Procurement Glossary
Rush order: definition and important aspects for buyers
Rush orders enable the rapid procurement of urgently needed materials and help companies to avoid critical bottlenecks. This overview systematically shows the most important aspects for Procurement - from correct prioritization to efficient processing of rush orders.
Rush order to the point:
An express order is an urgent procurement request that is processed with the highest priority outside of the regular ordering process. For Procurement , this means increased process costs and surcharges, which is why effective rush order management is essential to minimize unplanned express orders.
Example: An automotive supplier has to procure a spare part within 24 hours due to an unplanned machine downtime, resulting in express surcharges of EUR 250 and special travel costs of EUR 180 in addition to the regular parts price of EUR 800.
Express order - An introduction
Rush orders are an important tool in the operational procurement process of companies. It is used when materials or goods are urgently needed and the normal ordering process would be too time-consuming. Rush orders are often associated with higher costs, but can be necessary in critical situations to avoid production downtime or to fulfill important customer orders on time. In this guide, you will learn about the key aspects of rush orders, from the reasons for placing them to the associated challenges and optimization opportunities in the procurement process.
What is a rush order?
In Procurement , a rush order refers to the short-term procurement of goods or services that takes place outside of the regular procurement process. These orders are characterized by an urgent need and require fast processing in order to meet the company's time-critical requirements. Urgent orders often become necessary when unexpected events occur, such as machine breakdowns, sudden orders or stock shortages.
Key elements of rush orders
Importance of rush orders in Procurement
In procurement management, rush orders are an important tool for reacting flexibly to unexpected demand situations. They enable companies to avoid production downtimes, fulfill customer orders on time and ensure operational continuity. However, they pose challenges for Procurement , as they are often associated with increased costs and risks.
Express ordering: from manual processes to digital express procurement
Urgent orders are essential for reacting quickly to urgent material or service requirements in unexpected situations. Based on the theoretical understanding of rush orders as unscheduled procurement processes, their immense importance for maintaining operational processes is evident in practice. However, traditional methods often lead to inefficiencies and increased costs, which is why a transformation to modern approaches is necessary.
Old: Manual express order
Traditional approach: In the traditional process, rush orders are initiated manually and often ad hoc. Urgent requirements are transmitted to supplier management by telephone or fax, whereby internal approvals are usually accelerated or bypassed. Communication is direct and personal, but there is often a lack of standardized processes and documentation. This approach is time-consuming, error-prone and leads to a lack of transparency. It also results in higher costs due to express surcharges and a lack of room for negotiation. Manual processing makes it difficult to track and evaluate data, which hinders the efficient management of rush orders.
New: Digital Express Procurement
Express Procurement: Modern companies rely on digital solutions to make urgent orders more efficient. Integrated e-procurement systems automatically record urgent requirements and transfer them into standardized workflows. Electronic approval processes speed up internal approvals, while real-time communication with suppliers takes place via digital platforms. Automated ordering processes minimize sources of error and increase transparency. Key innovations include the use of AI in Procurement for demand forecasts and the integration of supplier portals. The benefits are a significant reduction in procurement time, cost savings through more favorable conditions and an improved database for strategic decisions.
Practical example: Automotive industry
A leading automotive manufacturer implemented a digital express procurement system to manage the frequent rush orders in production. Thanks to automation, rush orders could be processed within 30 minutes instead of the previous 8 hours. Real-time communication with suppliers reduced delivery times by 40%. In addition, preventative analysis led to a 20% reduction in rush orders within a year, resulting in savings of over €2 million.
Conclusion on the express order
Rush orders are an indispensable tool in modern purchasing management, enabling quick reactions to unexpected demand situations. Despite higher costs and risks, they ensure operational continuity and customer satisfaction. The key to successfully handling rush orders lies in the balance between flexible responsiveness and strategic forward planning. Digital solutions and proactive risk management can reduce the number of necessary rush orders in the future.
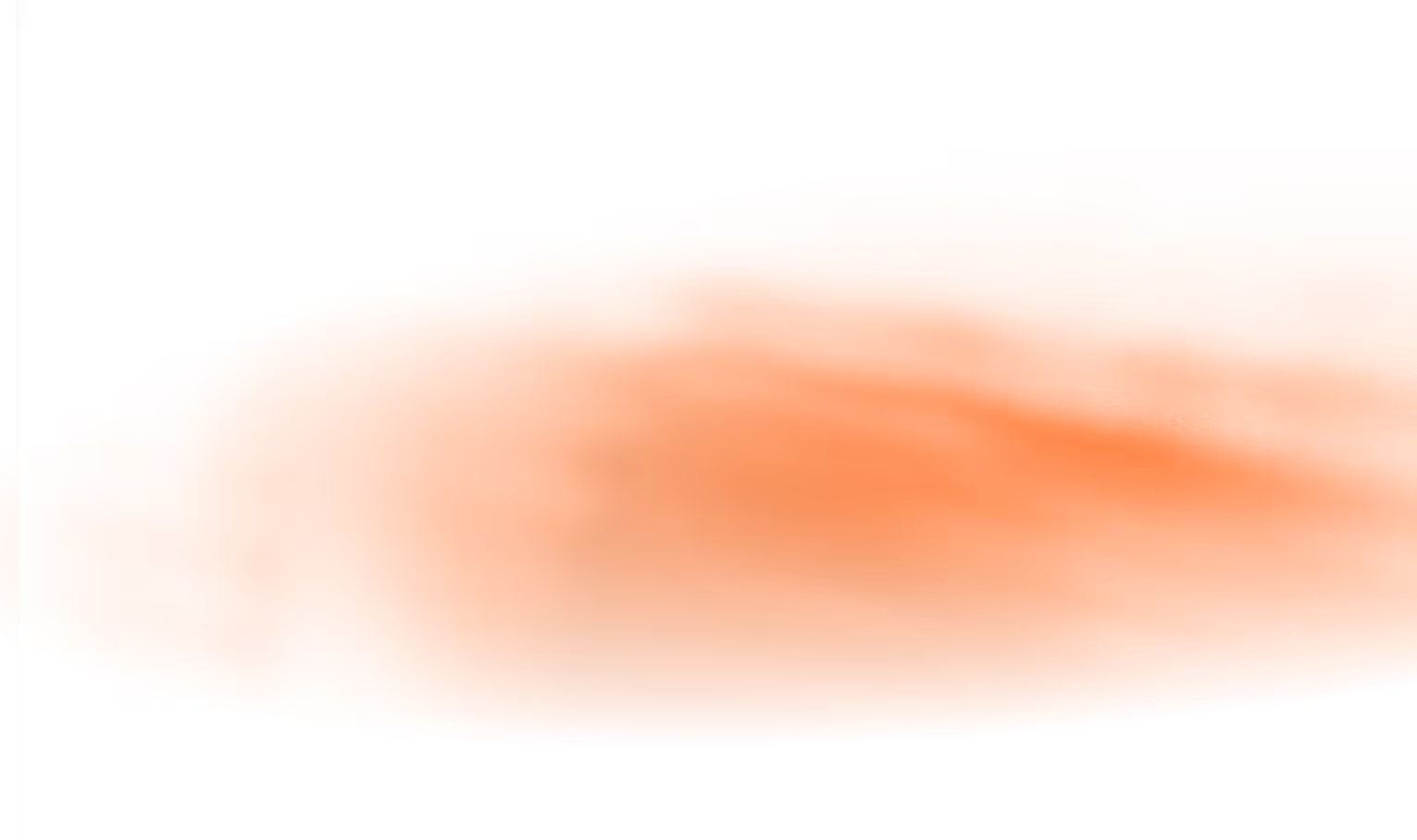
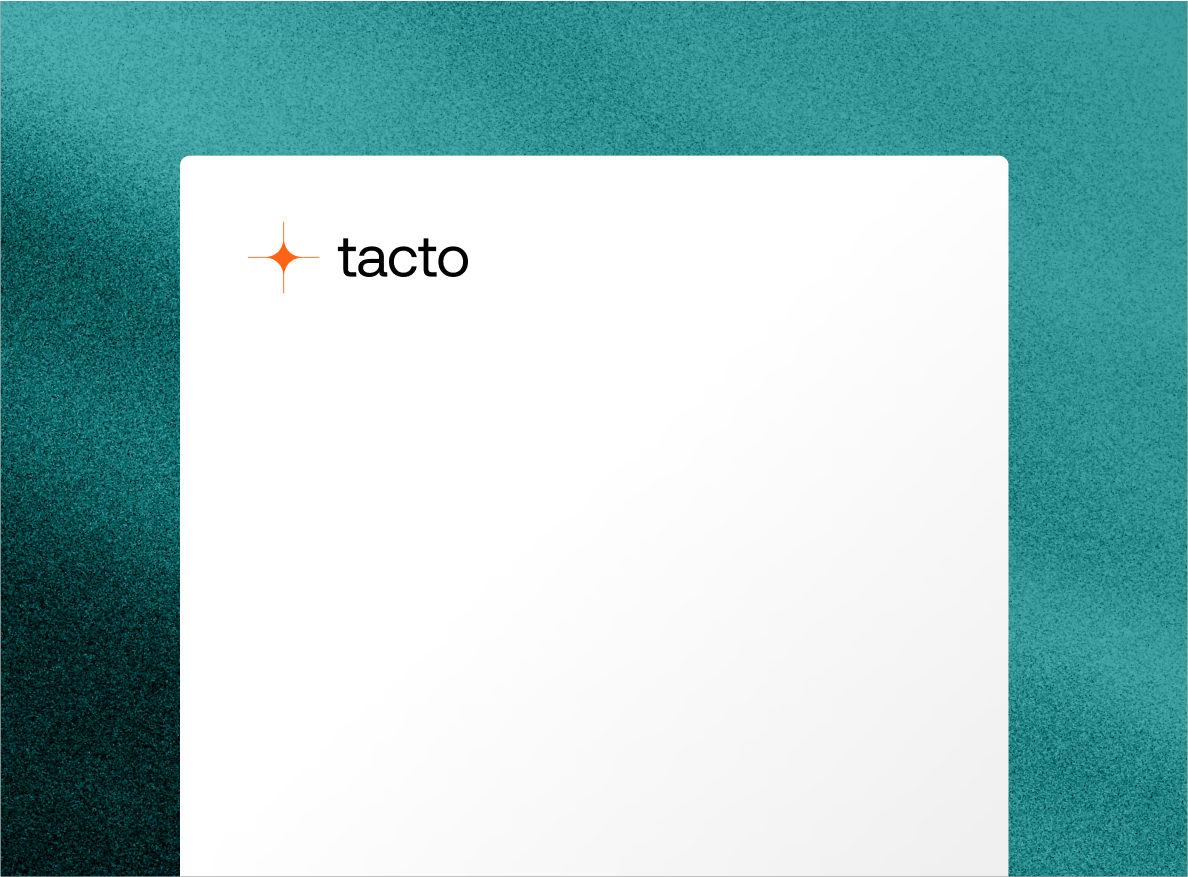