Procurement Glossary
Production control: definition & important aspects for buyers
Production control is at the heart of an efficient production process and enables companies to make optimum use of their resources and minimize throughput times. This structured overview shows how Procurement can optimize delivery times and sustainably reduce costs through clever production control.
Production control in a nutshell:
Production control is the operational planning, coordination and monitoring of all manufacturing processes to ensure that products are manufactured on time. It is essential for Procurement , as it forms the basis for needs-based material procurement and optimal warehousing.
Example: An automotive supplier uses production control to plan the production of 10,000 brake components over 4 weeks, whereby Procurement calls off the required 30,000 individual parts in three deliveries of 10,000 pieces each every 8 days, staggered according to the production plan.
Introduction to production control
Production control is a fundamental component of modern production management and plays a central role in the successful management of manufacturing companies. It encompasses all activities and measures for the operational planning, implementation and monitoring of the production process. The aim is to ensure optimum utilization of production capacities, minimize throughput times and at the same time maintain the highest quality standards. This introduction highlights the most important aspects of production control, from the basic concepts to modern methods and digital solutions of Industry 4.0.
What is production control?
Production control is a central process in manufacturing that includes the planning, monitoring and control of all production processes. It ensures that resources are used efficiently, production plans are adhered to and goods are manufactured on time and to the required quality. All steps from procurement logistics to production and delivery are coordinated.
Core elements of production control
Significance for Procurement
Production control plays a crucial role for Procurement , as it has a direct influence on material requirements and procurement times. Efficient production control enables Procurement to create demand forecasts, coordinate just-in-time deliveries and minimize stock levels. This leads to cost savings, improved supplier relationships and greater flexibility in the supply chain.
Production control: From manual planning to advanced planning and scheduling
Production control is at the heart of efficient production management. In an increasingly dynamic market environment, companies are faced with the challenge of reacting more quickly to customer requirements and reducing costs at the same time. Traditional methods are reaching their limits here, which is why a shift towards digitalized and integrated control systems is necessary to secure competitive advantages.
Old: Manual production control
Traditional approach: In manual production control, planning and control processes are mainly based on static data and empirical values. Order processing is often controlled manually using planning boards or simple software. Information is kept in silos and communication between departments is linear and time-delayed. Difficulties in adapting to short-term changes and limited transparency about the current production status lead to inefficiencies and increased costs. In addition, fluctuations in demand cannot be taken into account quickly enough, leading to overstocking or delivery delays.
New: Advanced Planning and Scheduling (APS)
Advanced Planning and Scheduling (APS): Modern production control systems use APS solutions that offer advanced functions for real-time planning and control. By integrating data from ERP systems, machines and sensors, APS enables a holistic view of the production process. Intelligent algorithms optimize the sequence of orders, taking into account resource availability and delivery deadlines. This leads to greater flexibility and efficiency. Bottlenecks can be proactively identified and rescheduling can be carried out automatically. The continuous demand analysis also allows a precise forecast of future production requirements.
Practical example: Introduction of APS at a mechanical engineering company
A medium-sized mechanical engineering company implemented an APS system to modernize its production processes. Within the first year, on-time delivery was increased from 85% to 98%. Throughput times were reduced by 30% as bottlenecks were identified and eliminated at an early stage. Thanks to the improved capacity planning the stock of semi-finished products fell by 25%, which led to considerable cost savings. Transparency across the entire production process also enabled better customer communication and significantly increased customer satisfaction.
Conclusion on production control
Production control is a fundamental success factor for modern companies. It not only efficiently connects production and Procurement , but also optimizes the entire value creation process. By using modern technologies such as AI and IoT as well as the integration of real-time data, companies can significantly increase their competitiveness. The key to success lies in the continuous development of processes and close collaboration between all departments involved.
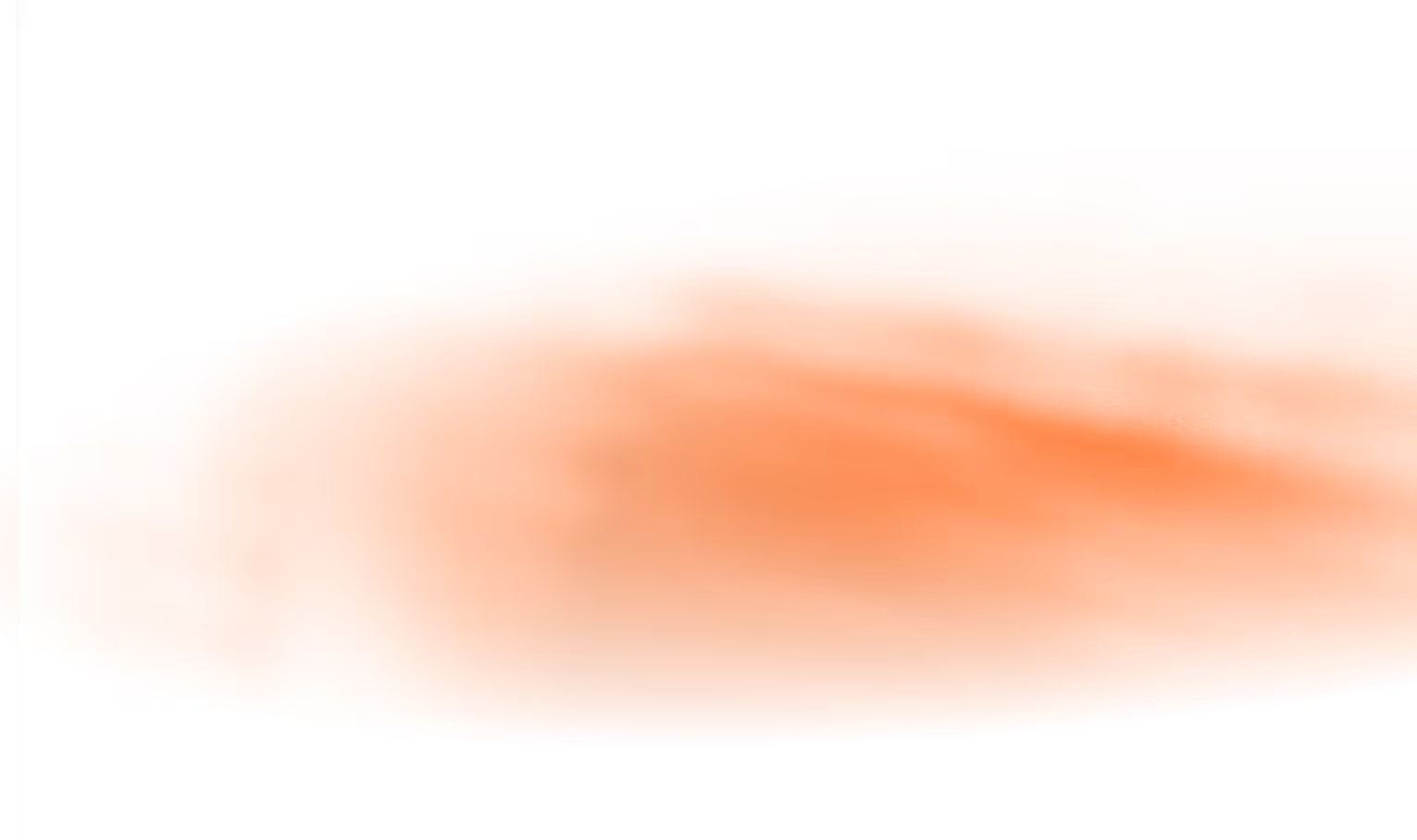
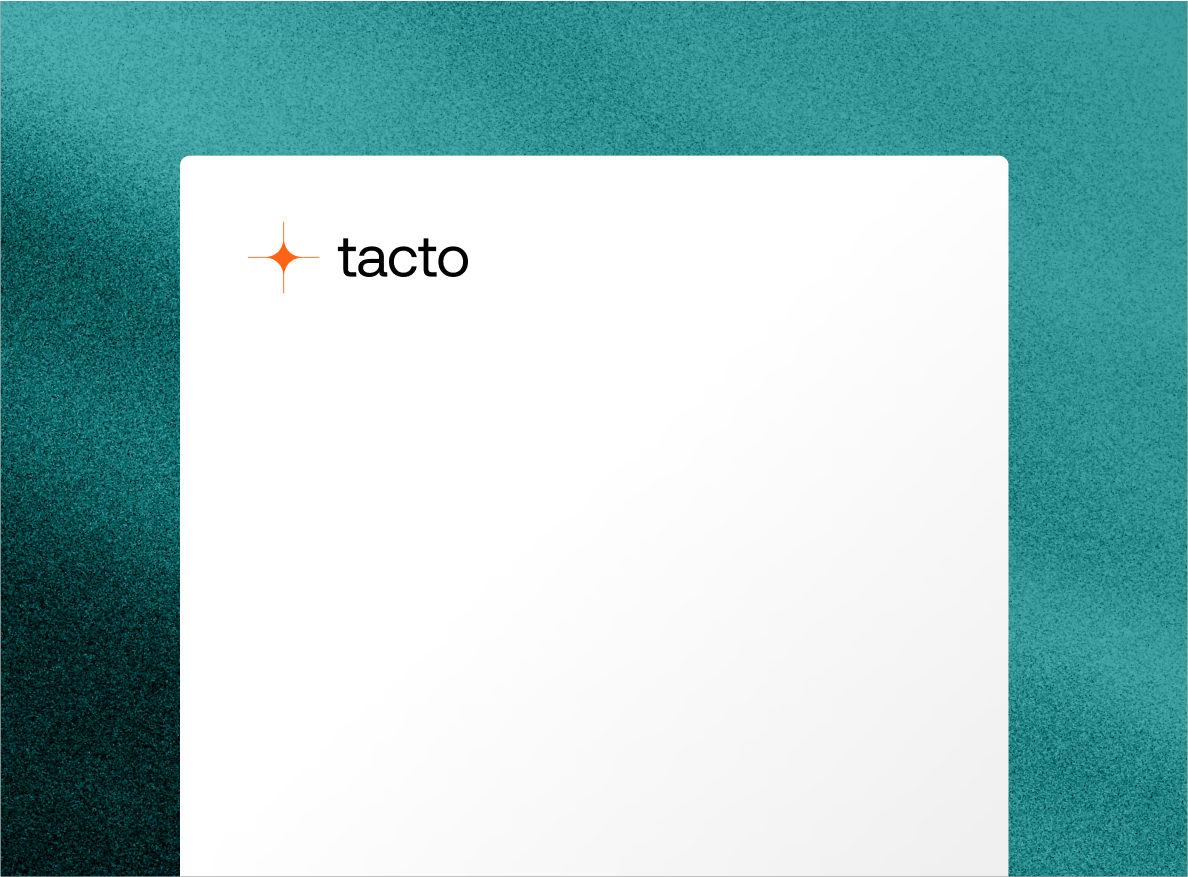