Procurement Glossary
Traceability of materials: definition and important aspects for buyers
The traceability of materials enables companies to document the entire life cycle of their products transparently, thereby fulfilling legal requirements and providing evidence of quality and sustainability. This structured overview shows how Procurement creates the basis for seamless material traceability through effective tracking systems and supplier management.
Traceability in a nutshell:
Traceability describes the ability to seamlessly document the entire path of a material or product across all stages of the supply chain - from raw material extraction to the end consumer. For Procurement , this is an essential tool for quality assurance, compliance with regulatory requirements and rapid response to problems in the supply chain.
Example: Ein Automobilzulieferer implementiert ein Tracking-System mit eindeutigen Chargen-Codes, das innerhalb von 2 Stunden den kompletten Werdegang einer spezifischen Stahlcharge nachverfolgen kann - von der Stahlproduktion über die Weiterverarbeitung bis zum Einbau in 2.500 verschiedene Fahrzeugkomponenten.
Introduction to the traceability of materials
The traceability of materials, also known as material tracking or traceability, is an essential part of modern production and logistics processes. It enables companies to track the path of materials and products along the entire supply chain - from the raw material supplier to the end customer. In times of global supply chains and increasing regulatory requirements, seamless traceability is becoming increasingly important. It not only serves quality assurance and process optimization, but is also essential for adhering to compliance requirements and reacting quickly to possible product recalls. In this guide, you will learn about the most important aspects of material traceability, its implementation and the associated opportunities and challenges.
What is traceability of materials?
The traceability of materials refers to the ability to follow the path of a material or product through all stages of production, processing and distribution. It enables companies to trace the origin, location and use of materials at any point in time. This is crucial for quality assurance, transparency and compliance with legal regulations in the supply chain.
Core elements of material tracking
Significance for Procurement
The traceability of materials is essential for Procurement in order to guarantee quality standards and minimize risks. It contributes to transparency in the supply chain and enables responsible procurement decisions to be made. It also makes it easier to meet compliance requirements and provides support in the event of recalls by quickly identifying affected batches.
Traceability of materials: from manual documentation to digital real-time tracking
Building on the importance of material traceability for transparency and quality in the supply chain, it becomes clear how crucial precise information is for modern companies. Traditional methods are reaching their limits, especially in the face of globalized markets and complex supplier networks. To remain competitive and meet regulatory requirements, a shift towards innovative technologies is essential.
Old: Manual documentation
Traditional approach: In the past, the traceability of materials was mainly based on manual processes. Companies used paper-based systems where employees manually recorded deliveries and material movements. Identification systems were often limited to simple barcodes and data was recorded in isolated spreadsheets or forms. This method was time consuming and prone to human error. The limited timeliness of the information made it difficult to respond quickly to quality issues or obtain accurate inventory overviews. In addition, the lack of standardized communication channels between suppliers and manufacturers led to inefficiencies and delays.
New: Digital Tracking
Digital tracking: Nowadays, companies rely on digital solutions to optimize traceability. The use of RFID tags, IoT sensors and advanced data management systems enables seamless and real-time monitoring of materials. These technologies seamlessly integrate identification, data collection and communication into existing ERP systems. Innovations such as blockchain also ensure the immutability and security of tracking data. Practical benefits include a significant reduction in errors, increased transparency along the entire supply chain and improved compliance with regulatory requirements. Companies report up to 70% faster response times for quality deviations and an increase in logistics efficiency of up to 50%.
Practical example: Pharmaceutical industry
A global pharmaceutical company implemented an integrated digital tracking system to monitor the origin and condition of its active ingredients. Thanks to RFID and IoT sensor technology, temperature and humidity could be monitored in real time during transportation. This led to an 80% reduction in damaged batches and saved over €5 million annually. It also enabled the company to meet stricter regulatory requirements and increased customer confidence.
Conclusion on the traceability of materials
Material tracking is an indispensable tool for modern companies, enabling transparency, quality assurance and risk minimization. By integrating digital technologies and standardized processes, companies can not only meet legal requirements but also increase their competitiveness. Success lies in consistent implementation across the entire supply chain and a willingness to invest in future-oriented technologies.
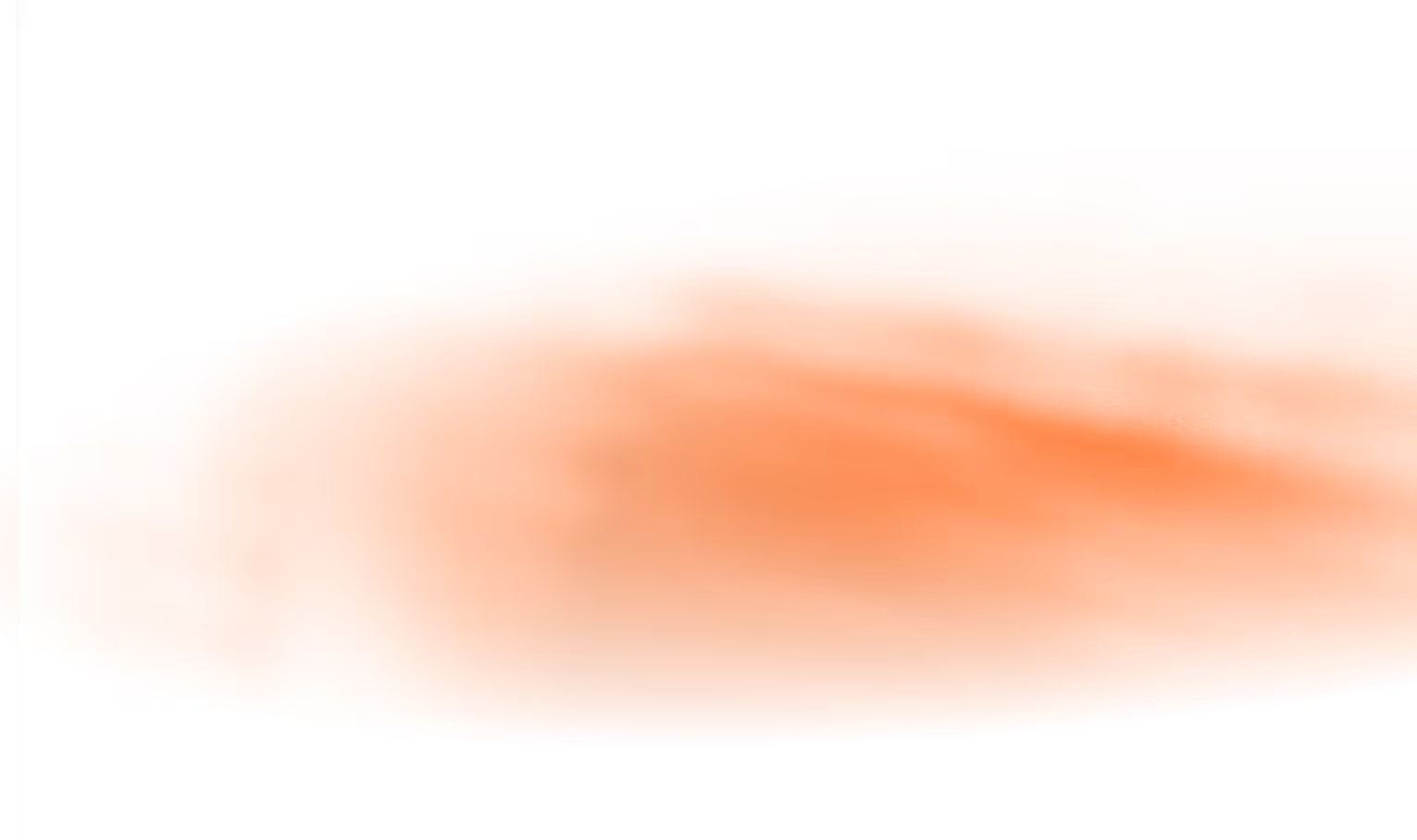
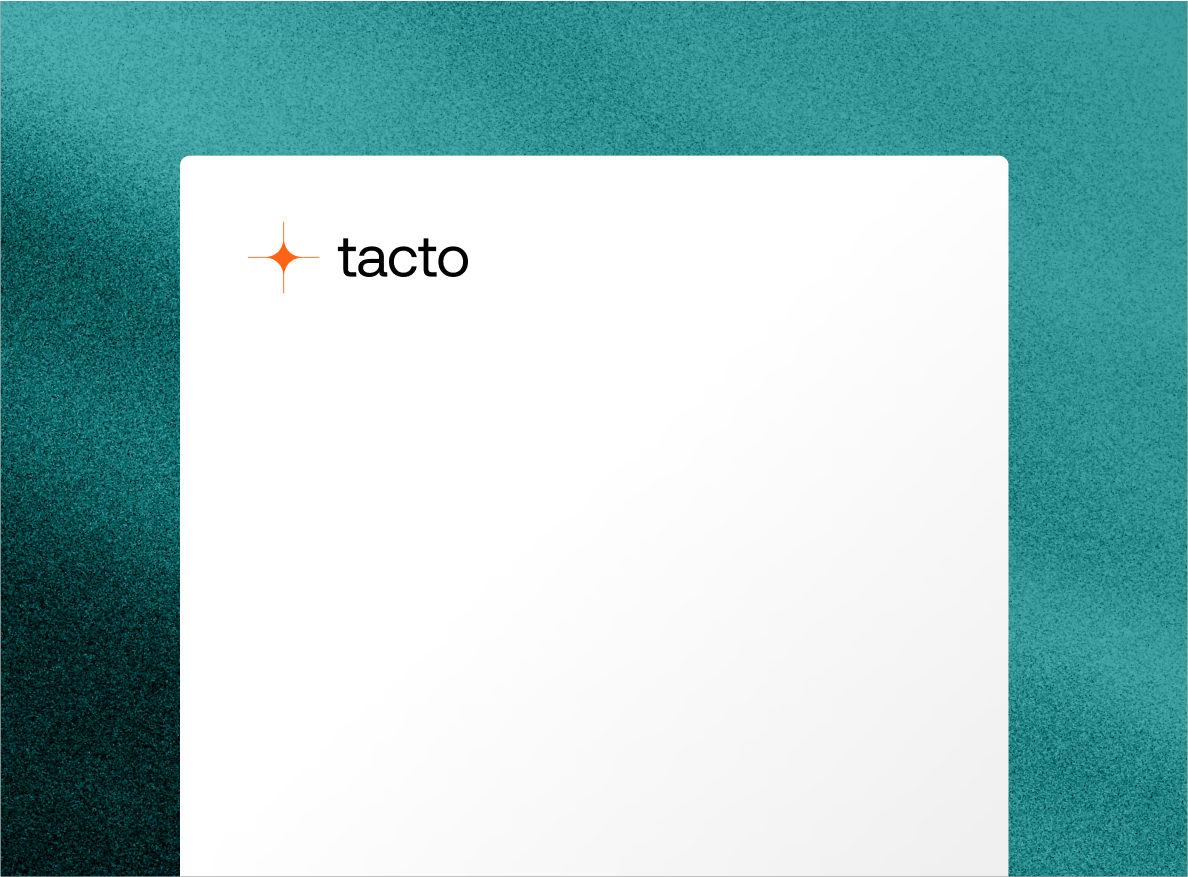