Procurement Glossary
Order point procedure: Definition & important aspects for buyers
The reorder point procedure enables optimal inventory management and helps companies to avoid supply bottlenecks while minimizing storage costs. This structured overview shows you how you can successfully use the procedure in Procurement and efficiently manage your material supply.
Order point procedure in a nutshell:
The reorder point procedure is a method of inventory management in which an order is automatically triggered as soon as a defined minimum stock level (reorder point) is reached. For Procurement , this enables systematic stock control and timely material procurement, taking into account replenishment time and safety stock.
Example: An automotive supplier has defined an order point of 1,000 pieces for standard screws, whereby an order of 5,000 pieces is automatically triggered when this point is reached, which ensures an optimum supply with a replenishment time of 5 days and an average daily consumption of 150 pieces.
Introduction to the reorder point procedure
The reorder point procedure is an important tool for materials management and inventory management in companies. It is a consumption-oriented method of materials planning that determines when a new order should be triggered. The process is based on the definition of a critical stock level - the order point - at which a reorder is automatically placed. The aim is to achieve an optimum balance between security of supply and storage costs. In today's world, where efficient supply chain management is of crucial importance, the reorder point process plays a central role in optimizing warehousing and material supply.
What is the order point procedure?
The reorder point procedure is a method of materials planning in which an order is triggered as soon as the stock level of an item falls below a previously defined reorder point. This reorder point takes into account factors such as average consumption, delivery time and any safety stocks. The aim of the process is to ensure continuous material availability and at the same time optimize stock levels by avoiding excess stock.
Core elements of the order point procedure
Significance for Procurement
In inventory management, the reorder point procedure enables efficient control of stock levels. The automatic triggering of orders when the order point is reached reduces the risk of material bottlenecks. At the same time, it helps to reduce storage costs, as orders are only placed according to actual demand. This promotes an optimum balance between delivery readiness and cost efficiency in Procurement.
Order point procedure: From manual inventory monitoring to automated inventory optimization
Building on the theoretical foundation of the reorder point process, its practical application is crucial for companies to remain competitive. At a time when supply chains are becoming increasingly complex, the efficient management of inventory plays a central role. The need for a shift from traditional, manual methods to modern, automated solutions is evident in order to reduce costs and optimize processes.
Old: Manual stock control
Traditional approach: Originally, the reorder point process was implemented by manually monitoring stock levels. Warehouse staff regularly checked stock levels and triggered orders as soon as the specified reorder point was reached. The tools were often limited to simple spreadsheets or even handwritten notes. This method was time-consuming and prone to errors such as overstocking or shortages. It also lacked the ability to react quickly to changes in demand or delays in delivery, leading to inefficiencies in inventory management.
New: Automated inventory optimization
Automated Reorder Point Planning: Modern companies rely on automated systems to make the reorder point process more efficient. By integrating with ERP systems, stock levels are monitored in real time and orders are automatically generated as soon as the reorder point is reached. Advanced technologies such as RFID and barcode scanning enable precise inventory management. In addition, algorithms allow order points to be dynamically adjusted based on consumption patterns and seasonal fluctuations. These innovations lead to a reduction in storage costs, minimization of stock shortages and increased flexibility in procurement.
Practical example: Increasing efficiency at Müller AG
Müller AG, a leading manufacturer in the automotive supply industry, implemented an automated reorder point process in their ERP system. Within a year, they reduced their stock levels by 15% and stock shortages by 80%. Automated order triggering and real-time monitoring increased delivery readiness to 99%. The optimization led to annual savings of over 500,000 euros and a significant improvement in customer satisfaction.
Conclusion on supplier evaluation using the order point procedure
The reorder point procedure is an effective tool for systematic material requirements planning that helps companies to optimally manage their stock levels. By striking a balance between security of supply and cost efficiency, it enables reliable material availability while minimizing storage costs. The success of the process depends largely on precise demand forecasts and flexible adaptation to changing market conditions. With increasing digitalization and AI integration, the reorder point process will become even more accurate and efficient.
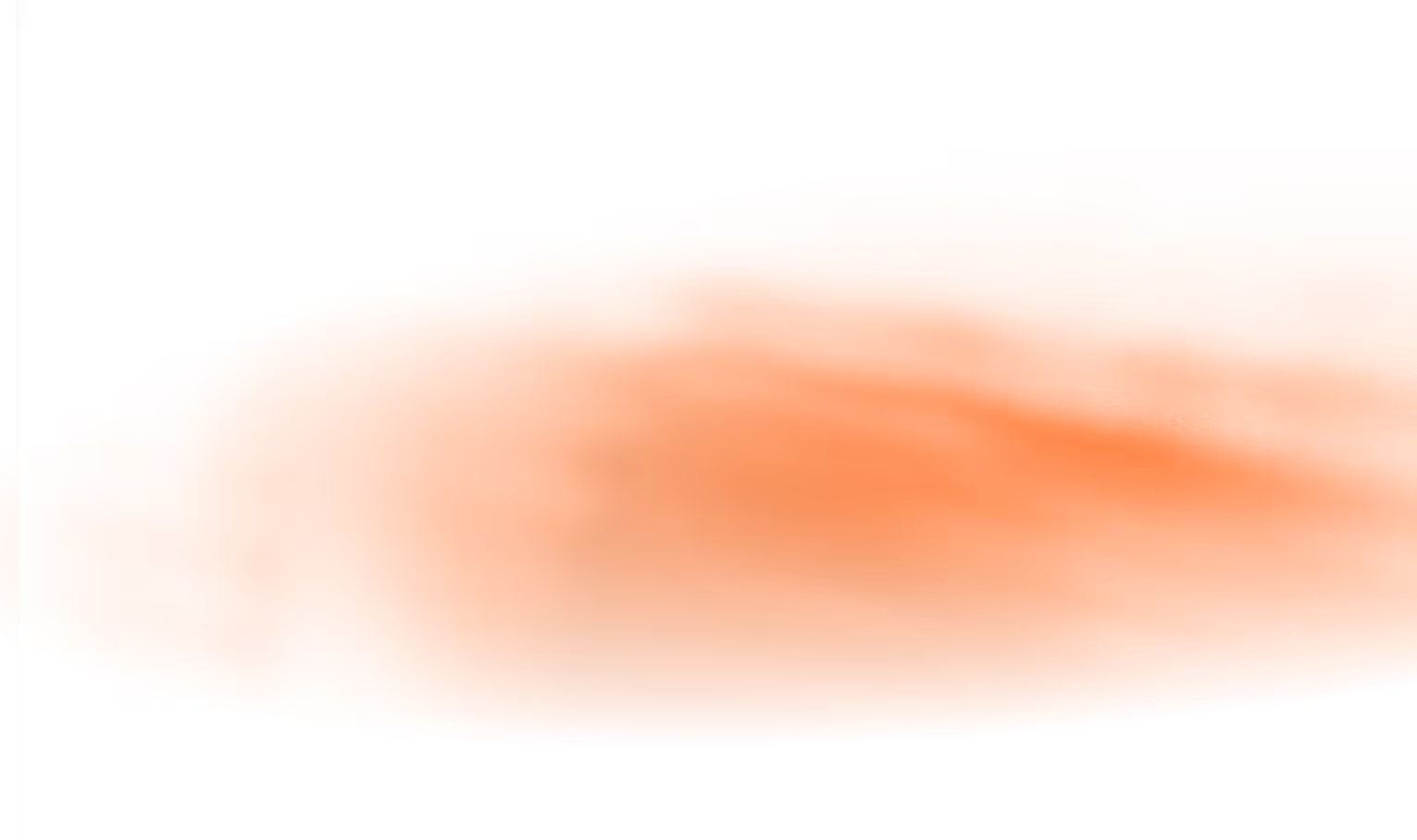
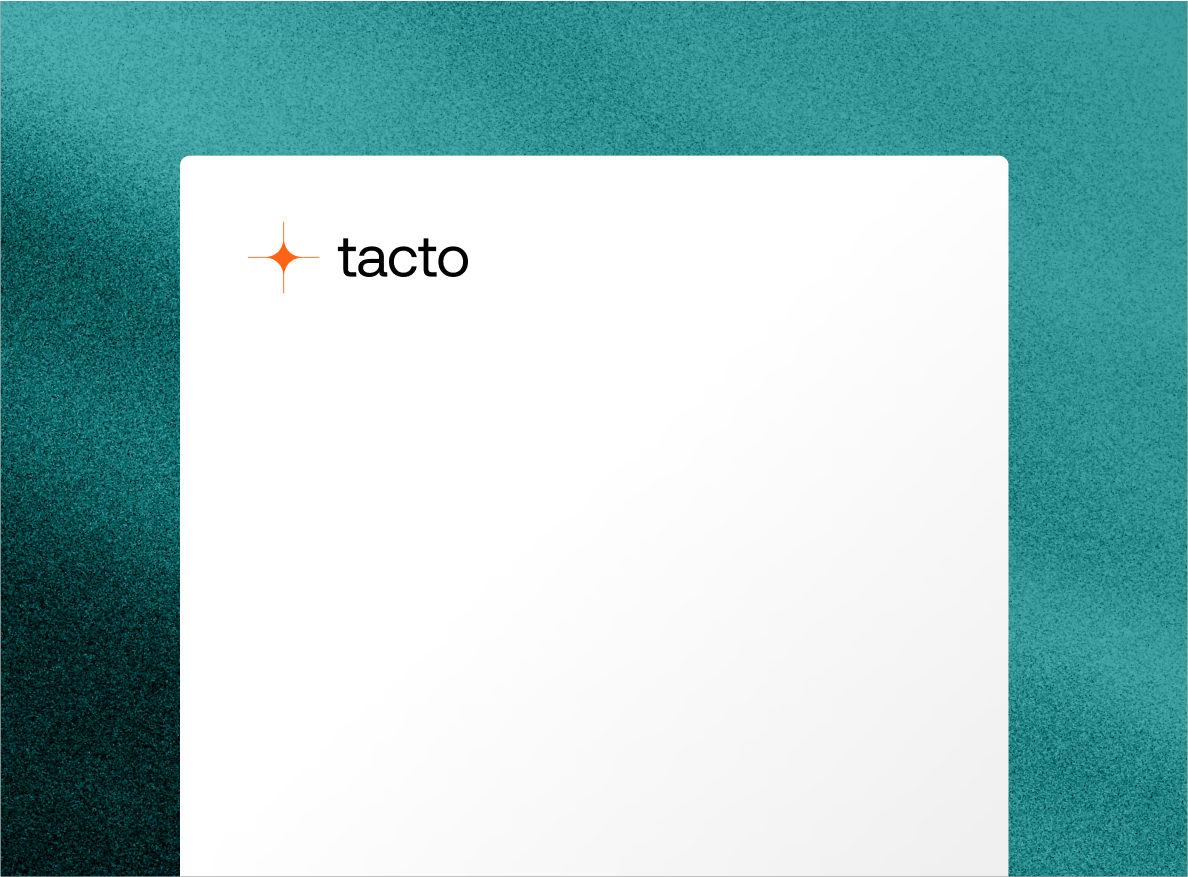