Procurement Glossary
Delivery quality: definition & important aspects for buyers
Delivery quality is a decisive factor for smooth processes and economic success throughout the entire supply chain. This structured overview shows you as a buyer how you can systematically optimize and measurably improve the quality of goods delivery.
Delivery quality in a nutshell:
Delivery quality describes the degree of conformity between agreed and actually delivered specifications in terms of quantity, time, condition and documentation of a delivery. For Procurement , it is a key performance indicator for evaluating and managing suppliers and ensuring smooth production and logistics processes.
Download our guide and you will find a strategy for optimizing delivery quality as well as detailed explanations of important key figures, formulas and reports.
Delivery quality - An introduction
Delivery quality is a decisive factor in modern logistics and supply chain management. It describes the quality and reliability with which goods or materials are transported and handed over from the supplier to the recipient. High delivery quality is of strategic importance for companies, as it has a direct impact on production processes, customer satisfaction and cost efficiency. In this guide, we look at the various aspects of delivery quality, its measurement and optimization, as well as the most important factors influencing the successful implementation of quality standards in delivery.
What is delivery quality?
Delivery quality refers to the condition and conformity of goods or materials that a supplier delivers to a company. It includes all aspects that ensure that the delivered products meet the agreed specifications, are free of defects and arrive on time. High delivery quality is crucial for a smooth production process and helps to avoid costs for reworking or complaints.
Core elements of delivery quality
Significance for Procurement
Delivery quality plays a central role in Procurement , as it has a direct impact on the efficiency of the value chain and end customer satisfaction. Consistent delivery quality makes it possible to avoid production interruptions, optimally manage stock levels and reduce costs through reworking or replacement purchases.
Delivery quality: from manual checks to digital inspection systems
Delivery quality is crucial for an efficient production process and customer satisfaction. Based on its theoretical importance, it is essential in practice to ensure that delivered goods meet the agreed quality standards. However, traditional methods reach their limits as they are often inefficient and prone to errors. Therefore, there is an urgent need for a transformation towards modern approaches that meet the increasing requirements.
Old: Manual incoming goods inspection
Traditional approach:
In the traditional delivery quality process, incoming goods were checked manually by warehouse staff. This included visual inspection for damage, manual counting of quantities and reconciliation of delivery bills with orders. Tools such as checklists and paper forms supported the process. Despite its simplicity, this approach had significant disadvantages: It was time-consuming, labor-intensive and prone to human error. It also often lacked systematic data collection, which made it difficult to track quality issues and limited the ability to evaluate suppliers.
New: Digital delivery quality check
Digital Inbound Inspection:
The modern approach revolutionizes delivery quality through the use of digital technologies. Automated systems record data on the quantity, quality and specifications of the delivered goods in real time. RFID tags and barcode scanners enable fast and error-free identification and quantity checks. Sensors and IoT devices check quality automatically and precisely. The integration of this data into the ERP system ensures seamless documentation and enables immediate analysis. AI-supported algorithms enable patterns to be recognized and proactive measures to be taken. This leads to a significant increase in efficiency, a reduction in error rates and improved transparency in the supply chain.
Practical example: Automotive supplier focuses on digitalization
A leading automotive supplier implemented a digital delivery quality check to optimize its processes. By using RFID technology and automated inspection stations, it was possible to reduce the time required for the incoming goods inspection reduced by 50%. The error rate dropped by 30% as human error was minimized. In addition, real-time data processing enabled a faster response to quality issues, which led to a 20% reduction in production downtime. Overall, digitization resulted in cost savings of 1.5 million euros per year and significantly increased both customer and employee satisfaction.
Conclusion on delivery quality
Delivery quality is a decisive success factor for a company's entire value chain. Systematic checks, standardized processes and close cooperation with suppliers can minimize production downtime and reduce costs. The increasing digitalization of quality control offers new opportunities for more efficient inspection processes and preventive quality management. Companies that invest in high delivery quality secure long-term competitive advantages and increase their customer satisfaction.
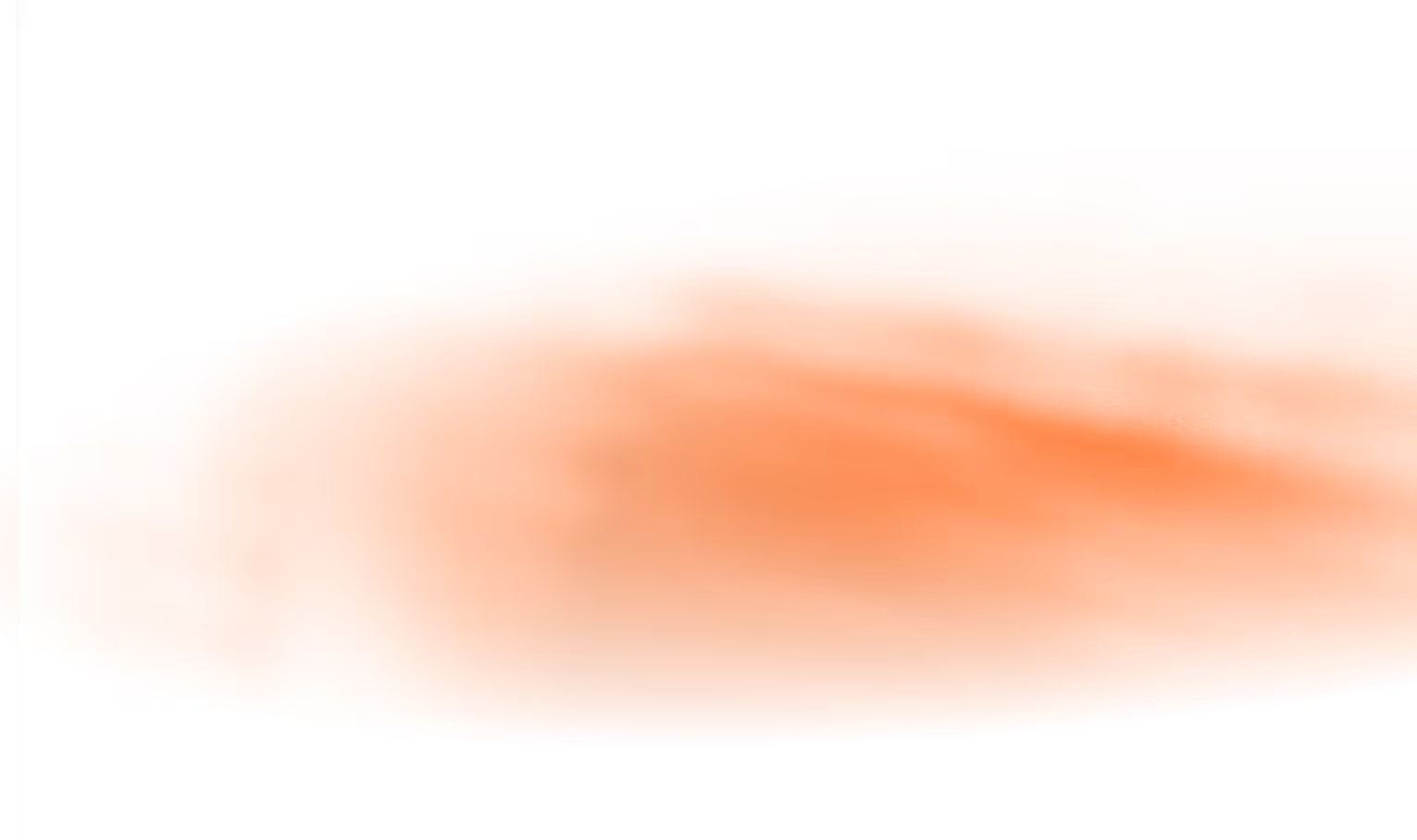
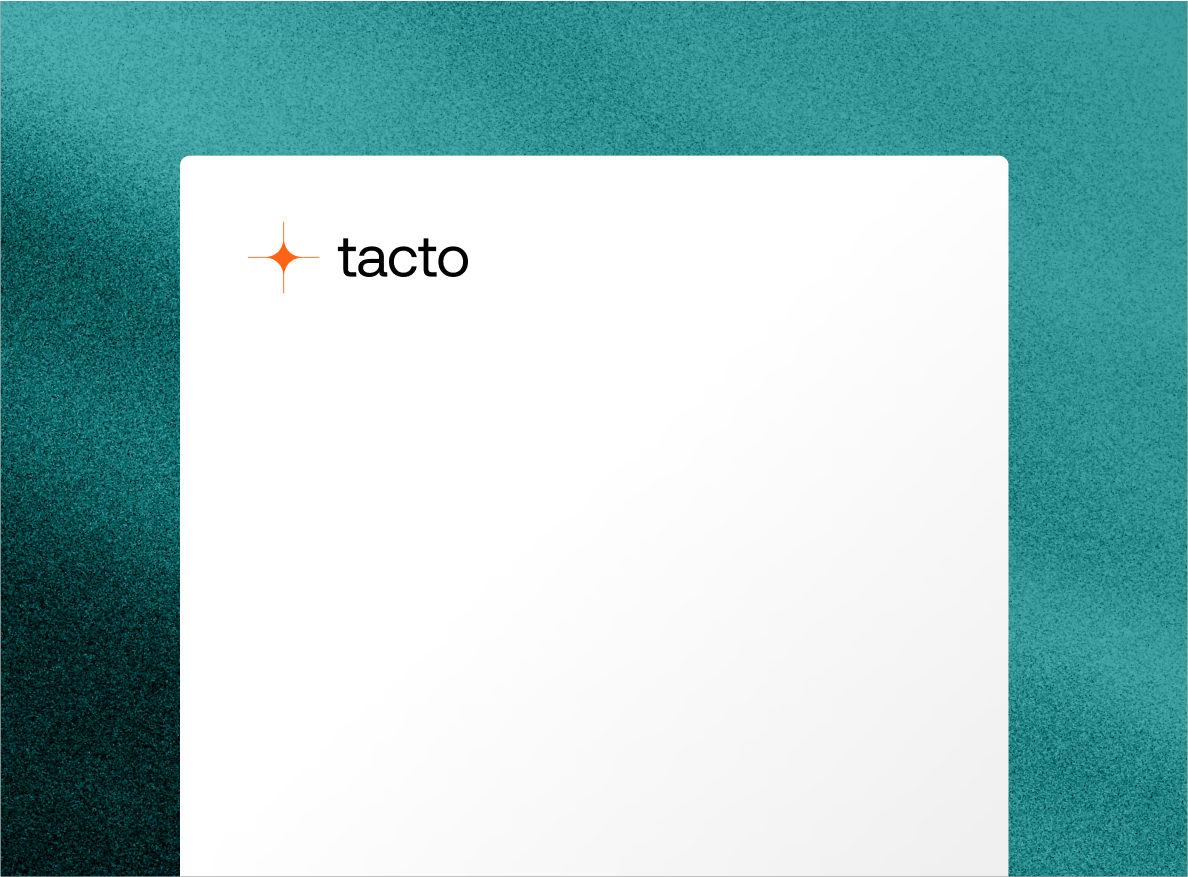