Procurement Glossary
Minimum stock: definition and important aspects for buyers
Minimum stock levels ensure the continuous availability of materials and protect companies from costly production interruptions. This structured overview shows how Procurement achieves a balance between security of supply and capital commitment by optimizing minimum stock levels.
Minimum stock in a nutshell:
The minimum stock level defines the minimum quantity of a material or product that must always be in stock in order to avoid production bottlenecks. For Procurement , this is a critical control parameter for ensuring security of supply while optimizing warehousing costs at the same time.
Example: An automotive supplier specifies a minimum stock level of 500 units for critical electronic components, which corresponds to a production requirement of 2 weeks and offers sufficient security against supply bottlenecks with a delivery time of 10 days.
Minimum stock - basics and optimization
The minimum stock level is a fundamental concept in warehousing and materials management. It defines the minimum quantity of goods or materials that should always be in stock to ensure the company's security of supply. Defining an optimal minimum stock level is of strategic importance, as it should prevent supply bottlenecks on the one hand, but must also take capital commitment and storage costs into account on the other. In this introduction, we will take a closer look at the most important aspects of minimum stock levels, how they are calculated and their significance for efficient warehousing.
What is the minimum stock level?
The minimum stock level, also known as safety stock, is the defined minimum quantity of an item in the warehouse that should not be exceeded. It serves as a buffer to cushion unforeseen fluctuations in demand, delivery delays or disruptions in supply chain resilience. By maintaining the minimum stock level, a company ensures that it is always able to deliver and that production or sales processes are not interrupted.
Core elements of the minimum stock
Importance of minimum stock levels in Procurement
In procurement, minimum stock levels are essential to ensure a continuous supply for production and customers. An optimally defined minimum stock level helps buyers to minimize the risk of supply bottlenecks and control storage costs at the same time. It contributes to improving delivery capability and customer satisfaction and helps to cushion unexpected market or supplier developments.
Minimum stock: from static to dynamic stock models
Based on the theoretical understanding of the minimum stock level, this serves as an essential safety reserve in warehousing. In practice, however, it is a challenge to determine the optimal minimum stock level, as too much stock leads to increased costs, while too little stock increases the risk of supply bottlenecks. Traditional methods often use static calculations that do not do justice to dynamic market conditions. Therefore, there is a need to move from static to dynamic inventory management to increase efficiency and responsiveness.
Old: Static minimum stock
Traditional approach: In traditional inventory management, the minimum stock level was often determined by fixed values or simple formulas, for example as a multiplier of average consumption or delivery time. Companies determined static safety stock levels based on historical data and empirical values. The calculations were usually done manually or with simple spreadsheets. This approach was uncomplicated, but could not react flexibly to fluctuations in demand or delivery times. The main problems were overstocking, which led to high storage costs, and understocking, which caused supply bottlenecks.
New: Dynamic inventory management
Dynamic Inventory Optimization: The modern method of inventory management uses advanced analytics and technologies to dynamically adjust minimum stock levels. Real-time data from ERP systems and the application of machine learning algorithms are used to accurately forecast consumption patterns and delivery times. Factors such as seasonal fluctuations, promotions and market analysis are taken into account. This makes it possible to continuously optimize minimum stock levels and minimize bottlenecks and excess stock. The implementation of inventory management software and the integration of supplier data significantly increase transparency and responsiveness along the supply chain.
Practical example: Automotive industry
A leading automotive manufacturer implemented a dynamic inventory management system to optimize the minimum stock levels of spare parts in its warehouses. By analyzing real-time consumption data and supplier performance, minimum stock levels were reduced by 20% without compromising delivery performance. At the same time, capital tied up in the warehouse fell by 15 million euros annually and delivery reliability increased by 10%. The introduction of predictive analytics made it possible to identify potential bottlenecks at an early stage and proactively initiate countermeasures.
Conclusion on minimum inventory planning
Minimum stock levels are an indispensable tool in modern inventory management. It not only ensures continuous supply capability and production stability, but also minimizes economic risks. Successful implementation requires a careful balance between security of supply and cost efficiency as well as regular adjustment to changing market conditions. With increasing digitalization and AI-supported optimization, inventory management is becoming even more precise and dynamic, offering companies new opportunities to increase efficiency.
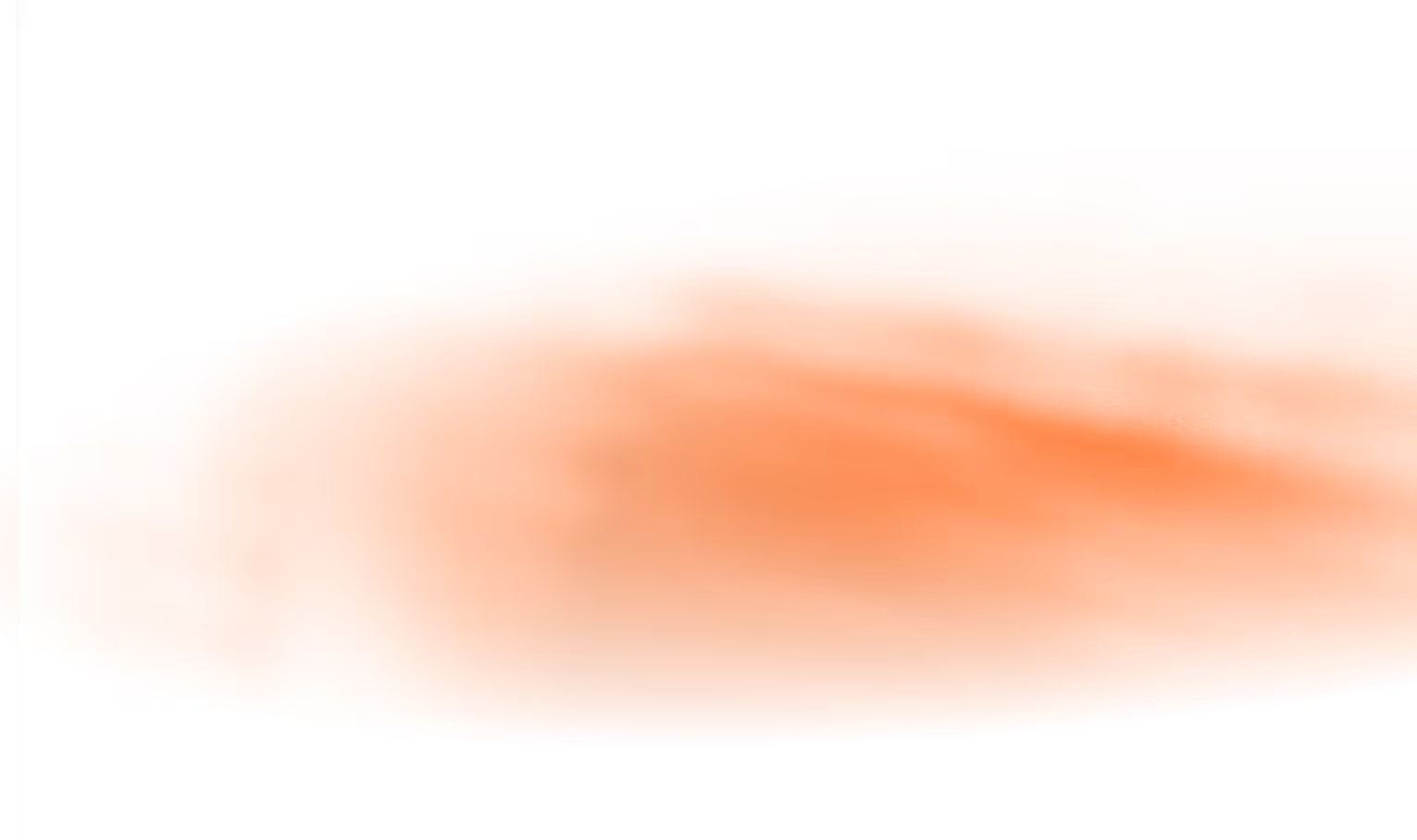