Procurement Glossary
Material classification: definition & important aspects for buyers
The systematic classification of materials forms the foundation for efficient procurement processes and strategic purchasing decisions. This structured overview shows you the most important classification methods and their practical application for optimized material procurement in Procurement.
Material classification in a nutshell:
Material classification is the systematic categorization and grouping of materials according to defined criteria such as quality, intended use or strategic importance. For Procurement , this enables an efficient procurement strategy, optimized supplier selection and targeted inventory management.
You can also read our article on the successful design of supplier strategies! Here you can find out how successful supplier strategies are implemented and what the decisive factors are.
Material classification: basics and application
Material classification is a fundamental instrument of modern procurement management and materials management. It enables a systematic classification and structuring of all materials used in the company according to certain criteria and characteristics. By effectively classifying materials, companies can optimize their procurement processes, better manage stock levels and reduce costs. This overview presents the various methods and approaches of material classification, explains their practical significance and demonstrates the advantages of structured material organization.
What is material classification?
Material classification is a systematic process in which materials and goods are divided into specific categories or classes based on defined criteria. The aim is to create a clear structure and overview of the materials available in order to optimize processes in Procurementwarehousing and production processes. The standardization of master data management facilitates communication within the company and with supplier management.
Core elements of material classification
Importance of material classification in Procurement
Material classification is of central importance for Procurement , as it creates transparency regarding the procurement volume and the variety of materials. It enables purchasing processes to be standardized, requirements to be bundled and negotiations with suppliers to be conducted more efficiently. It also helps to reduce costs by avoiding excess stock and optimizing inventories.
Material classification: from manual to AI-supported classification
Building on the theoretical foundation of material classification as the key to efficient procurement processes, the practical implementation becomes a crucial component for companies. Accurate and consistent classification of materials is essential in practice for transparency, cost savings and process optimization. However, traditional methods have reached their limits, highlighting the need for a transformation towards modern approaches.
Old: Manual classification
Traditional approach: In traditional practice, material classification is carried out manually by employees who categorize materials based on defined criteria. Excel spreadsheets or simple databases are often used for this. Those responsible sift through material masters, check properties and assign them accordingly. This method requires a considerable amount of time and is prone to human error. In addition, the consistency of the classification is often limited by individual interpretations, which leads to inconsistencies in master data management and reduces the efficiency of procurement processes.
New: AI-driven classification
AI-driven classification: Modern implementations rely on AI in Procurement and machine learning to automate and optimize material classification. By using algorithms that recognize patterns in material data, materials can be categorized quickly and accurately. This technology enables the processing of large amounts of data in a short time and reduces human error. In addition, continuously learning systems are used that adapt to new material types and properties. This leads to a significant increase in data quality, increases efficiency in procurement processes and supports strategic decisions through better data analysis.
Practical example: Automotive industry
A leading automotive manufacturer implemented an AI-supported material classification system to optimize its global procurement processes. Automation reduced classification time by 70%. Data quality improved significantly, resulting in savings of 15% of procurement costs. procurement costs resulted. In addition, the consistent classification enabled more effective negotiations with suppliers and better stock management, as material requirements were forecast more accurately.
Conclusion on material classification
Material classification is an indispensable tool for modern companies that creates transparency and optimizes processes. Systematic categorization and uniform standards not only reduce costs, but also significantly increase efficiency in procurement and warehousing. The initial implementation effort is more than offset by long-term benefits such as better supplier negotiations, reduced stock levels and optimized procurement processes. With a view to future developments such as AI-supported classification, the strategic importance of this tool will continue to increase.
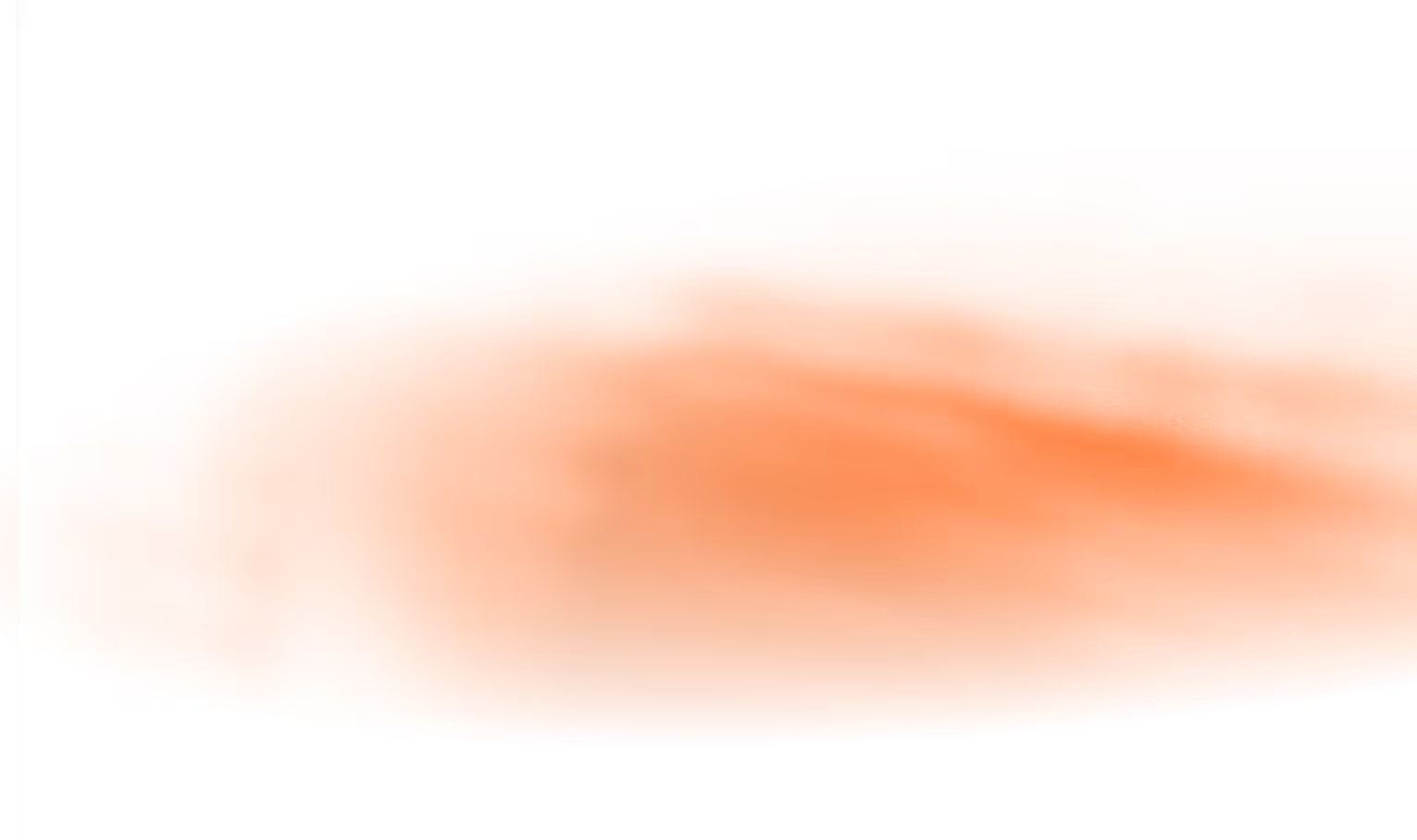
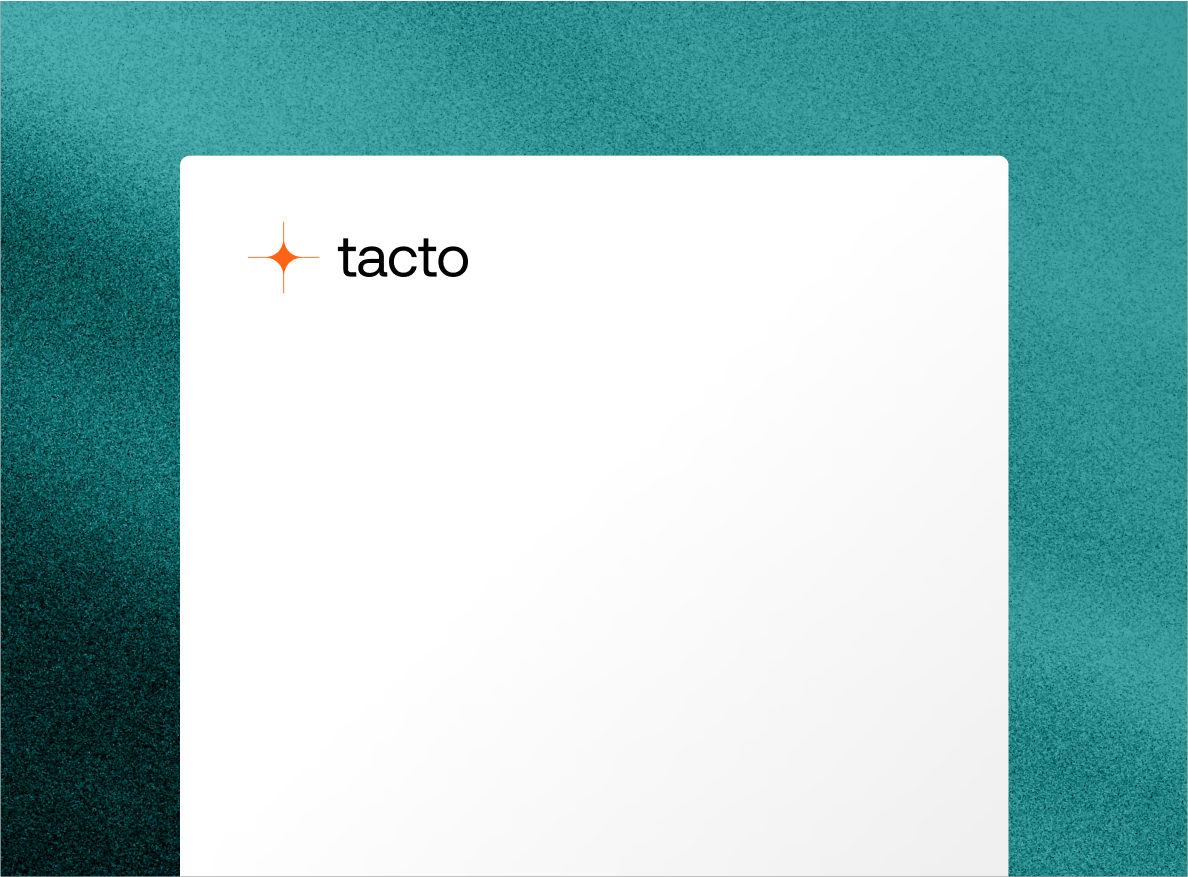