Procurement Glossary
Value analysis: definition & important aspects for buyers
Value analysis enables companies to systematically optimize products and processes while reducing costs and increasing quality. This structured overview shows you how you can use value analysis in Procurement to achieve sustainable competitive advantages.
Value analysis in a nutshell:
Value analysis is a systematic method for optimizing the relationship between product function and costs through structured analysis of all components and processes. In Procurement , it enables the targeted identification of potential savings while maintaining or improving the required functionality.
Example: An automotive supplier reduced the production costs of a control unit by 22% (from €85 to €66 per unit) through a 6-week value analysis by reducing the number of components from 47 to 32 without compromising technical performance.
Value analysis: An introduction
Value analysis is a systematic method for optimizing products, services and processes that was developed at General Electric in the 1940s. It aims to analyze the functions of a product or service and increase its value while simultaneously reducing costs. Value analysis not only considers the pure material costs, but also all other cost factors such as development, production and maintenance. In this guide, we will take a closer look at the basic concepts of value analysis, its areas of application and the practical implementation and associated benefits for companies.
What is value analysis?
Value analysis is a systematic method for reducing costs and improving the functionality of products, processes or services. It aims to identify and eliminate unnecessary costs without compromising essential functions. Through a detailed examination of all components, opportunities are identified to increase value for the customer while simultaneously increasing efficiency.
Core elements of value analysis
Importance of value analysis in Procurement
In procurement, value analysis makes a significant contribution to optimizing the supply chain. It enables buyers to evaluate products and services in terms of their actual added value and identify cost-efficient alternatives. Through supplier development, processes can be improved, materials optimized and innovative solutions found, leading to significant cost savings and quality improvements.
Value analysis: From traditional cost reduction to value engineering
Value analysis has established itself as an indispensable tool for increasing the value of products and processes through functional consideration and cost optimization. In practice, however, traditional methods of cost reduction are increasingly reaching their limits, as they often only enable superficial savings. In view of increasing market requirements and increasingly complex products, there is a need for a more comprehensive approach that takes both costs and functions into account holistically.
Old: Traditional cost reduction
Traditional approach: In traditional value analysis, the focus was primarily on the direct reduction of production costs. This was often achieved by replacing materials with cheaper alternatives or by outsourcing production steps. Companies used simple calculations and relied on tried and tested processes to achieve quick cost savings. However, this approach often led to compromises in product quality and ignored potential innovation opportunities. In addition, long-term costs, such as increased failure rates or reduced customer satisfaction, were not sufficiently taken into account.
New: Value Engineering
Value engineering: The modern value engineering approach extends traditional value analysis by taking a systematic and functional view of the entire product life cycle. Interdisciplinary teams are used to develop creative solutions that both reduce costs and improve functionality and quality assurance agreements. By using advanced tools such as CAD systems, simulation software and value-analytical databases, various design options can be evaluated. Innovations such as modular construction methods or the use of new materials make it possible to design products more effectively and efficiently. This leads to more sustainable products, higher margins and increased customer satisfaction.
Practical example: Value analysis in the electronics industry
A leading manufacturer of smartphones was faced with the task of reducing the production costs of its latest model by 10% in order to remain competitive. By applying value engineering, all components were checked for their functional contribution. The team identified redundant components in the hardware that could be replaced by multifunctional chips. The redesign of the circuit board resulted in material savings of 15%. In addition, the assembly time was reduced by 20 % thanks to optimized production control. Overall, the company was able to reduce costs by 12% without compromising the performance of the smartphone and recorded an 8% increase in customer satisfaction thanks to improved product quality.
Conclusion on value analysis
Value analysis is an indispensable tool in modern Procurement that systematically reduces costs and increases product value at the same time. Through the methodical combination of functional analysis, cost optimization and innovation promotion, it enables sustainable improvements along the entire value chain. Despite initial resource expenditure, consistent application pays off through significant cost savings and quality improvements. In view of the digital transformation and increasing sustainability requirements, the importance of value analysis will continue to grow.
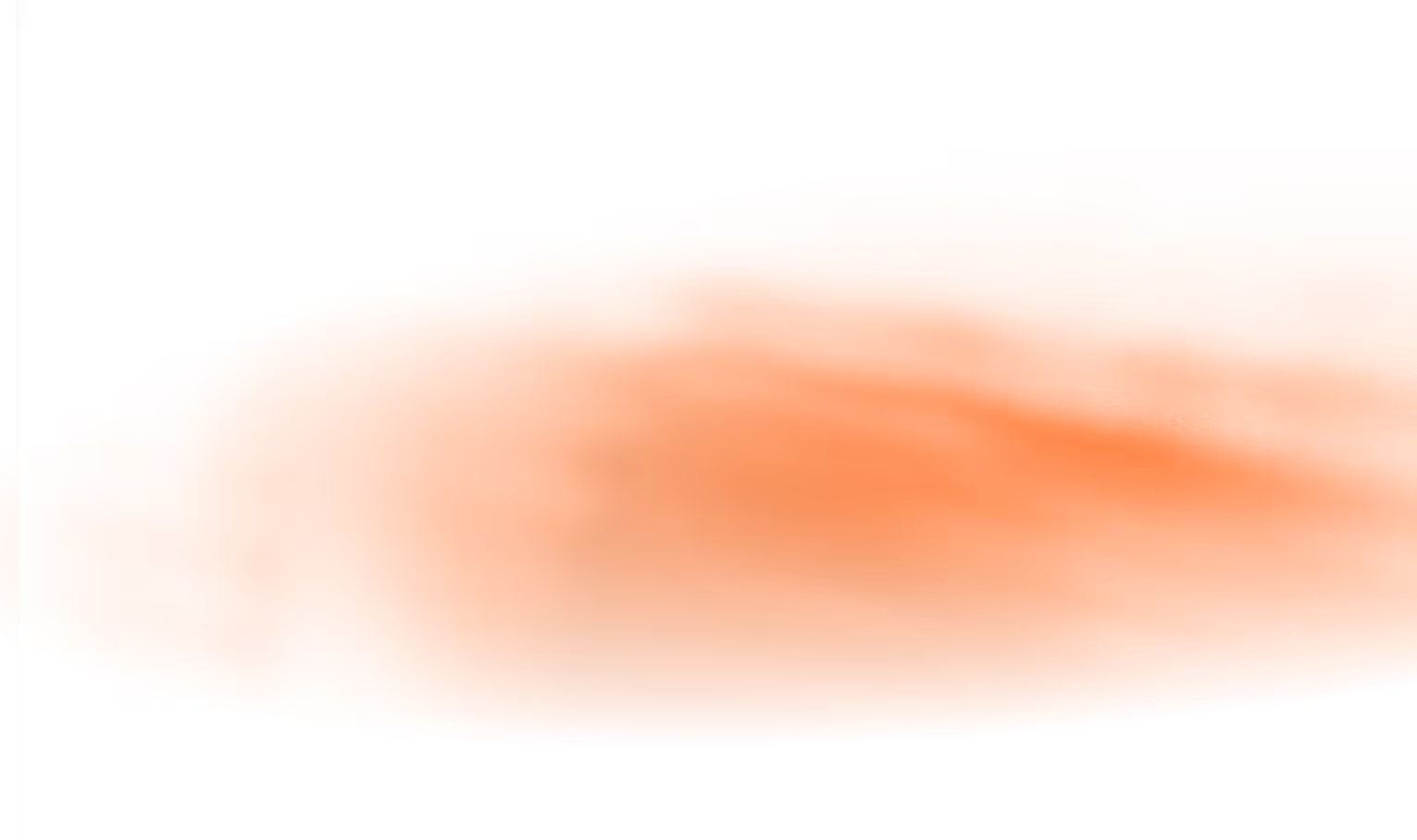
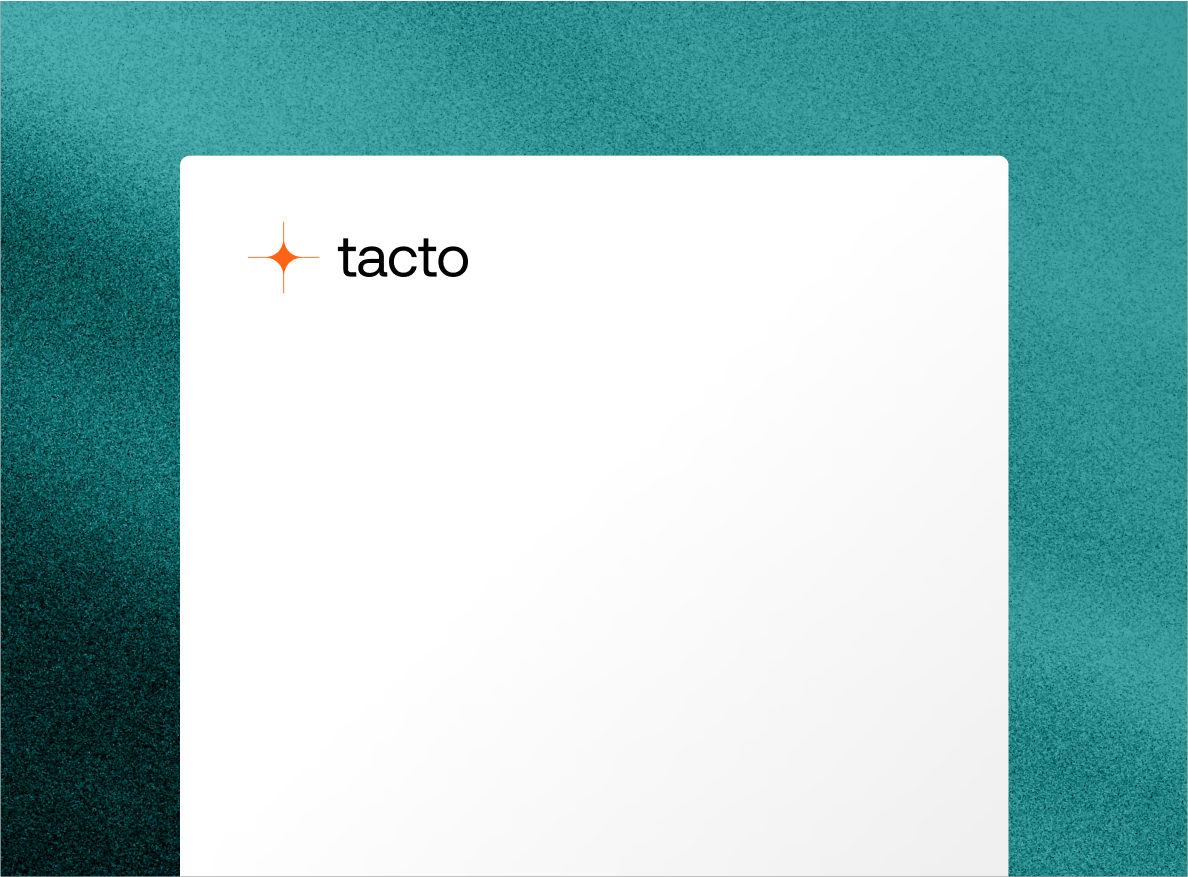