Procurement Glossary
Inventory optimization: definition and important aspects for buyers
Inventory optimization enables companies to find the perfect balance between security of supply and capital commitment, thereby creating real competitive advantages. The following overview shows how Procurement can both reduce costs and improve supply capability through systematic inventory optimization.
Inventory optimization in a nutshell:
Inventory optimization is the systematic control and adjustment of stock levels to minimize warehousing costs while at the same time ensuring delivery capability. For Procurement , this means achieving a continuous balance between security of supply and capital commitment through intelligent procurement strategies.
Example: By introducing a Kanban system, an automotive supplier reduces its average stockholding from 30 to 12 days, thereby lowering capital commitment by 1.2 million euros and reducing storage costs by 25%.
Inventory optimization - An introduction
Inventory optimization is a fundamental aspect of modern supply chain management and warehousing. It aims to find the optimum balance between security of supply and capital commitment. In times of global supply chains and increasing customer demands, efficient inventory management is becoming ever more important. Successful inventory optimization enables companies to reduce their storage costs and improve their ability to deliver at the same time. In this guide, you will learn the most important principles, methods and strategies for successful inventory optimization as well as their practical implementation in day-to-day business.
What is inventory optimization?
Inventory optimization refers to the strategic planning and management of stock levels to ensure the availability of materials and goods while minimizing storage costs. The aim is to achieve an optimal balance between holding sufficient stock to meet demand and avoiding excess stock, which ties up capital and increases risks such as obsolescence or spoilage.
Core elements of portfolio optimization
Significance for Procurement
For Procurement , inventory optimization plays a central role in controlling costs and increasing efficiency. By managing stock levels in a targeted manner, buyers can free up financial resources and reduce the risk of obsolescence or spoilage. In addition, optimized inventory management enables faster reactions to market changes and strengthens the position in supplier negotiations through clearly defined requirements.
Inventory optimization: from static warehousing to AI-supported inventory planning
Inventory management is a decisive factor for the efficiency and competitiveness of companies. Building on the theoretical foundations, the practical implementation is aimed at achieving the optimum balance between the availability of goods and storage costs. In a constantly changing economy, it is essential to rethink traditional methods and integrate modern approaches in order to meet increasing demands and ensure supply capability.
Old: Traditional warehousing
Traditional approach: In traditional warehousing, stocks are often managed on the basis of historical consumption data and static safety stock. Order quantities and timing are determined manually, often without taking into account dynamic market developments or fluctuations in demand. Tools such as simple spreadsheets or basic ERP systems serve as the main tools. This approach leads to high stock levels and increased inventory costs. There is also a risk of overstocking or shortages, as volatile market conditions and supply chain disruptions cannot be adequately taken into account.
New: AI-supported inventory optimization
Artificial intelligence: The modern approach uses artificial intelligence and machine learning to take inventory optimization to a new level. By analyzing large amounts of data from various sources such as sales data, market developments and supplier data, precise demand forecasts can be created. Dynamic ordering algorithms adapt to changes in real time. This makes it possible to reduce stock levels by up to 30% and increase delivery capacity at the same time. Modern systems integrate seamlessly into existing IT infrastructures and offer dashboards for transparent real-time monitoring. The implementation of these technologies leads to a significant reduction in capital commitment and increases the company's agility to react to volatile market conditions.
Practical example: Optimization at XYZ GmbH
XYZ GmbH, a medium-sized mechanical engineering company, integrated an AI-supported inventory optimization solution into its supply chain processes. Within six months, the average stock level was reduced by 25%, which corresponded to a capital release of 1.5 million euros. At the same time, delivery readiness increased to 99%, allowing customer orders to be served faster and more reliably. More accurate forecasting reduced the number of urgent orders by 40% and the associated additional costs were significantly reduced.
Conclusion on portfolio optimization
Inventory optimization is an essential tool in modern purchasing and warehouse management. Through systematic analyses such as ABC classification and the use of digital technologies, companies can manage their inventories efficiently, reduce costs and optimize their ability to deliver. Success lies in the balance between sufficient availability of goods and minimal capital commitment. Pioneering technologies such as AI and IoT will further revolutionize inventory optimization and offer even more precise control options.
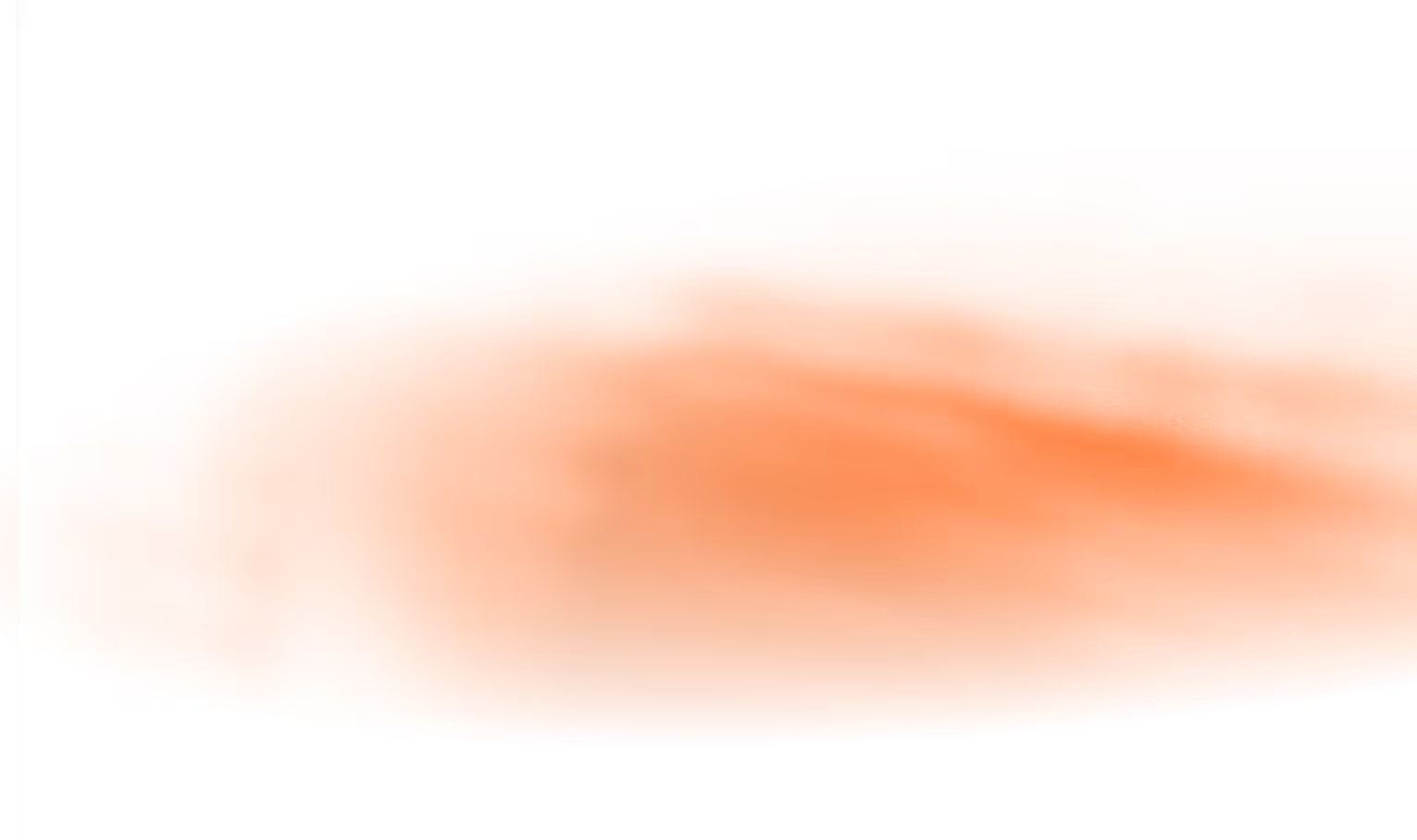
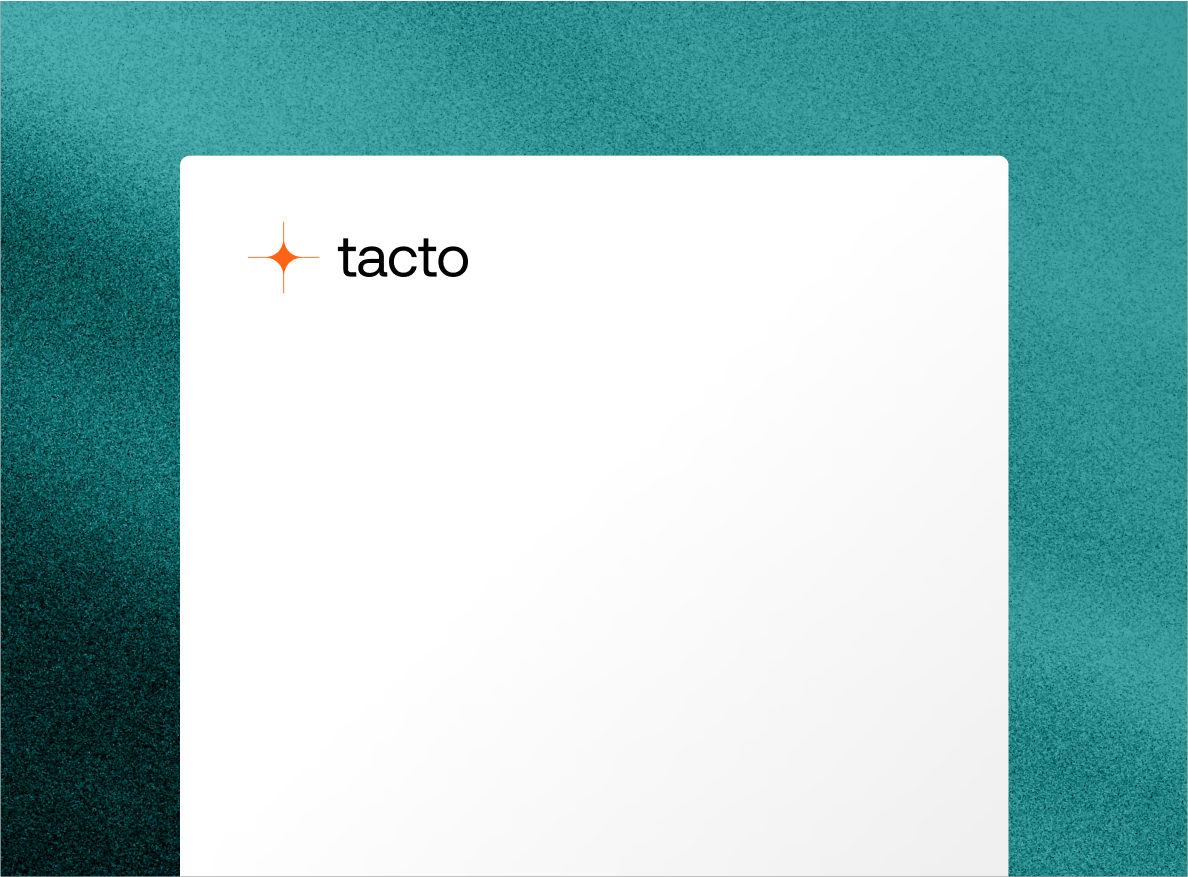