Procurement Glossary
Specification management: definition & important aspects for buyers
Specification management forms the foundation for successful procurement processes and ensures precise communication between all parties involved in the supply chain. This structured overview shows how Procurement optimizes quality, costs and risks through professional specification management and sustainably improves cooperation with internal and external partners.
Specification management in a nutshell:
Specification management is the systematic process of creating, managing and monitoring technical requirements and properties of products or services. For Procurement , this enables precise supplier selection, clear comparisons of offers and the assurance of product quality through clearly defined requirements.
Example: An automotive supplier manages detailed specifications for 2,500 components in a central system, reducing the development time for new products by 30% and cutting quality deviations for supplier parts by 45%.
Introduction to specification management
Specification management is an essential building block in modern quality and product management. It deals with the systematic recording, management and maintenance of product specifications and technical requirements. At a time when products are becoming increasingly complex and global supply chains are gaining in importance, the professional management of specifications plays a central role in a company's success. Effective specification management not only ensures product quality, but also contributes to cost savings and risk minimization. In this guide, we explain the principles, methods and best practices of specification management and its importance for modern corporate management.
What is specification management?
Specification management refers to the process of creating, managing and updating detailed requirements and specifications for products or services in Procurement. It forms the basis for clear communication channels between companies and suppliers by ensuring that all parties involved share the same expectations and quality standards. Effective specification management can avoid misunderstandings and increase efficiency in procurement processes.
Core elements of specification management
Significance for Procurement
In Procurement , specification management is crucial for the procurement of high-quality products and services that meet the company's requirements. It helps to minimize procurement risks, control costs and strengthen supplier relationship management. With clear specifications, buyers can ensure that suppliers meet expectations and projects are completed on time and within budget.
Specification management: from static documents to digital collaboration platforms
In practice, specification management is a key element in ensuring that products and services meet the defined requirements management. Building on the theoretical foundation, it becomes clear how important clear and up-to-date specifications are for successful procurement processes. Traditional methods are increasingly reaching their limits, especially in times of increasing complexity and speed of the flow of goods and information. A transformation towards digital solutions is essential in order to increase efficiency and competitiveness.
Old: Static documentation
Traditional approach: In traditional specification management, requirements were usually created in the form of static documents such as paper documents, Word files or PDFs. These documents were created manually and sent to the respective suppliers by email or post. Communication was time-consuming and error-prone, as updates were often not passed on consistently. Change management had to be tracked manually, which led to delays and misunderstandings. There was also a lack of centralized data storage and transparency, which made it difficult to keep track of the current specification status. This often led to quality deficiencies, delays in delivery and increased costs due to rework.
New: Digital collaboration platforms
Digital Collaboration Platforms: The modern approach relies on digital collaboration platforms that enable specifications to be managed centrally and in real time. By using cloud technologies, all participants can access current documents simultaneously and work on them together. Innovations such as automatic version control, change management and approval processes significantly improve efficiency. Suppliers have immediate access to the latest specifications and can provide feedback or clarify questions directly. This reduces communication errors and speeds up the approval process. In addition, these platforms enable seamless integration into existing systems such as ERP or PLM, resulting in increased transparency and data consistency.
Practical example: Automotive industry
A leading automotive supplier implemented a digital collaboration platform for specification management. The changeover reduced the time needed to coordinate product requirements by 40%. The number of errors due to outdated or inconsistent documents fell by 60%. At the same time, the time-to-market to customer change requests improved by an average of 3 days. This led to higher customer satisfaction and cost savings of over 500,000 euros per year due to avoided rework and process optimization.
Conclusion on specification management
Specification management is an indispensable tool in modern Procurement that ensures the quality of procurement through precise requirements definition and systematic documentation. Successful implementation requires a well thought-out digitalization strategy, standardized processes and close cooperation between all stakeholders. Only through consistent specification management can companies minimize procurement risks, optimize costs and remain competitive in the long term.
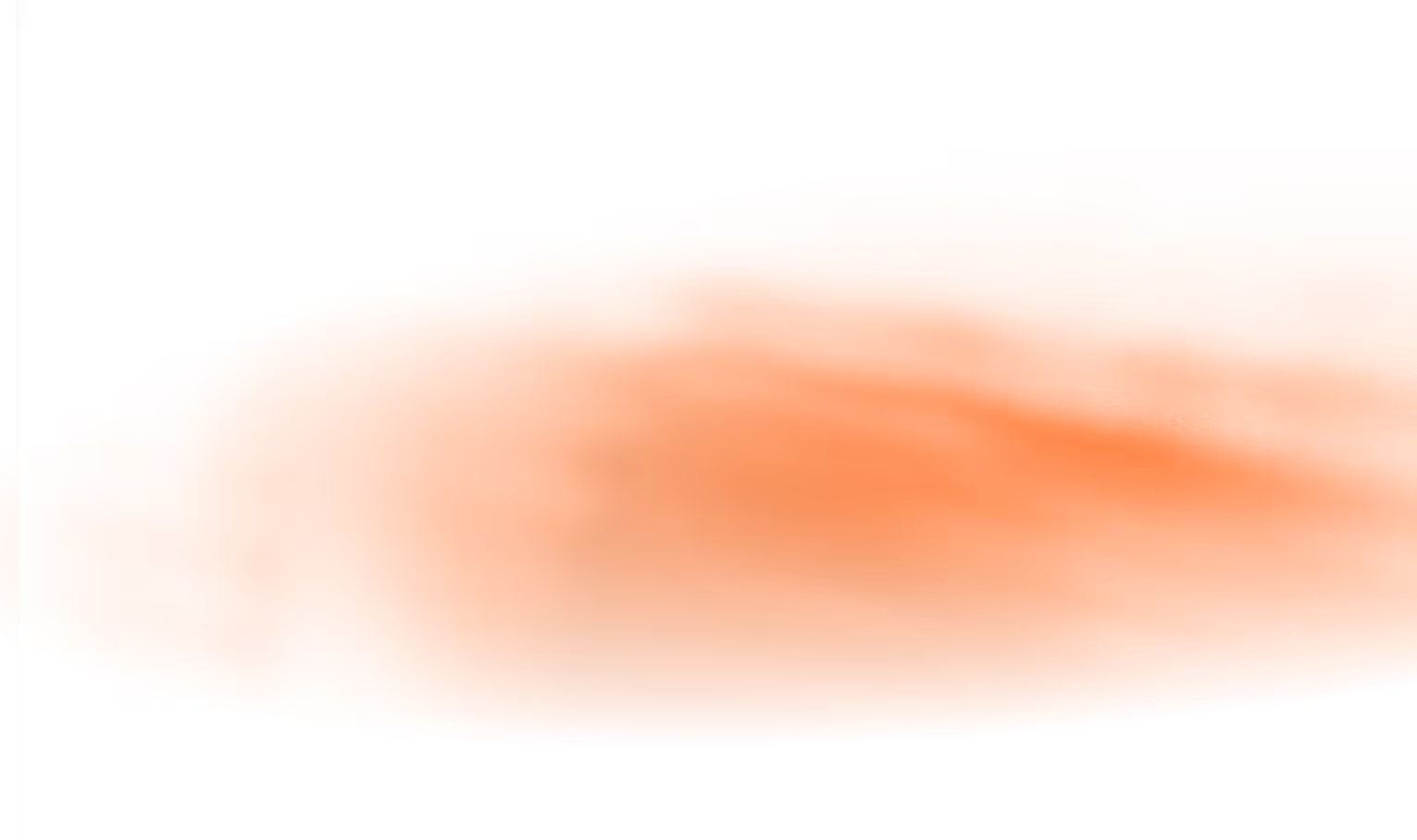
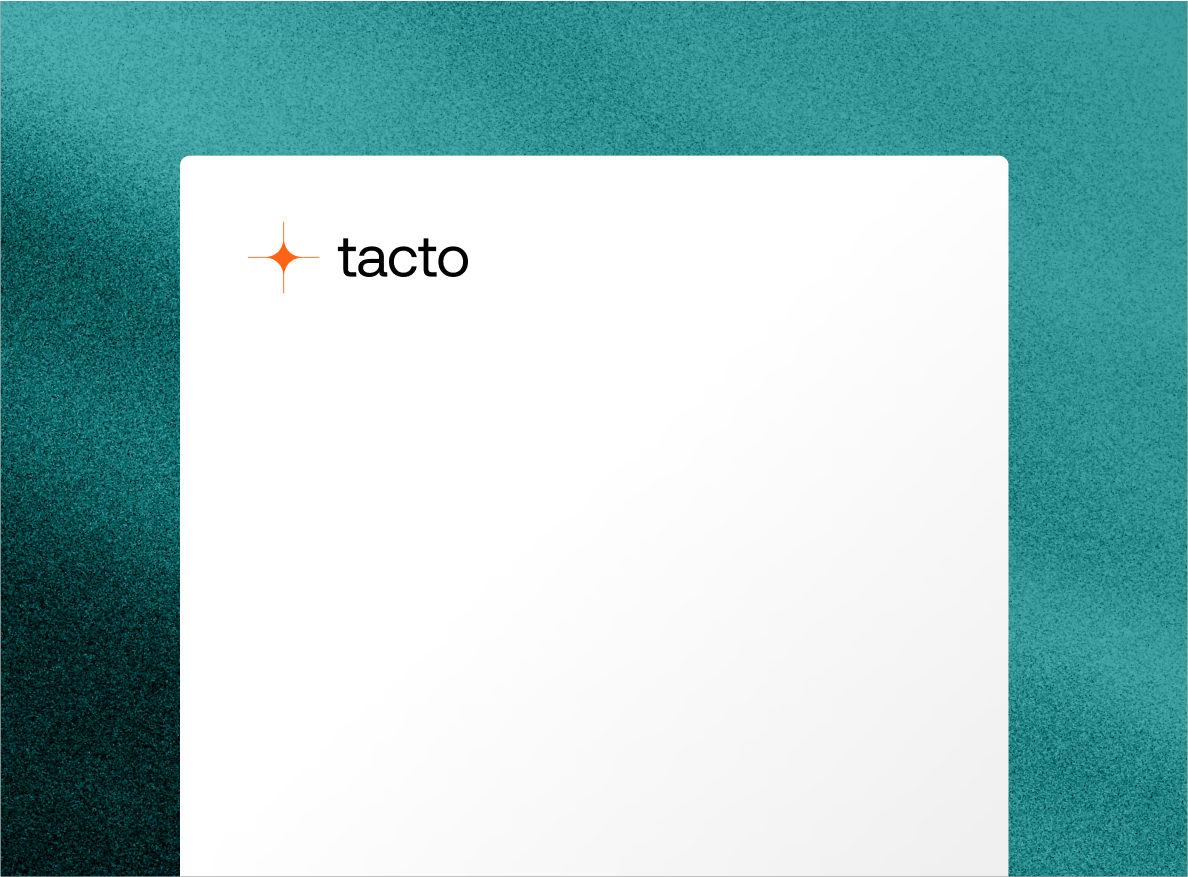