Procurement Glossary
Storage: definition, core elements & strategies
Putaway is a fundamental process in the logistics and warehouse management of companies. It describes the systematic receipt and storage of goods and materials in a warehouse or storage facility. Efficient putaway is crucial for the optimal use of storage capacity, minimizing storage costs and ensuring smooth merchandise management.
What is storage?
The professional storage of goods and materials forms the backbone of an efficient supply chain and ensures continuous availability for production and retail.
- Putaway refers to the systematic process of receiving, checking and properly storing goods in the warehouse according to defined storage strategies.
- Putaway refers to the receipt of goods or materials in the procurement process and their transfer to inventory management.
- The aim of storage is to ensure the availability of materials and guarantee a smooth production or distribution process.
- Efficient storage is essential for Procurement in order to ensure the availability of goods and minimize storage costs.
Introduction to the {{name}}
Core elements of storage
- Incoming goods inspection: checking the delivered goods for quality and quantity
- Storage location management: Systematic allocation of storage locations for optimum material availability
- Inventory management: updating stock levels and documenting movements
- Warehouse systems: use of technologies such as ERP systems for efficient management
Strategies for storage and order picking
In addition to receiving and quality control, proper storage is at the heart of putaway. In order to make the handover to production as smooth as possible, there are various strategies for storage and picking, which are described below.
- FIFO (First In, First Out): The items stored first are also removed first. This ensures a constant dwell time for all items, which is often used to prevent obsolescence or spoilage of resources. (Used in the food, pharmaceutical and automotive industries)
- LIFO (Last In, First Out): LIFO is the opposite of FIFO, as the items stored last are removed first, which is only suitable for non-perishable resources. Ease of implementation is the most common reason for using the LIFO strategy.
- FEFO (First Expired, First Out): FEFO is a variation of FIFO and is mainly used for items with a fixed expiration date. The article with the next expiration date is recognized and removed during picking.
- HIFO (Highest In, First Out): The resources with the highest values are removed first. This strategy is primarily used in industries where the value of goods fluctuates greatly. Here, too, IT support is required for putaway. (e.g. electrical industry)
- LOFO (Lowest In, First Out): LOFO is the opposite of HIO and is also used in industries with goods whose value fluctuates greatly (e.g. textile industry)
Importance of putaway for Procurement
Putaway plays a crucial role for Procurement , as it represents the interface between procurement and internal supply. Efficient storage helps to minimize storage costs, avoid supply bottlenecks and ensure continuous production. By coordinating closely with the warehouse, Procurement can plan requirements better, order quantities optimally and thus save costs.
- Cost control: reduction of stock levels and warehousing costs
- Needs-based procurement: avoidance of excess stock or material shortages
- Supplier management: optimization of delivery times and quantities through accurate inventory data
Storage: from manual warehousing to digital warehouse management
Putaway is a central process in Procurement and procurement logistics that ensures goods are placed efficiently and securely in the warehouse. The practical implementation of putaway is crucial to the performance of the supply chain. With increasing demands for speed and accuracy, the need for more efficient putaway methods is becoming ever more urgent. The transformation from traditional to modern approaches is therefore essential to remain competitive. To this end, some warehousing strategies, such as HIFO or LOFO, can only be implemented with advanced IT tools.
Traditional approach: Manual warehousing
- Storage through physical labor and without supporting technologies
- Moving goods with simple aids such as forklift trucks
- Paper lists for identifying storage bins
- Manual documentation in inventory management
- High susceptibility to errors, high workload, slow processes and low inventory transparency
- The main problems are incorrect storage, inventory discrepancies and time-consuming search processes.
New: Digital warehouse management system (WMS)
- Modern storage uses digital warehouse management systems
- Process automation and optimization
- Use of WMS to record goods movements in real time and optimize the allocation of storage locations
- Precise tracking of items using technologies such as barcode scanning and RFID
- Accelerated storage processes through the integration of automated conveyor systems and driverless transport systems
- Reduced error rates, improved storage space utilization and increased inventory transparency
Practical example: Automated high-bay warehouse
A medium-sized automotive supplier implemented an automated high-bay warehouse with an integrated WMS. Thanks to the automation, storage times were reduced by 60% and storage capacity increased by 30%. The storage error rate fell to less than 0.1%. In addition, real-time inventory management made it possible to plan production better and reduced the capital commitment period in the warehouse by 20%.
Conclusion on storage
Efficient storage processes are essential for modern Procurement . By using digital technologies such as RFID and warehouse management systems, inventory accuracy can be increased, costs reduced and processes optimized. The key to success lies in the integration of modern technologies, well-trained personnel and well thought-out process design. Despite initial investment costs, the optimization of storage pays off in the long term through increased efficiency and improved planning.
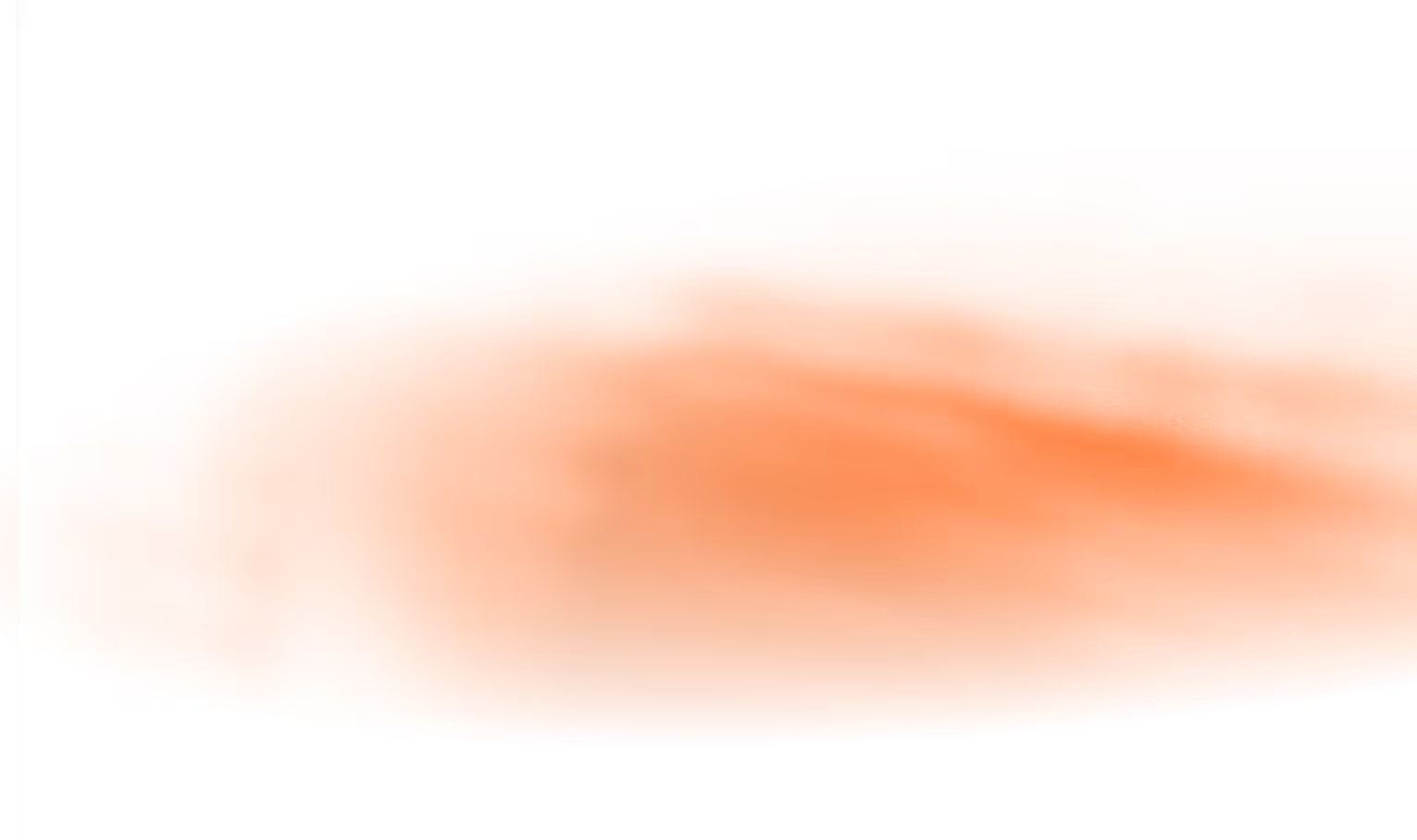
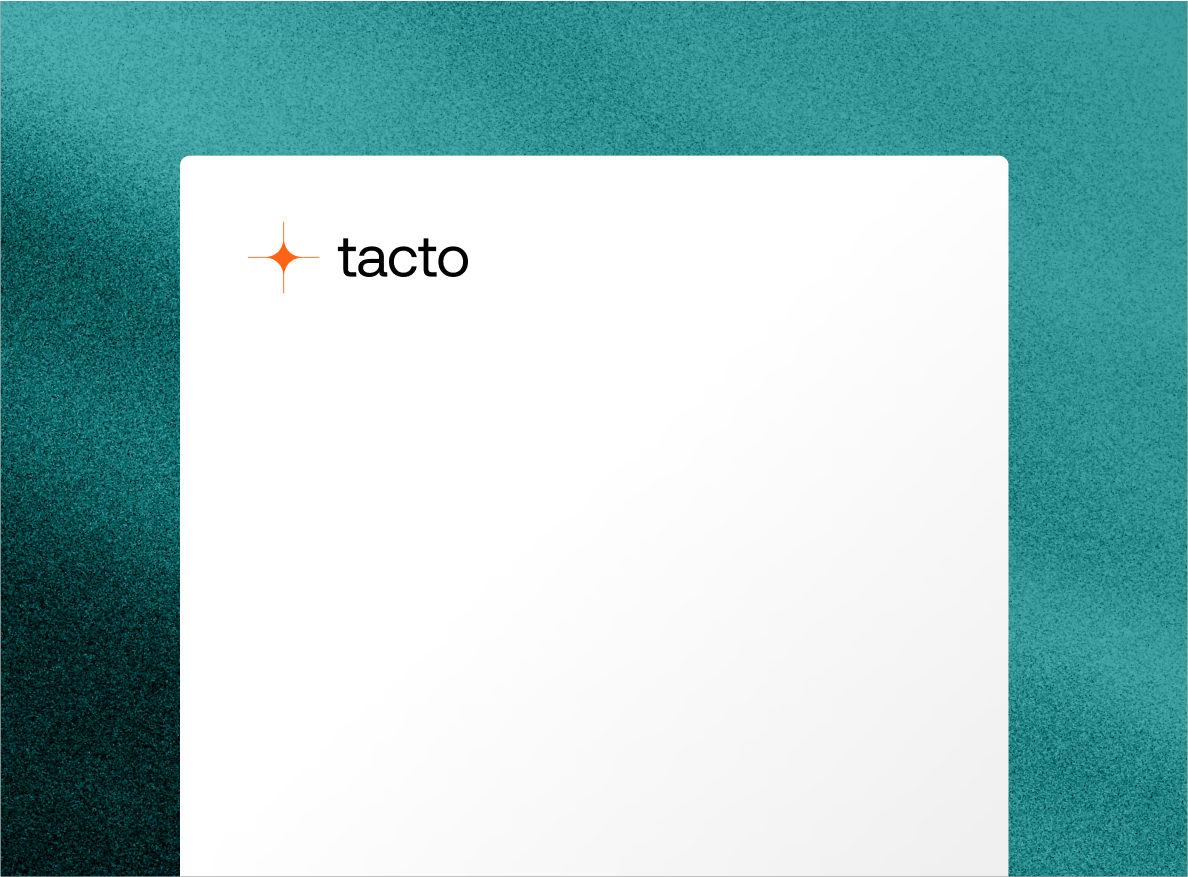