Procurement Glossary
ISO 9001: Definition & important aspects
As an internationally recognized standard, ISO 9001 establishes the foundations for successful quality management and helps companies to optimise their processes and reliably meet customer requirements. This structured overview shows you the most important requirements of the standard and how you can implement them profitably in your purchasing processes.
ISO 9001 in a nutshell:
ISO 9001 is an internationally recognized standard for quality management systems that defines requirements for the systematic control of company processes. For Procurement , it serves as an important criterion for supplier selection and evaluation as well as for ensuring standardized procurement processes.
Example: A medium-sized company introduces ISO 9001 certification over a period of 6 months, documents 15 core processes in Procurement and reduces the complaint rate for supplier parts from 5% to 1.8% thanks to standardized processes.
Contents
1.
Introduction to ISO 9001 for purchasers
2.
Basics of ISO 9001 - What is ISO 9001?
3.
Implementation of ISO 9001 in Procurement - steps and best practices
4.
ISO 9001 vs. other quality standards - comparison and advantages
5.
Conclusion: ISO 9001 as a strategic quality standard for efficient purchasing management
Introduction to ISO 9001 for purchasers
In an increasingly globalized and competitive economy, ensuring high quality standards is crucial to a company's success. ISO 9001 provides a proven framework for quality management that helps companies to systematically improve their processes and increase customer satisfaction. For purchasers, ISO 9001 is particularly relevant as it provides clear guidelines for optimizing procurement processes and ensuring the quality of purchased materials and services. This article explains the basics of ISO 9001, the benefits and challenges of implementing it, how it compares to other quality standards and provides practical recommendations for buyers to successfully implement it.
Basics of ISO 9001 - What is ISO 9001?
ISO 9001 is an internationally recognized standard for quality management systems (QMS) developed by the International Organization for Standardization (ISO). The standard defines the criteria for effective quality management and can be used across all industries. It is based on several fundamental principles of quality management, including customer focus, leadership, employee involvement, process-oriented approach, continuous improvement, fact-based decision making and relationship management.
Main components of ISO 9001:
- Quality policy and objectives: Definition of the strategic direction and measurable objectives for quality management.
- Process management: Identification, documentation and optimization of business processes to ensure quality.
- Risk managementIdentification and assessment of risks that could affect the quality of products and services.
- Documentation management: Creation and maintenance of the necessary documentation to demonstrate compliance with the standard.
- Internal audits: Regular review of the QMS to ensure continuous compliance and improvement.
- Management evaluation: Periodic evaluation of the QMS by the management level to identify opportunities for improvement.
Importance for buyers:
- Quality assurance: Ensuring that the materials and services purchased meet the defined quality standards.
- Increased efficiency: Optimized processes lead to faster and more cost-effective procurement procedures.
- Risk minimization: Proactive management of risks in the supply chain protects against quality defects and delivery failures.
- Building trust: ISO 9001-certified suppliers are considered to be more reliable and of higher quality, which strengthens trust in supplier relationships.
Best Practices:
- Management commitment: The support and active involvement of management are crucial to the success of ISO 9001 implementation.
- Employee training: Regular training and sensitization of employees to quality management processes.
- Continuous improvement: Establishment of a culture of continuous improvement and adaptation of processes.
- Clarity of documentation: Creation of clear and comprehensible documentation that is easily accessible and up-to-date.
- Use of technology: Use of quality management software to automate and optimize QMS processes.
ISO 9001: From internal quality control to international quality management
Based on the understanding of ISO 9001 as an internationally recognized standard for quality management systems, the practical significance for companies worldwide becomes clear. Systematic quality assurance is essential in order to survive global competition and meet increasing customer requirements. The need for transformation arises from the demand for continuous improvement and ensuring consistent process flows.
Old: Traditional quality control
Traditional approach: In the past, quality assurance was often based on reactive measures. Companies only carried out quality checks after production in order to sort out faulty products. This approach used simple methods such as random sampling and relied heavily on the expertise of individual employees. The lack of standardization led to inconsistent quality standards and increased error costs. In addition, the lack of documentation made it difficult to trace and analyze the causes of quality problems.
New: Implementation of the ISO 9001 quality management system
ISO 9001 Quality Management System: The modern approach is based on process-oriented quality management in accordance with ISO 9001, whereby all company processes are systematically recorded, documented and continuously improved. The introduction of standardized procedures and regular internal audit plans ensures that quality standards are maintained and optimized. By focusing on customer requirements and risk management, companies can act proactively. Practical benefits include increased efficiency, reduced error rates and increased customer satisfaction. ISO 9001 certification also serves as proof of trust towards business partners and strengthens competitiveness.
Practical example: Increasing product quality in the medical device industry
A manufacturer of medical devices decided to implement the ISO 9001 quality management system in order to meet strict regulatory requirements. Within a year of implementation, production errors were reduced by 40%. Thanks to clearly defined processes and responsibilities, delivery reliability improved to 98%. In addition, end customer satisfaction increased measurably, which was reflected in a 25% increase in sales. The successful certification enabled the company to enter new international markets.
Conclusion: ISO 9001 as a strategic quality standard for efficient purchasing management
ISO 9001 is an indispensable tool for purchasers who want to establish an effective and sustainable quality management system. By systematically optimizing procurement processes, ensuring high quality standards and promoting continuous improvement, ISO 9001 makes a significant contribution to increasing competitiveness and achieving corporate goals. Despite the potential challenges, such as the implementation effort and the associated costs, the advantages clearly outweigh the disadvantages. With clearly defined processes, committed employees and the support of modern technologies, ISO 9001 can be successfully integrated into purchasing management. This not only promotes the quality and efficiency of procurement, but also strengthens the trust of customers and business partners in the reliability and professionalism of the company. Overall, ISO 9001 is a valuable tool in every buyer's toolbox and helps companies to make their supply chains more efficient, more secure and of higher quality.
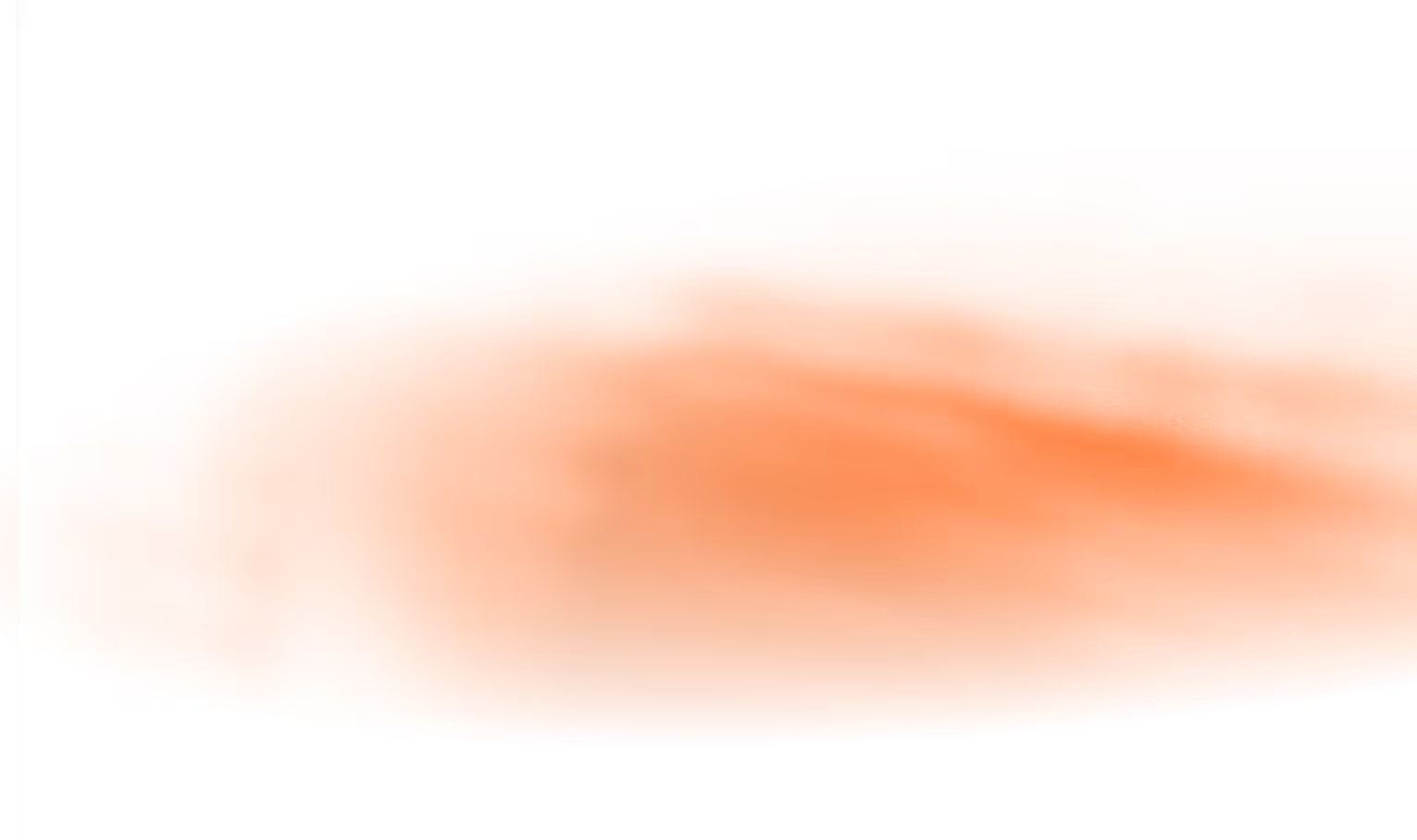
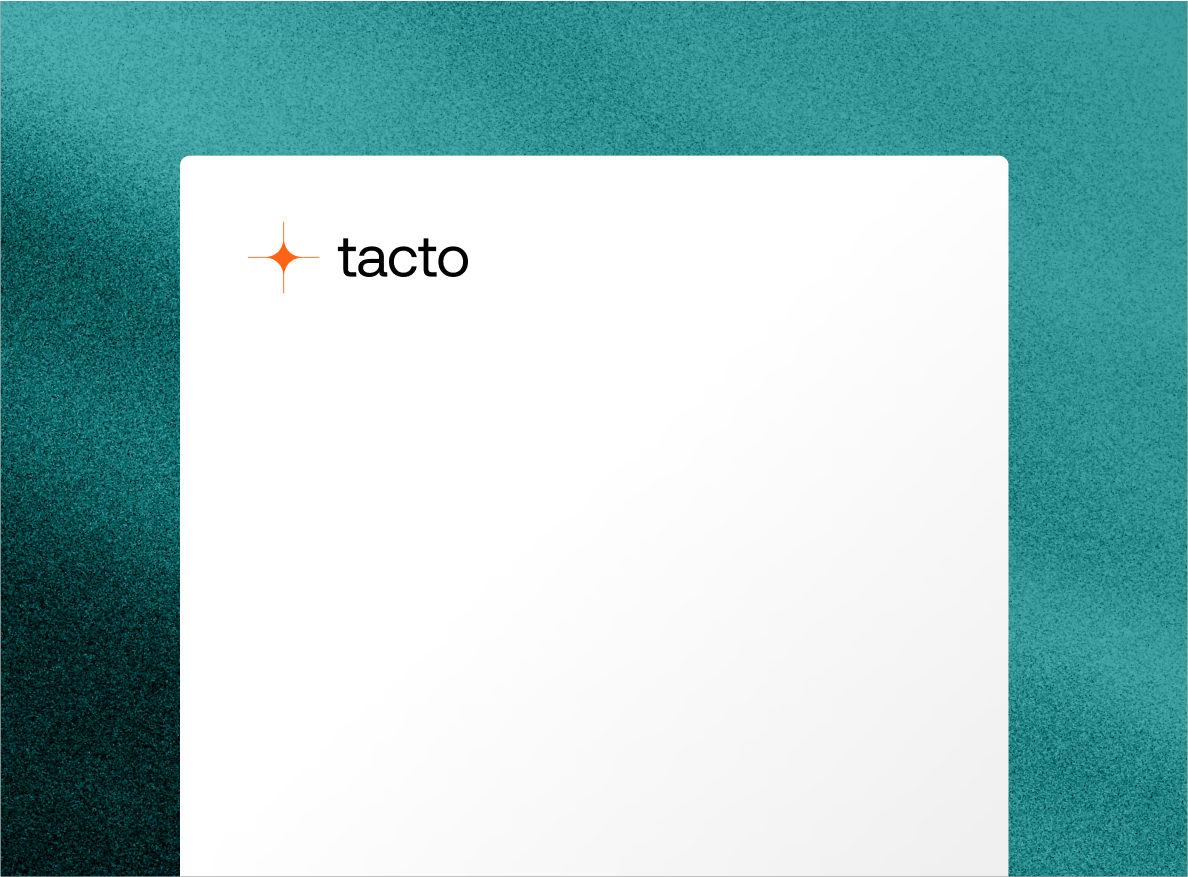