Procurement Glossary
Material requirements planning: definition & important aspects for purchasers
Materials planning controls the optimal flow of materials and thus ensures availability while minimizing stocks and costs. In this structured overview, you will learn how Procurement uses efficient scheduling strategies to ensure security of supply and reduce storage costs at the same time.
Material planning in a nutshell:
Material planning is the systematic planning, control and monitoring of material stocks to ensure production supply. It is essential for Procurement in order to avoid supply bottlenecks and optimize storage costs at the same time.
Example: An automotive supplier plans its requirements for electronic components three months in advance using an MRP system, whereby a safety stock of 14 days is defined for critical A parts and orders are automatically triggered if the minimum stock level of 1,000 units is not reached.
Introduction to material requirements planning controlling
"Materials planning is a fundamental component of operational materials management and plays a central role in production and logistics planning. It deals with the needs-based planning, control and monitoring of material stocks in companies. The aim is to ensure the optimal availability of materials and minimize storage costs at the same time. Effective materials planning not only ensures smooth production processes, but also contributes significantly to the company's competitiveness. This introduction takes a closer look at the most important aspects of materials planning, from the basics to modern planning methods and digital solutions."
What is material requirements planning?
Material planning is a central process in procurement management that deals with the planning and control of material requirements. It ensures that all necessary materials are available at the right time, in the right quantity and in the right place in order to guarantee a smooth production process. The core objective of materials planning is to avoid gaps in supply while managing stock levels and costs efficiently.
Core elements of material requirements planning
Significance for Procurement
Material planning is essential for Procurement , as it has a significant impact on the efficiency of the supply chain. Effective materials planning makes it possible to reduce costs, increase delivery capability and improve customer satisfaction. It supports Procurement in making strategic decisions, minimizing risks and achieving competitive advantages through optimized processes.
Material requirements planning: from traditional reorder point planning to digital demand forecasting
Material planning is at the heart of efficient supply chain management. In practice, it determines delivery readiness, storage costs and customer satisfaction. However, traditional methods are reaching their limits in an increasingly volatile market dynamic. A shift towards modern, digital scheduling processes is therefore necessary in order to meet the challenges of today's world.
Old: Traditional reorder point planning
Traditional approach:
In the traditional reorder point procedure, a fixed reorder level is defined, below which an order is triggered. In practice, this is often done through manual stock checks and the use of simple ERP systems. The order quantity is based on historical consumption data and fixed safety stock levels. This method is easy to implement, but is susceptible to stock-outs or overstocking, especially when demand fluctuates. It also requires a great deal of manual effort and reacts slowly to changes in the market.
New: Digital demand forecasting and AI-supported scheduling
Demand Forecasting:
Modern materials planning relies on digital demand analysis and AI-supported systems. By integrating real-time data such as sales figures, market trends and external factors, precise predictions can be made about future requirements. Artificial intelligence analyzes complex data patterns and dynamically adjusts scheduling parameters. This enables proactive control of the material flow, reduces stock levels by up to 30% and minimizes shortages. In addition, manual activities are replaced by automated processes, which increases efficiency and reduces error rates.
Practical example: automotive industry relies on AI-supported material planning
A leading car manufacturer implemented an AI-supported materials planning system in its production facility. By analyzing sales data, supplier information and external market trends, the forecasting accuracy of requirements was increased by 25%. This led to a 20% reduction in stock levels and a 15% reduction in missing parts. In addition, the administrative workload in materials planning fell by 40% as many processes were automated. Overall, the ability to deliver improved considerably, which contributed to higher customer satisfaction.
Conclusion on material planning
Materials planning is an indispensable tool in modern procurement management. It combines strategic planning with operational implementation and ensures an optimal flow of materials through precise determination of requirements, intelligent inventory management and close supplier coordination. Success lies in the balance between security of supply and cost efficiency. With increasing digitalization and AI-supported solutions, materials planning is becoming even more precise and sustainable.
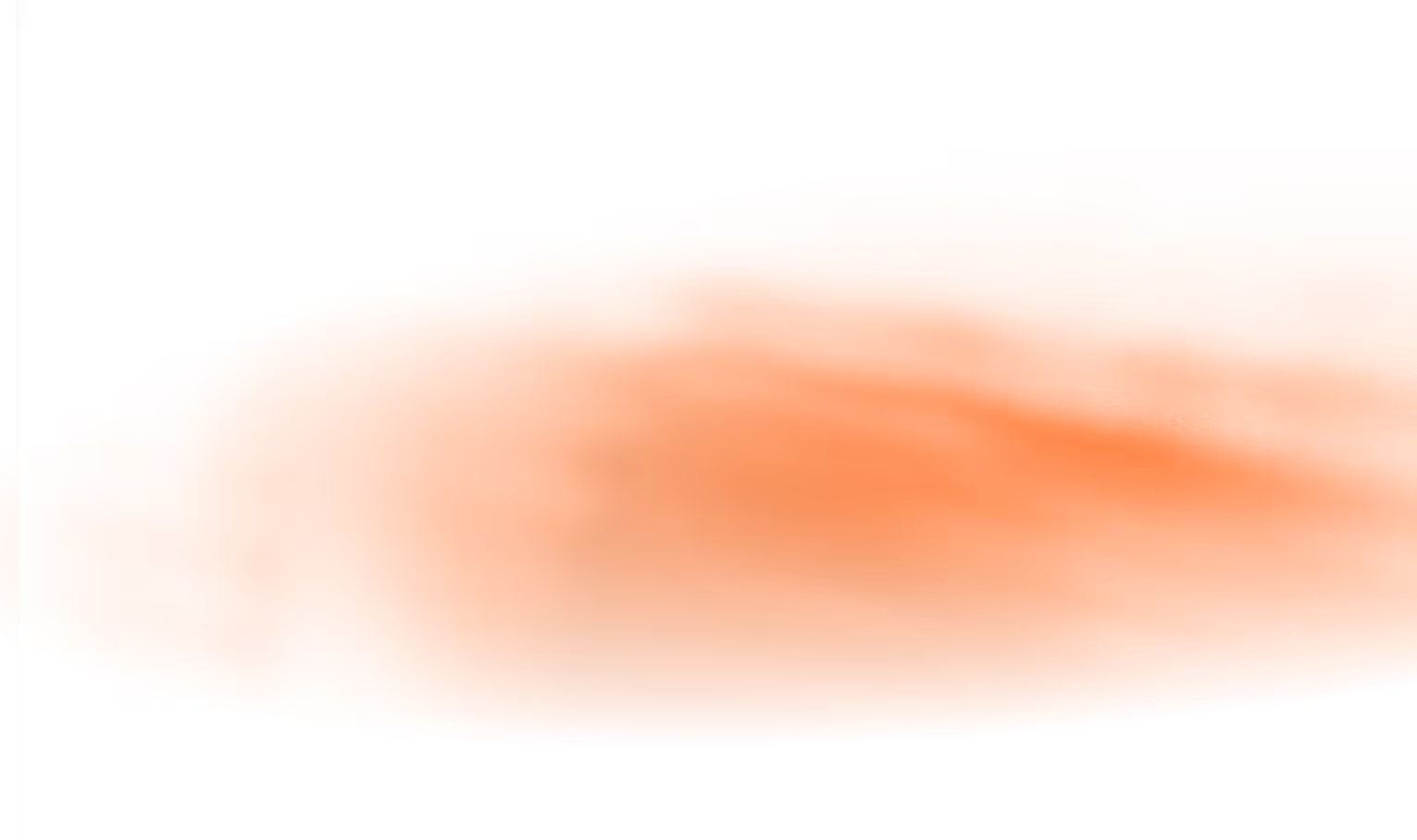
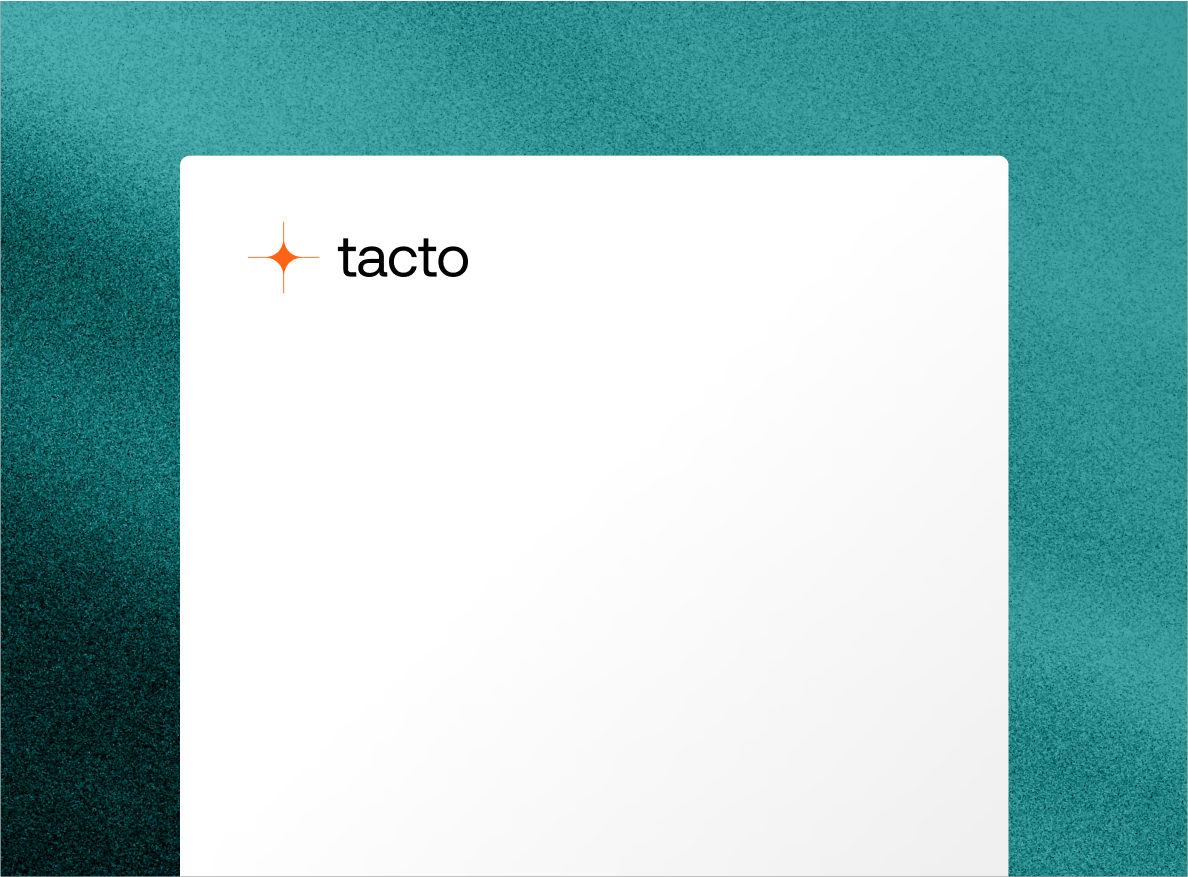