Procurement Glossary
Risk management: definition & important aspects for buyers
Risk management enables companies to identify potential risks at an early stage and take targeted measures to ensure their long-term competitiveness. The following overview systematically shows how you as a buyer can effectively identify, evaluate and manage risks in order to ensure your company's security of supply.
Risk management in a nutshell:
Risk management is the systematic process of identifying, evaluating and managing potential risks and uncertainties in business processes. In Procurement , it enables the early identification and minimization of procurement risks such as supplier defaults, price fluctuations or quality defects through targeted preventive and countermeasures.
Example: An automotive supplier implements an early warning system that evaluates 25 key suppliers on a monthly basis using 8 KPIs (such as delivery reliability, quality ratio, key financial figures) and automatically triggers a three-stage escalation process if defined thresholds are not met.
Risk management: An introduction
In today's increasingly complex business world, risk management is of crucial importance for the sustainable success of companies. It involves the systematic identification, analysis, assessment and management of potential risks that could jeopardize the achievement of corporate objectives. Effective risk management enables organizations to respond proactively to threats and take advantage of opportunities. This guide presents the basic concepts, methods and instruments of risk management and explains their practical application in various areas of the company.
What is risk management in Procurement?
Risk management in Procurement involves the systematic identification, assessment and management of potential risks within the supply chain. The aim is to identify risks to the supply chain at an early stage and to minimize or avoid negative effects on the company through suitable measures. Both internal and external factors are taken into account in order to ensure security of supply and competitiveness.
Core elements of risk management in Procurement
Importance of risk management in Procurement
In a globalized and dynamic market environment, effective risk management is essential for Procurement . It ensures the continuous supply of materials and services, minimizes financial losses and protects the company from reputationally damaging events. Through proactive risk management, companies can increase their resilience and secure competitive advantages.
Risk management: from a reactive to a proactive approach
Risk management in Procurement is now more important than ever to ensure supply chain stability and business continuity. Building on the theoretical foundations, it is clear that traditional methods are no longer sufficient to deal with the complex risks of the modern procurement environment. Therefore, a shift towards proactive and strategic approaches is required to identify potential risks at an early stage and manage them effectively.
Old: Reactive risk management
Traditional approach: In the past, risk management in Procurement was often reactive. Companies only reacted to risks after they had occurred, such as delivery delays or quality defects. Typically, simple tools such as manual checklists or sporadic supplier assessments were used. Communication was often limited to emails or phone calls, without systematic data collection. This approach led to limited transparency and made it difficult to predict risks. The main problems were the lack of predictability of supply chain disruptions and the inability to react quickly to unforeseen events.
New: Proactive risk management
Risk mitigation strategies: Modern approaches to risk management rely on proactive strategies and the use of advanced technologies. By integrating real-time data analysis, AI in Procurement and automated monitoring systems, companies can identify potential risks at an early stage. Innovative tools enable the continuous monitoring of supplier performance, market trends and geopolitical events. These methods not only improve risk prediction, but also allow scenarios and contingency plans to be developed. Practical benefits include reduced supply disruptions, improved cost efficiency and increased supply chain resilience. Companies can therefore react more quickly to changes and act more competitively.
Practical example: Automotive industry
A global automotive manufacturer implemented a proactive risk management system that uses AI-supported analyses and real-time data from over 500 suppliers. Within a year, the number of unforeseen supply bottlenecks was reduced by 40%. Annual savings of 10 million euros were achieved by identifying risks at an early stage. The response time to potential disruptions was reduced from an average of three weeks to two days, which led to a significant improvement in production planning and customer satisfaction.
Conclusion on risk management
Effective risk management in Procurement is indispensable in today's globalized economy. The systematic identification, assessment and management of risks along the supply chain not only ensures continuity of supply, but also strengthens the company's competitive position. By using modern technologies and proactive strategies, companies can identify risks at an early stage and take targeted countermeasures. Success lies in the balance between effective risk management and operational efficiency.
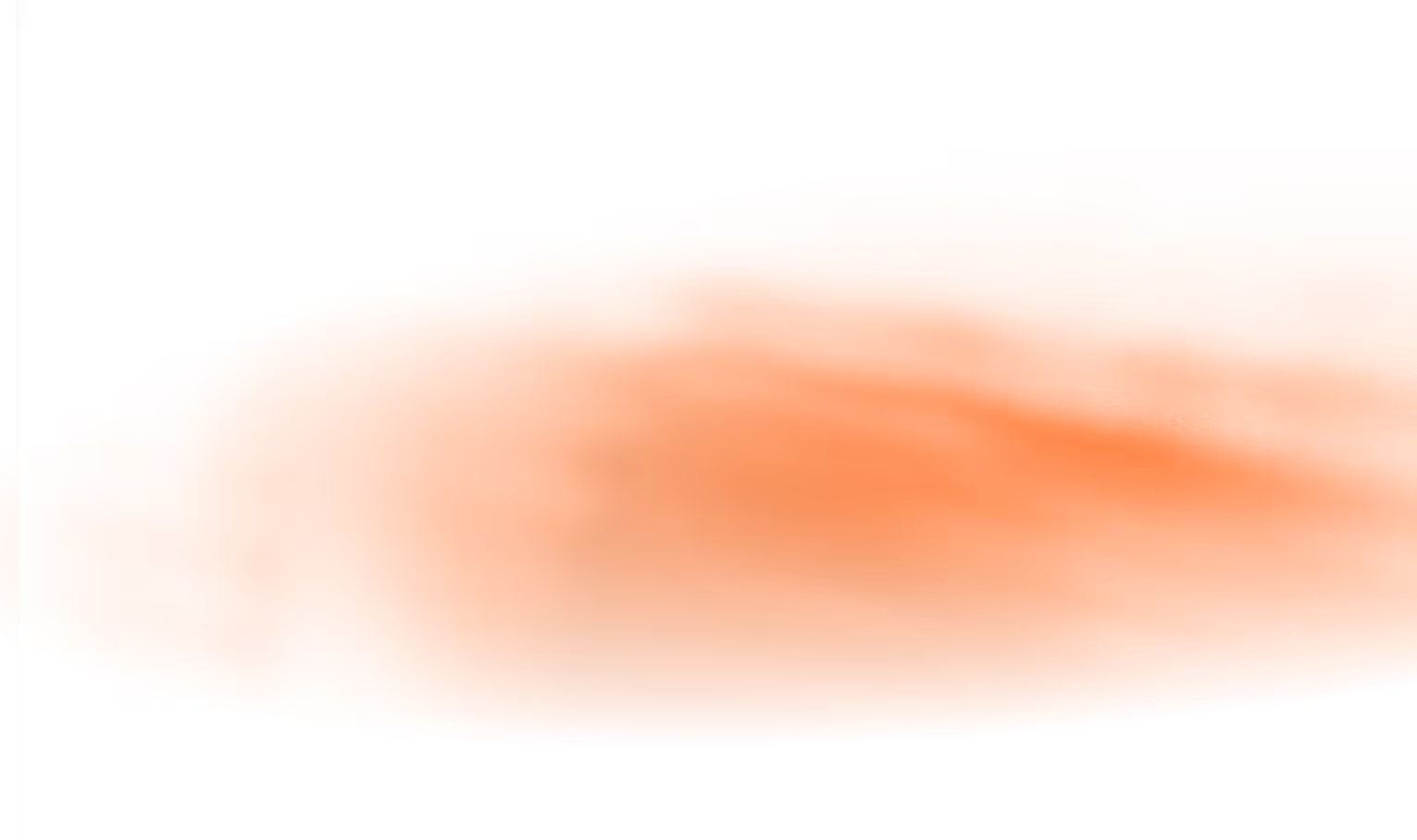
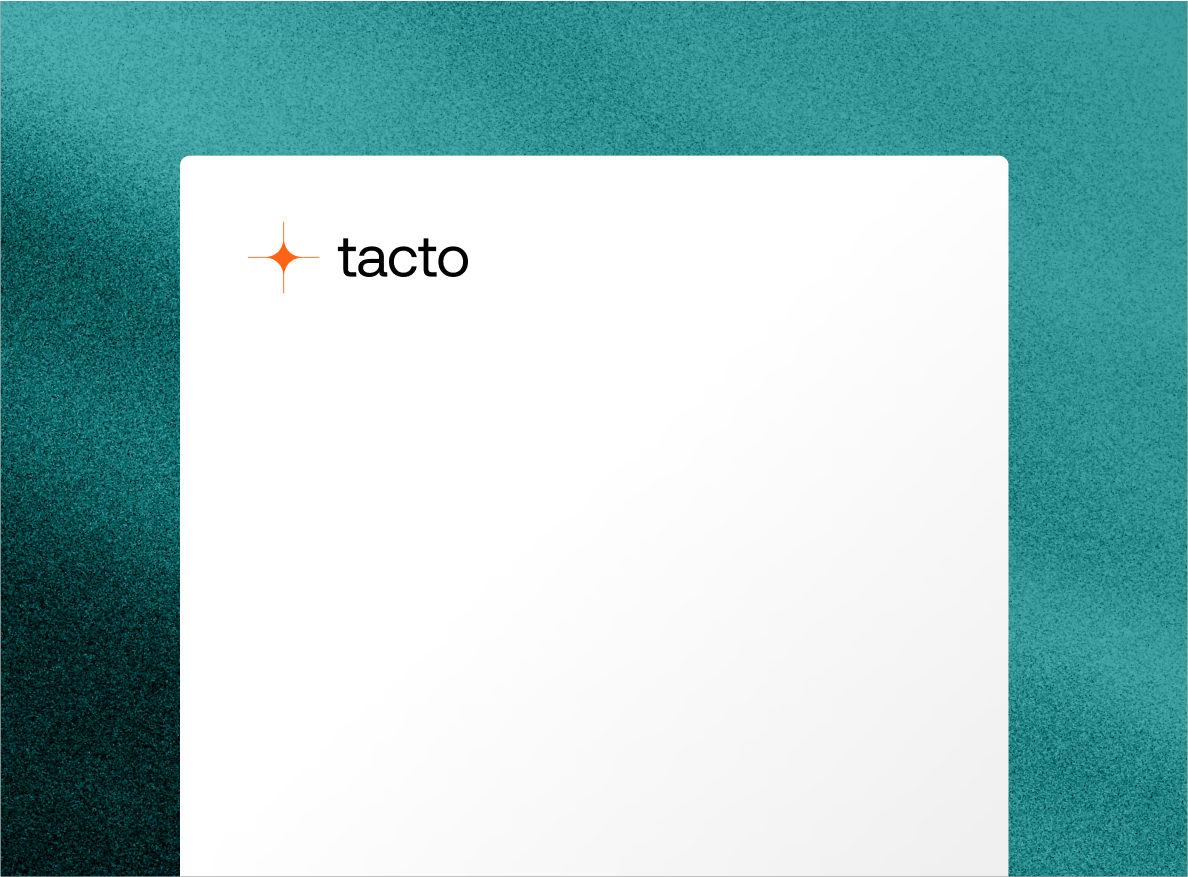