Procurement Glossary
System supplier: Definition & the meaning of Original Equipment Manufacturer
System suppliers develop and produce complete systems for original equipment manufacturers. The outsourcing of development, production and know-how by OEMs to system suppliers enables significant cost savings and supports competitiveness. Although there are disadvantages due to dependencies, the success of OEMs is largely based on long-term, partnership-based relationships and clear contractual framework conditions. For future-oriented companies, the integration of system suppliers is increasingly becoming a decisive competitive factor.
System supplier: The supplier of complex assemblies or systems to OEMs
A system supplier (Tier 1 supplier) produces and delivers not only individual products or components, but also complete systems or assemblies to original equipment manufacturers (OEMs). A system supplier sources its required materials and parts from Tier 2 suppliers and uses them to produce a complete component, e.g. a system supplier delivers a complete transmission or seating system to a car manufacturer (the OEM, in this example). These components are more complex than the parts from Tier 2 or Tier 3 suppliers, which places high demands on quality, integration and innovation.
Introduction to the purchasing controlling of system suppliers
System supplier number 2 among OEMs in the supplier pyramid:
Original equipment manufacturers (OEMs) are often in price competition with competitors, which causes great cost pressure in production. In order to reduce costs in Procurement and production, there is an increasing focus on system suppliers who can cover the development, manufacture and delivery of all production steps. System suppliers deliver complete systems to OEMs, which is associated with greater complexity and higher demands on quality, integration and innovation.
System suppliers are therefore in second place behind OEMs in the supplier pyramid, which symbolically represents the supply chain. They are followed by the suppliers of individual components and finally the suppliers of individual parts. This representation does not exclude the possibility that OEMs or system suppliers do not use Tier 3 suppliers. This representation, as well as the significant role of system suppliers, can be found particularly in the automotive industry. System suppliers take on a lot of development work in the automotive industry, thereby contributing to cost reductions and competitiveness.
High demands on a system supplier:
While cost advantages are particularly important for OEMs, they also enter into a relationship of dependency with the system supplier. There is not only a dependency on timely deliveries, but also on quality, innovation and external know-how. This is reinforced in particular by the strong integration of the system supplier's product with the OEM device and the associated set-up costs.
Requirements for system suppliers:
- Flexibility: System suppliers must be able to react quickly and flexibly to changes in the OEM's production.
- Quality: High quality is essential for the OEM to ensure a high quality product.
- Reliability: A system supplier must not only be reliable in terms of quality, but also in terms of time and quantity, so that the OEM's production time does not deteriorate.
- Innovation: To ensure that the OEM's product remains innovative and moves with the times, the system supplier must also continue to develop its parts.
- Digitization: System suppliers must adapt to trends by digitizing and automating their production and delivery in order to work optimally with OEMs.
Advantages of system suppliers over partial suppliers:
- Cost benefits: Outsourcing manufacturing expertise enables cost savings for OEMs.
- Risk minimization: system suppliers can reduce supplier and quality risks
- Relief: Core areas of the OEM's production are relieved.
- Flexibility: The OEM can flexibly request new components or spare parts.
- Development: Separate development and competencies can reduce time-to-market for new products.
Significance for Procurement
For the strategic partnership, the system supplier plays a decisive role in the optimization of procurement processes. By bundling services with one provider, costs can be reduced and efficiencies increased. Procurement also benefits from the expertise of the system supplier, which leads to higher product quality and innovative strength. Long-term partnerships enable better planning and reduce risk management in the supply chain.
At the same time, Procurement , together with Production, must weigh up the advantages against the disadvantages of dependency. As an OEM, you are dependent on the quality, reliability, innovation and external expertise of the system supplier.
System supplier: From parts supplier to system partner
The transition from traditional parts supplier to modern system supplier marks a decisive change in the procurement strategies of many companies. Based on the theoretical foundation of the system supplier, the latter not only supplies individual components, but also offers complete systems and solutions. This is of great importance in practice, as it reduces complexity in the supply chain and leads to more efficient processes. The need for this transformation arises from increasing competitive pressure and the demand for faster innovation cycles.
Traditional approach: parts supplier
In traditional procurement, companies worked with a large number of parts suppliers who were each responsible for supplying specific components. This approach required a great deal of coordination on the part of the purchasing department, as each part had to be ordered, checked and stored individually. In addition, the manufacturer was responsible for integrating the parts into the end product. The main tools were classic ordering systems and extensive quality checks for each delivery. The challenge was to harmonize delivery dates, manage quality fluctuations and avoid high stock levels.
New: System supplier
The modern approach relies on cooperation with system suppliers who deliver complete assemblies or systems. In addition to production, they also take on development tasks and integrate various components into a functional unit. Leaps in innovation such as the digitalization of the supply chain, just-in-time deliveries and closely interlinked development processes characterize this approach. Practical advantages include a reduced number of suppliers, less coordination effort and accelerated development cycles. By shifting responsibilities to the system supplier, companies can act more flexibly and focus on their core competencies.
Practical example: Automotive industry
In 2023, a leading European car manufacturer started the strategic changeover from individual parts to system suppliers for its cockpit production, which comprises 800,000 units per year. Previously, 24 different components were sourced from 18 tier-2 and tier-3 suppliers, which caused a considerable coordination effort with annual costs of 2.8 million euros for supplier management.
The switch to two system suppliers had an immediate effect: coordination costs fell by 75% to 700,000 euros per year, as the system suppliers took over the integration and quality assurance of the individual components. The assembly time per cockpit was reduced from 95 to 48 minutes because pre-tested systems were now installed instead of individual parts. With 800,000 units, this meant a saving of 627,000 working hours in assembly.
The early involvement of system suppliers in the development process proved to be particularly valuable: the time from the initial concept phase to series production of a new cockpit design was reduced from 36 to 24 months. The number of change loops in development fell by 60%, as the system suppliers contributed their expertise as early as the concept phase. Just-in-sequence delivery reduced inventories by 85%, which enabled cost savings of 4.2 million euros per year.
The system suppliers also benefited significantly: their turnover per cockpit rose by 140%, while their profit margin increased from 6% to 9% thanks to economies of scale and optimized processes. The longer-term development partnerships enabled higher investments in innovation and automation. The former Tier 2 and Tier 3 suppliers were partially integrated into the new system as sub-suppliers, with the system suppliers taking over quality and logistics management, which significantly improved the overall efficiency of the supply chain.
Conclusion: Strategic advantages through system suppliers
Cooperation with system suppliers offers companies considerable advantages through reduced complexity, optimized processes and increased efficiency. Despite possible dependency risks, the strategic benefits such as cost savings, quality improvements and innovation potential outweigh the risks. Success is largely based on a long-term, partnership-based relationship and clear contractual framework conditions. For forward-looking companies, the integration of system suppliers is increasingly becoming a decisive competitive factor.
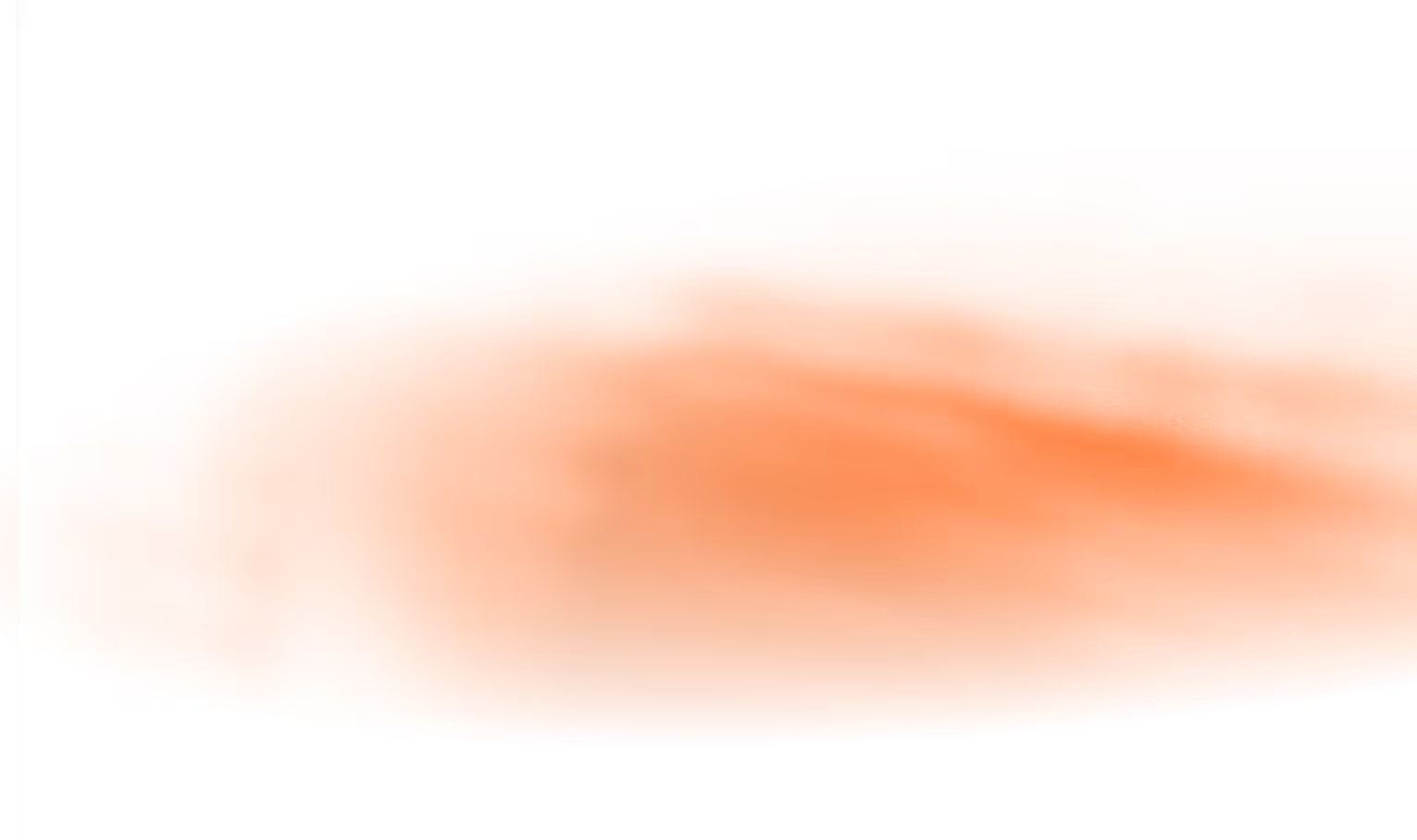
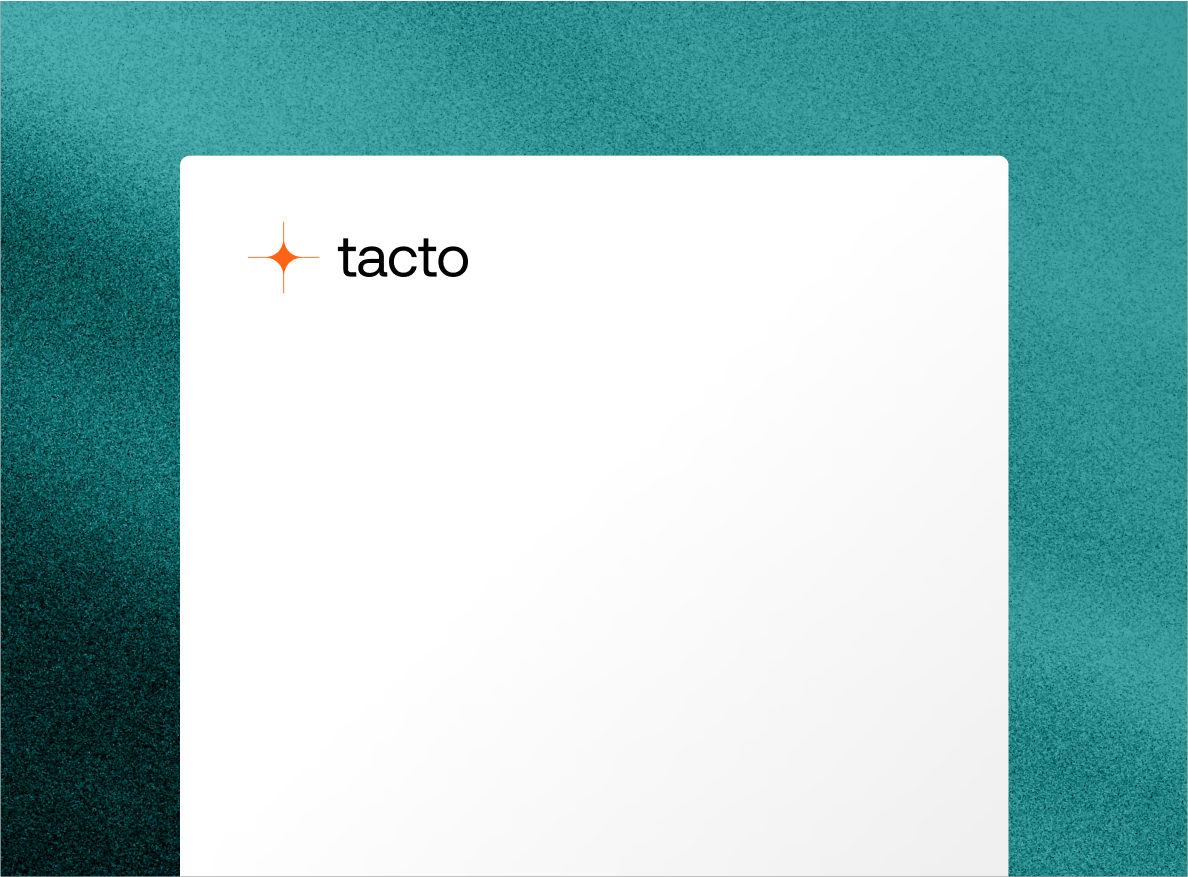