Procurement Glossary
Inventory turnover: definition & important aspects for buyers
The inventory turnover rate shows how efficiently a company manages its inventory and is a key indicator for working capital and liquidity. This structured overview provides the most important key figures and optimization levers for Procurement in order to sustainably reduce inventory costs.
Inventory Turnover in a nutshell:
Inventory turnover is a key figure that indicates how often the average stock is completely turned over within a defined period of time. For Procurement , this key figure is essential for optimizing order quantities and storage costs as well as for improving working capital performance.
Example: An automotive supplier with an average inventory of 2 million euros and an annual turnover of 12 million euros achieves an inventory turnover of 6, which means that the entire warehouse is turned over every 2 months.
Introduction to inventory turnover
Inventory turnover is an important key figure in the field of inventory management and logistics. It provides information on how often the average stock is completely turned over, i.e. sold and replenished, within a certain period of time (usually one year). This key figure is of great importance for assessing the efficiency of working capital management and the operational performance of a company. An optimal inventory turnover rate helps to minimize storage costs while ensuring the availability of goods. In this guide, you will learn everything you need to know about calculating, interpreting and optimizing the inventory turnover rate.
What is inventory turnover?
Inventory turnover is a key performance indicator in procurement and warehousing that shows how often the average stock is sold or consumed in a given period. It is calculated from the ratio of material consumption or turnover to the average stock level. A high inventory turnover indicates efficient use of stock, while a low value indicates excessive stock levels and unnecessary capital commitment.
Core elements of inventory turnover
Significance for Procurement
In Procurement , inventory turnover is a key indicator of the efficiency of warehousing and procurement processes. Optimized inventory turnover reduces storage costs, minimizes the risk of obsolete stock and improves the company's liquidity. Buyers can positively influence inventory turnover through precise demand planning, just-in-time deliveries and close cooperation with suppliers.
Inventory turnover: from manual calculation to real-time inventory analytics
Based on the importance of inventory turnover as a key performance indicator for the efficiency of warehousing, it is clear in practice how crucial precise and timely recording is for the success of a company. Traditional methods reach their limits here and can hardly meet the requirements of modern supply chains. A shift towards innovative, data-driven approaches is required in order to remain competitive and optimize inventory management.
Old: Manual stock turnover calculation
Traditional approach: In the past, inventory turnover was usually calculated manually or using simple spreadsheets. Employees periodically collected data on stock levels and sales figures to determine the inventory turnover rate. This method was time-consuming and error-prone. The lack of real-time visibility often led to sub-optimal ordering decisions, overstocking or shortages. It also made it difficult to react quickly to market analysis and impaired liquidity by tying up a lot of capital in the warehouse.
New: Real-Time Inventory Analytics
Real-time inventory analytics: Modern technologies enable comprehensive real-time analysis of inventory turnover. By integrating ERP systems, IoT devices and AI algorithms, inventory data is continuously recorded and analyzed. This enables companies to react immediately to changes in demand and automate order point processes. The use of big data and predictive analytics helps to make forecasts more precise and optimize the supply chain. This leads to reduced storage costs, a higher turnover rate and improved customer service.
Practical example: Digitalization in e-commerce
A leading e-commerce provider used real-time inventory analytics to optimize its warehouse processes. By recording sales and inventory data in real time, stock turnover was increased by 25%. The average storage period fell from 40 to 30 days. At the same time, warehousing costs were reduced by 1.5 million euros per year. The improved inventory management led to a higher delivery capacity and a 15% increase in customer satisfaction.
Conclusion on the inventory speed
Inventory turnover is a key indicator for the efficiency of warehouse management and capital commitment in the company. An optimal inventory turnover rate enables cost savings, improves liquidity and increases competitiveness. Thanks to modern technologies such as AI and predictive analytics, inventory turnover can be controlled and optimized with increasing precision. However, precise demand planning, close supplier relationships and a balance between security of supply and storage costs remain crucial to success.
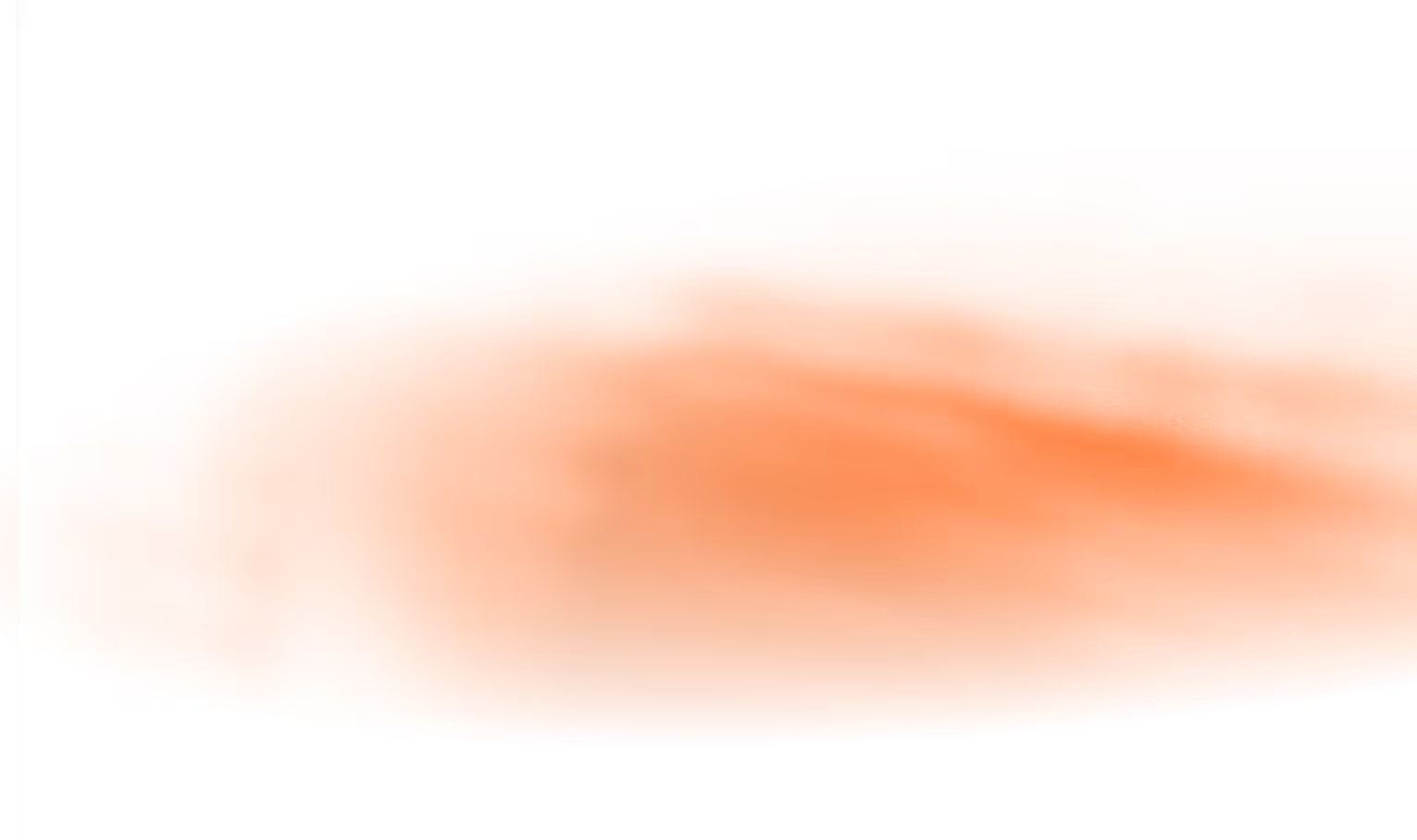