Procurement Glossary
Return delivery: definition & important aspects for buyers
Return deliveries are an important part of supplier management and have a direct impact on costs, quality and supplier relationships within the company. This structured overview shows you the most important aspects of a professional return delivery process and how you can organize it efficiently in Procurement .
Return delivery to the point:
A return delivery refers to the return of goods to the supplier due to quality defects, incorrect deliveries or excess quantities that are not required. Efficient return delivery management is essential for Procurement in order to minimize storage costs and systematically monitor supplier quality.
Example: An automotive supplier sends 200 faulty control units back to the supplier within 48 hours, documents the process in the complaints database and receives a complete replacement of the defective parts within 5 working days.
Returns - Efficient management
Return delivery is an important process in goods and business transactions that is of great importance to both companies and consumers. It describes the process by which goods that have already been delivered are returned to the sender for various reasons. In times of growing online trade, the issue of returns is becoming increasingly important and presents companies with logistical and economic challenges. This guide provides a comprehensive overview of the various aspects of return deliveries, from the legal basis to efficient handling processes and sustainable solutions.
What is a return delivery?
In the procurement process, a return delivery refers to the return of goods or materials from the buyer to the supplier. This occurs when delivered products have defects, do not meet the agreed specifications or were delivered incorrectly. The return delivery is an essential part of complaints management and serves to ensure quality assurance and customer satisfaction.
Core elements of the return delivery
Importance of return deliveries in Procurement
In Procurement , the efficient handling of returns plays a decisive role in ensuring product quality and optimizing processes. Effective returns management enables companies to reduce costs, strengthen supplier relationships and increase the satisfaction of internal stakeholders.
Return delivery: from manual processing to automated return management
The return delivery is a decisive process in Procurementwhich ensures that faulty or unneeded goods are efficiently returned to the supplier. Building on the theoretical importance of these processes, in practice it is essential to handle returns smoothly and transparently. With increasing demands for speed and accuracy, the need for a transformation from traditional to modern approaches is becoming ever clearer.
Old: Manual return delivery processes
Traditional approach: In traditional returns processes, returns are recorded and processed manually. Employees fill out return forms by hand, communicate with suppliers by phone or email and document processes in physical files or simple spreadsheets. This approach is time-consuming and error-prone, as human input errors can occur and tracking the returns process is difficult. There is also a lack of real-time information, which leads to delays and increased costs.
New: Automated Return Management
Automated Return Management: Modern return processes rely on digital technologies and automation. By integrating ERP systems and special returns management software solutions, returns are automatically recorded and processed. Barcodes and RFID tags enable fast identification of goods, while electronic data transmission ensures seamless communication with the supplier. Key innovations include real-time tracking, automatic notifications and the use of AI to forecast returns. These improvements lead to shorter processing times, fewer errors and reduced costs.
Practical example: Implementation at an electronics manufacturer
A leading electronics manufacturer implemented an Automated Return Management System in its purchasing process. Within the first year, the company was able to reduce the processing time for returns by 70%. The error rate when recording returns fell by 85% and transparency in the process was significantly increased. Automated communication with suppliers also reduced storage costs by 15%, as returns were processed more quickly and replacement deliveries were expedited.
Conclusion on the return delivery
Efficient returns management is essential for companies to ensure quality standards and optimize costs. Success is based on clear processes, digital documentation and close cooperation with suppliers. By integrating modern technologies and preventative measures, returns management is increasingly evolving from a reactive to a strategic tool in Procurement.
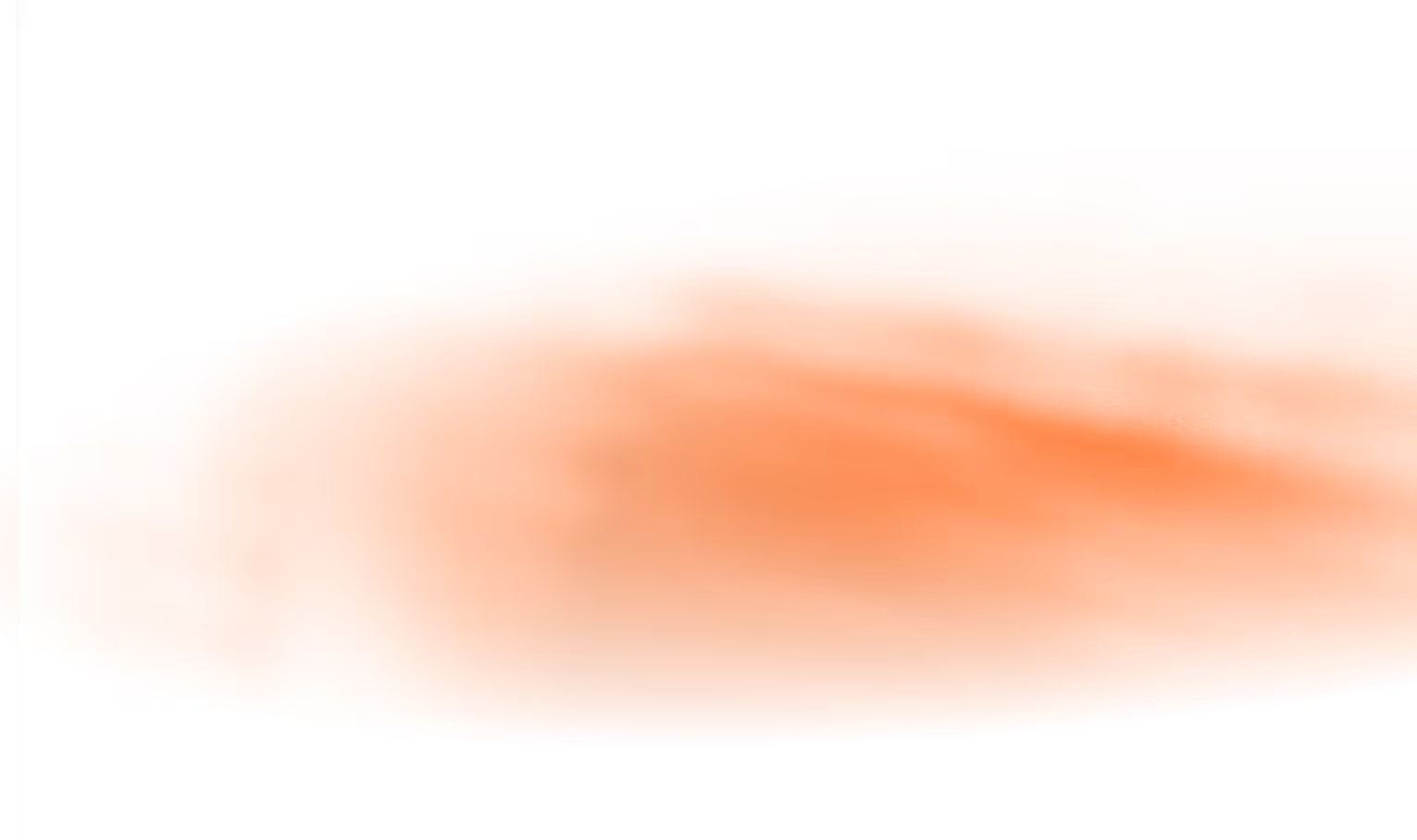
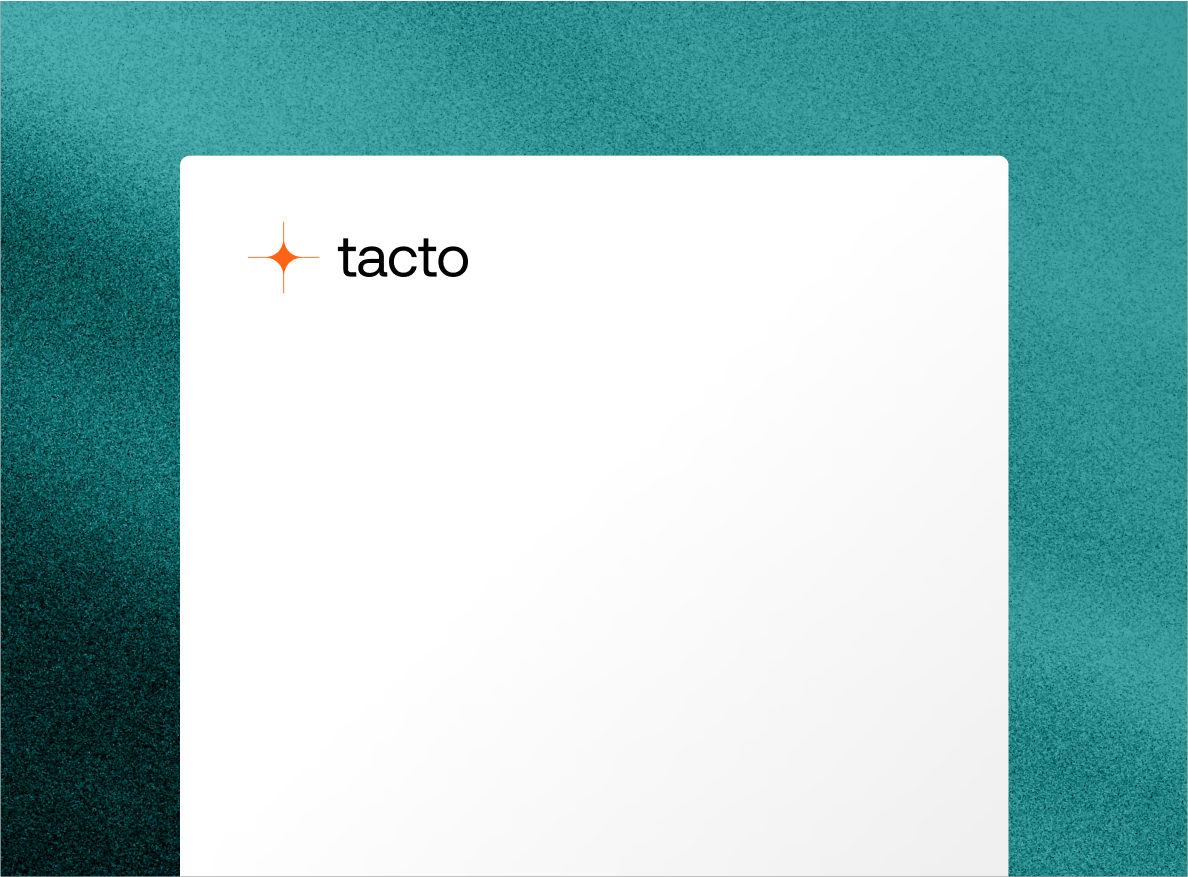