Procurement Glossary
Activity-based costing: definition & important aspects for buyers
Activity-based costing allows you to allocate costs according to cause and thus creates the basis for well-founded decisions in product and process design. The following overview shows you how you can use this method in Procurement to identify cost drivers and systematically tap into savings potential.
Activity Based Costing in a nutshell:
Activity-based costing is a cost accounting method that allocates overhead costs to cost centers based on the actual activities performed. For Procurement , this method enables a more precise assessment of the true procurement costs and helps to identify cost drivers in procurement processes.
Example: An automotive supplier uses ABC and determines that the procurement of C-parts incurs average process costs of 105 euros per order, which are made up of 45 minutes of working time (67.50 euros), IT systems (25 euros) and quality assurance (12.50 euros).
Introduction to Activity Based Costing
Activity-based costing (ABC) is an innovative cost accounting system that was developed in the 1980s. It represents a modern approach to allocating overhead costs by focusing on the actual activities and processes in the company. Unlike traditional cost accounting systems, ABC enables a more precise allocation of costs and thus a better basis for management decisions. In this introduction, we will take a closer look at the basic principles, advantages and challenges of activity-based costing and show how this system can be successfully implemented in practice.
What is activity-based costing?
Activity Based Costing (ABC) is a method for the precise recording and allocation of overhead costs to products, services or customers. In contrast to traditional cost accounting approaches, which distribute costs across the board, ABC analyzes the actual activities that consume resources and allocates the costs to these activities. This enables a more accurate representation of the cost structure and helps companies to identify cost drivers and manage costs more efficiently.
Core elements of activity-based costing
Importance of activity-based costing in Procurement
In Procurement activity-based costing enables a detailed analysis of procurement costs by making the costs of individual purchasing activities visible. This transparency enables buyers to identify inefficient processes, uncover hidden costs and take targeted measures to reduce costs. ABC also supports the evaluation of suppliers by taking into account the actual process costs and thus enabling well-founded decisions for strategic partnerships.
Activity-based costing: From traditional cost accounting to activity-based costing
Activity-based costing has developed from the need to analyze cost structures in more detail in order to meet the increasing demands of modern companies. Based on the theoretical foundation provided by traditional cost accounting, it is often found in practice that there is no precise allocation of overhead costs to the processes that cause them. This leads to distortions in product costing and makes well-founded decision-making more difficult. There is therefore an increasing need to switch from traditional methods to a more precise, process-oriented approach.
Old: Traditional cost accounting
Traditional approach: In traditional cost accounting, costs are mainly allocated to cost centers and cost objects, often using overhead and allocation keys. In practice, this means that overhead costs are allocated proportionally to direct costs or other base values. This approach uses tools such as cost element accounting, cost center accounting and cost object accounting. A key feature is the simplicity and standardization of the process. However, there are considerable limitations, as complex production processes and indirect costs are not adequately mapped. This leads to inaccuracies in cost allocation and can conceal inefficient areas, which impairs the company's competitiveness.
New: Activity-Based Costing
Activity-based costing: The modern approach to activity-based costing revolutionizes implementation through a detailed analysis of all operational activities. Instead of distributing costs across the board, they are allocated directly based on the actual processes and their cost drivers. Innovative technologies such as comprehensive ERP systems and special software solutions make it possible to record and analyze data precisely. This leads to better transparency of cost structures and promotes more efficient decision-making. Practical benefits include the identification of inefficient processes, targeted cost savings and increased flexibility in pricing. Overall, this approach increases the company's competitiveness and adaptability in dynamic markets.
Practical example: Introduction of activity-based costing in the automotive industry
A major automotive supplier implemented activity-based costing to better understand its complex production processes and optimize costs. By recording the process steps in detail and their specific cost drivers, it was possible to identify uneconomical activities. Within the first year, this led to a 12% reduction in overheads and increased the profitability of new product lines by 8%. In addition, the transparency gained enabled more efficient negotiation techniques with suppliers and a better allocation of resources, which strengthened the company's market position in the long term.
Conclusion on activity-based costing
Activity Based Costing is an indispensable tool for precise cost allocation and strategic decision-making in modern Procurement. Despite initial implementation challenges, the method enables significantly more accurate cost transparency than traditional methods. Increasing digitalization and AI integration make ABC even more efficient and meaningful, enabling optimized management of procurement processes and informed make-or-buy decisions. The long-term benefits of improved cost control and strategic purchasing decisions clearly outweigh the initial outlay.
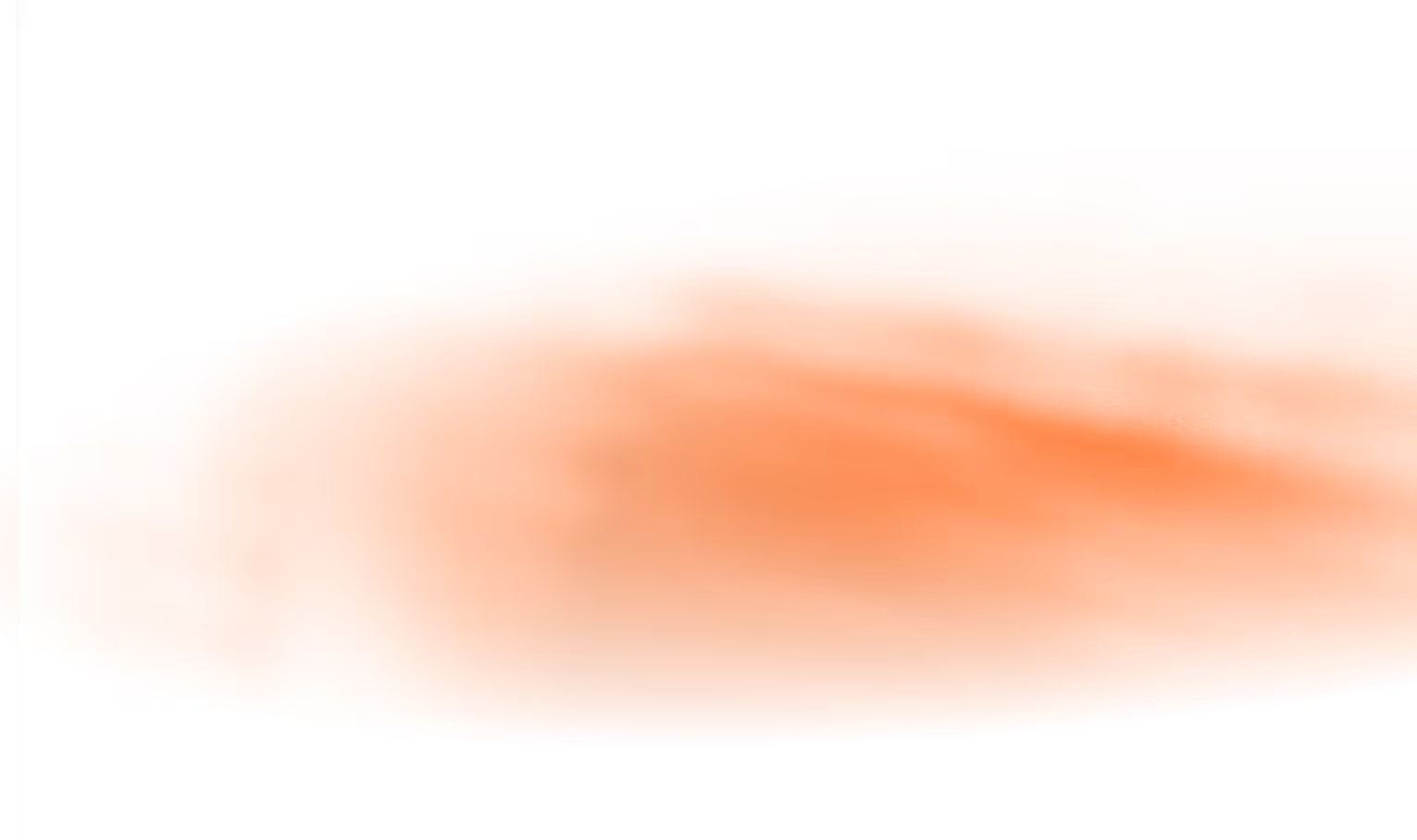
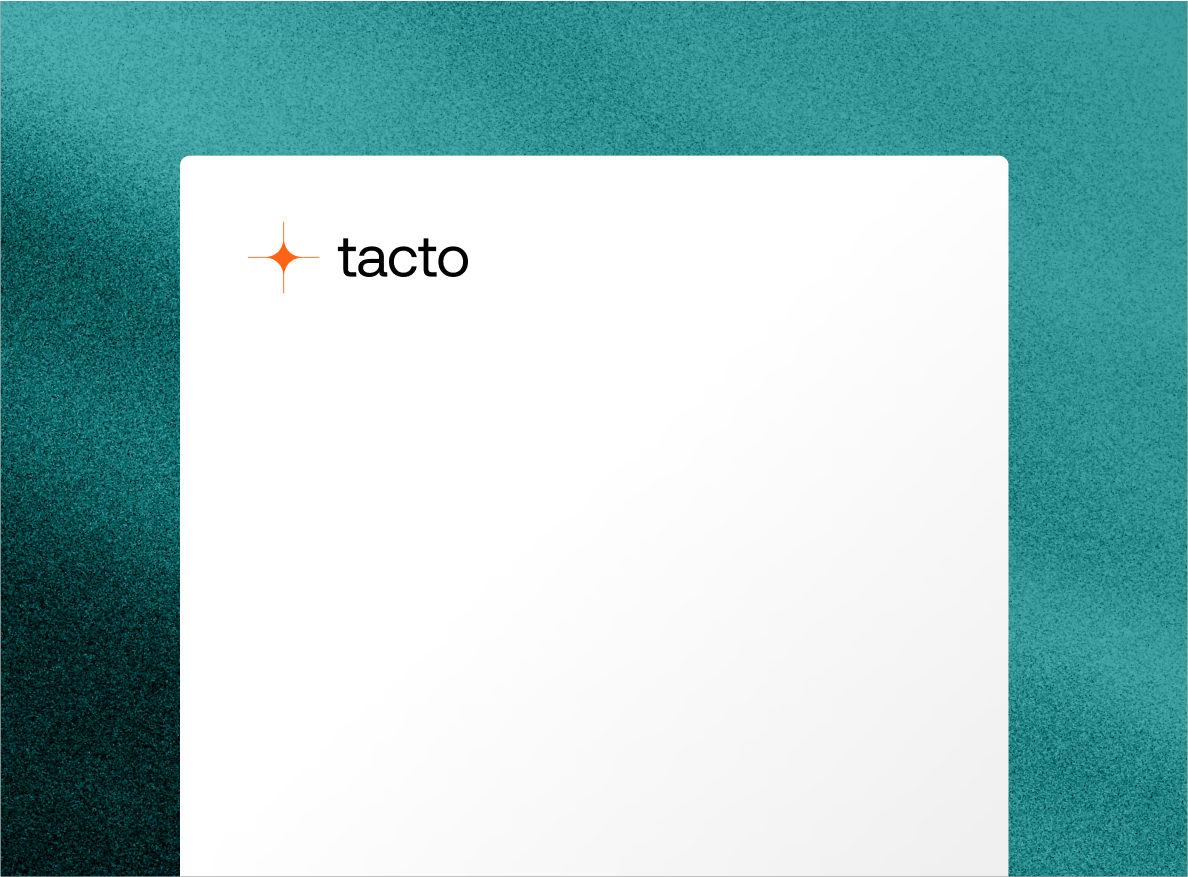