Procurement Glossary
Complaints management: definition & important aspects for buyers
Professional complaint management not only creates satisfied customers, but also offers valuable opportunities for the continuous improvement of products and processes. The following overview shows how you can systematically record complaints, process them efficiently and use the knowledge gained from them to benefit your Procurement .
Complaints management in a nutshell:
Complaints management encompasses all systematic measures for recording, processing and following up customer complaints regarding defective products or services. For Procurement , it is an essential tool for quality assurance and supplier development, which contributes to the optimization of procurement processes and the reduction of error costs.
Example: An automotive supplier implements a digital complaints system that responds to quality defects within 24 hours and uses standardized 8D reports to reduce complaint processing from an average of 14 to 5 working days, thereby reducing annual error costs by 35%.
Introduction to complaints management
Complaints management is an essential part of modern customer service and quality assurance in companies. It deals with the systematic recording, processing and evaluation of customer complaints and grievances. Professional complaints management not only offers the opportunity to restore customer satisfaction, but also serves as an important source of potential for improvement within the company. In this guide, you will learn how to set up an effective complaints management system, which processes are important and how you can use complaints as an opportunity for your company.
What is complaints management?
Complaints management refers to the systematic process for handling complaints and objections regarding goods delivered or services rendered. In Procurement , it includes all measures taken to record, analyze and rectify defects. The aim is to ensure quality management in Procurement, increase customer satisfaction and improve business relationships with suppliers in the long term.
Core elements of complaints management
Significance for Procurement
Complaints management plays a central role in Procurement in order to maintain quality standards and avoid financial losses due to faulty deliveries. Effective complaints management strengthens the company's position vis-à-vis suppliers and helps to optimize procurement processes. It also promotes the continuous improvement of supplier relationships and minimizes risk management in the supply chain.
Complaint management: from manual process to digital complaint management
Building on the theoretical basis of complaints management as an essential component for ensuring quality inspection and customer satisfaction, efficient practical implementation is of crucial importance for companies. Traditional, manual processes have often reached their limits, particularly in terms of efficiency, transparency and susceptibility to errors. In view of increasing customer requirements and a more complex supply chain, a transformation towards modern, digital approaches is essential in order to remain competitive and optimize processes sustainably.
Old: Manual complaint management
Traditional approach: In traditional complaint management, complaints were usually recorded and processed manually. This involved taking customer calls, filling out paper forms and manually entering data into simple spreadsheets. Supplier communication was by email or fax and the exchange of information was often delayed. Key features of this approach were high dependency on individual employees, lack of standardization and a lack of centralized data management. This method was prone to errors, led to redundant tasks and made it difficult to track complaints through their lifecycle. The main challenges were inefficient processes, limited transparency and limited opportunities to analyze data for continuous improvement.
New: Digital Complaint Management
Digital Complaint Management: The modern approach revolutionizes complaint management through the use of digital technologies and specialized software solutions. Complaints are recorded centrally in a digital platform that enables automated assignment to the responsible employees. Innovative functions such as real-time tracking, automated notifications and integrated communication channels significantly improve efficiency and transparency. The use of databases and analysis tools makes it possible to identify patterns in complaints and take proactive measures. In addition, this approach integrates supplier management and customers directly into the process, promotes collaboration and significantly shortens response times. Practical benefits include a reduction in processing time of up to 60%, a measurable increase in customer satisfaction and a sustainable improvement in product quality.
Practical example: Implementation in the electronics industry
A medium-sized company in the electronics industry implemented a digital complaint management system to meet the challenges of increasing complaint numbers. Before the introduction, the average processing time per complaint was around 12 days and the error rate in the documentation was 15%. After the changeover, the company saw a reduction in processing time to 4 days and a reduction in documentation errors to less than 2%. Real-time data analysis also enabled recurring quality problems to be identified and resolved together with the suppliers, resulting in a 25% reduction in the complaint rate within a year.
Conclusion on complaints management
Professional complaints management is indispensable for Procurement . It not only ensures product quality and minimizes costs, but also strengthens supplier relationships in the long term. Success lies in the systematic recording, rapid processing and consistent follow-up of complaints. With a view to digitalization, automated processes and data-driven analyses will shape complaints management in the future and make it even more efficient.
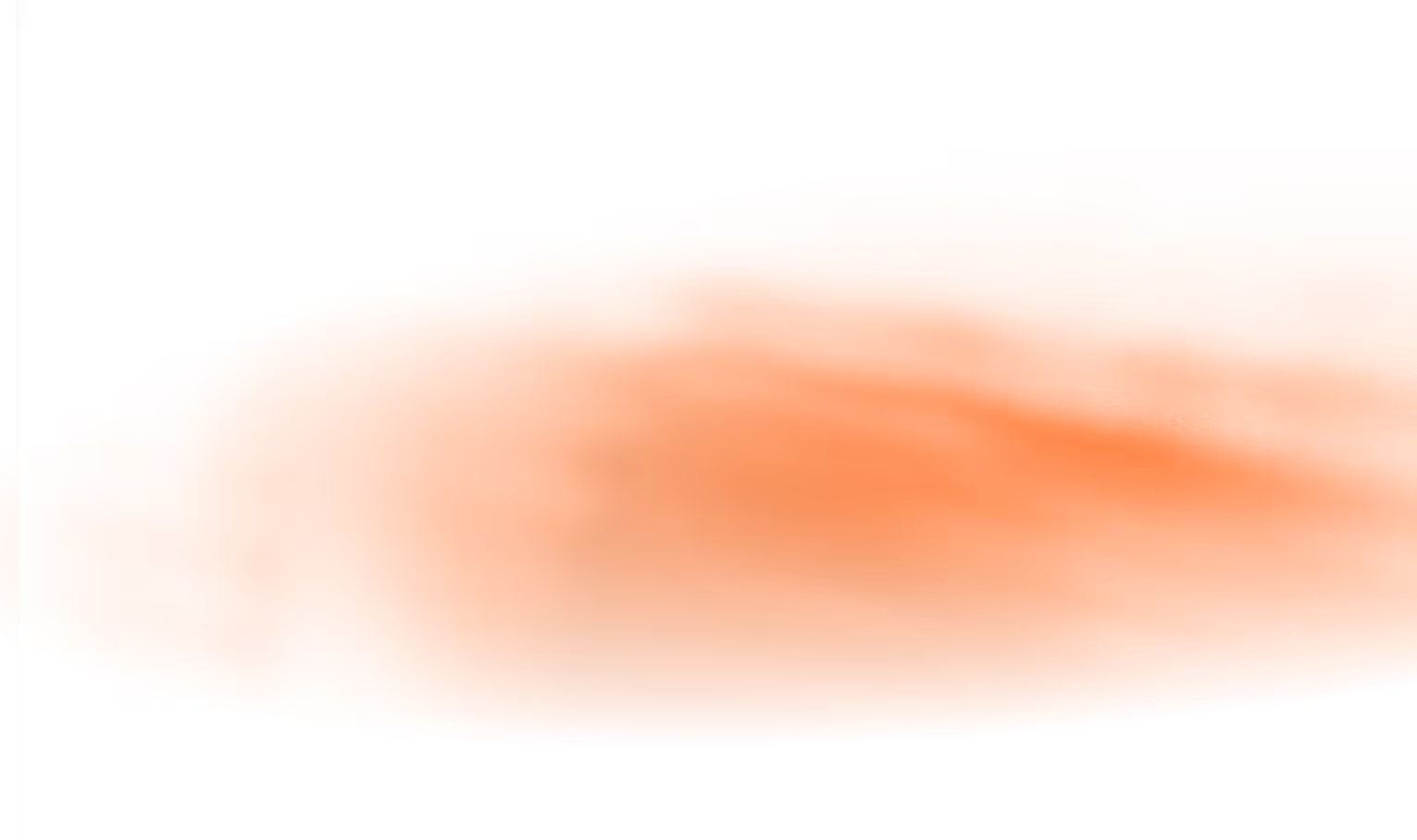
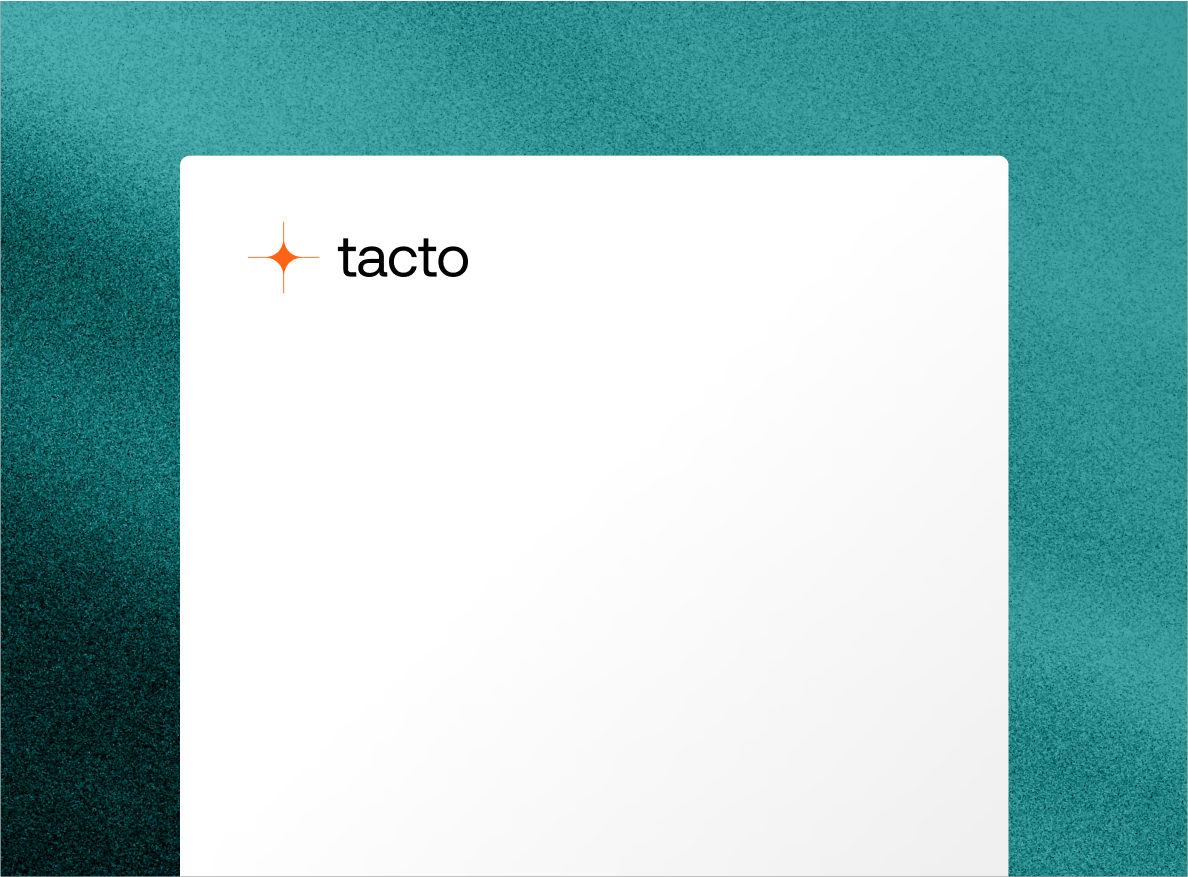