Procurement Glossary
Supplier evaluation: The foundation of strategic procurement decisions
A strategically well thought-out supplier evaluation is not just a tool for cost control, but a decisive success factor in modern procurement management that creates transparency, minimizes risks and secures competitive advantages. The systematic evaluation of suppliers according to objective criteria enables companies to continuously optimize their supplier base and build long-term partnerships based on performance and trust.
What is a supplier evaluation?
Supplier evaluation is a systematic process for qualitatively and quantitatively assessing the performance of suppliers based on defined criteria. It serves as a basis for strategic procurement decisions and enables companies to measure the overall performance of their suppliers in a transparent and comprehensible manner. As part of supplier management, it ensures that the selected suppliers optimally fulfill the company's requirements and that a continuous improvement process takes place.
Strategic importance of supplier evaluation
The importance of professional supplier evaluation can hardly be overestimated in today's business environment. Particularly in production companies with just-in-time manufacturing, precise compliance with delivery times and quality standards is essential for smooth operations. The evaluation not only creates transparency about the supplier's performance, but also forms the basis for:
Improving the quality of procurement
Systematic supplier evaluation contributes directly to improving procurement quality. By continuously monitoring and evaluating supplier performance, quality problems can be identified and rectified at an early stage. This leads to a reduction in rejects, rework and complaints, which directly increases the overall quality of the products and services purchased.
Risk minimization in the supply chain
Identifying and assessing risks in the supplier portfolio is a key aspect of supplier evaluation. By systematically analyzing factors such as financial stability, dependency relationships or security of supply, potential risks in the supply chain can be identified at an early stage and appropriate measures can be taken. This increases the company's resilience to disruptions in the supply chain and ensures a continuous supply of critical materials and components.
Optimization of the supplier base
The evaluation makes it possible to objectively compare the performance of different suppliers and optimize the supplier base accordingly. High-performing suppliers can be identified and promoted, while improvement measures can be introduced for low-performing suppliers or alternative sources of supply can be developed. This process leads to a more efficient supplier base that is better aligned with the company's needs.
Support for strategic decisions
The data and insights gained from the supplier evaluation form a sound basis for strategic supplier management decisions. They support decisions regarding the development of long-term partnerships, the awarding of new contracts or the realignment of the supplier portfolio. The objective evaluation prevents important decisions being made solely on the basis of subjective impressions or personal relationships.
Evaluation criteria for a comprehensive supplier evaluation
An effective supplier evaluation is based on a balanced and company-specific catalog of criteria. The selection and weighting of the criteria should reflect the company's strategic objectives and operational requirements. Typically, the evaluation criteria are divided into the following main categories:
Purchasing criteria
Purchasing criteria primarily relate to commercial aspects of the supplier relationship and have a direct influence on the profitability of procurement. The central purchasing criteria include
- Price and price structure: Evaluation of the price level in relation to the market price and the competition as well as the price structure and price adjustment mechanisms
- Price transparency: the supplier's willingness to disclose its cost structure and calculation, which enables negotiations on an equal footing
- Terms of payment: Assessment of agreed payment terms and conditions and their impact on the liquidity of the procuring company
- Contractual obligations: Existence and quality of framework agreements, quality assurance agreements and other contractual arrangements
Quality criteria
Quality criteria are the most important factors for many companies when evaluating suppliers, as they directly influence the quality of their own products and ultimately customer satisfaction:
- Delivery quality: evaluation of the quality of the delivered products using key figures such as the PPM rate (parts per million), which indicates how many parts per million are defective
- Certifications: Existence of relevant quality certificates (e.g. ISO 9001) and a functioning quality management system
- Complaint management: evaluation of the handling of complaints in terms of response time, problem-solving skills and implementation of sustainable corrective measures (e.g. using 8D reports)
- Quality in sampling: Assessment of the quality of initial samples and compliance with the production part approval process (PPAP)
Logistics criteria
Logistics criteria evaluate the reliability and efficiency of delivery logistics and are particularly important for companies with just-in-time production:
- On-time delivery: adherence to agreed delivery dates, measured as a percentage of on-time deliveries or as an average deviation from deadlines
- Quantity reliability: consistency between ordered and delivered quantities, an important factor for planning reliability in production
- Responsiveness: flexibility and adaptability to changes in demand or special requirements
- Delivery time: Evaluation of the regular delivery time and its consistency across different orders
- Packaging and accompanying documents: quality and completeness of the packaging and the associated documentation
Development and technology criteria
This category evaluates the supplier's technological competence and innovative ability and is particularly relevant for companies in dynamic or technology-intensive industries:
- Innovation capability: Assessment of the supplier's ability to develop and implement innovative solutions
- Technology position: Assessment of the technological status of products and production processes compared to the competition
- R&D investments: Scope of investment in research and development as an indicator for future innovations
- Technical advice: quality of technical advice and support for development projects
Sustainability criteria
With an increasing focus on corporate social responsibility and sustainability, corresponding criteria are also becoming more important in supplier evaluation:
- Environmental and energy policy: evaluation of the environmental impact of production and energy efficiency measures
- Compliance: adherence to relevant laws and regulations, particularly in the area of product and material compliance
- Code of Conduct: Acceptance and implementation of a Code of Conduct for ethical business practices
- Social responsibility: assessment of working conditions, occupational safety and social standards
Supplier evaluation methods
Various methods are available for the practical implementation of supplier evaluation, which can be used depending on the size of the company, the sector and the specific requirements:
Utility value analysis
The utility value analysis is one of the most frequently used methods for supplier evaluation. It is based on a weighted evaluation of various criteria and enables a differentiated and objective assessment of supplier performance:
- Definition and weighting of the evaluation criteria (e.g. quality: 40%, price: 30%, delivery reliability: 20%, innovation: 10%)
- Evaluation of suppliers based on each criterion on a defined scale (e.g. 1-5)
- Calculation of the weighted total value by multiplying the individual ratings by the respective weighting factors
Example of a utility analysis:
Suppose a company evaluates two suppliers of electronic components using the following criteria and weightings:
- Quality: 40%
- Price: 30%
- Delivery reliability: 20%
- Innovation: 10%
The rating is on a scale from 1 (poor) to 5 (very good):
Supplier A:
- Quality: 4 * 0.4 = 1.6
- Price: 3 * 0.3 = 0.9
- Delivery reliability: 5 * 0.2 = 1.0
- Innovation: 3 * 0.1 = 0.3
- Total value: 3.8
Supplier B:
- Quality: 5 * 0.4 = 2.0
- Price: 2 * 0.3 = 0.6
- Delivery reliability: 4 * 0.2 = 0.8
- Innovation: 5 * 0.1 = 0.5
- Total value: 3.9
In this example, supplier B with 3.9 points would score slightly better than supplier A with 3.8 points, despite the higher price, due to the better quality and innovative ability.
Profile analysis
The profile analysis visualizes the strengths and weaknesses of a supplier in the form of a profile and enables a quick visual comparison of different suppliers:
- Definition of the relevant evaluation criteria
- Evaluation of suppliers on a uniform scale for each criterion
- Creation of a profile that graphically displays the ratings
- Comparison of the profiles of different suppliers
ABC analysis
The ABC analysis is an instrument for prioritizing and classifying suppliers according to their strategic importance for the company:
- A-suppliers: Strategically important suppliers with high purchasing volumes or critical products
- B-suppliers: Medium-important suppliers with moderate purchasing volumes
- C-suppliers: Less important suppliers with low purchasing volumes
This classification enables differentiated management of supplier relationships and efficient use of resources in supplier management.
Implementation of a successful supplier evaluation system
The implementation of a successful supplier evaluation system requires careful planning and preparation. The following steps must be observed:
Determining the scope of the evaluation: Not all suppliers must or should be evaluated to the same extent. It makes sense to focus on strategically important suppliers or suppliers with significant volumes in order to limit the effort and increase efficiency.
Development of a precise catalog of criteria: The selection of evaluation criteria should be company-specific and reflect the company's strategic objectives. Attention should be paid to a balanced combination of quantitative (hard) and qualitative (soft) criteria.
Definition of clear evaluation scales: Clear rating scales should be defined for each criterion to enable an objective and comprehensible assessment. Concrete definitions for each assessment level increase the consistency and comparability of the assessments.
Integration into existing business processes: Supplier evaluation should be integrated into existing business processes in order to avoid duplication of work and increase acceptance. A connection to the ERP system or other relevant IT systems facilitates data collection and evaluation.
Regular implementation and evaluation: The supplier evaluation should be carried out at regular intervals (e.g. every six months or annually) in order to identify developments and trends. The results should be systematically evaluated and translated into concrete measures.
Feedback and communication with suppliers: The results of the evaluation should be communicated with suppliers in order to create transparency and develop joint improvement measures. An open and constructive dialog promotes the further development of the supplier relationship.
Digitization of supplier evaluation
Digitalization offers considerable potential for increasing efficiency and improving quality in supplier evaluation. Modern SRM (Supplier Relationship Management) systems and specialized software solutions support the entire supplier evaluation process.
Automated data acquisition
Digital systems enable the automated recording of relevant evaluation data directly from operational systems such as ERP or QM systems. Key figures such as delivery reliability, complaint rates or price changes can thus be continuously recorded and evaluated without manual effort.
Real-time monitoring and early warning systems
Digital supplier evaluation systems enable continuous monitoring of supplier performance in real time. Deviations from defined target values or negative trends can be identified at an early stage, enabling proactive measures to be taken.
Data analysis and business intelligence
Advanced analysis functions enable in-depth insights into supplier performance and the identification of potential for improvement. The use of business intelligence enables complex correlations to be recognized and strategic decisions to be made on a more informed basis.
Collaborative evaluation processes
Digital platforms make it easier for different specialist departments to collaborate on supplier evaluations. Quality management, logistics, development and Procurement can record their assessments decentrally in a shared system, creating a holistic picture of supplier performance.
Integration into the overall supplier management system
Digital supplier evaluation should not be viewed in isolation, but should be integrated into a comprehensive digital supplier management system. This enables seamless linking with other processes such as supplier selection, qualification, development and risk management.
Future prospects for supplier evaluation
Supplier evaluation is subject to continuous change, which is characterized by technological developments, changing market requirements and new business models. The following trends will shape the future of supplier evaluation:
Predictive analytics and AI
The use of artificial intelligence and predictive analytics makes it possible to use historical data to make predictions about future supplier performance and identify potential risks at an early stage. This enables proactive management of supplier relationships.
Sustainability-oriented evaluation
With an increasing focus on sustainability and social responsibility, corresponding criteria will become more important in supplier evaluation. Assessing the carbon footprint, ethical business practices and social standards will become an integral part of supplier management.
Real-time evaluation and continuous monitoring
Periodic assessments will be replaced by continuous monitoring and evaluation of supplier performance in real time. This enables a faster response to changes and more dynamic management of supplier relationships.
Conclusion: The strategic importance of supplier evaluation
A professional supplier evaluation is much more than an operational necessity - it is a strategic tool for optimizing procurement and ensuring competitiveness. By systematically and objectively evaluating supplier performance, companies can improve their procurement processes, minimize risks and build long-term partnerships with high-performing suppliers. Digitalization offers considerable potential for increasing efficiency and improving quality in the evaluation process, which should be used consistently. It is therefore crucial for Procurement managers to view supplier evaluation not as an isolated task, but as an integral part of holistic supplier management and to organize it accordingly. This is the only way to exploit the full potential of supplier evaluation as a competitive factor.
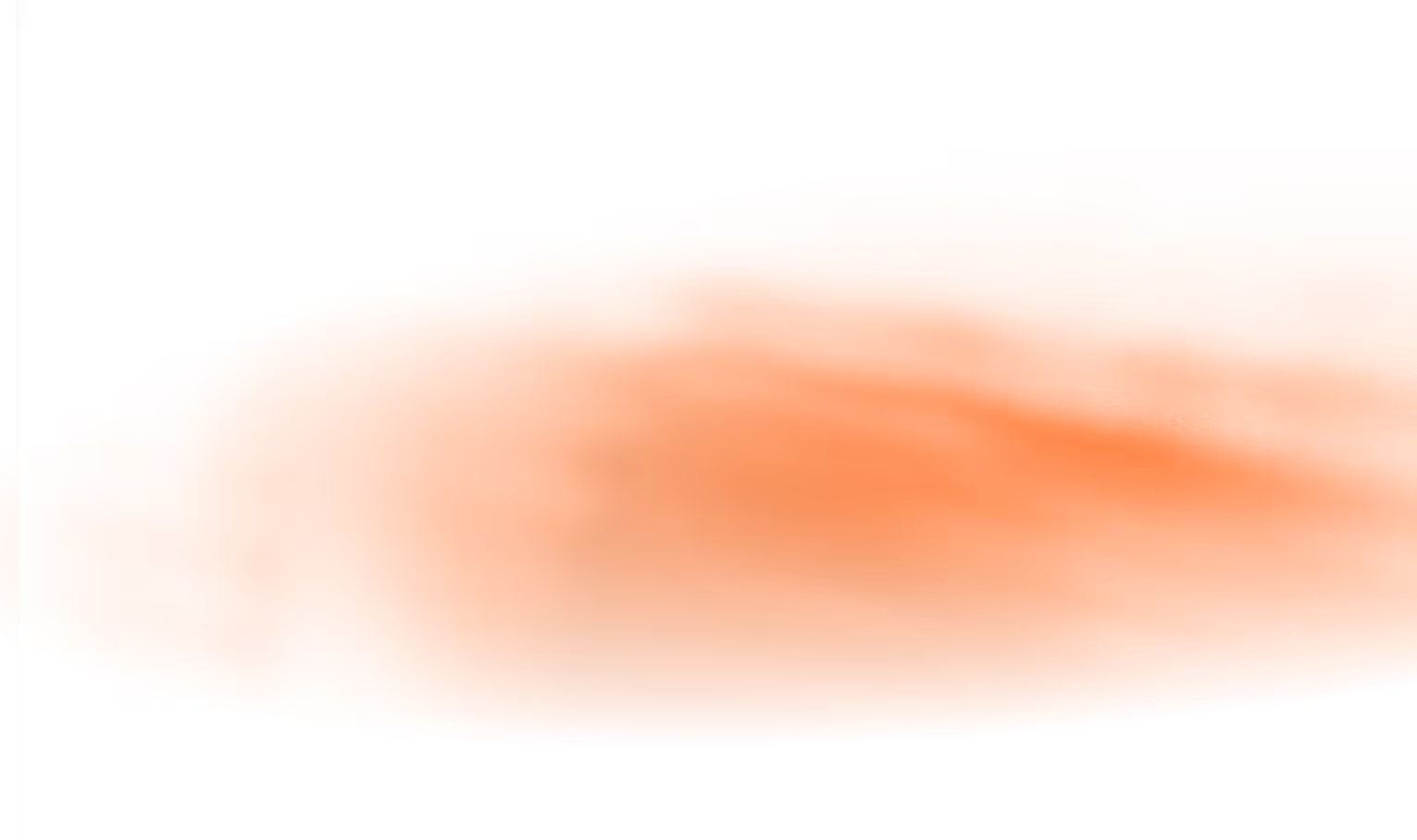
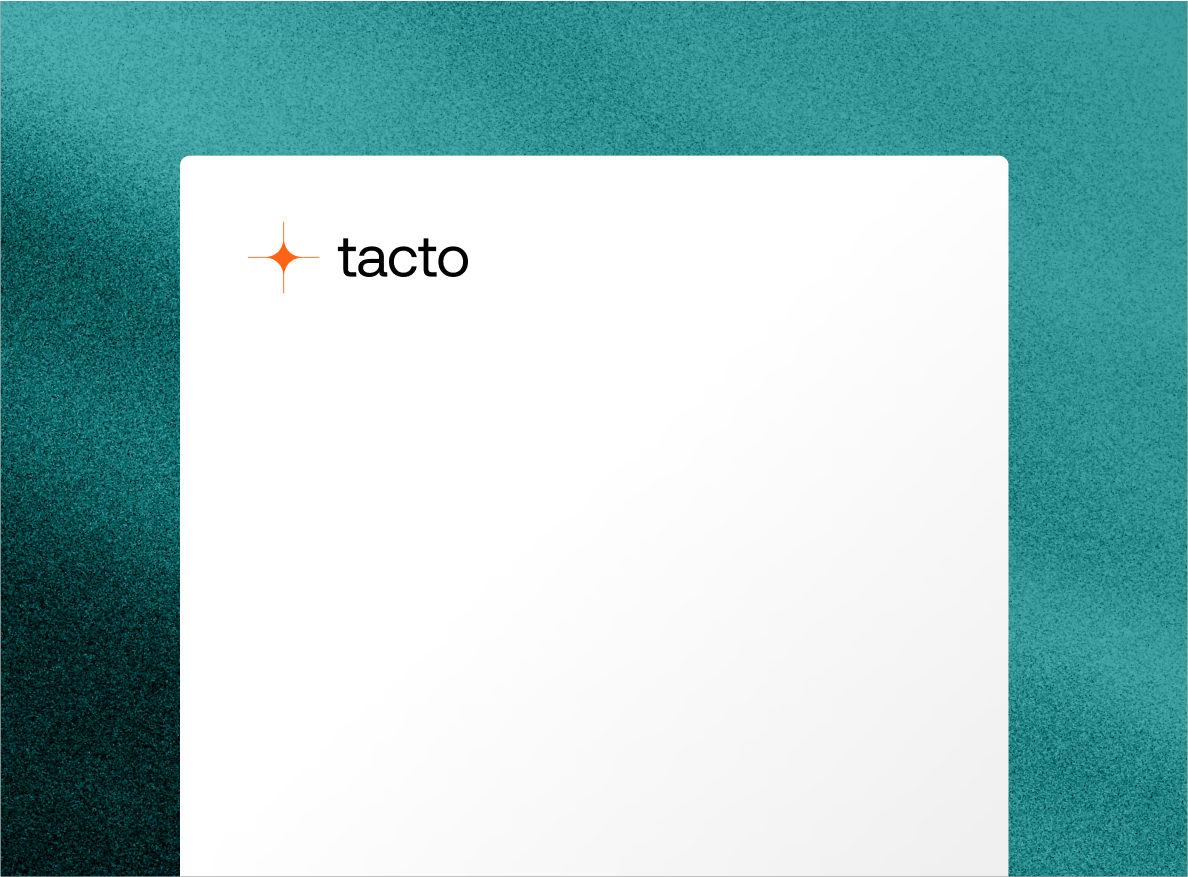