Procurement Glossary
Safety stock: definition and important aspects for buyers
Safety stock protects companies from supply bottlenecks and production stoppages and is therefore an important component of security of supply. This overview shows you how to determine the optimum safety stock for your company and thus find the balance between security of supply and capital commitment.
Safety stock in a nutshell:
Safety stock is a quantity of material held in addition to normal stock to compensate for delivery delays and fluctuations in demand. For Procurement , it serves as an important control instrument to ensure security of supply while optimizing warehousing costs.
Example: An automotive supplier maintains 2 weeks of safety stock for critical electronic components, based on an average lead time of 4 weeks and a historical delivery reliability of 95%, avoiding production interruptions despite global supply shortages.
Introduction to safety stock controlling
Safety stock is an essential component of warehousing and inventory management in companies. It serves as a buffer to compensate for unexpected fluctuations in demand or delivery delays and thus ensure security of supply. Determining the optimum safety stock level is a complex task that must take into account various factors such as delivery times, fluctuations in demand and service levels. In this guide, you will learn the most important basics about safety stock, how it is calculated and practical strategies for optimal stock management.
What is a safety stock?
Safety stock, also known as buffer or minimum stock, is a strategically defined reserve of materials or goods that a company holds in order to compensate for unexpected fluctuations in demand or delivery delays. This stock serves to maintain delivery capability and production readiness by minimizing the risk of bottlenecks. Safety stock is therefore a central element in inventory management and supports the stability of the supply chain.
Core elements of the safety stock
Importance of safety stock in Procurement
In Procurement , safety stock is a crucial tool for ensuring the continuous supply of production and supplying customers on time. An appropriately sized safety stock makes it possible to react flexibly to market changes and supplier failures. At the same time, it helps to optimize costs by avoiding unnecessary stock surpluses and reducing the capital commitment period.
Safety stock: From static warehousing to dynamic stock optimization
Safety stock plays a crucial role in inventory management in order to avoid supply bottlenecks and production interruptions. Traditionally, this inventory has been defined by fixed buffers, often resulting in high storage costs. However, in an increasingly volatile market environment, the need for more flexible and efficient methods is growing. The transformation to dynamic approaches enables companies to optimize inventory levels while ensuring security of supply.
Old: Static safety stocks
Traditional approach:
In traditional inventory management, safety stocks were determined on the basis of historical consumption data and fixed buffer sizes. Companies used simple formulas to maintain a constant stock level, regardless of current market changes. Typical tools were manual calculations and static parameters in the ERP system. This often led to excessive stock levels, high capital commitment and limited flexibility. The main problems with this approach were the inability to react adequately to sudden fluctuations in demand or supplier delays, which in turn affected inventory analysis.
New: Dynamic inventory optimization
Dynamic Safety Stock:
The modern method relies on dynamic inventory optimization using advanced technologies and real-time data. Integrated software solutions are used to continuously analyze current sales figures, supplier evaluations and market trends. Machine learning algorithms predict fluctuations in demand and automatically adjust safety stock levels. This innovation makes it possible to reduce stock levels by up to 30% without jeopardizing the ability to deliver. Practical benefits include lower storage costs, faster response times and improved customer satisfaction thanks to increased product availability.
Practical example: Electronics industry
A global electronics manufacturer implemented a dynamic inventory management system. By integrating real-time sales data and supplier information, the safety stock was significantly reduced. Within one year, inventory costs were reduced by 25%, while delivery capability was increased by 15%. The use of predictive analytics made it possible to react proactively to market changes, resulting in a competitive advantage in a fast-moving market.
Conclusion on safety stock planning
Safety stock is an indispensable tool in modern inventory management. It enables companies to avoid supply bottlenecks while maintaining a high level of service quality. Successful implementation requires a careful balance between costs and benefits as well as regular adaptation to changing market conditions. With the use of modern technologies such as AI and predictive analytics, the calculation and optimization of safety stocks is becoming increasingly precise and efficient.
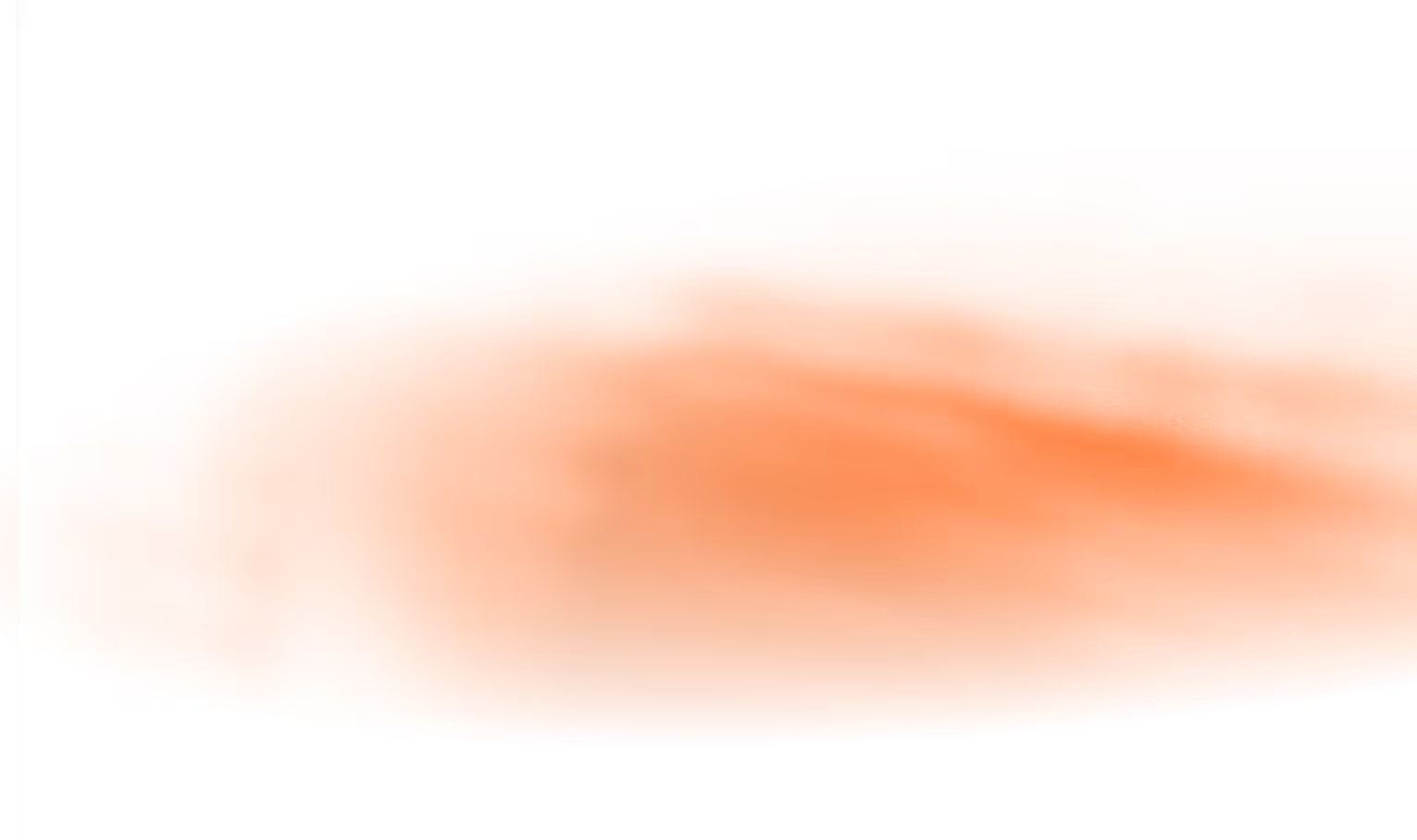