Procurement Glossary
Process costs: definition and important points for buyers
Process costs have a significant impact on a company's profitability and offer great potential for optimization along the entire value chain. The following overview shows how Procurement can generate real competitive advantages through systematic process cost analysis and control.
Litigation costs in a nutshell:
Process costs are all expenses incurred in the execution of business processes, including personnel, system and administrative costs. In Procurement , their systematic recording and analysis enables the identification of optimization potential and the evaluation of the actual profitability of procurement processes.
Example: A standard order with a goods value of 500 euros incurs average process costs of 85 euros, consisting of 45 minutes of working time (38 euros), IT system costs (22 euros) and administrative expenses (25 euros), which demonstrates the need for an order value limit of at least 250 euros.
Introduction to process cost analysis
Activity-based costing is a modern cost management tool that was developed in the 1980s to meet the increasing demands for cost transparency in companies. It represents a further development of traditional cost accounting and focuses in particular on the allocation of overhead costs to operational processes in line with their causation. At a time when the complexity of business processes is constantly increasing and indirect costs account for an ever greater proportion of total costs, activity-based costing is becoming increasingly important. This guide provides a comprehensive overview of the principles, methods and practical application of activity-based costing in the modern business environment.
What are legal costs?
Process costs are the costs incurred in the execution of business processes within a company. In purchasing optimization, process costs refer to all expenses associated with the procurement of goods and services, apart from direct material costs. This includes costs for order processing, supplier management, quality assurance and internal administration. Understanding and optimizing these costs is crucial to increasing efficiency in Procurement and securing competitive advantages.
Core elements of process costs in Procurement
Importance of process costs in Procurement
The analysis and optimization of process costs are of great importance for purchasing departments. By reducing these costs, companies can improve their margins and use resources more efficiently. Effective process cost management leads to:
Process costs: from manual recording to process mining
Building on the theoretical basis of process costs, it is essential for companies not only to understand these costs, but also to control them effectively. The practical significance lies in the fact that uncontrolled process costs can reduce competitiveness. In a time of increasing complexity and dynamics in the economy, a transformation from traditional methods to modern approaches is necessary in order to make processes more efficient and cost-effective.
Old: Manual process cost recording
Traditional approach: In the past, process costs were often recorded and evaluated manually. Employees documented their working hours and resource consumption on paper or in simple spreadsheets. The data was collected periodically and analyzed by Controlling. This process was time-consuming and error-prone, as it was based on self-recordings and estimates. In addition, the delayed evaluations meant that decisions were often based on outdated information. The limited transparency made it difficult to identify and optimize cost-driving processes at an early stage.
New: Process Mining
Process mining: The use of process mining has fundamentally changed the recording and risk analysis of process costs. Modern software solutions automatically extract data from existing IT systems such as ERP or CRM. This enables a detailed visualization of real process flows in real time. Algorithms are used to identify bottlenecks, delays and unnecessary process steps. The integration of AI in Procurement also allows forecasts and simulations of future process flows. The practical benefits are significant: companies can reduce process costs by up to 30%, increase efficiency and react more quickly to market changes.
Practical example: Optimization in the manufacturing industry
A medium-sized manufacturing company was faced with the challenge of coping with rising process costs in production planning. By implementing process mining, they were able to visualize the actual processes for the first time. It turned out that a large proportion of the costs were caused by unnecessary waiting times and redundant release loops. After targeted process adjustments, process costs were reduced by 20% and production throughput time was cut by 15%. In addition, adherence to delivery dates improved, which led to higher customer satisfaction.
Conclusion on legal costs
Process costs in Procurement are a decisive factor for a company's profitability. The systematic recording, analysis and optimization of these costs holds considerable savings potential. Process costs can be significantly reduced through the targeted use of digitalization and automation. The key to success lies in the combination of standardized processes, qualified employees and modern IT solutions. Only those who know their process costs and actively manage them will be able to remain competitive in the long term.
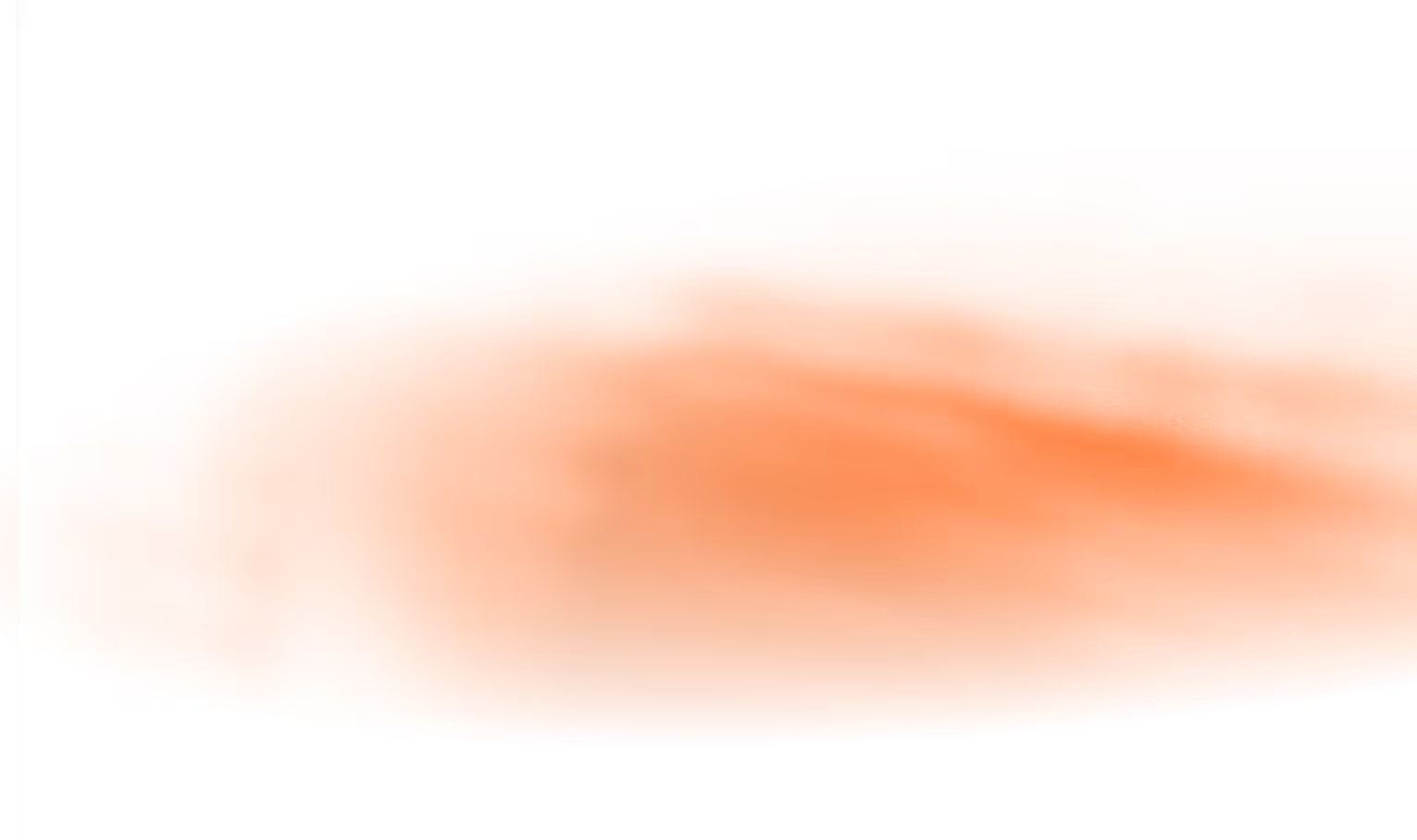