Procurement Glossary
Deviation analysis: definition and important aspects for buyers
Variance analysis systematically uncovers differences between target and actual values and thus enables targeted optimization of purchasing processes and cost structures. The following overview shows you how you can effectively use this important controlling tool in Procurement and thus achieve measurable cost savings.
Deviation analysis in a nutshell:
Variance analysis is a systematic comparison between target and actual values to identify and evaluate differences in key performance indicators. In Procurement , it enables the early detection of cost deviations, delivery delays and quality problems, allowing countermeasures to be initiated promptly.
Example: An automotive supplier discovers through monthly variance analyses that the actual material costs in the first quarter of 2023 are 12% above the planned budget of EUR 500,000, whereupon renegotiations are immediately initiated with the suppliers concerned.
Variance analysis: a key component of purchasing controlling
Variance analysis is a fundamental instrument of operational controlling and corporate management. It is used to systematically examine and evaluate differences between planned target values and actual values actually achieved. As an important control instrument, variance analysis enables the early recognition of deviations from plan and thus forms the basis for corrective measures in day-to-day business. This guide takes a closer look at the various aspects of variance analysis, its methods and areas of application, as well as its importance for successful corporate management.
What is variance analysis?
Variance analysis is a methodical tool for identifying and investigating differences between planned and actual results. In Procurement , it refers to the comparison of budgeted procurement costs, delivery dates or quality standards with the realized values. The aim is to identify the causes of deviations and initiate suitable measures for correction or improvement.
Core elements of the variance analysis
Importance of variance analysis in Procurement
In the purchasing process, variance analysis helps to increase the efficiency and effectiveness of procurement activities. By identifying deviations at an early stage, risks can be minimized and opportunities exploited. It supports purchasers in ensuring cost control, optimizing supplier relationship management and ensuring compliance with quality standards.
Deviation analysis: from manual checks to predictive analytics
Building on the fundamental importance of variance analysis in Procurement it becomes clear how crucial it is for identifying process inefficiencies and strategic adjustments. Traditionally, variances have been recorded and analyzed manually, which can be time-consuming and error-prone. With the increasing complexity of procurement logistics, there is a growing need for more accurate and efficient methods to identify and resolve deviations in real time.
Old: Manual variance analysis
Traditional approach: In traditional procurement processes, variance analysis was often carried out manually. Data from various sources such as purchase orders, delivery bills and invoices were merged and compared manually. This process was time-consuming and relied heavily on the accuracy of manual data entry. Incorrect or incomplete data led to unreliable results. In addition, this approach often only allowed a retrospective view, making it difficult to take proactive measures to reduce process costs.
New: Predictive analytics
Predictive analytics: The modern approach uses advanced data analysis technologies and artificial intelligence to identify deviations in real time and predict future trends. By integrating ERP systems and big data, large volumes of data are analyzed automatically. Algorithms recognize patterns and anomalies that indicate potential problems. This enables the proactive management of procurement processes and the early initiation of measures. In addition, interactive dashboards provide a comprehensive overview and facilitate well-founded decisions, leading to a significant increase in efficiency.
Practical example: Automotive industry
A leading automotive manufacturer implemented predictive analytics in Procurement in order to minimize risk management minimize risk. Real-time analysis of supplier data enabled potential bottlenecks to be identified at an early stage. Within six months, on-time delivery improved by 25% and inventory costs were reduced by 15%. In addition, quality deviations were reduced by 30% as anomalies were immediately identified and addressed.
Conclusion on the variance analysis
Variance analysis is an indispensable tool in modern Procurement that contributes to the optimization of procurement processes by systematically recording and evaluating planned and actual values. It not only enables the early detection of cost deviations, but also forms the basis for strategic decisions in supplier management. With increasing digitalization and AI integration, variance analysis is evolving from a reactive control instrument to a proactive management tool that helps companies minimize risks and sustainably improve purchasing processes.
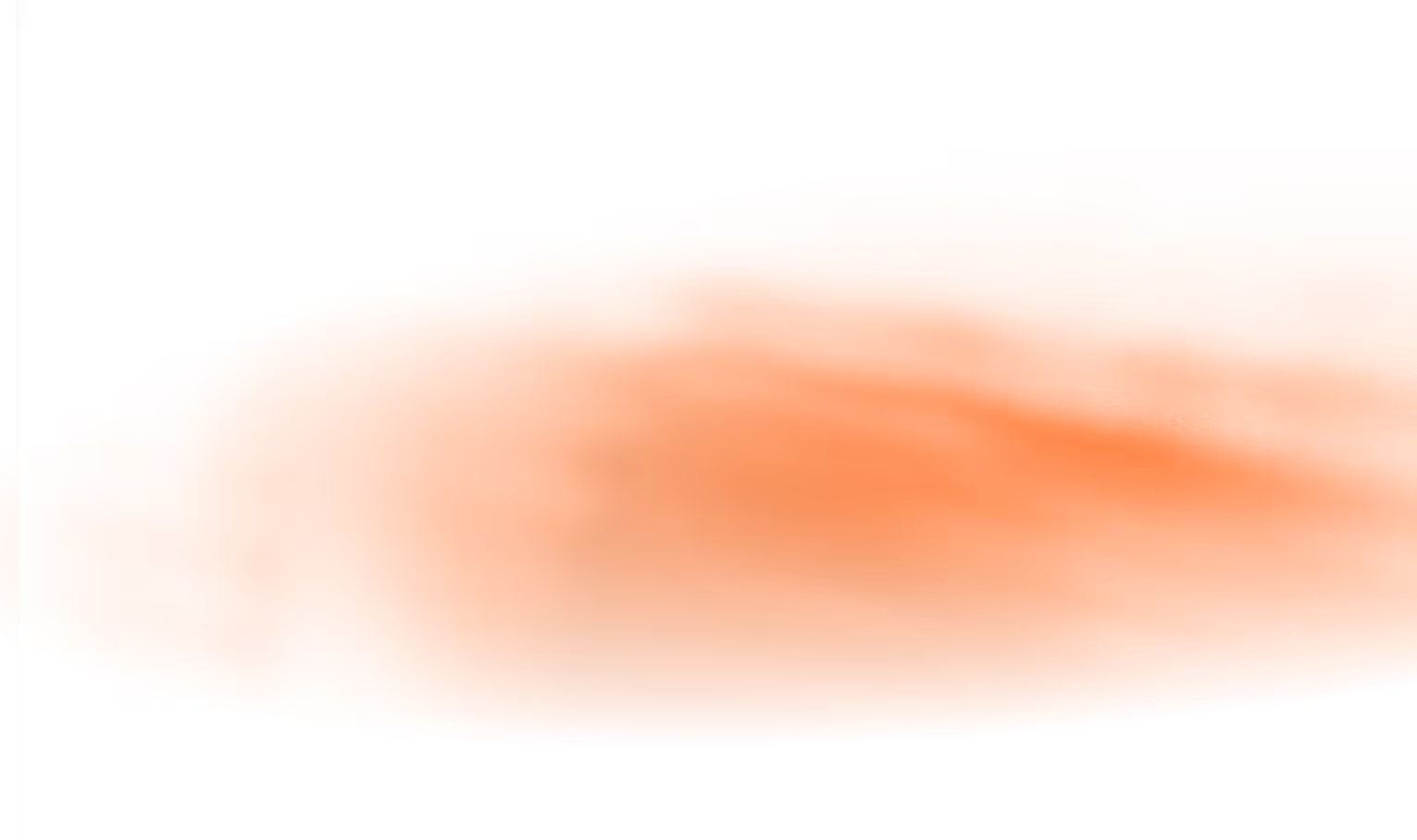
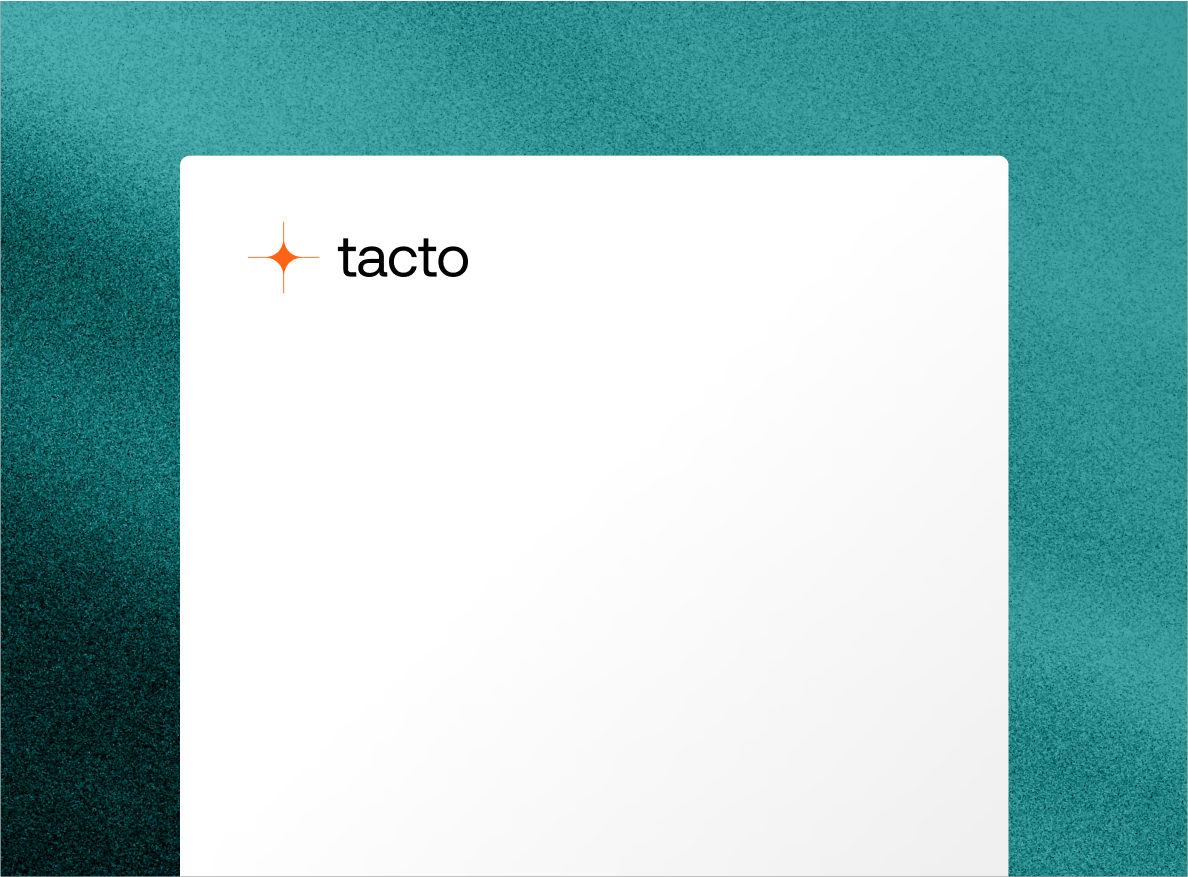