Procurement Glossary
Materials management: definition & important aspects for buyers
As a key success factor, materials management controls the optimal flow of materials and values within the company, thereby ensuring competitiveness in volatile markets. This structured overview shows how Procurement ensures security of supply and optimizes costs at the same time through efficient materials management.
Materials management in a nutshell:
Materials management encompasses all activities and processes for planning, managing and controlling the flow of materials and goods from the supplier to production. It is essential for Procurement , as it forms the basis for needs-based procurement, optimal stock levels and efficient use of resources.
Example: By introducing an integrated materials management system, an automotive supplier reduces its average stock levels from 2.5 to 1.8 million euros and shortens the lead time from order to goods receipt from 12 to 7 days.
Introduction to materials management
Materials management is a fundamental part of the operational value chain and encompasses all activities and processes related to the procurement, storage and provision of materials in a company. As the central interface between suppliers, production and other areas of the company, it plays a decisive role in the economic success of a company. Efficient materials management not only ensures that production is continuously supplied with the necessary resources, but also makes a significant contribution to reducing costs and optimizing stock levels. This guide covers the most important aspects of materials management in detail, from strategic planning to operational implementation.
What is materials management?
Materials management encompasses all of a company's activities relating to the procurement logistics, storage and provision of materials and goods. It ensures that the required materials are available in the right quantity, at the right time, in the right place and at optimum cost. The aim of materials management is to ensure the continuous supply of materials for production or sales while at the same time efficiently managing inventory and costs.
Core components of materials management
Significance for Procurement
Materials management plays a central role in Procurement , as it forms the interface between suppliers and internal users. Effective materials management makes it possible to reduce procurement costs, shorten delivery times and ensure the quality of purchased materials. For Procurement , this means working strategically with suppliers, planning requirements precisely and continuously improving internal processes.
Materials management: From traditional procurement to digital supply chain management
Building on the theoretical basis of materials management, its practical implementation is becoming increasingly complex and important in today's world. Companies are faced with the challenge of organizing material flows efficiently in order to remain competitive. The need to switch from traditional methods to modern, digital approaches is essential in order to meet the increasing demands of globalized markets.
Old: Traditional materials management
Traditional approach: In traditional materials management, processes were mainly carried out manually. Demand planning was often based on past consumption values and simple forecasts without taking real-time data into account. Orders were processed by telephone or fax and stock levels were recorded manually. Tools such as simple spreadsheets dominated day-to-day work. Key features were high safety stock levels to avoid supply shortages, but this led to high inventory costs. Limited transparency and slow responsiveness posed significant challenges, especially in the event of sudden market changes.
New: Digital Supply Chain Management
Digital supply chain management: Modern approaches integrate advanced technologies to optimize materials management. By using ERP systems and digital platforms, processes are automated and controlled in real time. Inventory management and data analytics improve demand planning, while the Internet of Things (IoT) enables accurate inventory monitoring. Key innovations such as cloud computing enable seamless collaboration with suppliers. Practical benefits include reduced stock levels, faster response times and increased transparency along the entire supply chain.
Practical example: Mechanical engineering company
A medium-sized mechanical engineering company implemented a digital supply chain management system. By integrating sensors in warehouse shelves, stock levels were monitored in real time. Automated orders were placed at defined minimum stock levels triggered directly to suppliers. The use of AI-supported forecasting tools enabled material requirements to be determined more precisely. This led to a 30% reduction in storage costs and a 20% reduction in procurement times. In addition, transparent data increased collaboration with suppliers, resulting in improved delivery reliability of 95%.
Conclusion on the importance of materials management for corporate success
Effective inventory management is a key success factor in modern materials management. By integrating digital technologies, precise demand planning and close supplier relationships, companies can optimize their inventories while ensuring security of supply. The key lies in striking a balance between cost savings and availability as well as continuously adapting to changing market conditions. Pioneering technologies such as AI and IoT will continue to revolutionize materials management and open up new potential for optimization.
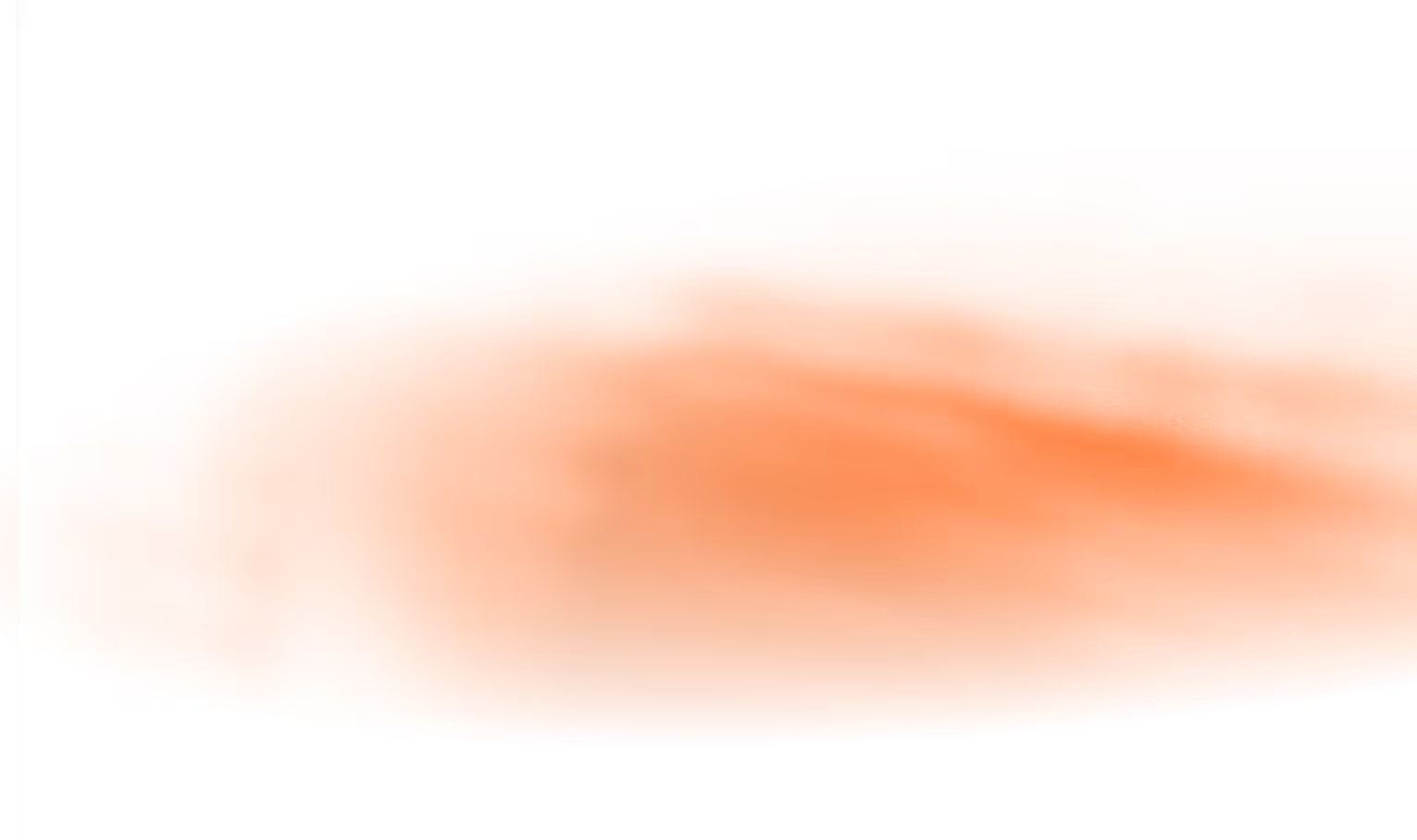
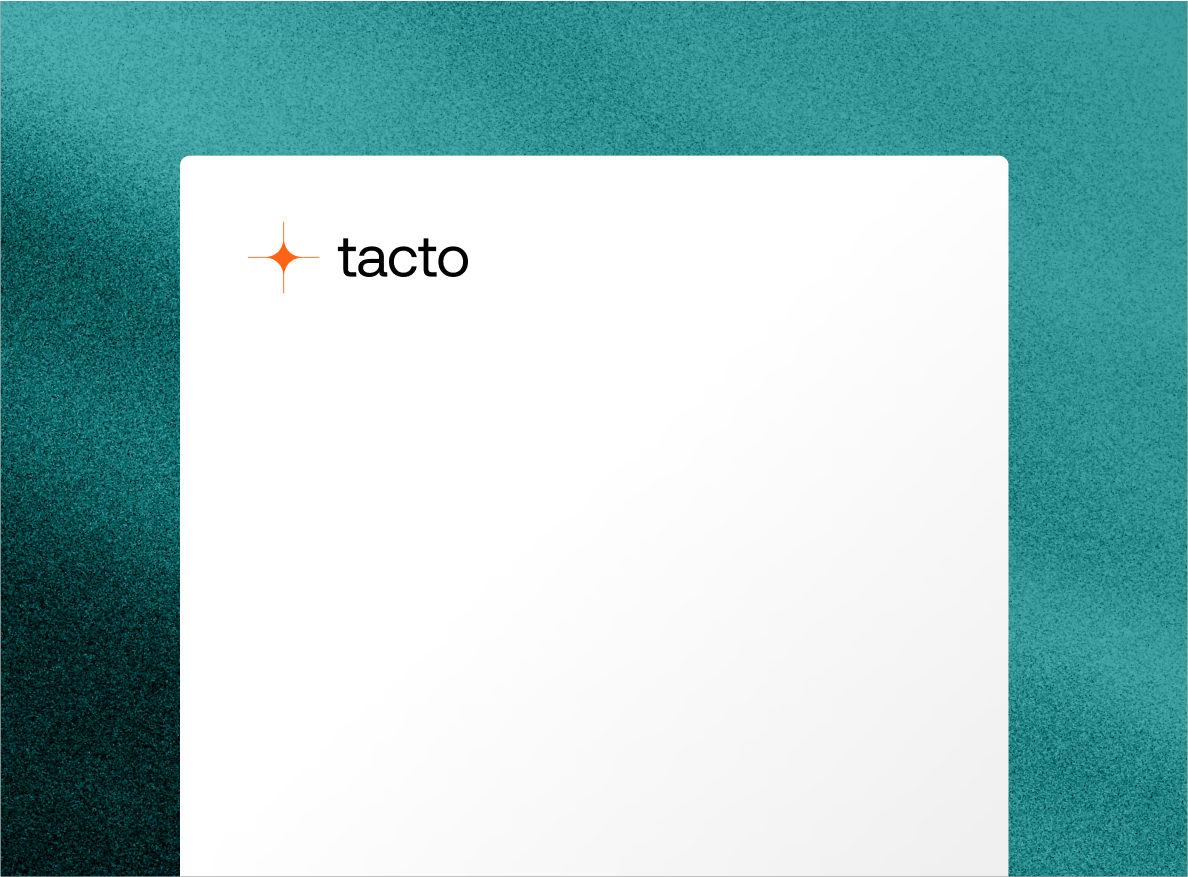