Procurement Glossary
Determining requirements: definition & important aspects for buyers
Who hasn't experienced it - too much material in stock costs money unnecessarily, too little material jeopardizes production. Professional needs assessment is the key to mastering this balancing act and having the right amount of material available at exactly the right time. With modern methods and digital tools, demand determination is evolving from a pure consumption estimate to a precise planning tool that gives companies a real competitive edge.
What is the needs assessment?
Determining requirements is a systematic process for identifying and quantifying the materials, goods and services required in a defined period of time. It forms the foundation of every procurement process and enables precise planning of order quantities and delivery dates. Determining requirements ensures that all necessary resources are available at the right time and in the right quantity.
Determining requirements - principles and methods
In strategic Procurement , the determination of requirements is the starting point for all further procurement activities and has a direct influence on costs, stock levels and security of supply. It comprises various methods - from consumption-driven (stochastic) to program-oriented (deterministic) procedures - and takes into account both historical data and future planning. Modern demand forecasting increasingly uses data-driven approaches and AI-supported forecasting models, which enable greater accuracy and flexibility. It is particularly important for purchasers that the determination of requirements takes into account not only the primary requirements (end products), but also the secondary and tertiary requirements (components and auxiliary materials) derived from them. Precise determination of requirements is therefore the key to optimizing procurement costs, inventories and ultimately the entire supply chain.
The two most important methods for determining requirements
The two most important methods of determining demand are the consumption-driven (stochastic) and the program-oriented (deterministic) method:
Consumption-controlled method:
- Based on the analysis of historical consumption data and statistical evaluations
- Particularly suitable for:
- Regularly required standard items
- Materials with constant consumption
- C-parts and indirect materials
- Functionality:
- Past consumption is analyzed and extrapolated
- Consideration of trends and seasonality
- Inclusion of safety stocks for fluctuations in demand
- Advantages:
- Simple implementation
- Low planning effort
- Easy to automate
- Disadvantages:
- Reacts with a delay to changes in demand
- Less precise with strongly fluctuating requirements
Program-oriented method:
- Based on specific production and sales plans and parts lists
- Particularly suitable for:
- Production materials
- A and B parts
- Order-related production
- Functionality:
- Derivation of demand from production planning
- Consideration of parts lists and work planning
- Precise quantity and schedule planning
- Advantages:
- High planning accuracy
- Direct response to changes in demand
- Precise scheduling possible
- Disadvantages:
- High planning effort
- Dependent on precise input data
- Susceptible to planning changes
The choice of the appropriate method depends on various factors, such as the type of material, the demand structure and the available database. In practice, both methods are often combined in order to make optimum use of the respective advantages.
Decisive factors for choosing the method of determining requirements
The choice of the appropriate method for determining requirements depends on several key factors. Firstly, the type of material is decisive - the consumption-based method is suitable for standard items and C-parts with regular consumption, while the program-based method is preferable for A- and B-parts and production-critical materials. The demand structure also plays an important role: the consumption-based method is efficient for even, easily predictable consumption, while the program-based method delivers more precise results for highly fluctuating or order-related requirements. The available database and the possible planning effort must also be taken into account - the program-oriented method requires detailed production and planning data as well as higher administrative effort, while the consumption-based method gets by with historical consumption data and is easier to implement. In practice, a combination of both methods is often recommended, with the more suitable method being used for different material groups.
Determining demand: from traditional planning to data-driven forecasting
Determining requirements is essential for ensuring efficient materials management. materials management and the optimization of stock levels. It plays a central role in procurement logistics and production planning. However, in times of volatile markets and increasing complexity, traditional methods are reaching their limits. This requires a transformation towards modern, data-driven approaches in order to meet the challenges.
Traditional approach: Traditional needs assessment
In traditional demand calculation, requirements are usually determined manually on the basis of historical consumption data. Planners use simple tools such as spreadsheets to estimate future requirements. This is characterized by static forecasts without taking current market changes or external influences into account. This approach is prone to inaccuracies, which can lead to overstocking or supply bottlenecks. It also requires a great deal of manual effort and is not very flexible in the face of short-term changes.
New: Data-Driven Forecasting
The modern approach to determining requirements relies on data-driven forecasts using advanced technologies such as AI in Procurement and machine learning. The integration of real-time data from ERP systems, sales statistics and external market information enables more precise and dynamic forecasts. Key innovations include big data analytics, the processing of large volumes of data and the consideration of complex influencing factors. This leads to greater accuracy in forecasting demand, reduces stock levels and significantly increases responsiveness to market changes.
Conclusion on the needs assessment
Precise determination of requirements is the foundation for a successful procurement process and is crucial for optimizing costs and inventories. The choice of the right method - consumption-based or program-based - depends on various factors such as material type, demand structure and available database. Modern, data-driven approaches and AI-supported forecasting models enhance traditional methods and enable even more accurate demand forecasting. The trend is clearly moving towards the hybrid use of different methods, supported by digital tools, in order to continuously optimize the determination of demand and ensure security of supply.
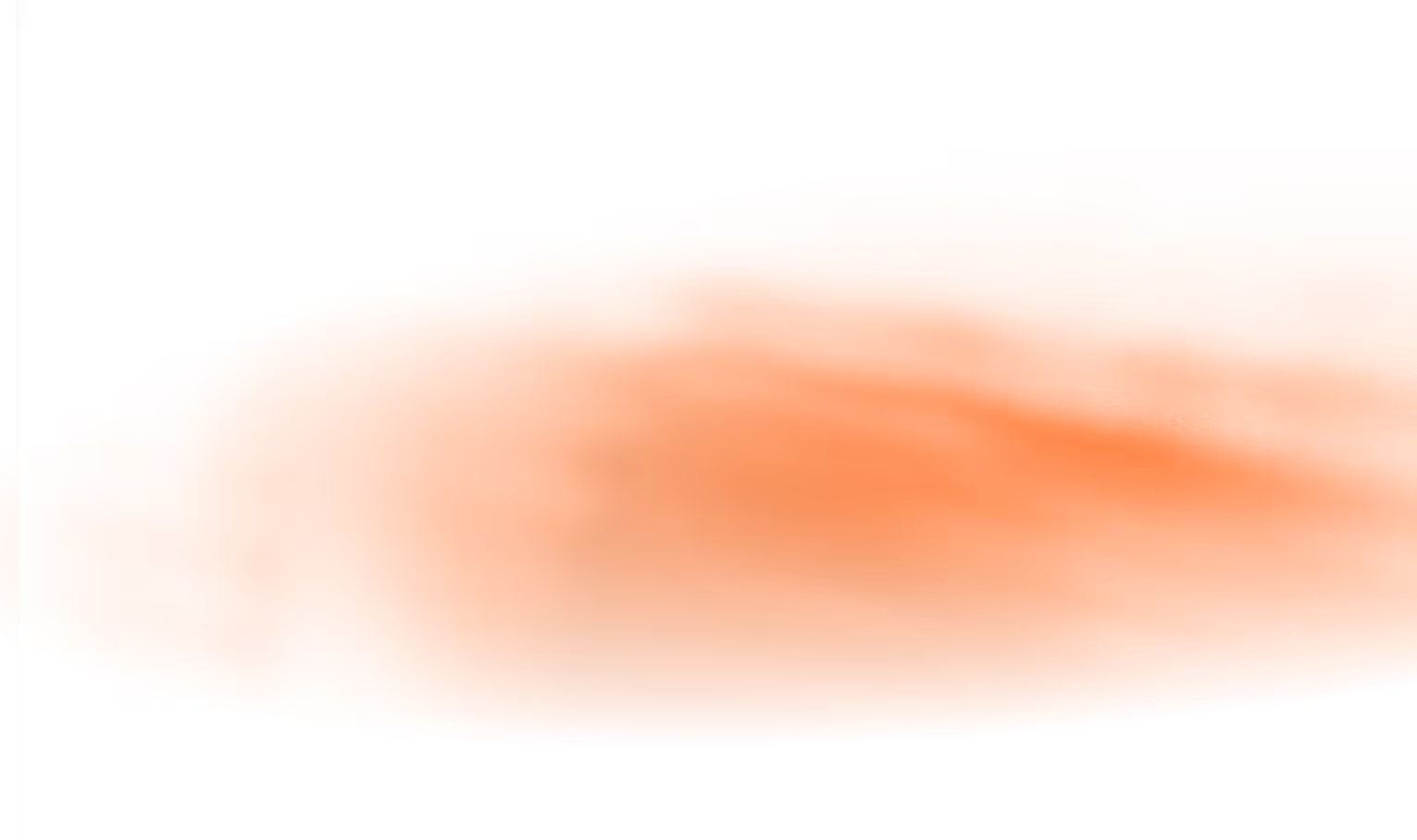