Procurement Glossary
Cross-sectional sourcing: definition & important aspects for buyers
Cross-functional sourcing is revolutionizing traditional procurement through the systematic collaboration of all relevant corporate divisions, thereby creating sustainable competitive advantages. This structured guide shows how Procurement generates maximum added value for the company through cross-functional strategies and processes.
Cross-functional sourcing in a nutshell:
Cross-functional sourcing describes a cross-departmental procurement approach in which experts from different areas of the company make joint procurement decisions. This approach enables Procurement to achieve optimal supplier selection and product specifications by integrating different specialist skills.
Example: When procuring a new production system, a team from Procurement, Production, Quality and Technology works together for 6 months, which not only achieves 15% cost savings, but also shortens the implementation time by 4 weeks.
Introduction to cross-functional sourcing
Cross-functional sourcing is a modern and holistic approach to strategic Procurement in which different company divisions and specialist departments work closely together to make optimal procurement decisions. This cross-departmental process brings together different perspectives, skills and requirements to achieve the best possible procurement results. In today's complex business world, cross-functional sourcing is becoming increasingly important as it enables companies to leverage synergies, drive innovation and develop competitive solutions. In this guide, you will learn about the most important aspects of cross-functional sourcing, from the basics to practical implementation in day-to-day business.
What is cross-functional sourcing?
Cross-functional sourcing refers to a collaborative approach to Procurement in which different departments of a company work together on procurement processes. By involving specialists from areas such as production, development, quality management and finance, decisions in Procurement are made in a more versatile and well-founded manner. This interdisciplinary approach promotes efficiency, reduces risks and helps to optimize the entire supply chain.
Core elements of cross-functional sourcing
Significance for Procurement
In Procurement , cross-functional sourcing enables a holistic view of procurement decisions. By working closely with other departments, buyers can ensure that products and services are not only cost-efficient, but also of high quality and functionally appropriate. This leads to improved supplier relationships, reduced risk of procurement errors and contributes significantly to the company's added value.
Cross-functional sourcing: from functional Procurement to cross-departmental procurement
The change in procurement strategies reflects the increasing complexity and dynamics of global markets. Based on a theoretical foundation that emphasizes the importance of interdisciplinary collaboration, it becomes clear why traditional procurement approaches are reaching their limits. In order to meet the diverse requirements, companies need to broaden their focus and integrate the expertise of different specialist areas. This need for transformation is central to remaining competitive and promoting innovative solutions.
Old: Functional Procurement
Traditional approach:
In functional Procurement , procurement responsibility lay primarily with the purchasing organization, which operated in isolation from other areas of the company. In practice, this meant that buyers made decisions based on price and availability without having in-depth insight into technical specifications or production requirements. Tools such as simple price comparison lists and supplier evaluation were common. The main characteristics of this approach were limited communication and few interfaces with other departments. The challenges were a lack of innovation, longer procurement cycles and the risk of wrong decisions due to incomplete information.
New: Cross-functional sourcing
Cross-Functional Sourcing:
The modern approach of cross-functional sourcing is revolutionizing procurement by integrating different departments into the purchasing process. In practice, this means that teams from Procurement, Development, Quality Assurance and Finance develop procurement strategies together. Innovation-promoting tools such as collaborative software platforms and data-driven decision support are used. This approach is characterized by increased transparency, improved communication and holistic decision-making. The benefits are faster product launches, cost savings through optimized processes and higher product quality through integrated quality standards.
Practical example: Implementation at an electronics manufacturer
A global electronics manufacturer introduced cross-functional sourcing to shorten its product development cycles. By forming interdisciplinary teams, procurement decisions could be accelerated and better aligned with market requirements. Specifically, this led to a reduction in the time-to-market by 25 %. In addition, production costs were reduced by 12% as cost-driving factors were identified and eliminated at an early stage. Close cooperation with quality assurance resulted in a 30% reduction in warranty costs within the first two years of the new approach being introduced.
Conclusion on the cross-functional sourcing strategy
Cross-functional sourcing is proving to be an indispensable approach for modern companies, leading to better procurement decisions through collaboration between different departments. The integration of different areas of expertise not only optimizes procurement processes, but also increases the quality of results and reduces risks. Despite challenges such as longer decision-making paths and potential conflicts of interest, the benefits clearly outweigh the disadvantages. Clear structures, effective communication and the use of digital technologies are crucial for long-term success.
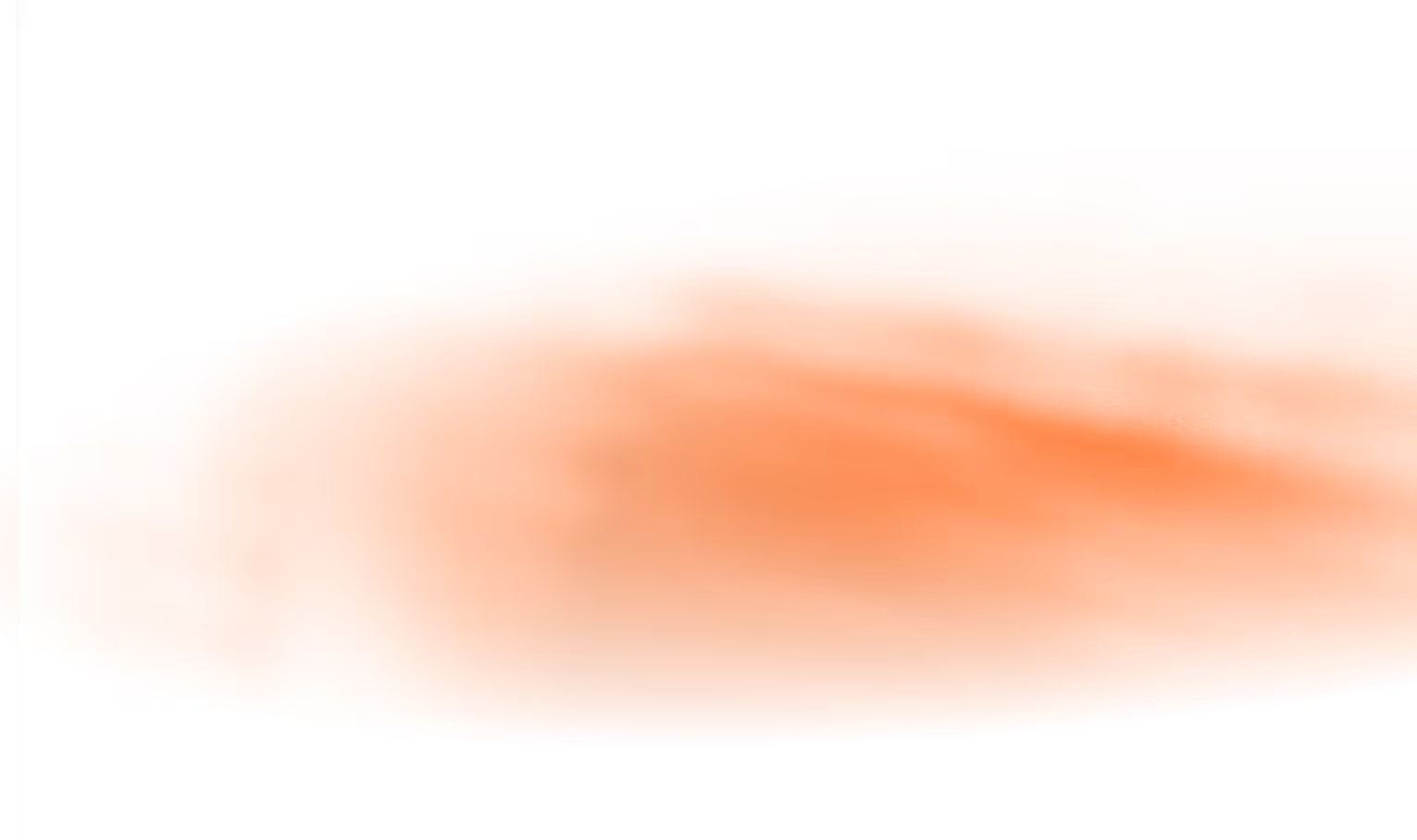
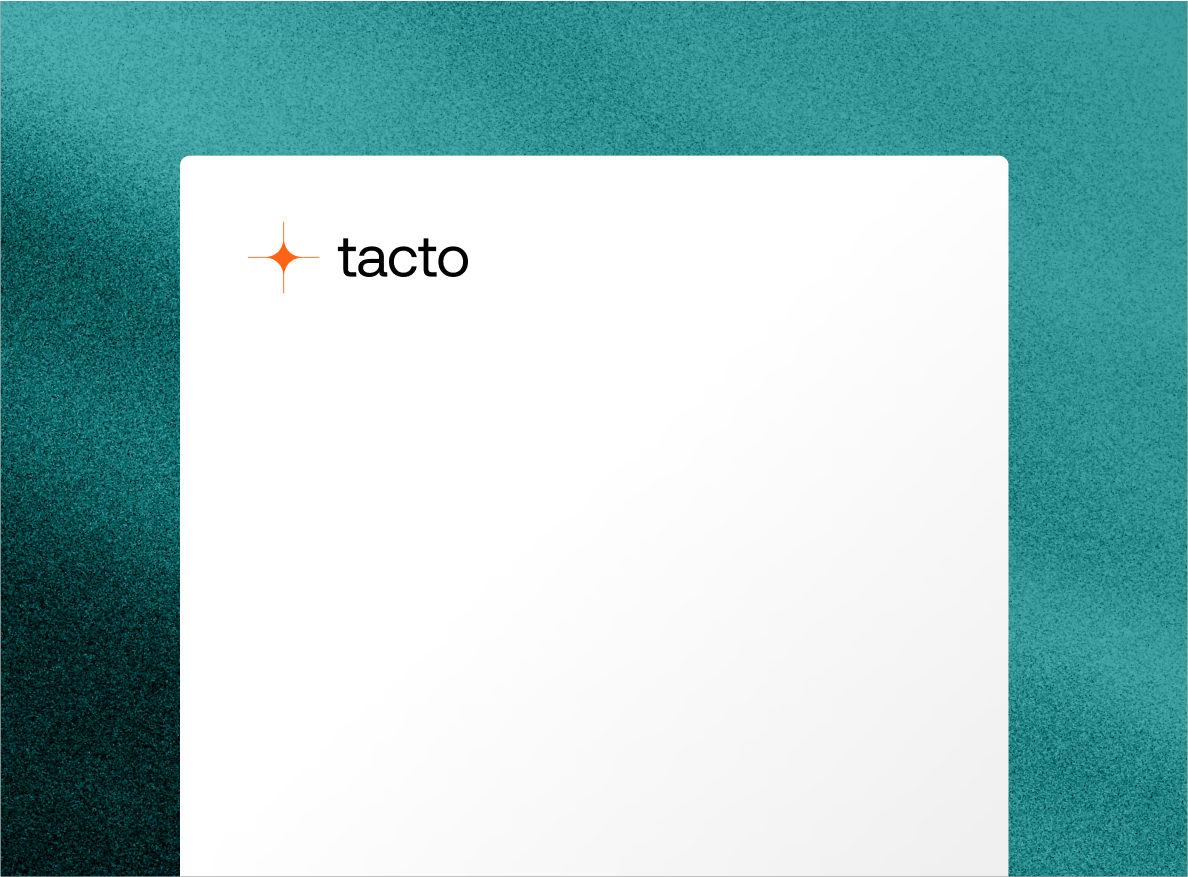