Procurement Glossary
Needs analysis: definition & important aspects for buyers
Systematic requirements analysis forms the foundation for successful procurement processes and prevents costly mistakes in Procurement. This structured overview shows you how you can identify potential savings and optimize your company's security of supply through professional requirements analysis.
Needs analysis in a nutshell:
Requirements analysis is a systematic process for determining and quantifying a company's current and future material requirements. It forms the basis for efficient procurement planning and helps Procurement to avoid supply bottlenecks and achieve cost savings through optimized order quantities.
Example: An automotive supplier carries out a quarterly demand analysis for electronic components, in which an annual requirement of 50,000 units is determined by evaluating consumption data, forecasts and seasonalities, resulting in a 25% reduction in stock levels and a cost saving of 120,000 euros.
Needs analysis: principles and methods
Needs analysis is a fundamental process in strategic corporate planning and operational management. It is used to systematically determine and evaluate the current and future needs of a company or organization. Careful needs analysis enables resources to be used optimally, costs to be minimized and security of supply to be guaranteed. This guide highlights the most important aspects of needs analysis, from the methodological basics to practical application examples and modern analysis tools. The correct implementation of a requirements analysis is crucial for the sustainable success of companies and forms the basis for efficient procurement processes.
What is a needs analysis?
The requirements analysis is a fundamental step in the procurement process in which a company's exact need for goods or services is determined. It serves to define the requirements in terms of quantity, quality and delivery time. A thorough analysis allows resources to be used efficiently, costs to be optimized and security of supply to be guaranteed.
Key elements of the needs analysis
Significance for Procurement
In Procurement , the requirements analysis forms the basis for all further process steps. It enables procurement strategies to be planned and implemented effectively. By knowing the exact requirements, companies can select suppliers in a targeted manner, take advantage of volume discounts and optimize delivery times. It also helps to minimize stock levels and avoid bottlenecks.
Needs analysis: from manual needs assessment to data-driven forecasts
Requirements analysis is at the heart of effective purchasing. Building on the theoretical basis, in practice it makes it possible to precisely determine actual requirements and thus make optimum use of resources. However, in order to meet the increasing demands of the market, there is a need to evolve from traditional methods to modern, technology-based approaches. This transformation is necessary in order to increase accuracy, efficiency and responsiveness.
Old: Manual determination of requirements
Traditional approach: In traditional companies, requirements are often determined manually. Purchasing employees collect information through direct communication with the specialist departments, review historical consumption data and use simple tools such as Excel spreadsheets. This approach is not only time-consuming, but also prone to errors. The limited possibilities of data analysis lead to inaccurate forecasts, which can result in overstocks or supply bottlenecks. In addition, there is a lack of flexibility to react to market analyses at short notice.
New: Advanced Demand Forecasting
Advanced demand forecasting: Modern approaches rely on advanced forecasting techniques. By using AI in Procurement and machine learning, large amounts of data are analyzed in order to make precise predictions. Real-time data from ERP systems, sales figures, market trends and even external factors such as weather data are incorporated into the analysis. This enables dynamic and flexible demand planning. The benefits are obvious: reducing stock levels by up to 30%, minimizing supply bottlenecks and increasing customer satisfaction through reliable delivery times.
Practical example: Automotive industry
A leading automotive manufacturer has implemented Advanced Demand Forecasting to optimize its demand planning. By integrating sales data from dealer networks and real-time production data, the company was able to increase forecasting accuracy by 20%. This led to a reduction in inventory ratios by 15 % and shortened response times to market changes. In addition, delivery bottlenecks were virtually eliminated, which significantly increased customer satisfaction.
Conclusion on the needs analysis
Demand analysis is an indispensable tool of modern purchasing, which contributes significantly to the company's success through precise planning and systematic implementation. It not only enables cost savings and increases in efficiency, but also minimizes risks in the supply chain. With increasing digitalization and the use of AI-supported technologies, demand analysis is constantly evolving and offers companies new opportunities for even more precise and future-oriented demand planning.
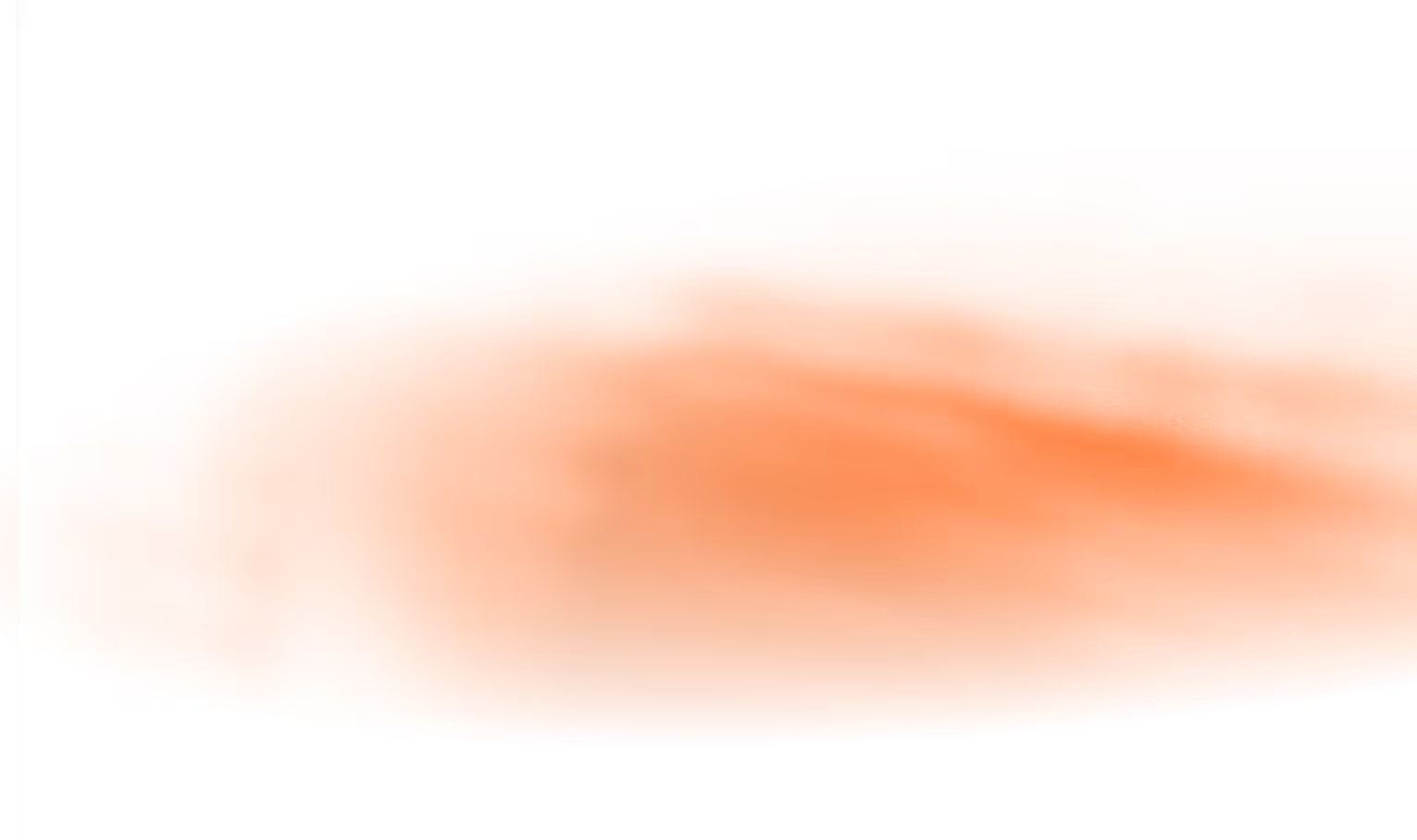