Procurement Glossary
Make or buy analysis: definition & important aspects
The make-or-buy analysis supports companies in making strategic decisions between in-house production and external sourcing and thus contributes significantly to competitiveness. This structured overview shows how Procurement makes well-founded sourcing decisions and identifies potential savings by systematically evaluating all relevant factors.
Make or buy in a nutshell:
The make-or-buy analysis is a systematic decision-making process for evaluating whether products/services should be manufactured in-house or purchased externally. For Procurement , this is a strategic tool for optimizing the company's vertical integration and cost structure.
Example: An automotive supplier evaluates the production of a component and determines through a make-or-buy analysis that in-house production with costs of €85/unit compared to external procurement for €72/unit with an annual production of 50,000 units leads to savings of €650,000 per year through outsourcing.
Introduction to make or buy analysis for buyers
In a dynamic and highly competitive economy, the efficient design of the procurement strategy is crucial to a company's success. Make or buy analysis is an essential tool to help buyers make strategic decisions about whether to manufacture certain products or services internally or source them externally. This analysis considers a variety of factors, including cost, quality, availability of resources and strategic importance, to identify the best sourcing option. This article highlights the fundamentals, benefits and challenges of make or buy analysis and offers practical recommendations for its successful implementation.
What is a make or buy analysis?
The make or buy analysis is a systematic evaluation process in which companies decide whether they should produce certain products or services themselves (make) or purchase them from external providers (buy). This decision is based on a thorough analysis of various economic, strategic and operational factors.
Core components of the make or buy analysis:
- Cost analysis: Comparison of internal production costs with external procurement costs, including direct and indirect costs.
- Quality assessment: Assessment of the quality standards that can be achieved internally compared to external suppliers.
- Capacity check: Review of internal capacities and resources for the production of the product or service.
- Strategic importance: Assessment of the strategic importance of the product or service for the company.
- Risk assessment: Identification and assessment of potential risks in internal production or external procurement.
- Time factor: Analysis of the time required for internal production compared to rapid procurement from external suppliers.
Importance for buyers:
- Optimization of the procurement strategy: Support in selecting the most cost-efficient and highest-quality procurement option.
- Improving competitiveness: Companies can strengthen their market position by making well-founded decisions.
- Conservation of resources: Effective use of internal resources by focusing on core competencies.
- Risk minimization: Diversification of procurement sources and reduction of dependencies.
Carrying out a make or buy analysis:
- Identification of the products/services to be evaluated: Selection of the products or services to be subjected to a make or buy decision.
- Data collection and analysis: Collection of relevant data on costs, quality, capacities and other decision-relevant factors.
- Comparison and evaluation: Comparison of internal and external options based on the data collected.
- Decision-making: Selection of optimal procurement strategies based on the results of the analysis.
- Implementation: Implementation of the decision made and adaptation of the processes accordingly.
Best Practices:
- Detailed cost analysis: Consideration of all relevant cost factors, including hidden and long-term costs.
- Holistic approach: Inclusion of not only financial, but also qualitative and strategic aspects.
- Regular review: Continuous updating of make or buy decisions based on market analysis and company changes.
- Involvement of relevant stakeholders: Collaboration with various departments such as finance, production and quality management for a comprehensive basis for decision-making.
Make or buy analysis: From the traditional decision to advanced make or buy analysis
Building on the theoretical foundation of make or buy analysis, it is crucial to understand the practical implications for companies. In today's dynamic business landscape, a simple cost consideration is often no longer sufficient to make competitive decisions. The need to incorporate deeper strategic considerations and utilize modern technology is leading to a transformation from the traditional method to advanced analytical approaches. This change enables companies to operate more efficiently and achieve sustainable competitive advantages.
Old: Traditional make or buy analysis
Traditional approach: The traditional make-or-buy analysis focuses mainly on a direct cost-benefit analysis between in-house production and external procurement of a product or service. In practice, this means that companies survey their internal production costs and compare these with the offers of external suppliers. This method often uses static data and rarely takes into account factors such as long-term strategic effects, quality differences or flexibility requirements. Tools such as simple spreadsheets and linear costing models are commonly used. The main difficulties lie in the limited availability of data and the lack of consideration of indirect costs and non-cost factors, which can lead to suboptimal decisions.
New: Advanced Make or Buy Analysis
Advanced Make or Buy Analysis: The modern approach uses advanced technologies and comprehensive data analysis to make more informed decisions. By integrating big data, AI and machine learning, companies can now take into account not only costs, but also qualitative factors such as production capacities, risk management and market dynamics. In practical terms, this means using specialized software solutions that can simulate and forecast complex scenarios. Innovation points such as real-time data analysis and predictive modeling make it possible to react more quickly to market changes and manage strategic partnerships effectively. This leads to improved efficiencies, cost savings and increased competitiveness.
Practical example: Automotive industry
A leading car manufacturer was faced with the decision of whether to build the production of a new electric motor internally or procure it externally. Advanced Make or Buy Analysis was used not only to compare costs, but also to analyze factors such as supplier reliability, technological know-how and time to market. The use of simulation tools showed that the outsourcing-option would lead to a 15% faster time to market and savings of €10 million over five years. This informed decision allowed the company to focus its resources on core competencies while securing market share in the growing electric mobility sector.
Conclusion: Make or buy analysis as a strategic tool for efficient purchasing management
Make or buy analysis is an indispensable tool for buyers who want to make well-founded and strategic decisions in procurement management. By systematically evaluating internal production options against external procurement options, make or buy analysis helps companies to optimize costs, minimize risks and make their supply chains more efficient. Although conducting a make or buy analysis involves a certain amount of effort and complex decision-making processes, the advantages clearly outweigh the disadvantages. With clearly defined goals, precise data and a structured approach, make or buy analysis can make a significant contribution to increasing competitiveness and achieving corporate goals. By integrating this analysis into comprehensive purchasing and supply chain management, companies can continuously optimize their procurement strategies and successfully assert themselves in a dynamic market environment. Overall, the Make or Buy analysis is a valuable tool in every buyer's toolbox and helps companies to use their resources more efficiently and ensure sustainable business success.
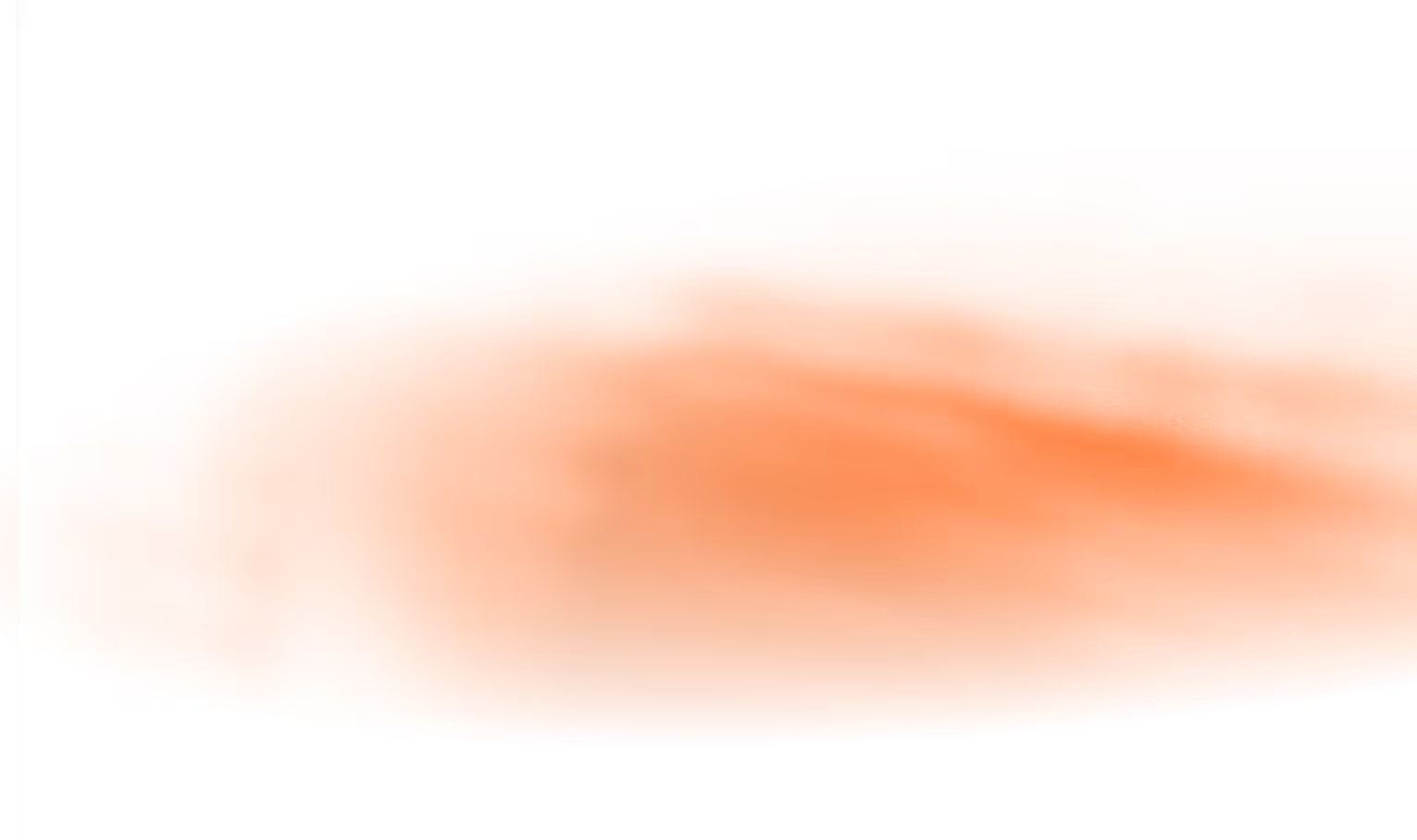
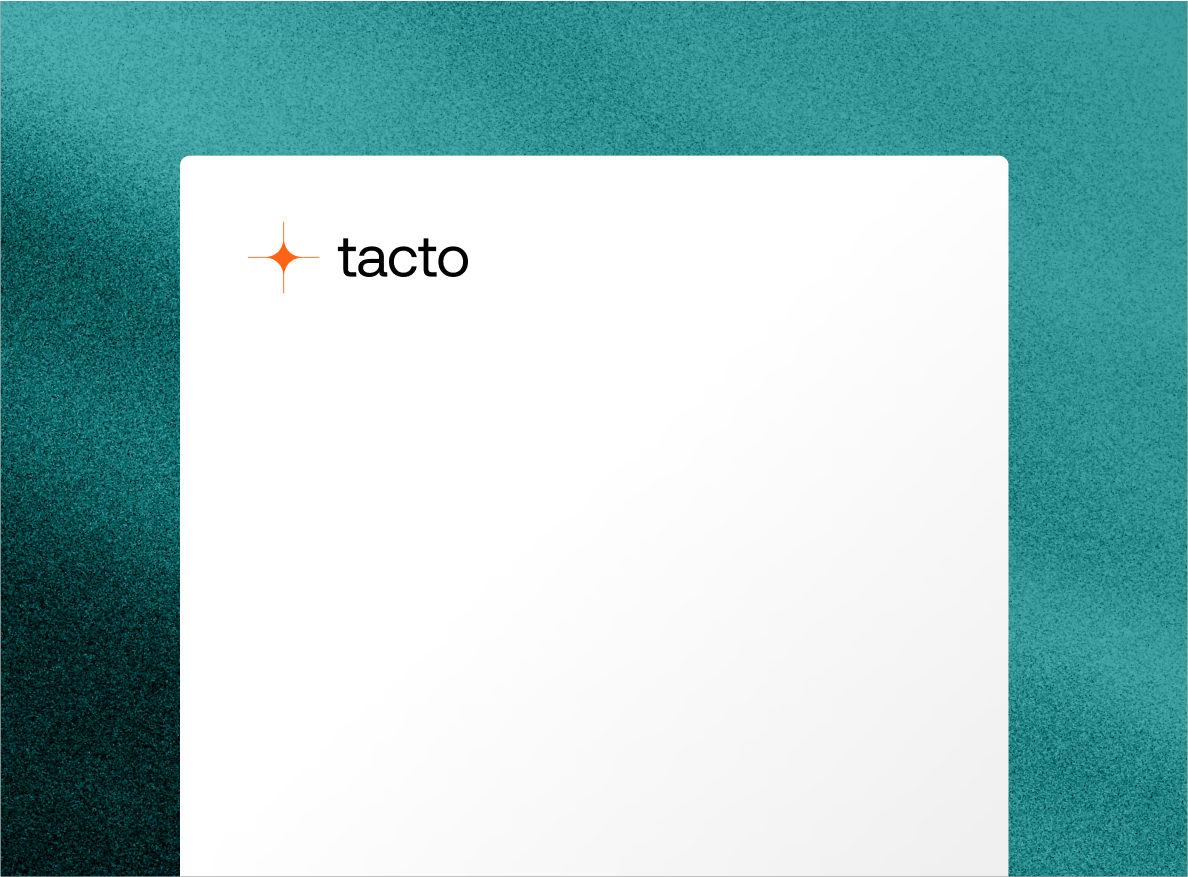