Procurement Glossary
Quality audits: Definition & important aspects for buyers
Quality audits help companies to systematically review and continuously improve their processes in order to remain competitive in the long term. This structured overview shows you how you as a buyer can use audits effectively to qualify suppliers and ensure sustainable quality in the supply chain.
Quality audits in a nutshell:
A quality audit is a systematic, independent investigation process for evaluating suppliers' quality standards, processes and systems. For Procurement , it serves as an important tool for supplier qualification and development as well as for minimizing risks in the supply chain.
Example: An automotive supplier conducts a two-day quality audit at a new electronics component supplier, in which 87 test criteria in the areas of production planning, quality control and documentation are evaluated, resulting in an audit score of 82 out of a possible 100 points.
Quality audits: An introduction
Quality audits are systematic and independent investigations that are carried out to evaluate and improve quality management systems in companies. They are an important tool for checking whether quality standards are being adhered to and whether the processes implemented are effective and efficient. In today's world, where quality is becoming increasingly important, quality audits have become an indispensable part of modern quality management. They help companies to identify weaknesses, uncover potential for improvement and sustainably increase customer satisfaction. In this guide, you will learn all the important aspects of quality audits, from the different types of audit to practical implementation and documentation.
What are quality audits?
Quality audits are systematic and independent checks that serve to evaluate compliance with quality management in Procurement and processes within a company or at suppliers. They check whether products, services and processes meet the specified requirements and identify opportunities for improvement. Regular audits ensure that quality targets are achieved and continuously improved.
Core elements of quality audits
Importance of quality audits in Procurement
In procurement, quality audits are a key tool for ensuring the quality of purchased products and services. They make it possible to evaluate the performance of suppliers, minimize risks and check compliance with legal and contractual requirements. Through effective audits, Procurement strengthens its position, increases the reliability of the supply chain and contributes to customer satisfaction.
Quality audits: From manual checklists to digital real-time assessments
Quality audits are a key tool for ensuring compliance with quality standards and promoting continuous improvement. In practice, they enable companies to systematically evaluate supplier assessments and identify risk analysis at an early stage. In view of increasing requirements and complex supply chains, there is a growing need to transform traditional audit methods and integrate more efficient, data-driven approaches.
Old: Manual checklists
Traditional approach: In the past, quality audits were mainly carried out using manual checklists. Auditors visited supplier audits on site and recorded their observations on paper forms. This process was time consuming and prone to error as the data had to be manually entered into systems later. The limited ability to analyze data made it difficult to identify patterns or proactively respond to problems. In addition, the high level of effort often led to longer intervals between audits, which increased the risk of quality deviations.
New: Digital Audit
Digital audit: Modern quality audits rely on digital technologies to increase efficiency and accuracy. By using mobile devices and specialized software, auditors can record data directly on site in real time. Functions such as photo and video recording supplement the documentation and offer a more comprehensive view of the audited processes. The immediate availability of data makes it possible to carry out automated analyses and react quickly to deviations. In addition, integration with other systems, such as ERP or quality assurance agreement platforms, facilitates the exchange of information and promotes a holistic quality strategy.
Practical example: Use in the pharmaceutical industry
A global pharmaceutical company has implemented digital quality audits to ensure supplier compliance. By introducing an audit app for tablets, auditors were able to generate reports immediately after the audit was completed. This reduced report generation time by 60%. Real-time data analysis identified critical deviations immediately, enabling corrective actions to be initiated 40% faster. Overall, this led to a 25% reduction in quality incidents in the supply chain within one year.
Conclusion on supplier evaluation
Quality audits are indispensable instruments of modern supplier management. They not only enable the systematic evaluation and development of suppliers, but also make a significant contribution to risk minimization and quality assurance throughout the entire supply chain. By integrating digital technologies and standardized processes, audits are becoming increasingly efficient and meaningful. Success lies in the consistent follow-up of results and partnership-based cooperation with suppliers.
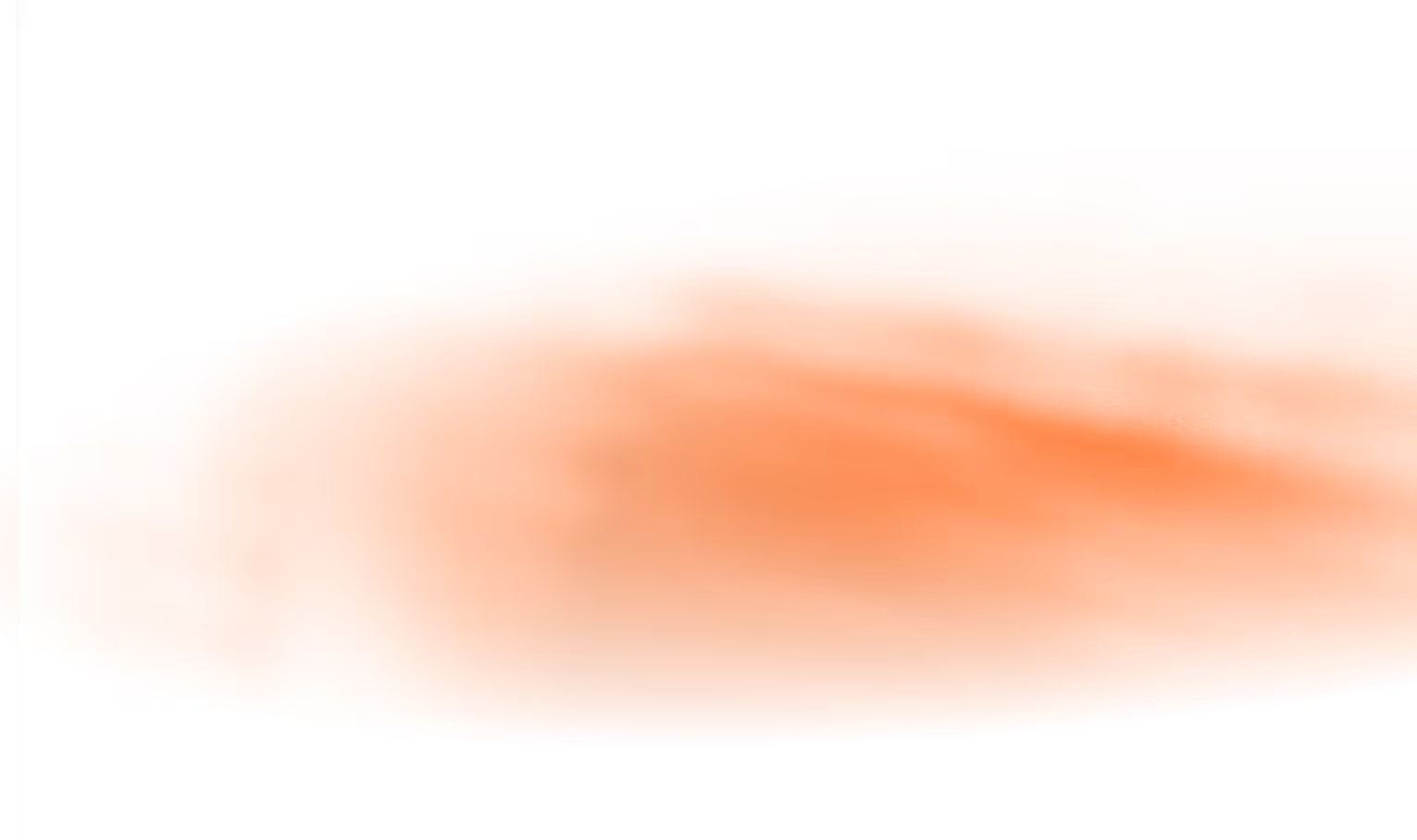
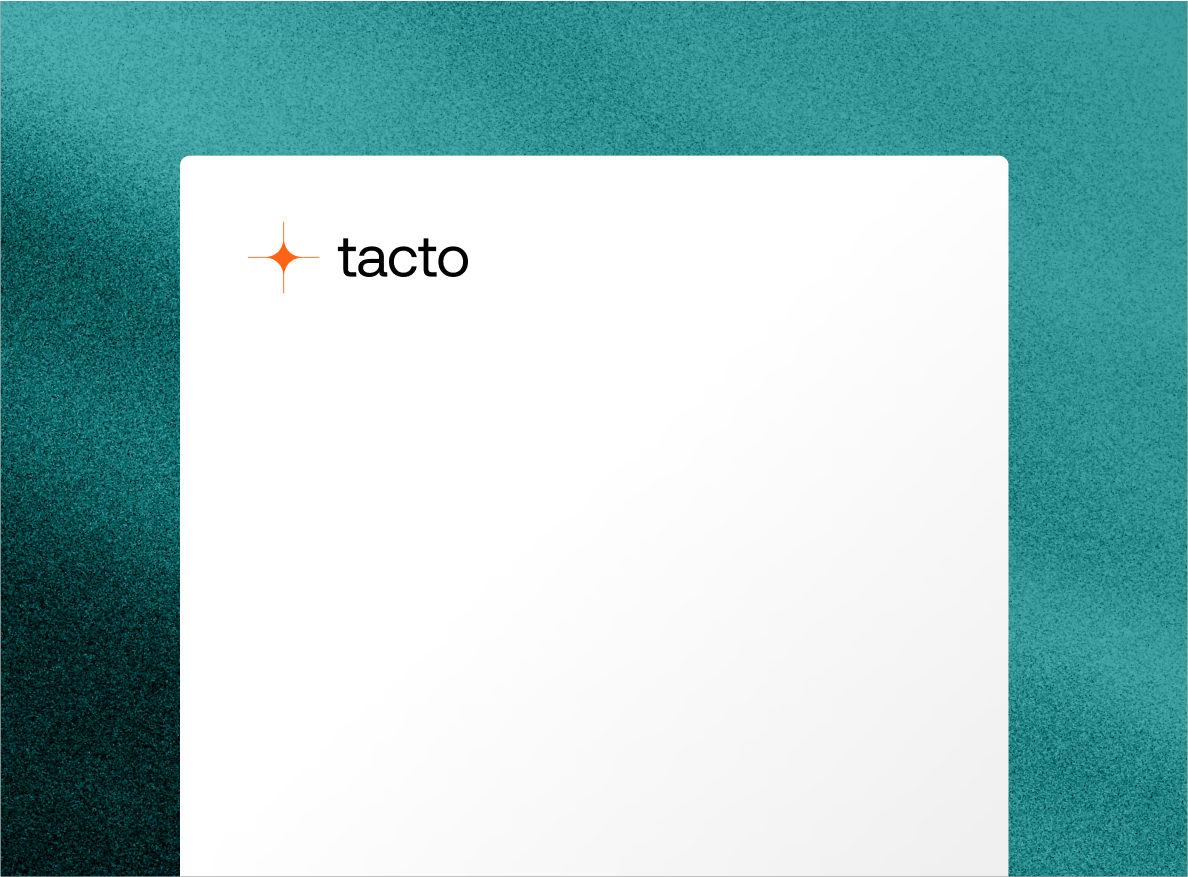