Procurement Glossary
Inventory difference: definition & important aspects for buyers
Inventory discrepancies have a direct impact on a company's success and require systematic management to uncover weaknesses in inventory management. The following overview shows the most important causes and measures for Procurement in order to effectively minimize differences and sustainably improve inventory accuracy.
Inventory difference in a nutshell:
Inventory differences are discrepancies between the stock recorded in the accounts and the stock actually held by a company. These differences are relevant for Procurement , as they can lead to unplanned reorders and have a direct impact on requirements planning and inventory costs.
Example: During the annual inventory of an electronics retailer, it was found that only 985 of the 1,000 smartphones booked were actually physically present, which corresponds to a negative inventory difference of EUR 6,000 at a unit price of EUR 400.
Introduction to purchasing controlling: Inventory difference
Inventory discrepancy is an important issue in retail and warehouse management that can have a significant financial impact on companies. It refers to the difference between the stock recorded in the accounts and the actual physical stock of goods or materials. These differences can be both positive and negative and arise for various reasons such as theft, shrinkage, spoilage or accounting errors. The systematic recording and analysis of inventory differences is of great importance for companies, as it not only has a direct influence on the company's success, but also provides important information on organizational weaknesses and potential for optimization. This guide highlights the most important aspects of inventory discrepancies, their causes and measures to reduce them.
What is an inventory difference?
An inventory difference is the difference between the target stock recorded in the accounts and the actual stock of goods or materials in the company. This difference is usually determined during stocktaking and can indicate both shortages and surpluses. Causes can include theft, shrinkage, incorrect bookings or counting errors.
Main causes and core elements of inventory differences
Relevance of inventory differences in Procurement
Inventory differences have a direct impact on Procurement, as they affect stock accuracy and therefore the ability to plan and forecast. Unknown differences can lead to wrong decisions, such as over-ordering or delivery bottlenecks. It is therefore essential for Procurement to minimize inventory differences in order to save costs and ensure security of supply.
Inventory difference: from manual stocktaking to automated inventory management
Inventory discrepancies present companies with significant challenges, as discrepancies between accounting and actual stock levels can lead to financial losses and disruptions in the supply chain. Building on the theoretical importance of inventory discrepancies, it becomes clear how important accurate inventory management is in practice. Traditional methods are reaching their limits, which is why a shift towards modern approaches is necessary to increase efficiency and accuracy.
Old: Manual inventory
Traditional approach: In traditional practice, inventory is usually recorded by manual counts. Employees walk through the warehouse and physically note each item to then reconcile it with the accounting records. This method is time-consuming and prone to human error such as counting mistakes or incorrect data entry. It also often leads to business interruptions, as the regular course of business is restricted during stocktaking. The limitations of this method are reflected in inaccurate inventories and increased costs for corrections and rework.
New: Automated inventory management
Automated Inventory Management: Modern companies rely on inventory management to effectively minimize inventory discrepancies. By using technologies such as RFID, barcode scanning and integrated inventory management systems, stocks are recorded and updated in real time. These innovations enable permanent stocktaking without interrupting operations. Advanced analytics and AI algorithms detect anomalies immediately and enable proactive measures to be taken. Practical benefits include increased stock accuracy of up to 99%, reduced storage costs and an optimized supply chain.
Practical example: Implementation of RFID in the logistics center
An international logistics service provider implemented RFID technology in its main warehouse to reduce inventory discrepancies. By automatically recording incoming and outgoing goods, the inventory discrepancy was reduced by 85%. Inventory time was reduced from two weeks to just a few hours. In addition, the increased stock accuracy reduced delivery delays by 30%, which led to an increase in customer satisfaction.
Conclusion on the inventory difference
Inventory differences are a critical factor for a company's stock accuracy and profitability. The systematic analysis and minimization of these differences through modern technologies, trained personnel and optimized processes is crucial for efficient Procurement and reliable warehousing. Only through continuous monitoring and preventative measures can companies sustainably improve their inventory management and reduce costs.
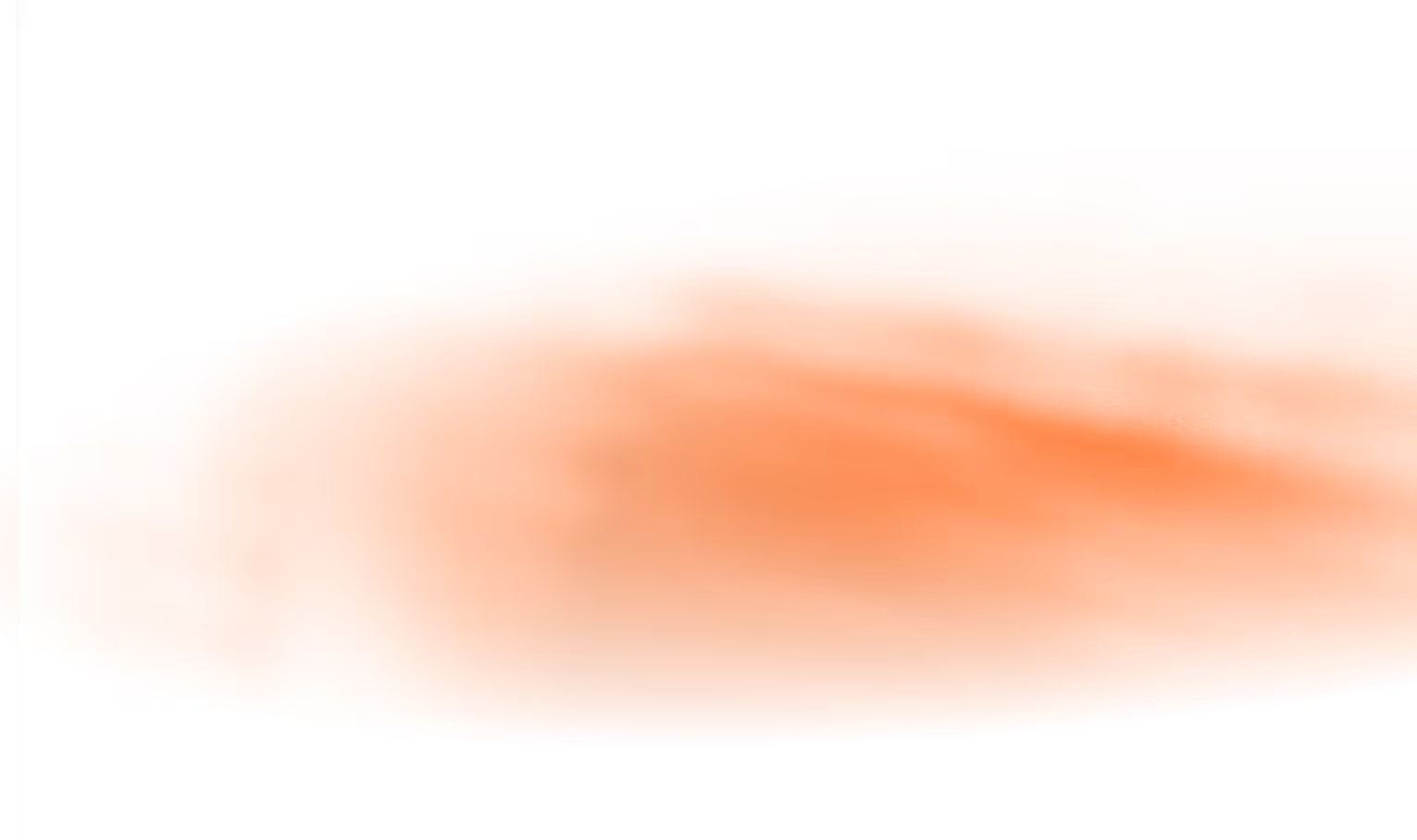
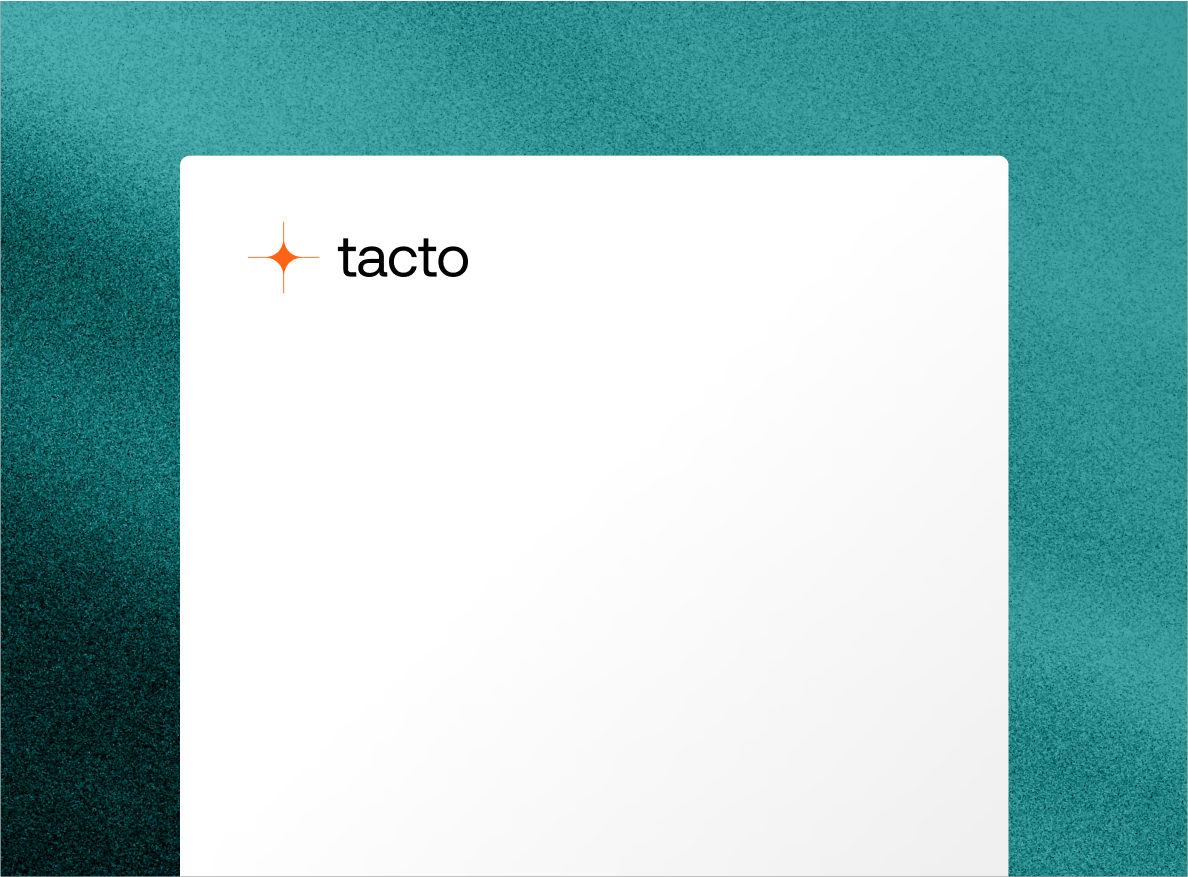