Procurement Glossary
Modular procurement: definition and important aspects for buyers
Modular sourcing is revolutionizing the procurement strategy by systematically splitting complex products into standardized assemblies, thereby creating enormous efficiency potential in the supply chain. This structured overview shows how Procurement can use modular sourcing concepts to cut costs, reduce complexity and significantly increase flexibility when working with suppliers.
Modular sourcing in a nutshell:
Modular sourcing is a procurement strategy in which complex products are divided into standardized subsystems (modules) and procured separately. For Procurement , this enables a reduction in supplier complexity while at the same time increasing flexibility and utilizing specialization advantages.
Example: A car manufacturer purchases only 5 pre-assembled cockpit modules from specialized system suppliers instead of 147 individual components, reducing procurement complexity by 80% and cutting assembly time by 45 minutes per vehicle.
Introduction to Modular Sourcing
Modular sourcing is an innovative approach in modern procurement strategy that has become increasingly important in recent years. In this concept, complex products are divided into individual, standardized modules that can be sourced from specialized suppliers. This strategy enables companies to optimize their procurement processes and at the same time benefit from the advantages of modularization. The combination of flexibility, cost savings and quality assurance makes modular sourcing an important tool in strategic Procurement. This guide takes a closer look at the fundamentals, opportunities and challenges of modular sourcing as well as its practical implementation in the corporate context.
What is modular sourcing?
In procurement management, modular sourcing refers to the strategy of purchasing complete modules or assemblies from external suppliers instead of manufacturing or procuring individual components in-house. Prefabricated, often standardized modules are purchased and integrated into the company's own end product. This approach enables companies to shorten development times, reduce costs and benefit from the expertise of specialized suppliers.
Core elements of modular sourcing
Significance for Procurement
In Procurement modular sourcing enables an effective procurement strategy that leads to cost savings and increased flexibility. By sourcing modules, companies can react more quickly to market changes and drive forward product innovations. It also reduces administrative costs, as fewer individual parts need to be coordinated.
Modular sourcing: from the procurement of individual parts to modular procurement
Building on the theoretical basis of modular sourcing, there is a clear shift in practice from traditional procurement strategies to innovative approaches. Companies are increasingly recognizing the practical advantages of sourcing entire modules instead of individual components. This transformation is necessary in order to meet the increasing demands for efficiency, flexibility and speed in globalized markets.
Old: Procurement of individual parts
Traditional approach: In traditional single-part procurement, all required components are procured separately from different suppliers. The internal assembly of these individual parts requires considerable resources in terms of inventory figures, logistics costs and personnel. This approach is characterized by complex supply chains with many interfaces, which leads to increased coordination effort and potential sources of error. The main limitations are long production times, high costs due to multiple handling and low flexibility in the event of product changes or adaptations.
New: Modular Sourcing
Modular sourcing: With the modern implementation of modular sourcing, companies rely on the Procurement of prefabricated modules from specialized suppliers. This approach brings innovative improvements such as reducing the number of suppliers, closer partnerships and joint development projects. Practical benefits include a shorter time-to-market, cost savings through economies of scale and increased product quality thanks to the expert knowledge of module manufacturers. The internal depth of added value is reduced, allowing companies to concentrate on their core competencies.
Practical example: Automotive industry
A leading car manufacturer has successfully switched to modular sourcing. Instead of sourcing and assembling individual components such as seats, electronics and trim separately, the company sources complete interior modules from a specialized supplier. This has led to a 20% reduction in assembly time per vehicle, a 15% reduction in warehousing costs and a 10% improvement in product quality as measured by customer satisfaction. In addition, thanks to the close cooperation with the supplier, the manufacturer was able to introduce innovative interior concepts to the market more quickly.
Conclusion on the modularization of procurement activities
Modular sourcing is a forward-looking procurement strategy that can offer companies significant competitive advantages. Strategic cooperation with specialized suppliers can shorten development times, optimize costs and accelerate innovation. Despite possible risks such as supplier dependency and loss of know-how, the advantages outweigh the disadvantages - especially if clear structures, careful supplier selection and well thought-out interface management are established.
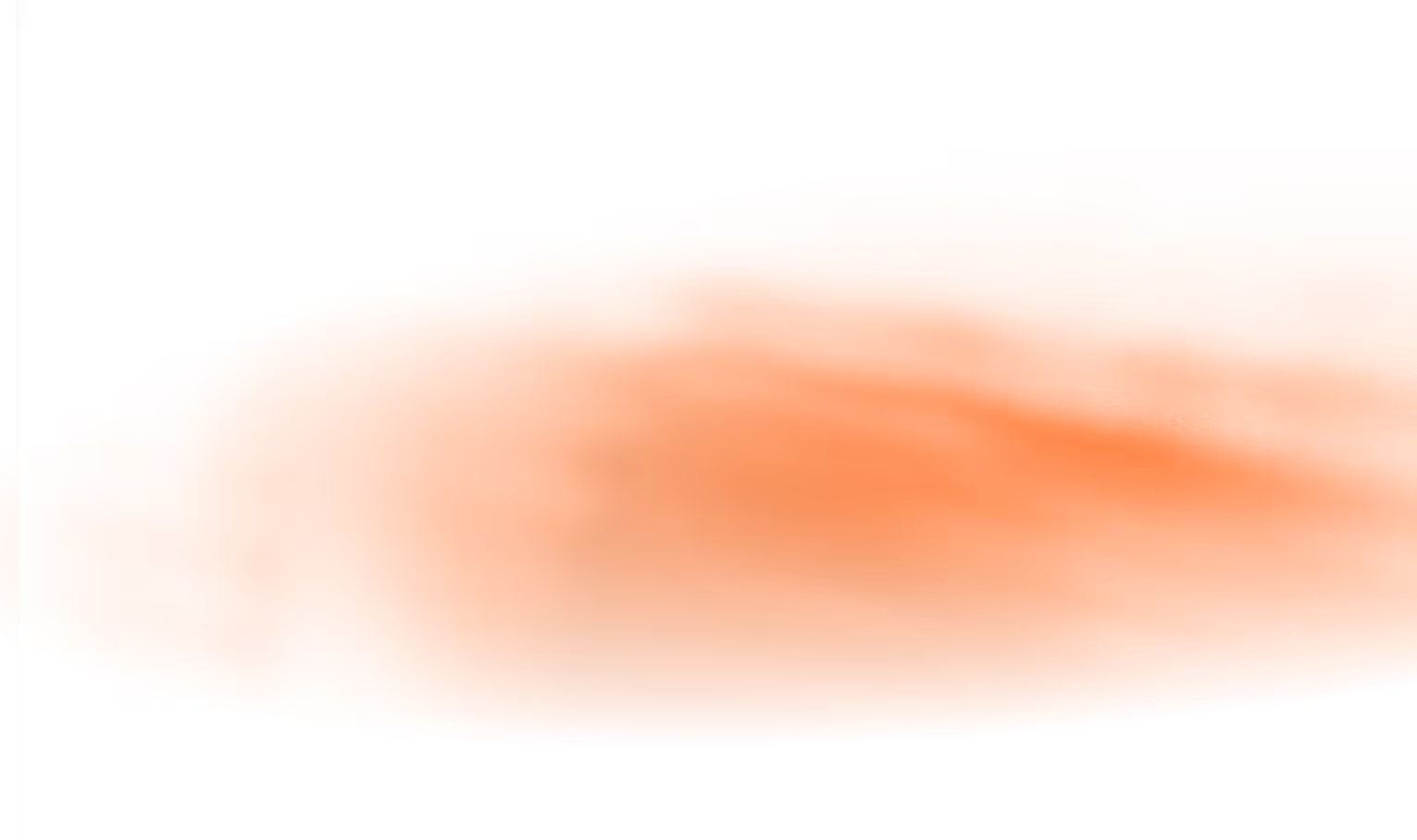
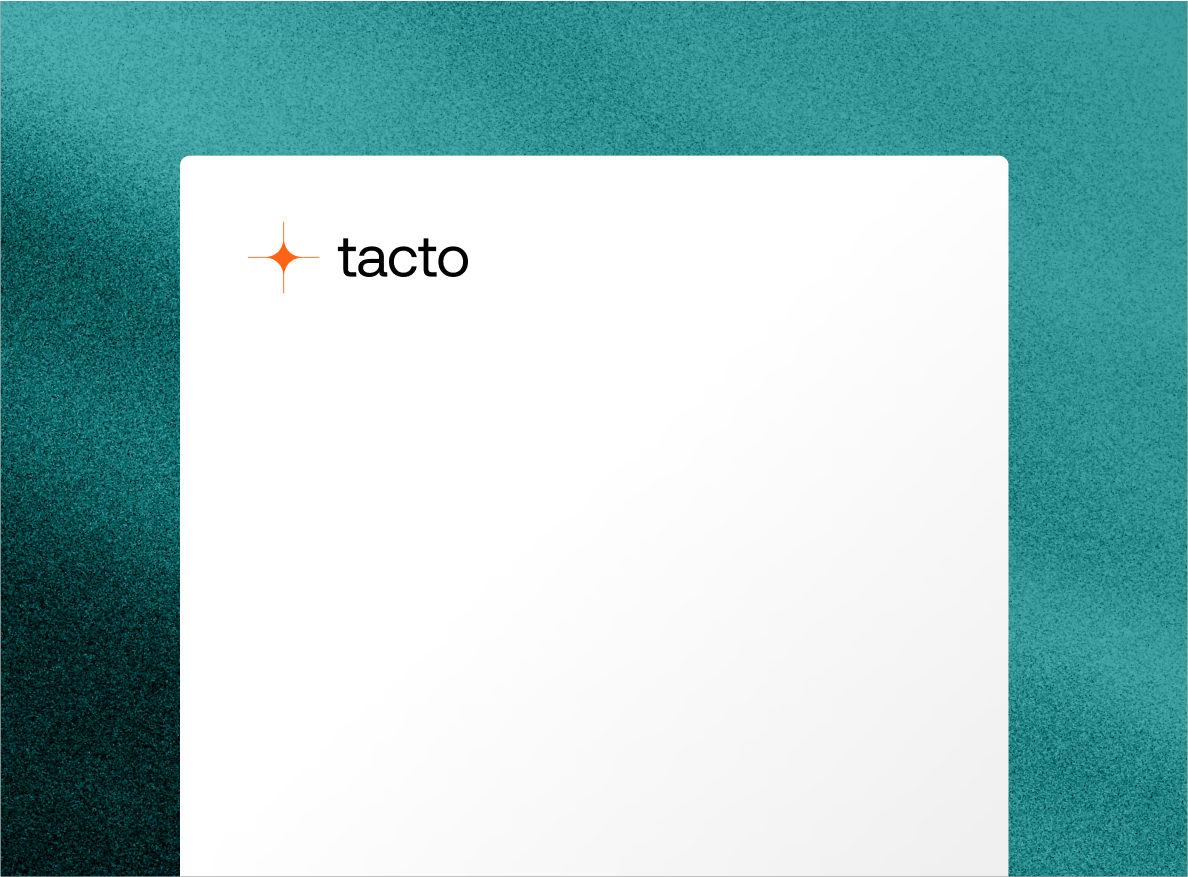