Procurement Glossary
Compliance in Procurement: definition, importance & implementation in procurement
Compliance in Procurement encompasses adherence to legal regulations and internal company guidelines in all procurement processes and is essential today for sustainable, legally compliant purchasing practices. In a time of increasing regulatory requirements and complex global supply chains, strategic compliance management not only offers protection against legal risks, but also creates competitive advantages through increased transparency and efficiency in supplier relationships.
What is compliance in Procurement?
Compliance in Procurement refers to the systematic assurance of adherence to laws, guidelines and internal company codes of conduct within all procurement processes. It includes measures to avoid breaches of rules and legal risks and to maintain ethical standards in supplier relationships, thereby protecting the integrity of procurement processes and protecting the company from corruption, fraud and reputational damage.
Introduction to Compliance Procurement
Historical development and current significance
The issue of compliance in Procurement has evolved considerably in recent decades. Around ten years ago, compliance in Procurement focused primarily on avoiding agreements with preferred partners, bribery and so-called maverick buying - purchases made outside the official purchasing department. Today, compliance in Procurement encompasses a much broader spectrum of requirements.
As the central interface between internal departments and external suppliers, Procurement occupies a key position in the value chain. This position entails particular responsibility, as numerous compliance risks can arise here. Due to the increasing density of regulation at national, European and global level, compliance is becoming increasingly important for Procurement . Companies must ensure that all employees in Procurement comply with legal regulations in order to avoid legal consequences and sanctions that could jeopardize their existence.
Compliance in Procurement makes a significant contribution to this:
- Avoid financial losses due to fines or claims for damages
- Averting reputational damage
- Strengthening the trust of stakeholders
- Ensuring fair competitive conditions
- Building sustainable business relationships
Core areas of compliance in Procurement
In modern Procurement , compliance covers several core areas, each of which entails specific requirements and challenges:
- Anti-corruption and bribery prevention: Purchasers are in an exposed position as they decide on the awarding of contracts. This makes them vulnerable to bribery attempts. Effective compliance management must define clear guidelines for dealing with gifts, invitations and other benefits. The introduction of the dual control principle and regular reviews of supplier relationships help to minimize corruption risks.
- Competition law and ban on cartels: Buyers must ensure that their actions do not violate competition law. This includes the prohibition of price fixing with or between suppliers and the avoidance of abuse of market power. At the same time, buyers must be in a position to recognize possible violations of competition law on the supplier side, for example if potential suppliers have agreed offer prices with each other.
- Supply Chain Act and sustainable procurement: With the introduction of the Supply Chain Duty of Care Act (LkSG) in Germany and comparable regulations at European level (Corporate Sustainability Reporting Directive, CSRD), companies are obliged to ensure human rights and environmental standards along their supply chain. Procurement must implement appropriate due diligence processes in order to identify risks at an early stage and take suitable measures.
- CO₂ border adjustment mechanism (CBAM) and climate protection: The CO₂ border adjustment mechanism places new demands on procurement, particularly for products from third countries. Buyers must consider the CO₂ intensity of their supply chain and collect the relevant data. This requires close cooperation with suppliers and robust data management systems.
- Data protection and information security: The exchange of sensitive data with suppliers requires compliance with data protection regulations such as the GDPR. Buyers must ensure that suppliers have implemented appropriate technical and organizational measures to protect personal data.
- Compliance risks in the purchasing process: Various compliance risks can occur along the entire purchasing process:
- Determining requirements and specifications: Compliance risks can already arise when defining purchasing requirements, for example if specifications are tailored to a specific supplier and competition is restricted as a result.
- Supplier selection and qualification: The selection of suitable suppliers must be based on transparent, objective criteria. Insufficient supplier screening can lead to violations of anti-corruption laws, environmental standards or labor law.
- Contract design and management: Contracts must contain legally compliant clauses that clearly define compliance requirements for suppliers. Systematic contract management helps to monitor compliance with these requirements.
- Order processing and invoice verification: Manipulation during order processing or unjustified price increases represent compliance risks. A structured invoice audit can reduce such risks.
- Modern compliance management in Procurement: To manage compliance risks effectively, modern companies rely on a systematic approach:
- Risk-based approach: Effective compliance management in Procurement is based on continuous risk analysis. This involves categorizing business relationships according to their risk potential in order to deploy resources in a targeted manner.
- Clear guidelines and processes: Companies should develop specific compliance guidelines for Procurement that provide clear instructions for action in different situations. These guidelines must be updated regularly and made available to employees.
- Training and awareness-raising: Regular compliance training for purchasing employees is crucial in order to raise awareness of compliance risks and impart skills for action. These training sessions should be practice-oriented and use specific case studies to illustrate the relevance of compliance in day-to-day work.
- Monitoring and control: Continuous monitoring of purchasing processes helps to identify compliance violations at an early stage. Regular audits and spot checks are important instruments of compliance monitoring.
Digitalization and compliance in Procurement
Digitalization plays a decisive role in effective compliance management in Procurement. Traditional, manual compliance processes are reaching their limits in view of the increasing complexity of regulatory requirements and global supply chains.
Advantages of digital compliance solutions
Modern SRM (Supplier Relationship Management) systems offer comprehensive functionalities to support compliance processes in Procurement:
- Automated compliance checks during supplier selection
- Central documentation of all compliance-relevant information
- Structured processes for compliance due diligence
- Real-time monitoring of compliance risks
- Automated reporting for regulatory requirements
An integrated SRM system that links Procurement and compliance is not just a technological investment, but a strategic decision for long-term success. By consolidating data from ERP systems and Office applications, these solutions create transparency at the touch of a button and provide a sound basis for decision-making in supplier development.
From manual to digital processes
In the past, compliance checks in Procurement were mainly carried out manually. Procurement staff checked suppliers and contracts for compliance-relevant aspects, often using checklists and paper-based procedures. Information was exchanged by email or fax and documentation was archived in physical folders. This approach was time-consuming and prone to human error. In addition, decentralized data storage made it difficult to maintain transparency and respond quickly to compliance violations.
Modern companies, on the other hand, rely on digital compliance management systems (CMS), which offer the following advantages:
- Reduction of manual effort through automation
- Higher data quality and consistency
- Improved transparency and traceability
- Faster response to new regulatory requirements
- Better integration into existing business processes
Practical example: Efficient compliance management at Harro Höfliger
The company Harro Höfliger provides a successful example of the implementation of modern compliance management in Procurement . The company was faced with the challenge of efficiently coping with increasing regulatory requirements such as the Supply Chain Due Diligence Act (LkSG) and the CO₂ Border Adjustment Mechanism (CBAM).
Initial situation and challenges
Harro Höfliger was confronted with complex supply chains and a large number of suppliers. The manual implementation of compliance requirements was reaching its limits, particularly in terms of:
- Incomplete information about suppliers
- Time-consuming individual solutions for various compliance requirements
- Lack of transparency in the supply chain
- Inefficient communication with suppliers
Implemented solution
To overcome these challenges, Harro Höfliger implemented a central SRM platform that intelligently combines Procurement and compliance. The company pursued a step-by-step approach:
- First, basic requirements such as the LkSG were mapped
- Additional modules such as CBAM were then integrated
- Implementation was carried out in close cooperation with suppliers in order to create transparency and identify potential hurdles at an early stage
Results achieved
By introducing the central SRM solution, Harro Höfliger was able to achieve the following improvements:
- Automation of supplier communication
- Central management of master data
- Compliance with regulatory requirements without manual effort
- Significant reduction in workload
- Increased transparency in the supply chain
- Proactive integration of new regulatory requirements
The successful implementation of CBAM and LkSG has provided Harro Höfliger with a solid basis for future requirements. The company is now well equipped for upcoming regulations such as the Corporate Sustainability Reporting Directive (CSRD) or the EU Supply Chain Directive (CSDD).
Practical example: Continental Automotive
Continental Automotive offers another example of successful compliance implementation in Procurement . The company set itself the goal of ensuring 100% compliance in Procurement .
The challenge
Continental Automotive was faced with the task of establishing compliant Procurement processes without compromising the efficiency of its procurement processes. The company needed a solution that:
- Creates transparency in all procurement processes
- Ensures compliance with internal and external requirements
- Collaboration with suppliers standardized
- Reduced administrative effort
Implemented approach
Continental Automotive opted for a sourcing solution that offers purchasing organizations an optimal technological basis for the introduction of rule-compliant processes. The company recognized that a suitable tool is only part of the solution and systematically implemented the software in its purchasing processes.
The implementation approach included:
- Standardization and centralization of processes, contracts and master data
- Integration into existing ERP systems
- Training of purchasing staff
- Continuous monitoring and improvement
Results
By consistently implementing the sourcing solution, Continental Automotive was able to achieve the following results:
- Greater transparency in all procurement processes
- Reduction of compliance risks
- Improved cooperation with suppliers
- Increased efficiency through standardized processes
- Better data basis for strategic decisions
These case studies show that successful compliance in Procurement requires a combination of suitable technological solutions, clear processes and an appropriate corporate culture.
Conclusion: Compliance in Procurement as a strategic competitive advantage
In today's complex procurement landscape, compliance in Procurement is no longer just a mandatory task to avoid legal risks, but a strategic success factor. By integrating compliance principles into the procurement process, companies can reduce risks, ensure fair competitive conditions and build sustainable business relationships. The increasing density of regulation at national and international level and the growing demands for transparency and sustainability in the supply chain make systematic compliance management in Procurement essential. Modern SRM systems that combine Procurement and compliance offer companies the opportunity to overcome these challenges efficiently and at the same time strengthen the strategic role of procurement. For procurement managers, this means seeing compliance not as an obstacle, but as an opportunity - an opportunity to achieve long-term competitive advantages through transparency, integrity and sustainability in procurement and to protect the company from legal and reputational risks.
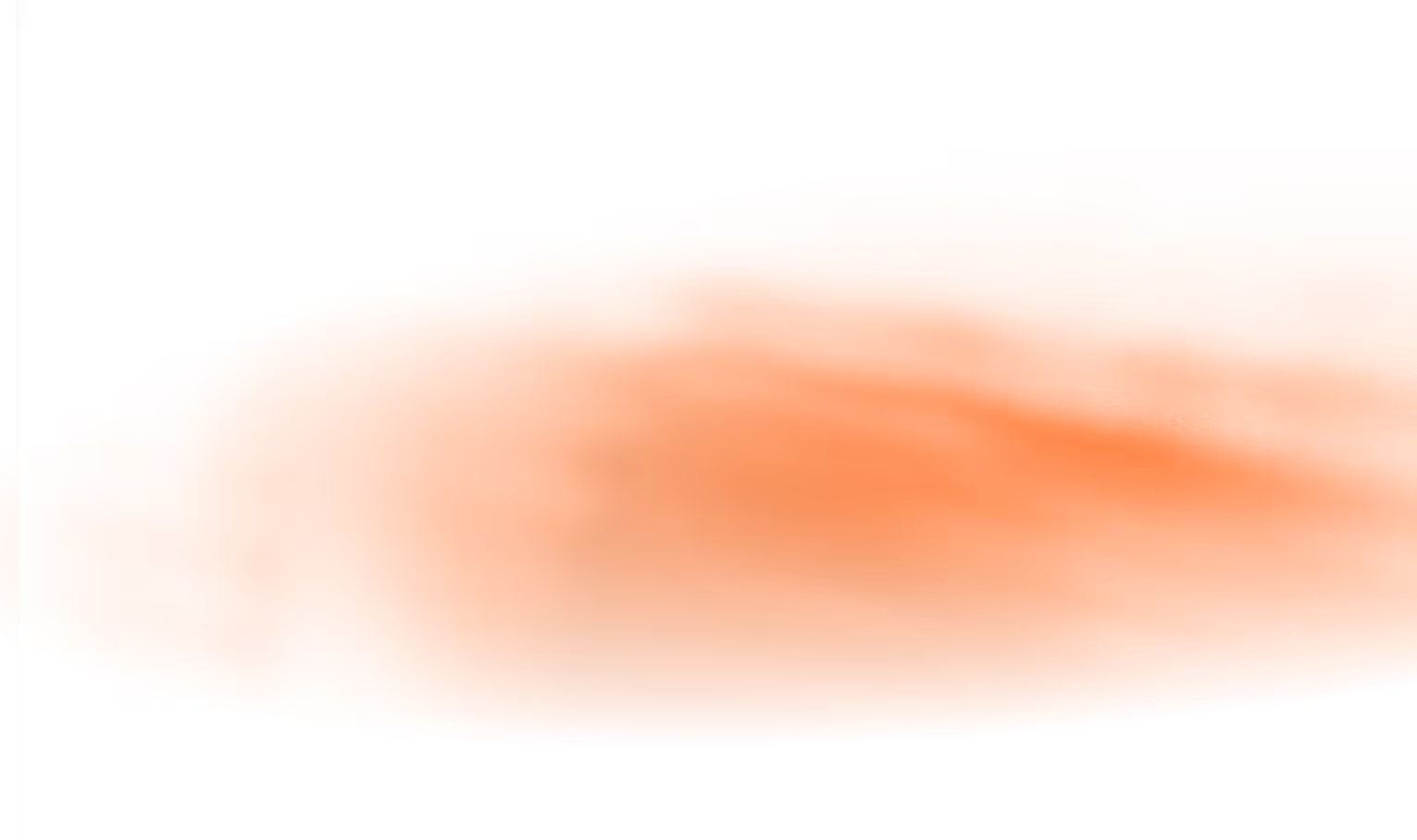
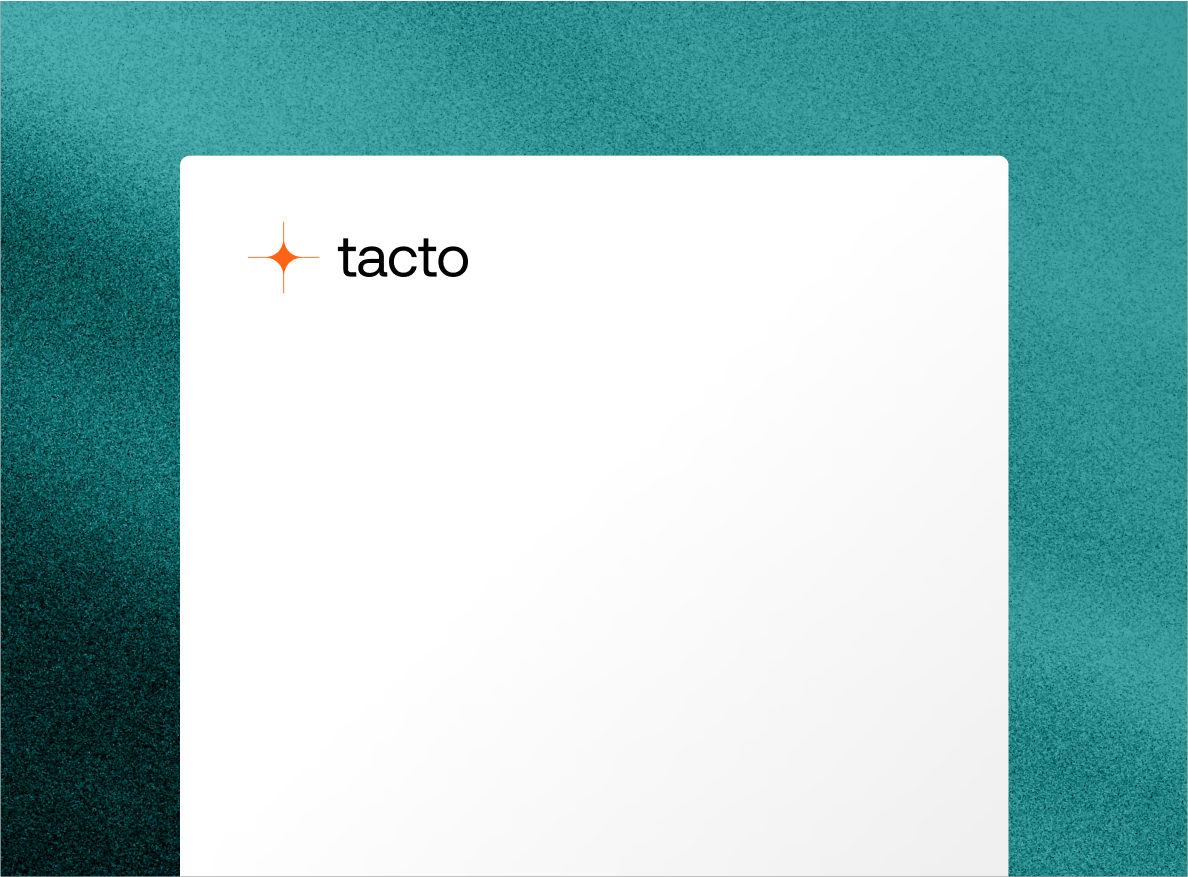