Procurement Glossary
Security of supply: definition and important aspects for buyers
Security of supply forms the foundation for stable business processes and is becoming increasingly strategically important in times of global uncertainty. This structured overview shows how Procurement can ensure the continuous availability of critical resources through targeted measures and strategies.
Security of supply in a nutshell:
Security of supply describes the reliable and uninterrupted availability of goods, raw materials or services at the required times. It is a strategic success factor for Procurement , as it ensures continuous production and business processes and prevents potential supply bottlenecks.
Example: An automotive manufacturer secures its supply of critical semiconductor components through dual sourcing, holds a 4-week safety stock and concludes binding supply contracts with both suppliers for 24 months with guaranteed minimum purchase quantities of 50,000 units per quarter.
Security of supply: An introduction
In today's globalized economy, security of supply is of fundamental importance for companies, economies and societies. It refers to the reliable and continuous availability of essential goods, raw materials and services. In times of international crises, supply chain disruptions and geopolitical tensions, the topic is becoming increasingly relevant. This guide deals with the various aspects of security of supply, from strategic planning and risk management to concrete measures to ensure a stable supply. Economic as well as political and technical dimensions of security of supply are examined.
What is security of supply?
Security of supply in Procurement refers to ensuring a continuous and reliable supply of required goods, materials or services to a company. It ensures that all the necessary resources are available in the right quality, quantity and at the right time in order to maintain production processes and business operations without interruptions.
Core elements of security of supply
Significance for Procurement
In procurement, security of supply plays a decisive role in a company's competitiveness and stability. It enables production interruptions to be avoided, delivery times to be met and customers to be served reliably. Effective management of supply security therefore contributes significantly to customer and stakeholder satisfaction.
Security of supply: from traditional strategies to modern approaches
Building on the importance of supply security as an essential factor for smooth operations, companies today are facing increasingly complex challenges. Global supply chains, volatile markets and unpredictable events such as pandemics require a rethink of how to secure the supply of materials. The need to switch from traditional methods to innovative approaches is becoming increasingly urgent in order to ensure competitiveness and stability.
Old: Traditional security of supply strategies
Traditional approach: Historically, companies relied on high stock levels and long-term contracts with a small number of suppliers to secure supplies. This"just-in-time" model meant that large quantities of materials were held in stock to mitigate any shortages. Relationships with suppliers were often rigid and there was a lack of flexibility to react to market changes. This strategy led to high inventory costs, tied-up capital and an increased risk of stock obsolescence. In addition, external disruptions such as natural disasters or political unrest could still severely affect supply chains.
New: Supply Chain Resilience
Supply chain resilience: Modern companies rely on a resilient supply chain that prioritizes agility and adaptability. By using digital technologies such as IoT, big data and AI, supply chains become transparent and can be monitored in real time. This enables proactive risk analysesand rapid responses to disruptions. Strategies such as nearshoring and flexible contract models increase flexibility. In addition, collaboration across the entire value chain promotes innovation and strengthens relationships. The implementation of supply chain resilience leads to reduced inventories, lower costs and higher customer satisfaction through reliable deliveries.
Practical example: Automotive industry
A leading automotive manufacturer was facing challenges due to supply bottlenecks for electronic components. By converting to a resilient supply chain strategy, the company was able to expand its supplier base within six months. supplier base by 30% within six months. The use of AI-supported forecasting tools improved demand planning by 20%, which led to a 15% reduction in inventory levels. The response time to supplier disruptions was reduced from an average of ten to two days. Overall, the company increased its production efficiency and achieved annual cost savings of 50 million euros.
Conclusion on security of supply
Security of supply is a key success factor for modern companies. The combination of strategic supplier management, optimized inventory management and digital risk management enables robust and future-proof procurement. Despite higher costs and coordination efforts, the advantages of a diversified procurement strategy clearly outweigh the disadvantages - especially in times of global uncertainty and rapidly changing markets.
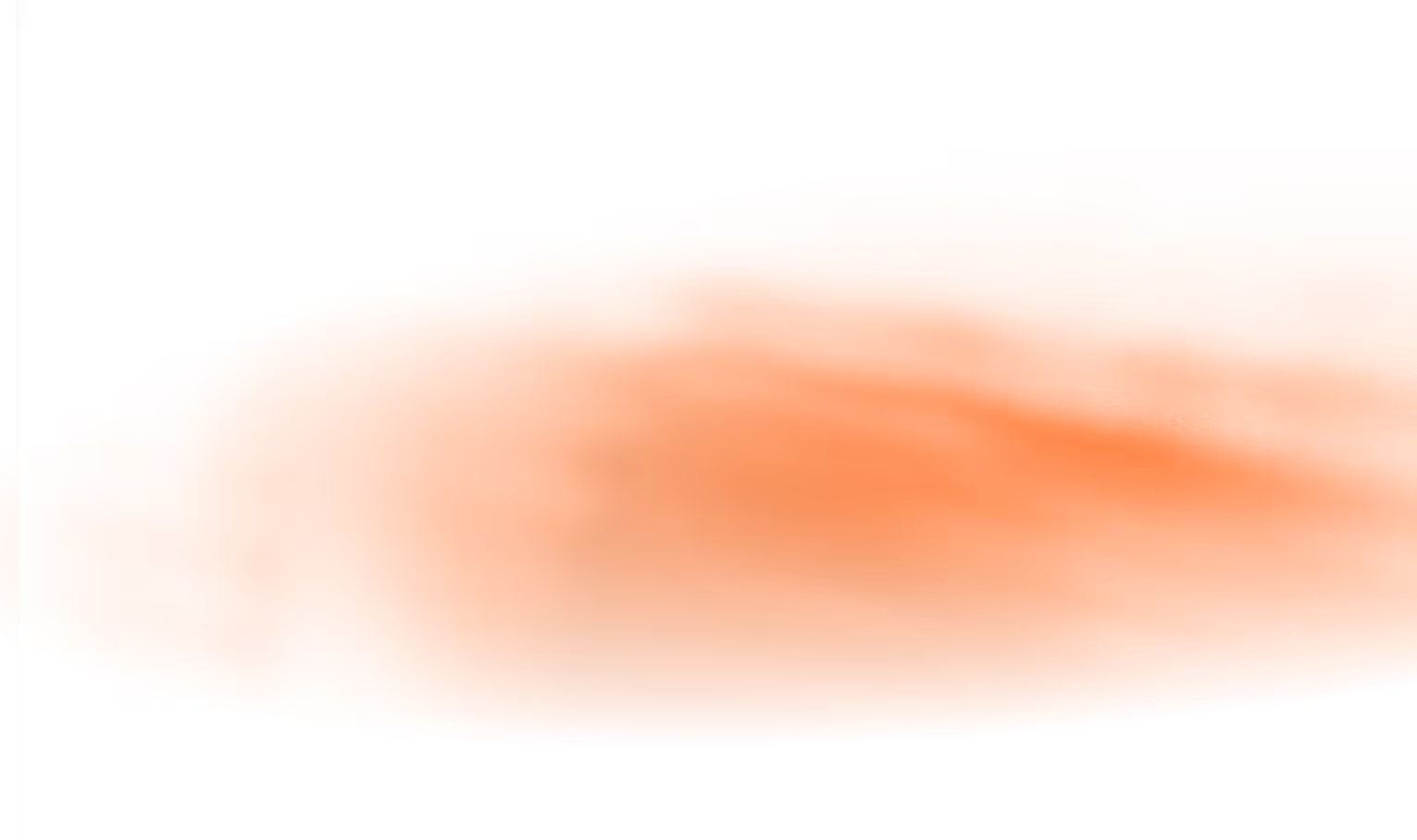
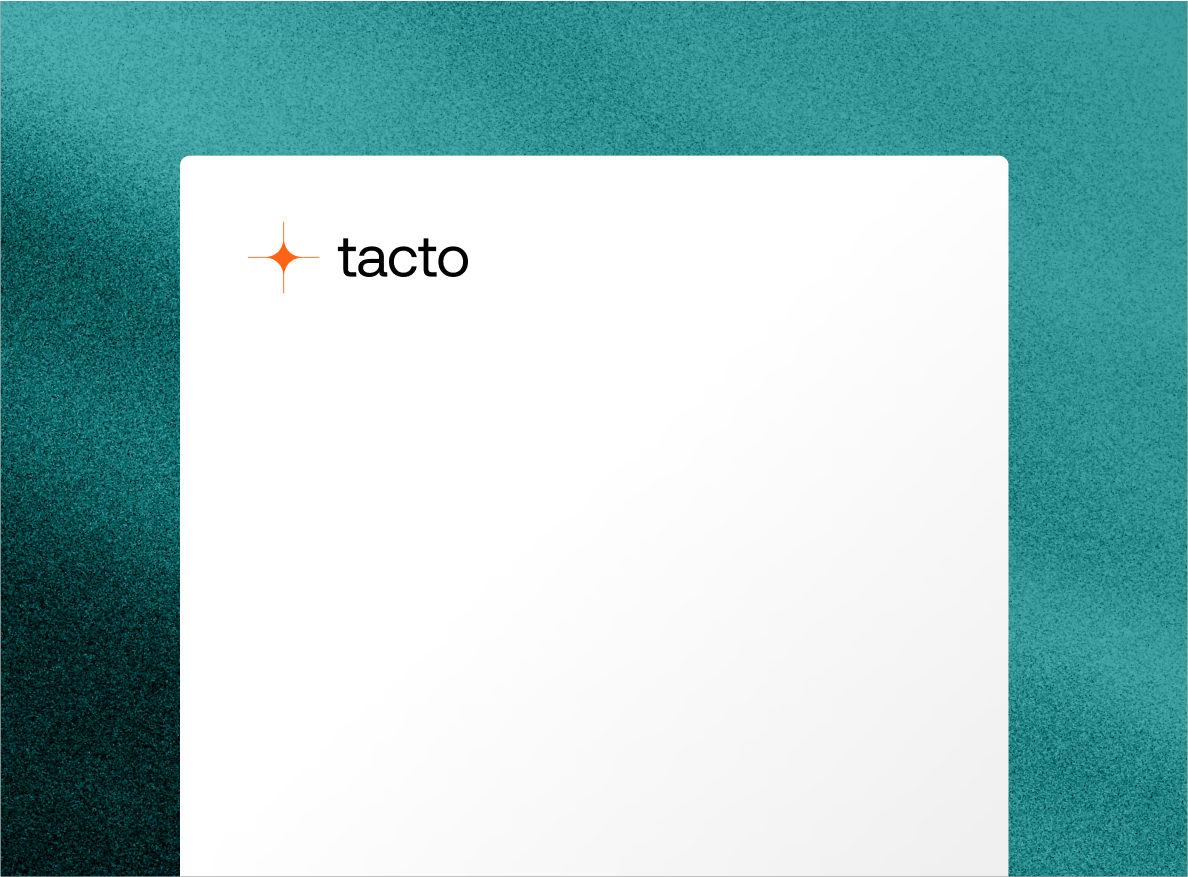