Procurement Glossary
Scheduling: definition & important aspects for buyers
Effective scheduling is the foundation for successful procurement processes and prevents costly delays in the supply chain. This structured overview shows you how to professionally plan, monitor and manage deadlines as a buyer - for greater efficiency and reliability in your projects.
Scheduling in a nutshell:
Scheduling is the systematic determination and coordination of activities and milestones within a defined time frame. For Procurement , it enables the timely procurement of materials, adherence to delivery deadlines and optimal coordination with internal suppliers.
Example: An automotive supplier plans the procurement of critical electronic components with a lead time of 16 weeks by scheduling the order date 20 weeks before the start of production and defining weekly milestones for ordering, production release and goods receipt.
Scheduling in purchasing controlling
Scheduling is a fundamental component of modern project management and efficient work organization. It is used for the systematic planning, coordination and monitoring of schedules in companies, projects and in the personal sphere. Well thought-out scheduling enables resources to be used optimally, deadlines to be met and processes to be coordinated smoothly. In this introduction, you will learn the most important basics of scheduling, get to know various methods and tools and receive practical tips for successful implementation in everyday working life.
What is scheduling?
Scheduling in Procurement refers to the systematic coordination of all time-related aspects within the procurement process. It includes the planning of order times, delivery dates and internal processing times to ensure a smooth process. Effective scheduling ensures that the required materials and services are available at the right time and in the right quantity.
Core elements of scheduling
Significance for Procurement
Scheduling is a central component of purchasing, as it contributes significantly to the efficiency and reliability of the supply chain. Effective scheduling helps to avoid bottlenecks, optimize stock levels and reduce costs. It enables purchasers to react flexibly to changes in the market and ensure that internal and external customers are kept to deadlines.
Scheduling: From manual processes to Advanced Planning and Scheduling (APS)
Building on the theoretical foundation of scheduling in Procurement , it is essential to understand the practical aspects of this concept. In today's dynamic business environment, efficient scheduling is crucial to ensure competitiveness and customer satisfaction. However, traditional manual scheduling is reaching its limits, which is why modern approaches are needed to meet the increasing demands.
Old: Manual scheduling
Traditional approach: In the past, scheduling was mainly done manually. Buyers used spreadsheets or simple ERP systems to coordinate order and delivery dates. Updating delivery deadlines was based on personal phone calls or emails with suppliers. This method was time-consuming and error-prone. Responding to changes, such as delays in the supply chain or sudden fluctuations in demand, was difficult. The lack of real-time visibility often led to overstocking or material shortages, which impacted the efficiency of the entire supply chain.
New: Advanced Planning and Scheduling (APS)
Advanced planning and scheduling: Modern scheduling uses advanced planning and scheduling (APS) systems that enable integrated and automated planning. By linking ERP systems with real-time data from suppliers, the entire supply chain can be displayed transparently. APS systems take into account various parameters such as production capacities, delivery times, stock levels and demand forecasts in order to calculate optimal order times and quantities. Artificial intelligence and machine learning improve forecasts and enable proactive adaptation of planning in the event of changes. This leads to greater efficiency, reduces storage costs and minimizes the risk of delivery bottlenecks.
Practical example: Automotive industry
A leading car manufacturer implemented an APS system to optimize its scheduling. Thanks to the real-time link with suppliers, the average storage time for parts was reduced by 20%. Supplier notifications of delays were automatically taken into account and the production plan was adjusted accordingly. This led to a 15% reduction in production downtime and cost savings of several million euros per year. The improved efficiency enabled the company to react more quickly to market changes and increase customer satisfaction.
Conclusion on scheduling
Scheduling is an indispensable tool in modern Procurement that increases the efficiency of the entire supply chain by systematically coordinating order times and delivery dates. Successful implementation requires precise demand forecasts, reliable supplier management and digital support. Only by integrating all relevant factors and using modern technologies can companies secure their competitiveness and optimize costs at the same time.
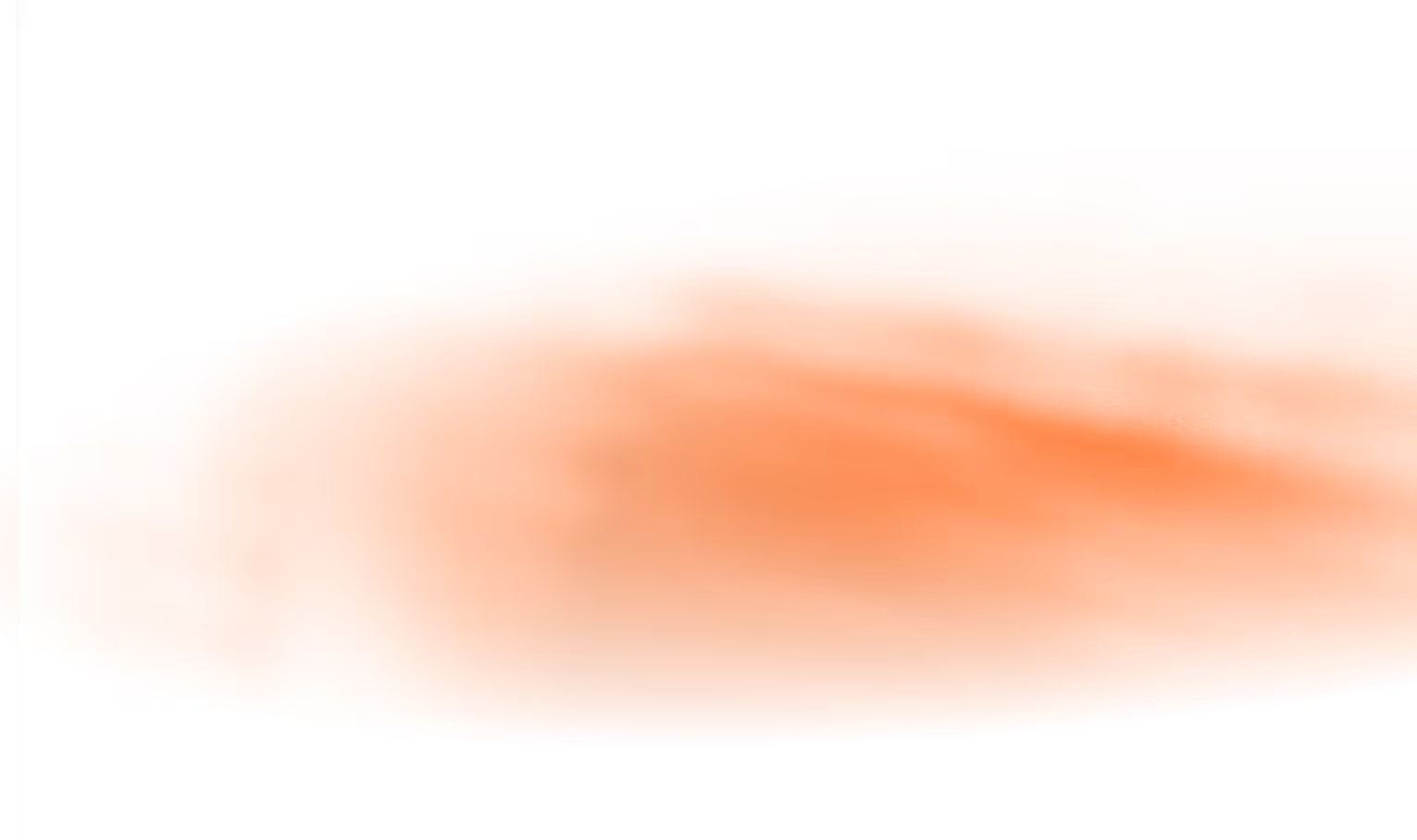
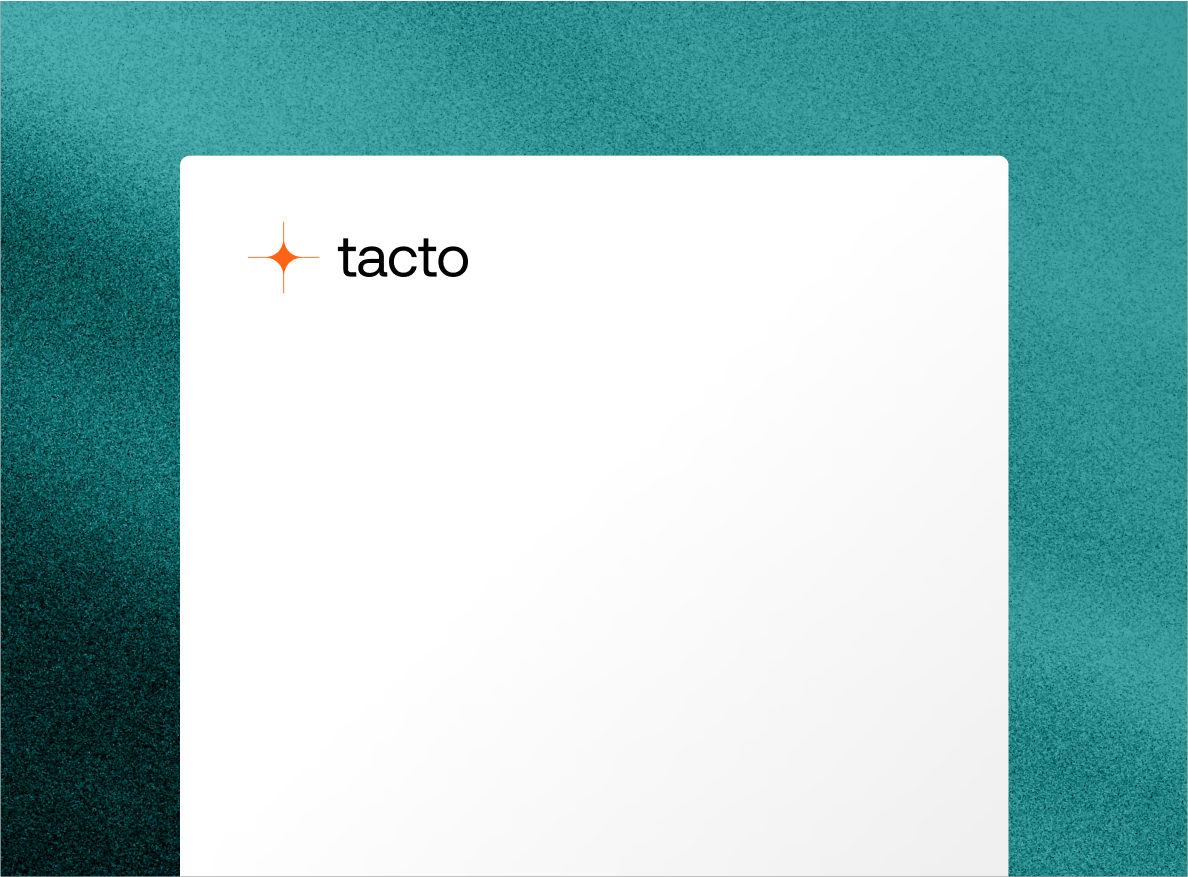