Procurement Glossary
Obsolescence management: definition & important aspects for buyers
Obsolescence management helps companies to ensure the long-term availability of components and spare parts and avoid expensive production downtime. This structured overview shows how Procurement can use systematic obsolescence management to identify supply risks at an early stage and take proactive countermeasures.
Obsolescence management in a nutshell:
Obsolescence management is the systematic planning, monitoring and control of product life cycles in order to minimize the risk of obsolescence of components and materials. This is essential for Procurement in order to avoid supply bottlenecks and develop alternative solutions or stockpiling strategies in good time.
Example: An electronics manufacturer identifies through its obsolescence management that a critical microchip will be taken off the market in 18 months and secures production for a further 5 years through a last-time buy of 50,000 units, while a redesign with alternative components is initiated in parallel.
Introduction to obsolescence management
Obsolescence management is becoming increasingly important in today's fast-moving industrial world. It deals with the systematic planning, monitoring and control of products and components that are at risk of becoming obsolete or are already considered obsolete. At a time when technological developments are progressing ever more rapidly and product life cycles are becoming ever shorter, effective obsolescence management is essential for companies. This guide provides a comprehensive overview of the principles, strategies and challenges of obsolescence management as well as practical approaches for successful implementation in companies.
What is obsolescence management?
Obsolescence management refers to the systematic planning and implementation of measures to minimize the impact of components, materials or technologies that are no longer available or obsolete in the supply chain. Essentially, the aim is to ensure the availability of required components throughout the entire product life cycle and to identify and control risk management due to discontinued components at an early stage.
Core elements of obsolescence management
Significance for Procurement
Obsolescence management is crucial in the procurement process to avoid supply bottlenecks and production downtime. Effective obsolescence management enables purchasers to reduce costs by identifying alternative sources of supply and taking timely action. It also helps to ensure product quality and compliance with customer requirements.
Obsolescence management: from a reactive to a proactive strategy
Building on the understanding of obsolescence management as a strategic approach to dealing with the obsolescence of components within the supply chain, its practical implementation is becoming increasingly important. Companies are faced with the challenge of ensuring the continuity of their production and minimizing costs at the same time. The need for a shift from traditional reactive methods to modern proactive approaches is intensified by increasing competitive pressure and the growing complexity of markets.
Old: Reactive obsolescence management
Traditional approach: In traditional practice, companies only reacted to obsolescence when problems became acute. As soon as a supplier announced the discontinuation of a product, hectic search processes for replacement parts or alternative suppliers began. This reactive approach often used manual processes and unsystematic communication channels. Tools were mostly simple spreadsheets and occasional meetings with suppliers. The main problems with this approach were unexpected production interruptions, increased procurement costs and long-term supply bottlenecks due to a lack of strategic planning.
New: Proactive obsolescence management
Obsolescence management: The modern approach integrates obsolescence management as an integral part of the corporate strategy. Advanced software and data analysis are used to continuously monitor component lifecycles. Innovation steps such as predictive analytics and artificial intelligence make it possible to detect discontinuations long before they occur. Practical benefits include a reduction in stock levels of up to 25%, improved supplier communication thanks to automated interfaces and increased planning reliability. Companies benefit from optimized procurement processes, cost savings and increased competitiveness.
Practical example: Electronics industry
A medium-sized company in the electronics industry implemented a proactive obsolescence management system. Thanks to the early identification of over 200 endangered components, alternative components could be qualified in good time. This led to a 15% reduction in procurement costs and a 90% reduction in production downtime. In addition, the time-to-market for new products improved by an average of two months, giving the company a significant competitive advantage.
Conclusion on product service life optimization
Obsolescence management is an indispensable part of modern procurement strategies. The systematic approach to early detection and management of product discontinuations not only secures the supply chain, but also minimizes financial risks. By combining proactive planning, digital solutions and strategic partnerships, companies can effectively manage obsolescence risks and secure their long-term competitiveness.
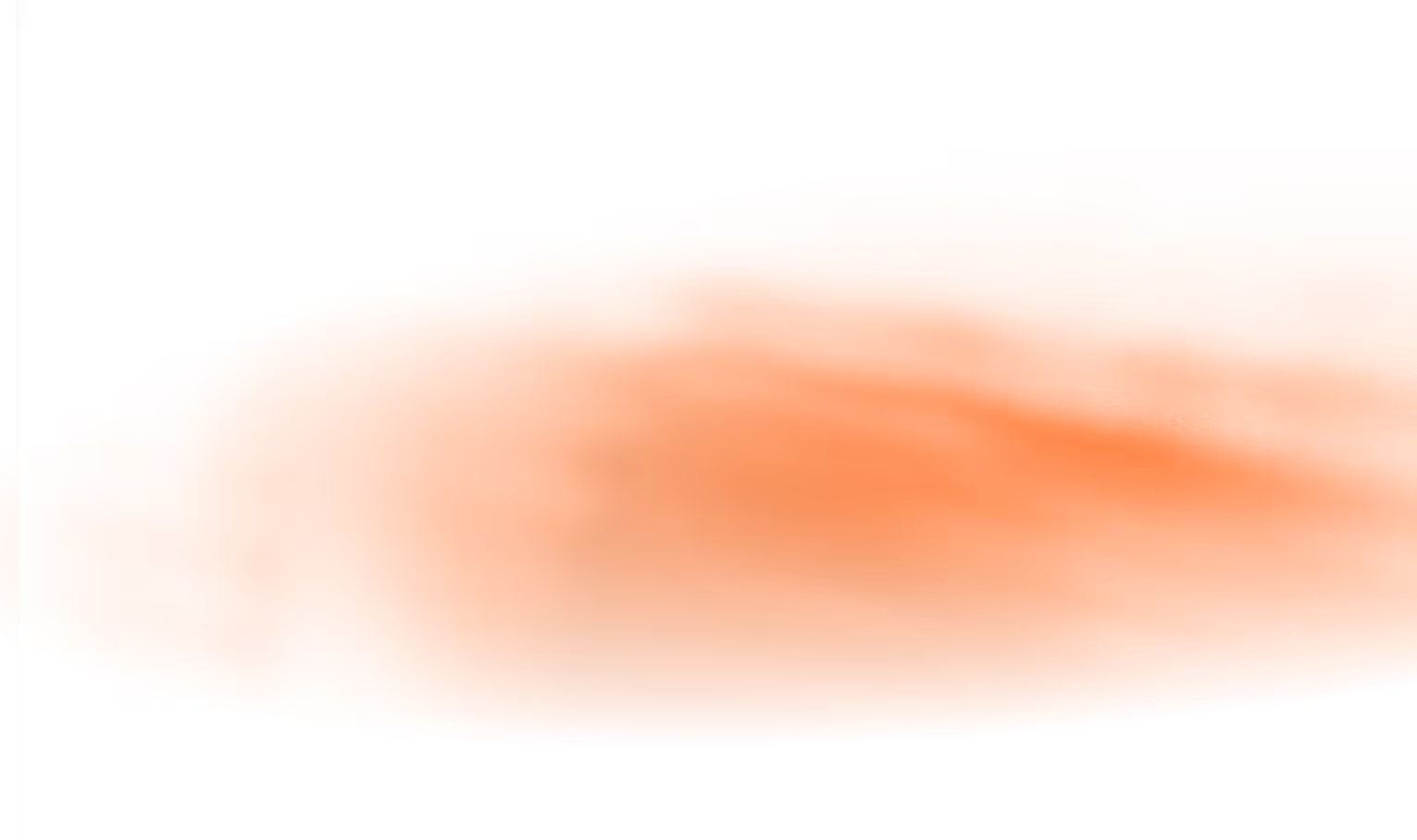
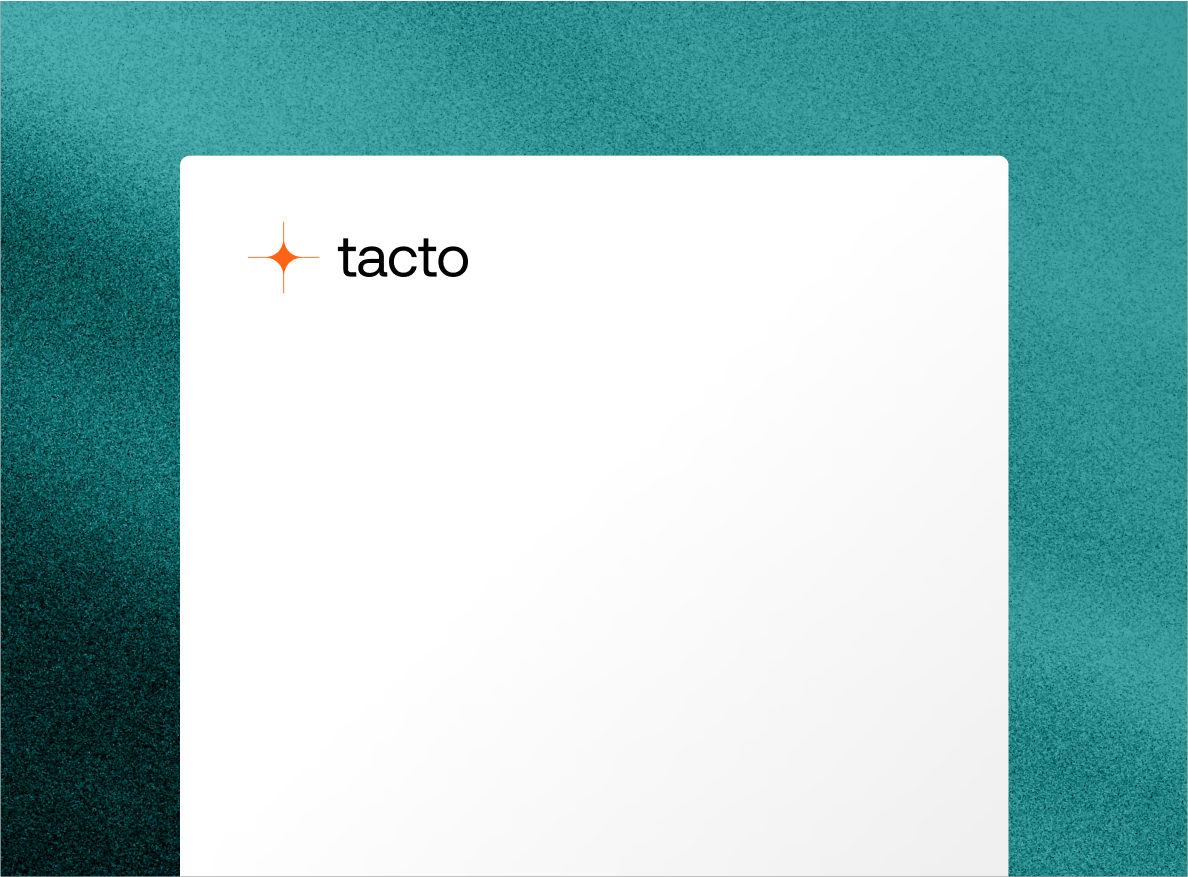