Procurement Glossary
Synergy effects: Definition & important aspects for buyers
Synergy effects create measurable added value for companies through the skillful combination of resources and expertise. This structured overview shows how Procurement realizes cost savings and generates competitive advantages through the systematic use of synergies.
Synergy effects in a nutshell:
Synergy effects describe the positive interaction of various factors, whereby the overall benefit is greater than the sum of the individual benefits. In Procurement , they enable considerable cost savings and efficiency gains by bundling procurement activities, harmonizing processes and pooling requirements.
Example: Following the merger of two companies, the previously separate purchasing volumes for packaging materials of EUR 2 million each are combined, resulting in total savings of EUR 600,000 (15%) in the first year thanks to the strengthened negotiating position and optimized logistics.
Synergy effects in purchasing controlling
Synergy effects are a fascinating phenomenon in the business world and describe the interaction of various factors which, when combined, generate a greater overall benefit than the sum of their individual effects. The term originally comes from the Greek "synergos" (working together) and has developed into a key concept in modern corporate management. Especially in times of mergers, takeovers and strategic alliances, synergy effects play a central role in business decisions. In this introduction, we will take a closer look at the different types of synergy effects, their significance for corporate success and the challenges involved in realizing them.
What are synergy effects?
Synergy effects refer to the additional benefits that arise when two or more companies, departments or processes work together to achieve better results than they could on their own. In the context of purchasing strategy, this means that efficiency increases and cost savings are achieved by pooling resources, knowledge or purchasing volumes. The principle is based on the idea that the whole is greater than the sum of its parts.
Core elements of synergy effects
Importance of synergy effects in Procurement
Synergy effects are particularly important in Procurement in order to achieve competitive advantages and make optimum use of resources. By working together with other departments or companies, buyers can negotiate better conditions, minimize risk management and increase the degree of innovation. Synergies help to strengthen procurement strategies and build long-term partnerships with suppliers.
Synergy effects: From isolated to integrated processes
Synergy effects are indispensable in the modern corporate world in order to achieve competitive advantages and use resources efficiently. Although theory emphasizes the potential of joint efforts, companies have long faced the challenge of putting this into practice. Traditional structures with separate departments often prevented optimal cooperation. However, the increasing complexity of markets requires a transformation towards integrated approaches in order to develop the full effect of synergies.
Old: Fragmented cooperation
Traditional approach: In traditional companies, departments such as the purchasing organization, production and sales often act as independent silos. Each unit pursues its own goals and processes without considering the impact on other areas. This fragmented collaboration leads to inefficiencies, duplication of effort and missed opportunities for cost savings. Typical tools are isolated systems and manual communication channels that make it difficult to share information. The main problems are a lack of transparency, slow decision-making and a low capacity for innovation.
New: Collaborative sourcing
Collaborative sourcing: The modern approach relies on close, cross-departmental collaboration and the integration of supplier management. By using digital platforms, information is shared in real time and joint projects are made possible. Key innovations include cloud-based systems, the integration of supplier data and AI-supported analyses. This leads to improved processes, faster market launches and sustainable procurement costs of up to 15%, shorter development cycles and increased innovation potential.
Practical example: Automotive industry
An international automotive manufacturer implemented collaborative sourcing by combining its purchasing, development and quality departments and strategic partnership on a common platform. The integrative collaboration reduced material costs by 10% and product development time by 20%. The exchange of knowledge also led to innovative technologies that increased market share by 5% and improved customer satisfaction.
Conclusion on synergy effects
Synergy effects in Procurement offer considerable opportunities to save costs and increase efficiency. Successful implementation requires a strategic approach, standardized processes and the active involvement of all stakeholders. Despite initial challenges during implementation, the long-term benefits of improved negotiating positions, optimized use of resources and increased innovative strength outweigh the costs. As digitalization progresses, additional opportunities for synergies will open up, further strengthening strategic Procurement .
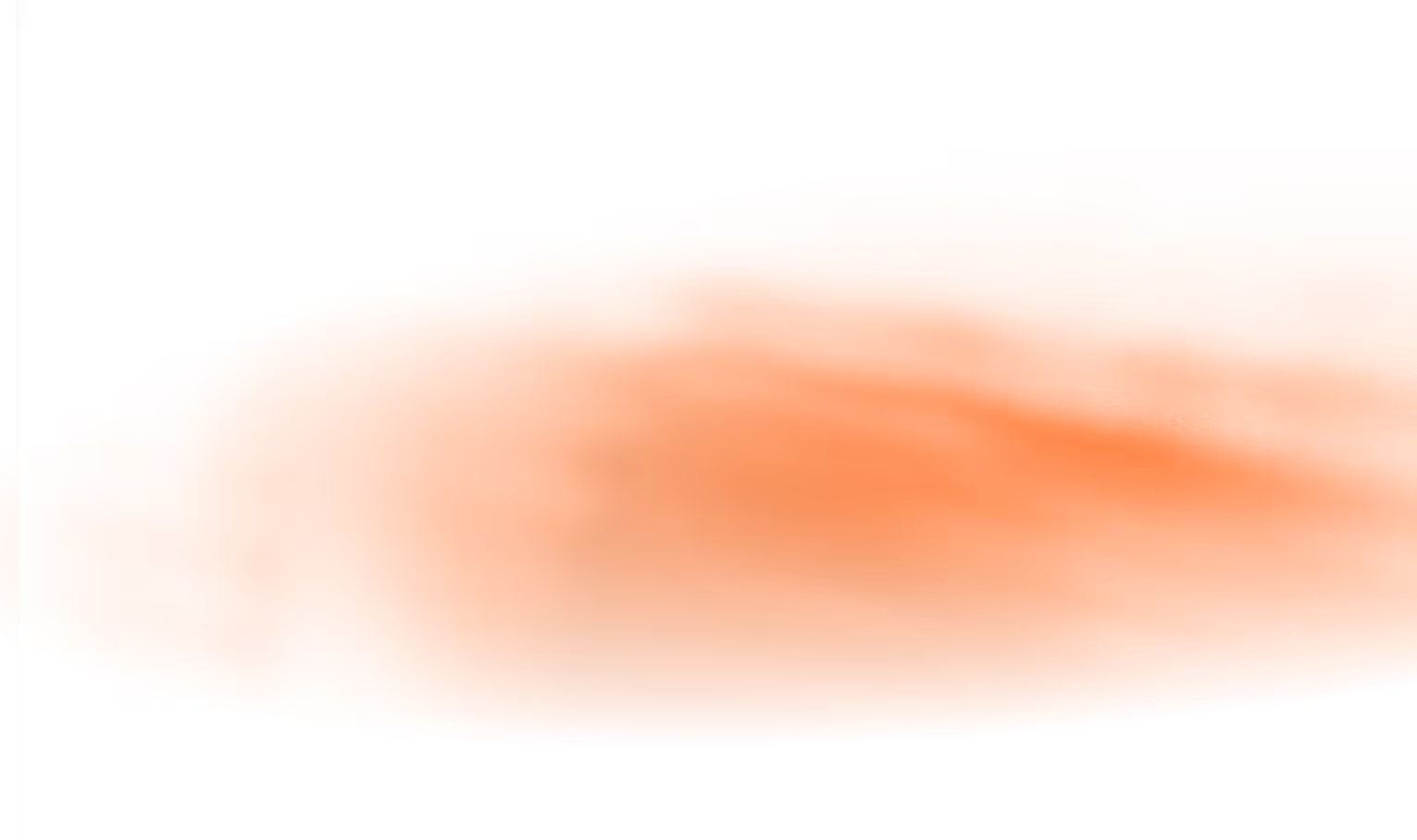
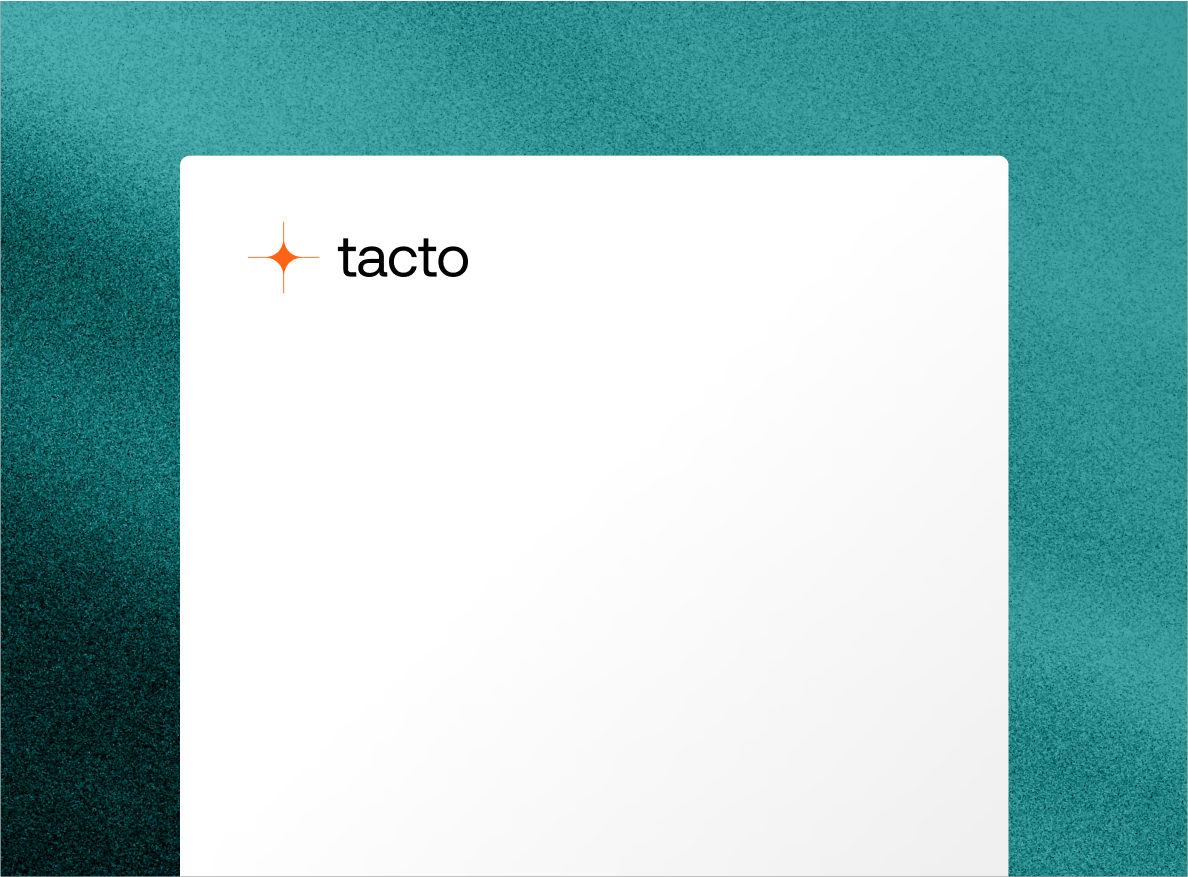