Procurement Glossary
Inventory analysis: definition & important aspects for buyers
Inventory analysis provides important insights into stock levels and material flows and therefore forms the basis for efficient procurement decisions. In this overview, you will learn how you can optimize your inventory costs through systematic inventory analyses and at the same time ensure security of supply.
Inventory analysis in a nutshell:
Inventory analysis is a systematic examination of existing stocks in terms of quantity, value and movement frequency. It enables Procurement to optimize procurement planning and helps to avoid excess stock and reduce capital commitment.
Example: An automotive supplier carries out an ABC analysis and discovers that 20% of its items (A parts) account for 80% of the inventory value, whereupon it reduces the order quantities for these parts by 30% and changes the order frequency from quarterly to monthly.
Inventory analysis - a key to efficient purchasing management
Inventory analysis is a fundamental instrument of operational controlling and warehouse management. It is used to systematically record, evaluate and optimize stock levels in companies. Through a thorough inventory analysis, companies can reduce their capital commitment, optimize storage costs and ensure security of supply. This guide highlights the most important aspects of inventory analysis, from basic methods and various analysis tools to modern digital solutions for efficient inventory management.
What is inventory analysis?
Inventory analysis is the systematic examination and evaluation of a company's stock levels. It comprises the recording of all available materials and products, their consumption and replenishment. The main aim of inventory analysis is to determine the optimum stock level in order to ensure production and delivery capability, minimize storage costs and reduce capital commitment. The analysis enables overstocks and stock shortages to be identified and measures to optimize stock levels to be introduced.
Core elements of the inventory analysis
Importance of inventory analysis in Procurement
In procurement management, inventory analysis plays a crucial role in optimizing warehousing and ordering processes. It enables purchasers to make well-founded decisions about order quantities and timing, thus ensuring security of supply. Effective inventory analysis helps to reduce costs by reducing excess stock and avoiding stock-outs. It also supports the development of strategic purchasing decisions and improves relationships with suppliers through clear demand planning.
Inventory analysis: from manual collection to real-time data analysis
Inventory analysis is an essential tool for effectively managing stock levels and optimizing costs. Building on the theoretical basis, it enables companies to reduce excess stock and avoid bottlenecks. Given the increasing market dynamics and complexity of supply chains, there is a growing need to modernize traditional methods and adapt inventory analysis to the requirements of the digital economy.
Old: Manual stock control
Traditional approach: In the past, stock analysis was mainly carried out manually. Stock levels were recorded through regular stocktaking, where employees counted goods and entered data manually into lists or simple IT systems. This was characterized by time-consuming processes, a high susceptibility to errors and limited up-to-dateness of the data. Tools such as stock cards and simple spreadsheets dominated practice. The main challenges lay in the lack of transparency, delayed information flows and the inability to react quickly to changes in consumption or demand.
New: Automated real-time inventory analysis
Real-time inventory analytics: Modern approaches rely on automation and digital technologies to monitor and analyze inventories in real time. Data is continuously collected and processed through the use of ERP systems, IoT devices and AI algorithms. Innovations such as machine learning enable forecasts of future demand, while big data analyses take into account external factors such as market analysis. Practical benefits include a reduction in stock levels of up to 30%, increased delivery capability and a significant reduction in capital commitment costs. Changes such as the integration of suppliers into digital networks also improve the entire supply chain.
Practical example: Increasing efficiency in retail through real-time data
An international retailer implemented automated inventory analysis using RFID technology and cloud-based data platforms. This reduced stock levels by 25% and increased inventory turnover by 40%. Stock-outs were reduced by 60%, leading to a 15% increase in sales. The investment paid for itself within 18 months and significantly improved customer satisfaction.
Conclusion on the inventory analysis
ConclusionInventory analysis is an indispensable tool in modern procurement management. By systematically combining ABC and XYZ analyses, companies can optimize their inventories and significantly reduce costs. Success lies in the consistent implementation of the insights gained and the digital integration of all processes. It is particularly important to continuously adapt the analysis methods to changing market conditions. This is the only way for companies to secure their long-term competitiveness and guarantee their ability to deliver.
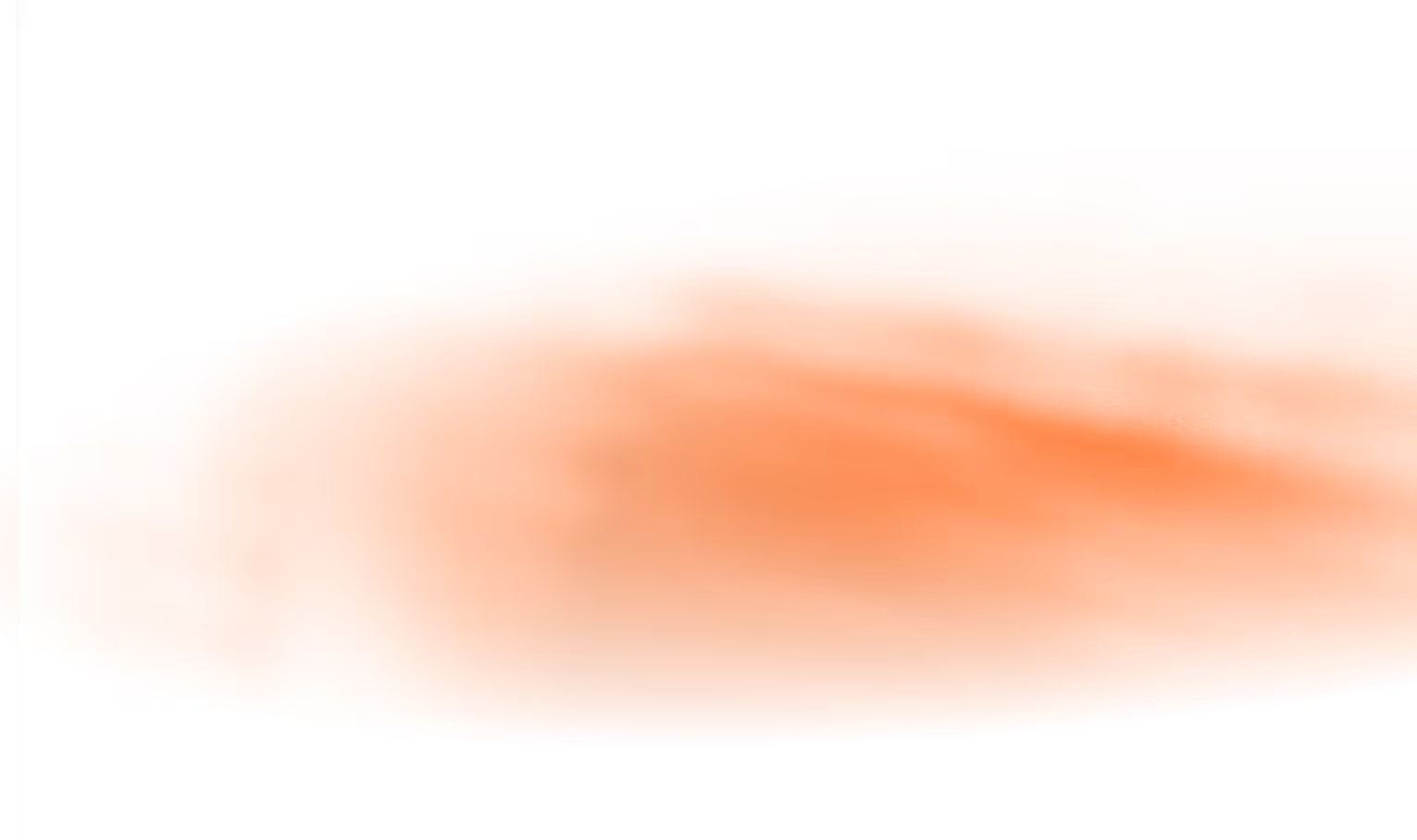
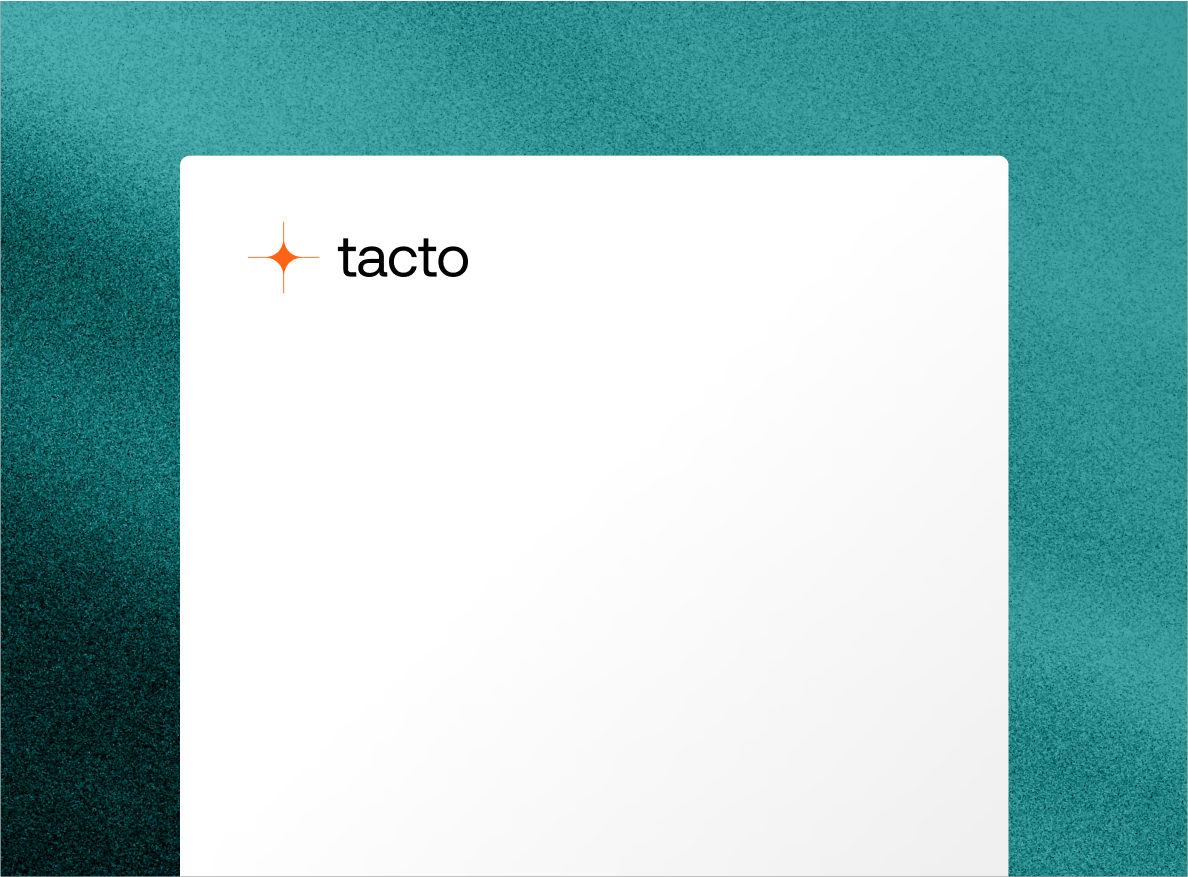