Procurement Glossary
Degree of standardization: definition & important aspects for buyers
The degree of standardization significantly determines the efficiency of procurement processes and directly influences costs, quality and flexibility in Procurement. This overview shows you the various forms of standardization and how you can use them specifically for your procurement strategy.
Level of standardization in a nutshell:
The degree of standardization describes the extent to which products, processes or specifications are standardized and aligned with defined norms. In Procurement , a high degree of standardization makes it possible to reduce complexity, improve the negotiating position and achieve economies of scale.
Example: A car manufacturer increases the degree of standardization of its screw types from 47 to 12 variants, reducing the number of suppliers from 8 to 3 and achieving a cost saving of 23% within one year.
Degree of standardization: An introduction
The degree of standardization is an important concept in modern business and production that describes the standardization of processes, products and services. It indicates the extent to which certain elements are aligned with defined norms and standards. Standardization plays a central role in the optimization of work processes, quality assurance and cost savings in companies. In this introduction, we will take a closer look at the various aspects of the degree of standardization, its significance for the economy and the advantages and disadvantages of increasing standardization.
What is the degree of standardization?
The degree of standardization indicates the extent to which products, processes or services are standardized within a company or between different companies. In Procurement , the degree of standardization refers to the extent to which procurement objects and processes are designed according to uniform standards. A high degree of standardization leads to more efficient processes, facilitates cooperation with suppliers and can reduce costs.
Core elements of the degree of standardization
- Product standardization: standardization of materials and components to reduce diversity and leverage economies of scale
- Process standardization: Uniform procurement processes and procedures for consistent workflows
- Document standardization: use of standard contracts, specifications and forms to simplify communication
- Supplier standardization: cooperation with selected suppliers according to defined criteria and standards
Significance for Procurement
A high degree of standardization in Procurement is crucial for increasing a company's efficiency and competitiveness. Standardization can speed up processes, reduce costs and guarantee quality standards. It also facilitates the integration of supply chains and promotes close cooperation with strategic suppliers.
- Cost savings: Reduction of procurement costs through volume bundling and lower variance
- Process optimization: Simplified and faster processes thanks to standardized procedures
- Quality assurance: Consistent product and service quality through defined standards
- Risk minimization: Reduction of sources of error and delivery bottlenecks through clear specifications
Degree of standardization: From individual procurement to digital standardization
The degree of standardization in the purchasing strategy has become a key success factor for companies. The starting point was often individual procurement costs with a high number of variants, which resulted in complex processes and increased costs. The need to work more efficiently and achieve competitive advantages has paved the way for a transformation to standardized procurement processes. By increasing the degree of standardization, companies can optimize their purchasing processes, achieve cost savings and ensure the quality of the goods procured.
Old: Individual procurement
Traditional approach: In the past, procurement was often characterized by individual orders in which each part and each service was specifically requested. This led to a large number of variants and a complex supplier landscape. The lack of standardization made it difficult to compare offers and increased the administrative effort. Tools and processes were mostly manual and paper-based, which led to inefficiencies and susceptibility to errors. The main challenges were high procurement costs, long lead times and the difficulty of reliably ensuring quality and delivery dates.
New: Digital standardization
Digital standardization: The modern approach relies on digital technologies to increase the degree of standardization. Electronic procurement systems (e-procurement) and digital catalogs are used to define and process products and services according to fixed standards. Key innovations include automated order processing, electronic data interchange formats (EDI) and the integration of supplier systems. This enables efficient process handling, better data quality and increased transparency in the digital supply chain. Practical benefits include reduced costs, faster response times and improved collaboration with suppliers.
Practical example: Optimization in mechanical engineering
A medium-sized mechanical engineering company implemented a digital procurement system to increase the degree of standardization. By introducing electronic catalogs and standardizing parts, the number of different components was reduced by a third. This led to a significant reduction in storage costs and simplified production processes. At the same time, the relationship with suppliers improved thanks to clearly defined specifications and automated ordering processes. Overall, procurement costs were significantly reduced and production times shortened.
Conclusion on the degree of standardization
Standardization in Procurement is a key lever for increasing efficiency and saving costs. By systematically standardizing products, processes and documents, companies can not only optimize their operational processes, but also strengthen their negotiating position with suppliers. Despite initial challenges during implementation, the long-term benefits such as reduced complexity, improved quality control and increased competitiveness outweigh the costs. The key to success lies in striking the right balance between standardization and the necessary flexibility as well as the consistent involvement of all stakeholders.
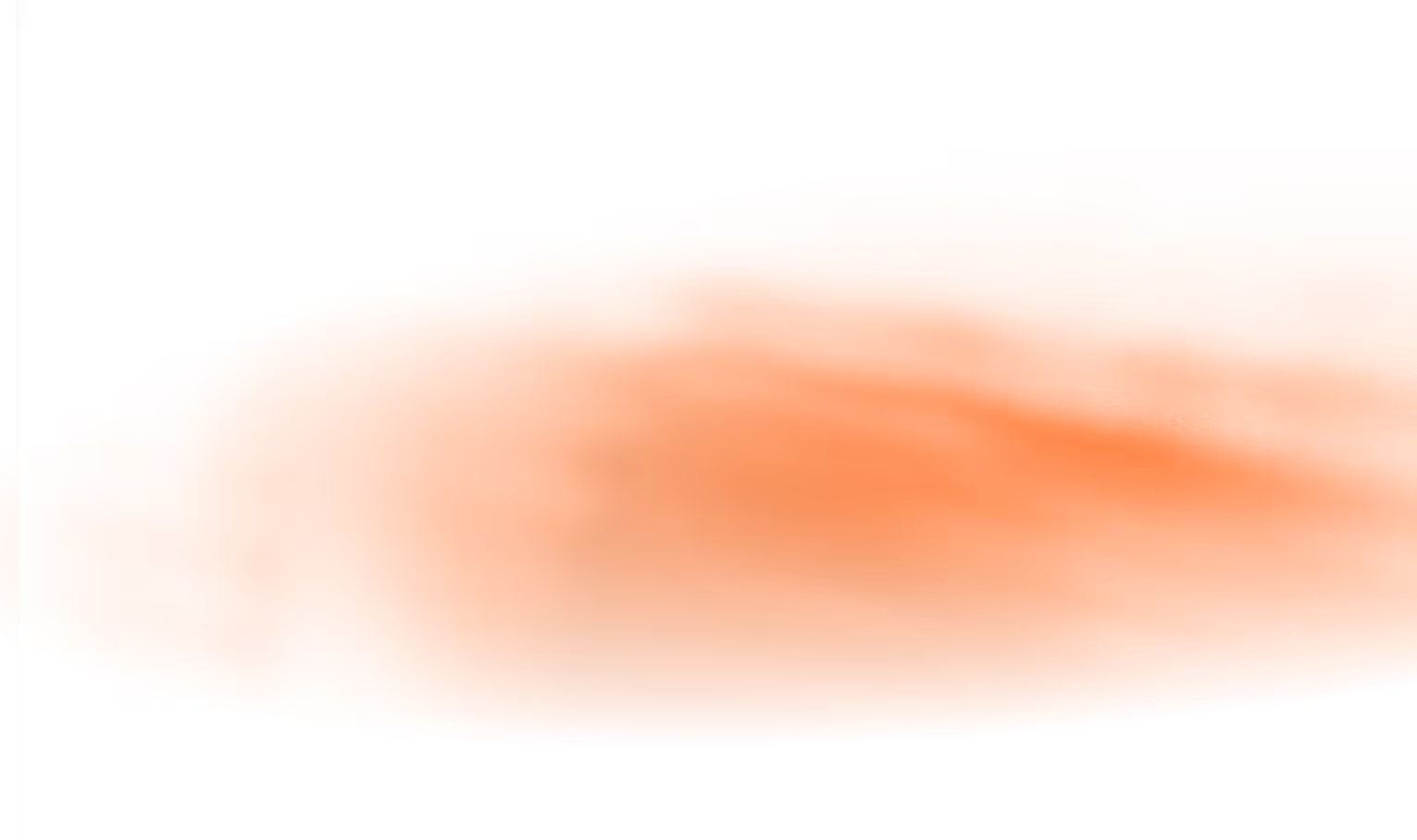
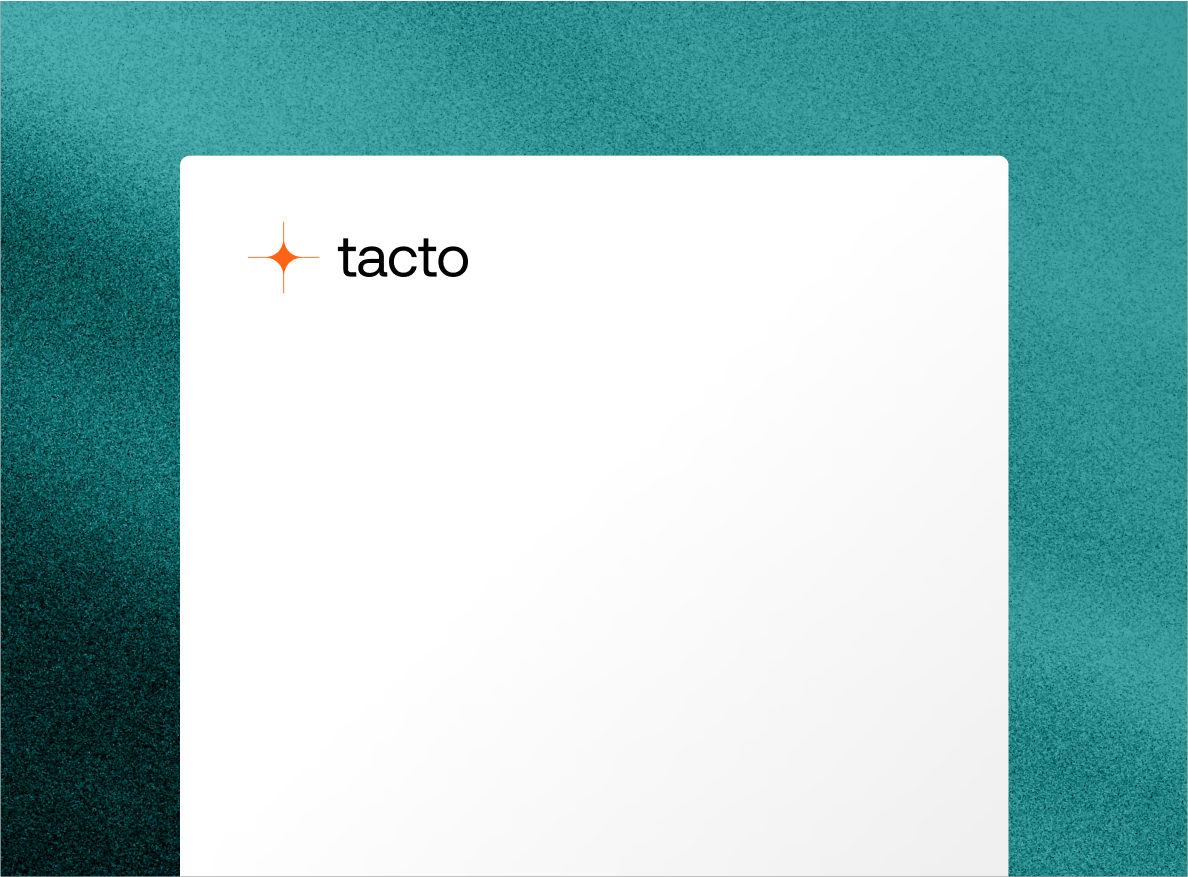