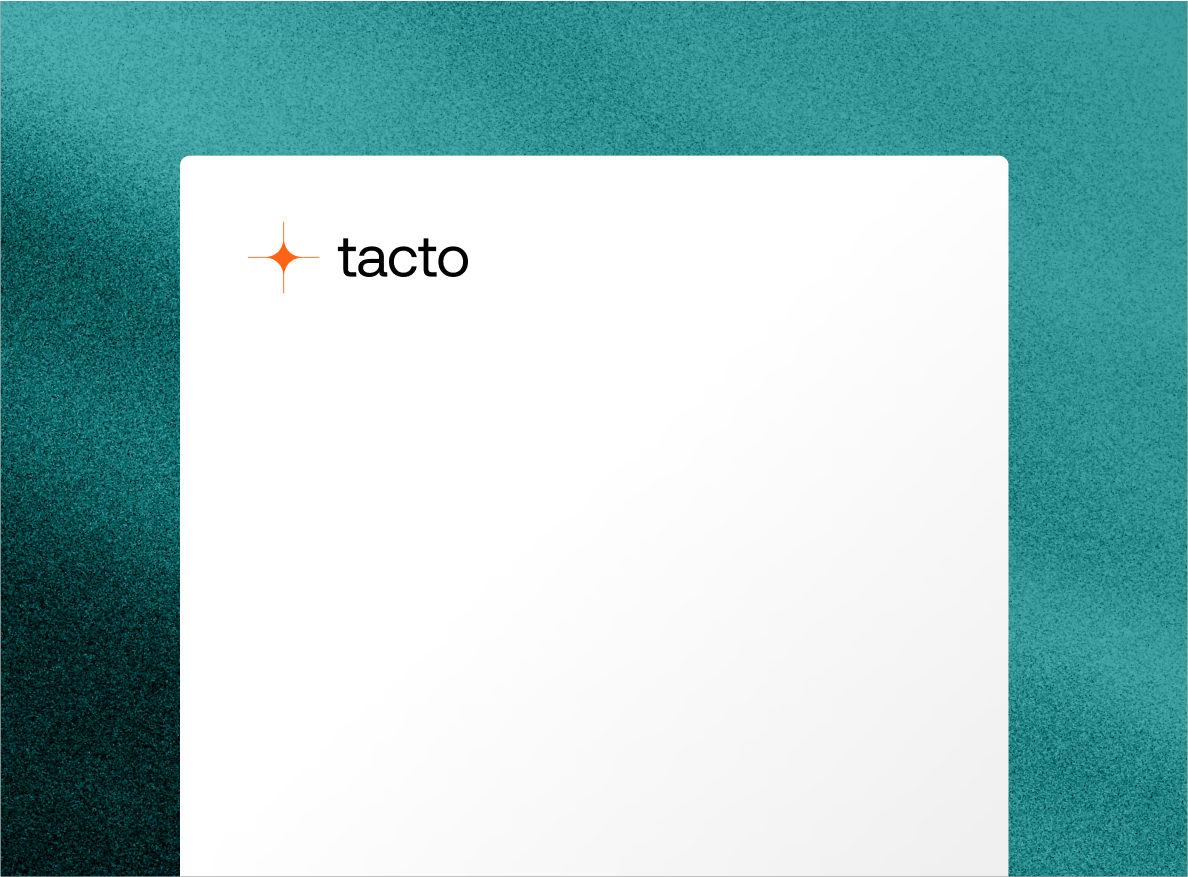