Procurement Glossary
Supply chain resilience: definition & important aspects for buyers
The increasing complexity and susceptibility to disruption of global supply chains requires new approaches to ensure security of supply and competitiveness in the long term. This structured overview shows how Procurement can contribute to strengthening supply chain resilience through targeted measures and thus ensure the long-term success of the company.
Supply chain resilience in a nutshell:
Supply chain resilience describes the ability of a supply chain to withstand disruptions, adapt and quickly restore normal operations. It is a strategic success factor for Procurement , as it ensures security of supply through targeted measures such as dual sourcing, inventory optimization and risk analyses.
Example: An automotive manufacturer reduced its dependency on a single semiconductor supplier in Asia by qualifying a second supplier in Europe and increasing safety stocks from 2 to 4 weeks, allowing production to continue with only a 15% reduction during the 2021 chip crisis.
Introduction to supply chain resilience
Supply chain resilience has gained considerable importance in recent years, especially since the COVID-19 pandemic and various geopolitical crises. It describes the ability of companies and their supply chains to successfully overcome external disruptions and challenges and to recover quickly from them. A resilient supply chain is characterized by flexibility, adaptability and resilience. In this introduction, we will highlight the most important aspects of supply chain resilience, from basic concepts to strategies for strengthening resilience and practical implementation approaches for companies.
What is supply chain resilience?
Supply chain resilience refers to the ability of a supply chain to respond flexibly to unexpected disruptions and recover quickly to ensure the continuity of the supply of goods and services. This resilience is becoming increasingly important as global supply chains become more complex and susceptible to risks such as natural disasters, political unrest or pandemic-related disruptions.
Core elements of supply chain resilience
- Risk management: Identification, assessment and prioritization of potential risks along the supply chain.
- Flexibility: Adaptable processes and systems that enable quick reactions to changes.
- Transparency: Clear visibility across all stages of the supply chain Visibility for early detection of disruptions.
- Redundancy: building up alternative sources of supply and stocks to safeguard against failures.
Significance for Procurement
Supply chain resilience is critical for Procurement to ensure security of supply and minimize business disruption. Through strategic sourcing practices, buyers can strengthen resilience by identifying risks early, building robust supplier relationships and developing alternative sourcing strategies.
- Continuity assurance: Ensuring continuous deliveries despite external disruptions.
- Cost reduction: Avoidance of costs due to production downtime or expensive rush orders.
- Competitive advantage: Increased responsiveness and adaptability to market dynamics.
Supply chain resilience: from traditional risk management to an integrated resilience strategy
Building on the theoretical foundation of supply chain resilience, it becomes clear how crucial a robust and adaptable supply chain is for a company's success. In practice, it is clear that traditional approaches are often not sufficient to meet current global challenges. The need for a transformation towards an integrated resilience strategy is underlined by increasing risks such as natural disasters, geopolitical tensions and pandemic events.
Old: Traditional risk management
Traditional approach: In the past, the focus of risk management in supply chains was on reactive measures. Companies often only recognized risks after disruptions had occurred and then reacted with short-term solutions. The instruments were usually limited to diversifying suppliers or holding safety stocks. Operational KPIs were mainly used for control, without in-depth analyses of supply chain complexity. This approach often led to increased costs and a lack of flexibility in the event of unexpected events.
New: Integrated resilience strategy
Resilience engineering: The modern approach focuses on proactively shaping the supply chain through comprehensive resilience strategies. Advanced technologies such as AI and big data analytics are used to identify and assess risks at an early stage. Companies integrate digital twins of their supply chains to simulate different scenarios and react optimally to changes. This enables flexible replanning of delivery routes and faster adaptation to market conditions. Close collaboration with suppliers and transparent information sharing make supply chains more agile and resilient. Practical benefits include a reduction in downtime of up to 50% and cost savings through optimized inventory levels.
Practical example: Automotive industry
A global automotive manufacturer implemented an integrated resilience strategy after natural disasters affected suppliers in Asia. By using real-time data analytics, the company was able to identify alternative suppliers and restructure production. Within two weeks, new supply chains were established, minimizing production downtime. The measures led to a 30% increase in supply chain stability and reduced inventory costs by 15%.
Conclusion on supplier assessment and supply chain resilience
Supply chain resilience is essential in today's globalized economy. Successful implementation requires a balanced combination of risk management, strategic supplier diversification and digital transformation. While implementation is associated with challenges and costs, the long-term benefits outweigh them: increased security of supply, reduced dependencies and increased competitiveness. Companies that proactively invest in their supply chain resilience are better prepared for future crises and can react flexibly to market changes.
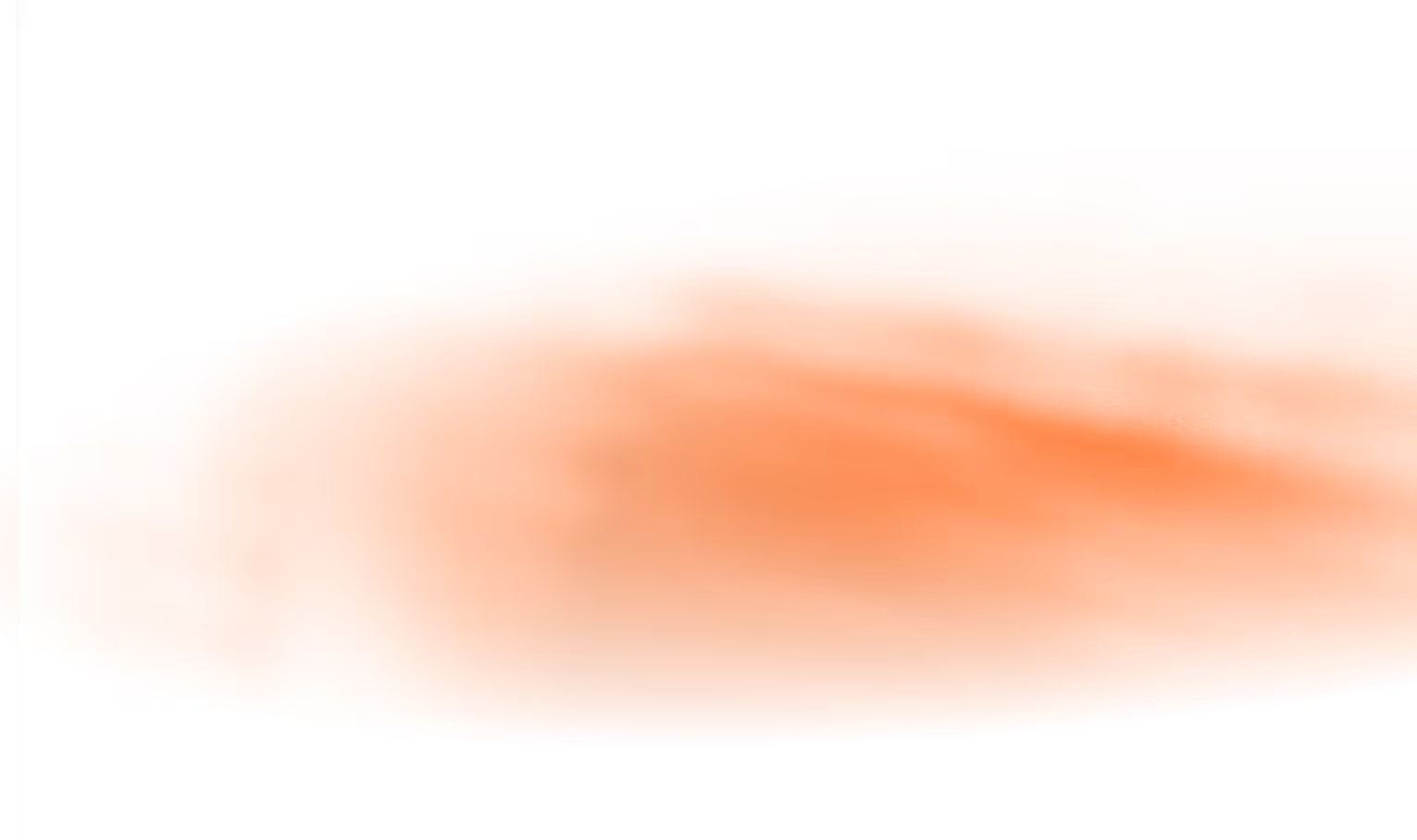
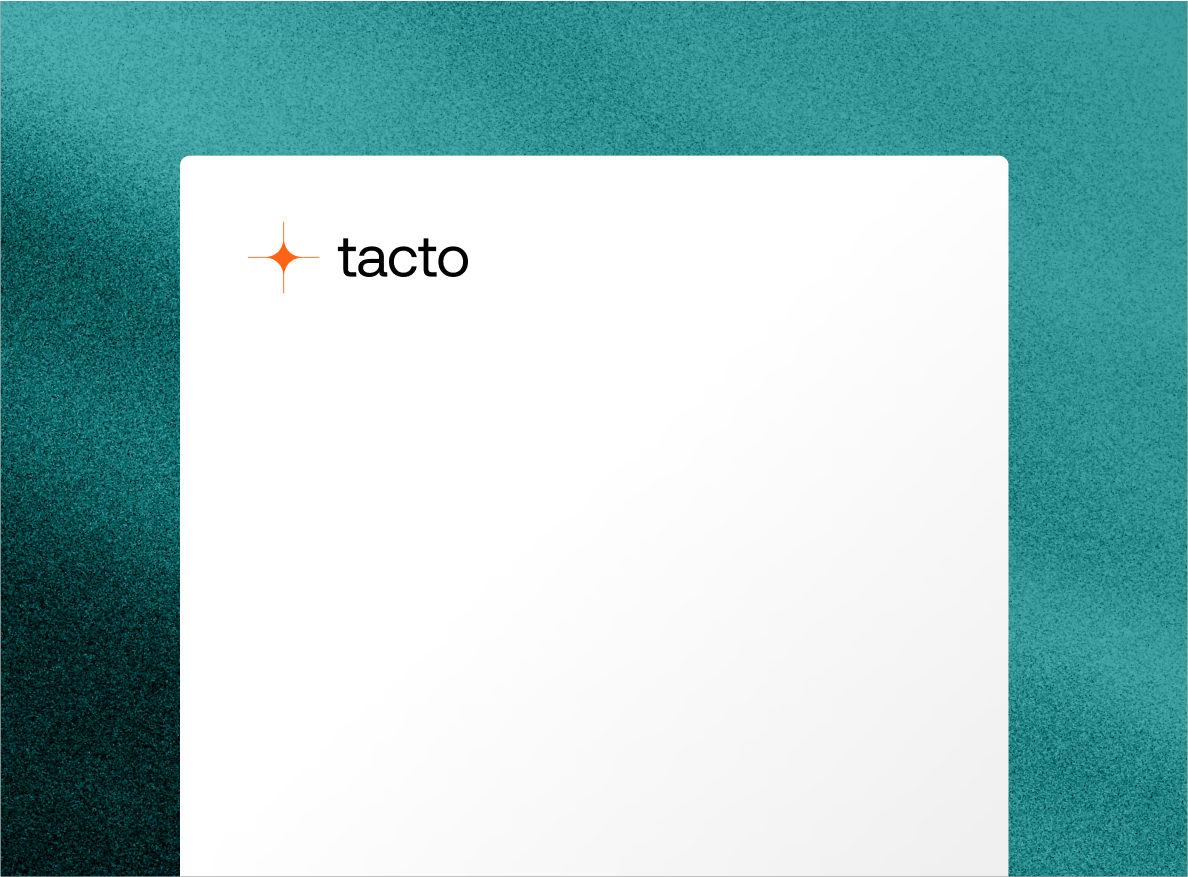