Procurement Glossary
Procurement controlling: definition and important aspects for buyers
Procurement controlling helps companies to systematically plan, manage and optimize their purchasing activities - an indispensable tool for sustainable business success. This structured overview shows you the most important methods and key figures with which you can make the performance of your purchasing measurable and continuously improve it.
Procurement controlling in a nutshell:
Procurement controlling is the systematic planning, management and control of all procurement-related activities based on defined key figures and target values. For Procurement , it enables fact-based decision-making and the continuous optimization of procurement processes and costs.
Example: An automotive supplier implements a monthly procurement controlling dashboard that makes supplier performance (98% delivery reliability), purchasing volume (EUR 2.3 million), inventory range (23 days) and realized savings (EUR 185,000) transparent and shows deviations from the target values.
Introduction to procurement controlling
Procurement controlling is an essential part of modern corporate management and is becoming increasingly important in times of global supply chains and rising material costs. It encompasses all activities for the systematic planning, management and control of a company's procurement processes. The strategic orientation of procurement controlling not only optimizes costs, but also ensures security of supply and minimizes risks. This guide highlights the most important aspects of procurement controlling, from basic concepts and key performance indicators to modern instruments and methods of procurement optimization.
What is procurement controlling?
Procurement controlling refers to the process of planning, managing and controlling all procurement-related activities within a company. It is an essential part of strategic purchasing and aims to increase the efficiency of purchasing processes, reduce costs and ensure security of supply. By applying controlling methods, data is collected and analyzed in order to make well-founded decisions and continuously improve the performance of purchasing.
Core elements of procurement controlling
Significance for modern Procurement
In today's competitive environment, procurement controlling is indispensable for an effective purchasing organization. It enables transparency regarding costs, supplier performance and procurement risks. Targeted controlling enables companies to identify potential savings, optimize processes and support strategic decisions.
Procurement controlling: from manual reporting to digital real-time controlling
Building on the theoretical basis of procurement controlling as a central instrument in purchasing controlling, practical implementation is becoming increasingly important. In a globalized economy, it is crucial to design procurement processes efficiently in order to reduce costs and secure competitive advantages. Traditional methods are reaching their limits here, which is why a shift towards modern, digital approaches is necessary in order to meet the increasing requirements.
Old: Manual procurement controlling
Traditional approach: In practice, traditional procurement controlling often meant a high level of manual effort. Data was recorded in different systems or even in paper form and then consolidated manually. Reports and analyses were usually created with a time delay and were based on historical data, which made proactive management difficult. The lack of system integration led to isolated islands of information, making it almost impossible to gain a holistic overview of procurement costs and performance. In addition, error rates were high due to manual data entry, and adjustments to market changes were slow.
New: Digital real-time procurement controlling
Real-time procurement analytics: Modern implementations rely on digital technologies and enable real-time procurement controlling. By using integrated ERP systems and specialized analytics tools, data is automatically collected and made available immediately. Artificial intelligence and machine learning are used to recognize patterns and create forecasts. This enables proactive management of procurement processes and a rapid response to market analysis. Decisions are based on up-to-date data, which increases efficiency and reduces costs. Practical benefits include up to 25% faster order turnaround times and a 40% improvement in data quality thanks to automated processes.
Practical example: Transformation at Müller Technik AG
Müller Technik AG, a leading plant engineering company, was faced with the challenge of modernizing its procurement processes. By implementing a digital real-time procurement controlling system, the company was able to achieve significant improvements within a year. Automated data collection reduced manual effort by 35% and the use of predictive analytics cut procurement costs by 15%. With the introduction of a dashboard, decision-makers had access to current key figures at all times, which significantly improved strategic planning. Overall, the transformation led to a 20% increase in process speed and made a significant contribution to increasing competitiveness.
Conclusion on supplier evaluation
Procurement controlling is an indispensable tool of modern purchasing that optimizes the efficiency of procurement processes through systematic planning, management and control. The integration of digital technologies and AI-supported analyses not only enables cost savings, but also supports strategic decisions. The success of procurement controlling depends largely on the quality of the database, standardized processes and the consistent implementation of the insights gained. Only by continuously developing these components can procurement controlling sustainably increase its contribution to value creation in the company.
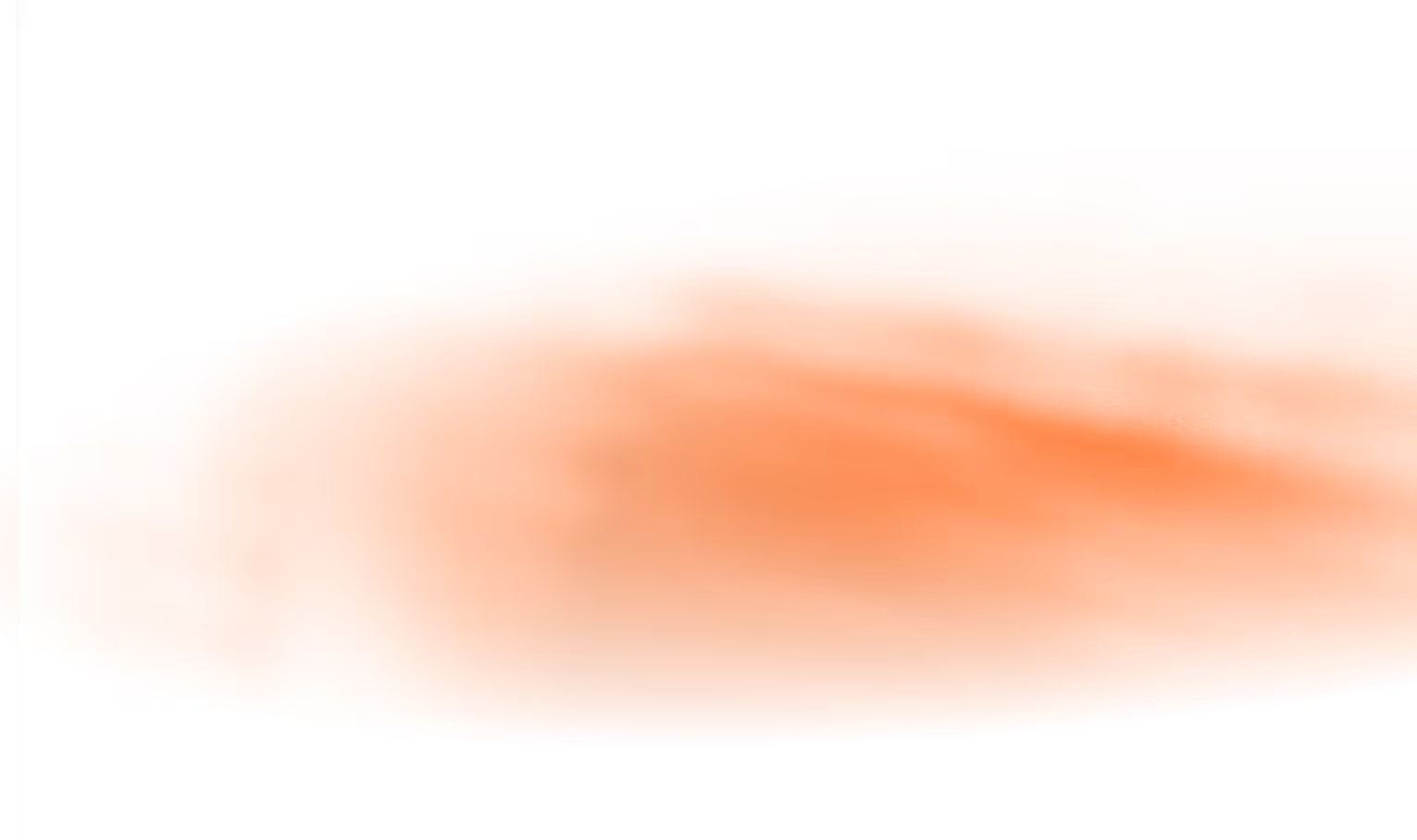
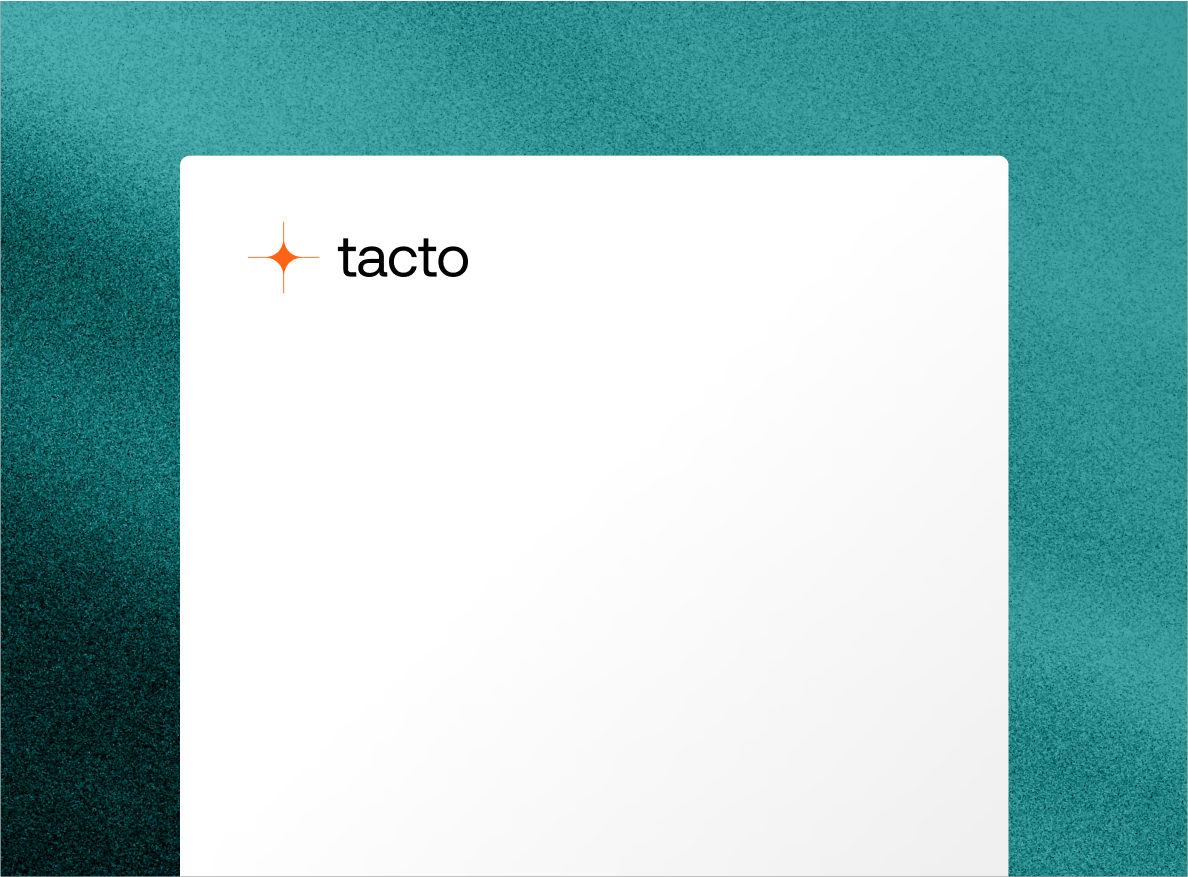