Procurement Glossary
Insourcing: definition & important aspects for buyers
Insourcing enables companies to bring back outsourced activities, creating new opportunities for value creation, quality assurance and cost control. This structured overview shows you the most important aspects of insourcing and how you as a buyer can successfully manage the process of reintegration.
Insourcing in a nutshell:
Insourcing describes the (re)transfer of previously outsourced business activities back into the company's own organization. For Procurement , this represents a strategic opportunity to achieve better control, higher quality and long-term cost savings by internalizing processes.
Example: In 2023, a car manufacturer is relocating the production of important electronic components from an Asian supplier back to its own plant and investing 50 million euros in new production facilities, which will reduce delivery times by 70% and improve quality control.
Introduction to insourcing
Insourcing is a strategic management concept in which previously outsourced business processes or services are brought back in-house. This management decision is becoming increasingly important in today's business world as companies seek greater control, quality assurance and cost savings. Insourcing can affect different areas of the business, from production to IT services and administrative tasks. This guide takes a closer look at the most important aspects of insourcing, its advantages and disadvantages and how to implement it successfully in a corporate context.
What is insourcing?
Insourcing refers to the strategy of bringing previously outsourced business processes or services back in-house. In the context of the purchasing strategy, this means that tasks that were previously performed by external suppliers or service providers are now handled internally. The aim of insourcing is to increase control over critical processes, reduce costs and build up or strengthen internal expertise.
Core elements of insourcing
Importance of insourcing in Procurement
In Procurement , insourcing offers the opportunity to reduce dependencies on external supplier management and to better manage risk management. By handling processes internally, companies can react more flexibly to market changes and implement innovations more quickly. In addition, costs can be saved by eliminating external margins and realizing efficiencies through process optimization.
Insourcing: from outsourcing to internal value creation
Building on the importance of insourcing as a strategic return of outsourced business processes, companies are increasingly recognizing the benefits of this practice. By insourcing, they gain more control over critical areas, increase product quality and strengthen their competitiveness. The need to react more flexibly to market changes and reduce dependencies on external service providers is driving this change.
Old: Outsourcing
Traditional approach: In the past, companies outsourced numerous business processes to external service providers in order to reduce costs and focus on core competencies. Typical areas of outsourcing were IT services, customer support or parts of production. Contract management and service level agreements (SLAs) were used as central tools. However, factors such as cultural differences, communication difficulties and quality problems often led to challenges. In addition, dependence on third-party providers increased risk management for supply chain disruptions and limited the ability to react to market changes.
New: In-House Production
In-house production: Modern companies are increasingly relying on the internal provision of previously outsourced services. The value chain is being expanded by investing in in-house resources, technologies and employees. Key innovations such as automation, robotics and artificial intelligence enable efficient processes and cost benefits. Practical benefits include increased quality assurance agreements, protection of sensitive data and greater flexibility when adapting products. This change strengthens internal expertise and promotes faster implementation of innovations.
Practical example: Automotive industry
A leading car manufacturer decided to outsource the production of battery components for electric vehicles, which had previously been outsourced to suppliers, to its own company. By insourcing, production time was reduced by 25% and the error rate was cut by 30%. Investments in modern production facilities and employee training led to an increase in product quality. In addition, in-house production enabled a faster response to technological developments and market requirements, which led to a 15% increase in sales in the electromobility sector.
Conclusion on insourcing
Insourcing in Procurement offers companies the opportunity to bring strategically important processes back under their own control and optimize costs in the process. Despite initial investments and challenges in building up expertise, the long-term benefits outweigh the costs: improved quality control, reduced dependency on external suppliers and increased internal know-how. Success depends largely on careful planning and professional change management.
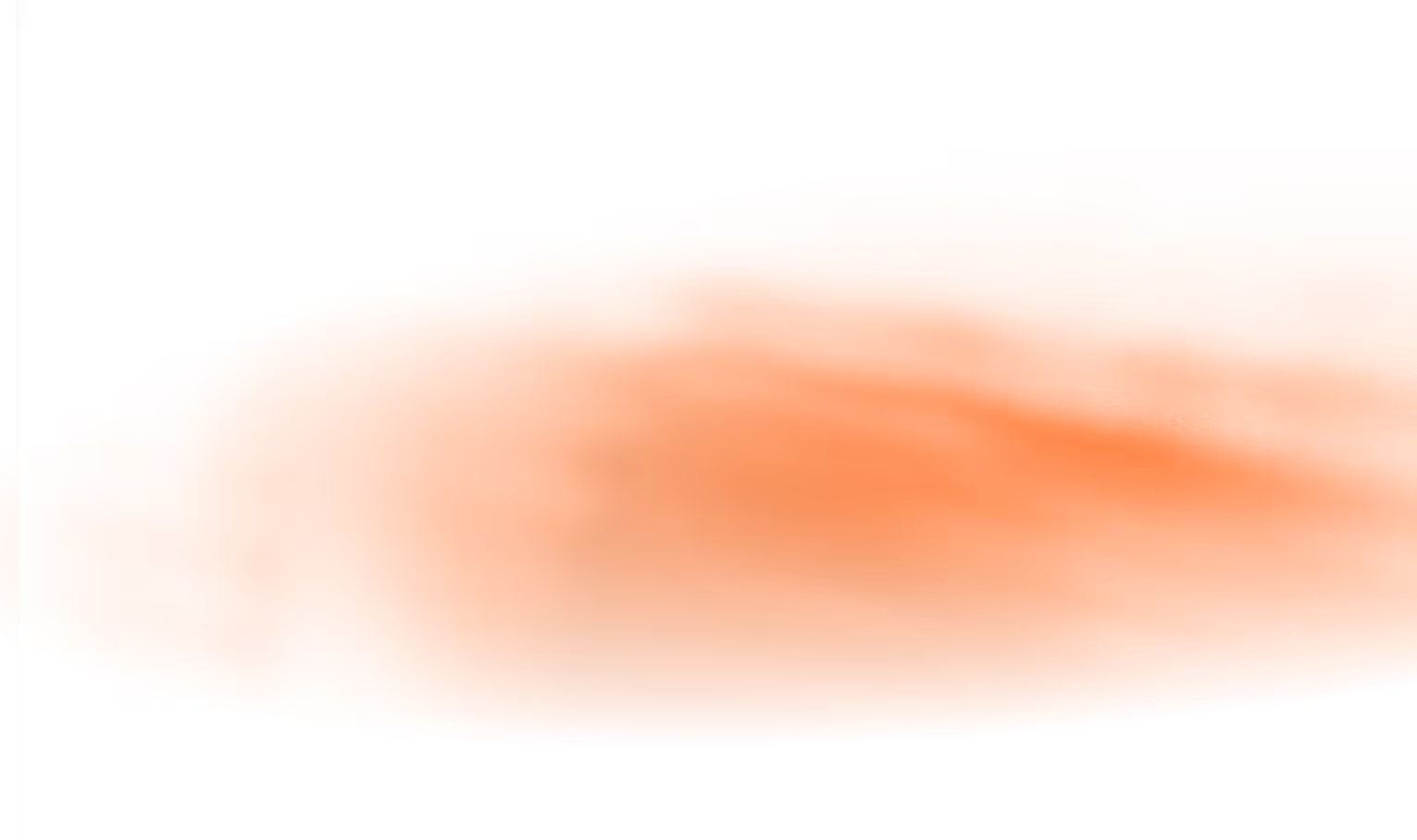
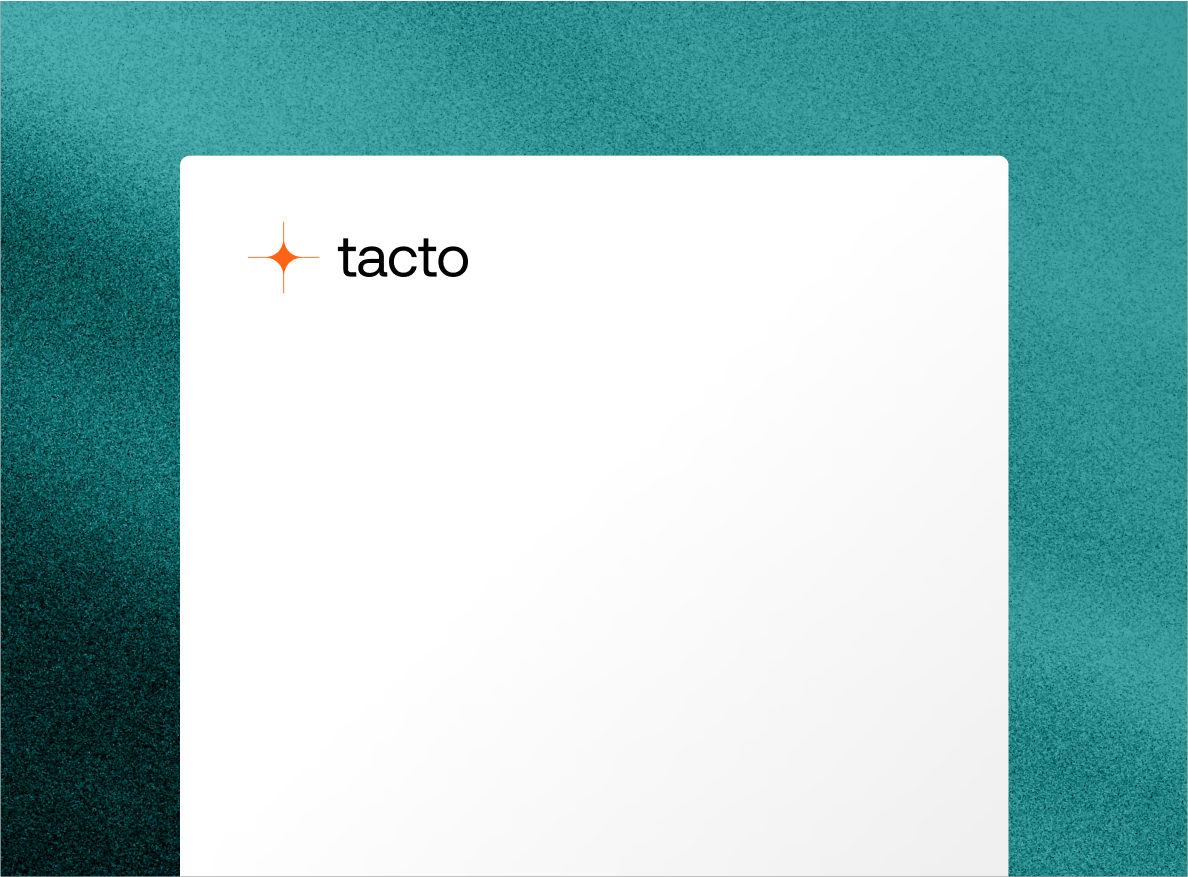