Procurement Glossary
Purchasing controlling: definition & important aspects
Purchasing controlling provides management with the key performance indicators and control instruments for efficient and value-adding Procurement. This structured overview shows you the most important methods and tools with which you can systematically optimize the performance of your procurement and make it measurable.
Purchasing controlling in a nutshell:
Procurement controlling is the systematic planning, management and control of all procurement-related activities based on defined key figures and processes. It enables Procurement to identify potential savings, measure process efficiency and make strategic decisions based on sound data.
Example: An automotive supplier implements a monthly purchasing controlling dashboard that demonstrates savings of EUR 2.3 million in the first half of 2023 by monitoring supplier prices, order quantities and process costs and leads to the optimization of the Categories 10 categories.
Introduction to purchasing controlling
Purchasing controlling is a central component of purchasing management in companies. It encompasses the planning, management and control of purchasing activities in order to increase the efficiency and effectiveness of purchasing. Well-implemented purchasing controlling helps to reduce costs, minimize risks and improve supplier relationships. In this guide, you will learn everything you need to know about purchasing controlling, from basic definitions to practical applications and best practices.
What is purchasing controlling?
Purchasing controlling refers to the systematic planning, management and monitoring of purchasing activities within a company. The aim is to make purchasing processes efficient, optimize costs and ensure the quality of purchased products and services. Purchasing controlling comprises various tasks, including the analysis of key purchasing figures, risk management, supplier management and cost control.
Why is purchasing controlling important?
Purchasing controlling offers numerous advantages for companies:
Increased efficiency: By systematically analyzing and optimizing purchasing processes, companies can save time and resources.
Cost control: Purchasing controlling helps to monitor and reduce purchasing costs by identifying and exploiting potential savings.
Risk management: Identification and minimization of risks that can occur in Procurement , such as supplier defaults or price fluctuations.
Improved supplier relationships: Long-term and trusting relationships with suppliers can be established through structured and transparent communication.
Strategic decision-making: Purchasing controlling provides important data and key figures that are necessary for well-founded decisions in Procurement .
Key figures in purchasing controlling
Various key figures are used in purchasing controlling to measure and manage performance. The most important of these include
- Purchasing costs: Total costs incurred for the Procurement goods and services.
- Cost per unit: Average cost per unit ordered, which helps to monitor price developments.
- Supplier evaluation: Evaluation of the performance and reliability of suppliers based on criteria such as delivery time, quality and price.
- Savings potential: Identification of areas where costs can be saved, for example through negotiations or alternative procurement sources.
- Average order quantity: Analysis of order quantities to optimize order cycles and reduce storage costs.
- Stock turnover: The number of times stock is completely sold and replaced within a certain period of time.
Methods and strategies in purchasing controlling
Buyers use various methods and strategies to effectively manage and optimize purchasing processes:
SWOT analysis
The SWOT analysis (strengths, weaknesses, opportunities, threats) helps to identify the internal and external factors that influence Procurement . This analysis supports the development of strategies to exploit strengths and opportunities and to minimize weaknesses and risks.
Benchmarking
By comparing your own purchasing processes and key figures with those of best-in-class companies, you can identify potential for improvement and adopt best practices.
Total Cost of Ownership (TCO)
The TCO (Total Cost of Ownership) method considers not only the acquisition costs, but all costs incurred over the entire life cycle of a product or service. This includes, for example, maintenance costs, operating costs and disposal costs.
Supplier management
Effective supplier management is crucial for purchasing controlling. This includes the selection, evaluation and development of suppliers as well as the maintenance of long-term partnerships.
Procurement controlling: From traditional controlling to data-driven procurement
Procurement controlling is a key instrument for increasing the effectiveness and efficiency of procurement processes. Based on the theoretical foundation, it forms the basis for strategic decisions in Procurement. In practice, it enables companies to gain transparency regarding expenditure and supplier evaluation and thus achieve competitive advantages. The transformation from the traditional approach to modern, data-driven methods is necessary in order to meet the increasing demands for speed and accuracy.
Old: Traditional purchasing controlling
Traditional approach: In traditional purchasing controlling, data is recorded manually and analyzed at regular intervals. Typically, simple tools such as spreadsheets are used to analyze spend by commodity group management and supplier. The reports are retrospective and offer little flexibility for ad hoc analyses. The main focus is on cost control and budgeting compliance. This approach is time-consuming and prone to errors. In addition, there is often a lack of up-to-date information, which leads to delayed reactions to market changes and leaves potential savings untapped.
New: Data-driven procurement
Data-driven procurement: The modern approach to procurement controlling uses advanced technologies such as big data, artificial intelligence and machine learning. The integration of real-time data from ERP systems, supplier portals and external market data creates a comprehensive picture of the procurement situation. Predictive analytics makes it possible to forecast price trends and supplier risks. Dashboards provide interactive visualizations that allow complex data to be interpreted quickly. This data-driven approach leads to more informed decisions, faster response times and sustainable cost savings.
Practical example: Digitalization in mechanical engineering
A medium-sized mechanical engineering company implemented data-driven procurement to optimize its purchasing processes. By introducing a cloud-based analysis system, procurement costs were reduced by 12% within 12 months. Real-time data enabled a better negotiating position with suppliers, as price developments were recognized at an early stage. In addition, the supplier base was consolidated by 15%, which led to more efficient processes. The automated evaluation of quality indicators led to a 20% reduction in complaints. Overall, the company achieved a significant increase in efficiency and improved its market position thanks to the modern approach to purchasing controlling.
Conclusion
Purchasing controlling is an essential part of the procurement process for buyers. Well-implemented purchasing controlling makes a significant contribution to increasing efficiency, controlling costs and strengthening business relationships with suppliers. By systematically planning, managing and controlling purchasing activities, companies can ensure that their purchasing processes run smoothly and in line with the company's objectives.
The use of patterns and templates facilitates the development of a consistent and professional purchasing controlling strategy. In addition, technological solutions are playing an increasingly important role in the automation and optimization of the purchasing process. Regular reviews and adjustments to purchasing controlling ensure that it is always in line with current market conditions and company requirements.
Invest in the development and optimization of your purchasing controlling to secure long-term competitive advantages. A well-structured purchasing process not only promotes efficiency and transparency, but also the satisfaction of your suppliers and customers. With the right strategies and tools, you can lay the foundations for successful and sustainable business transactions.
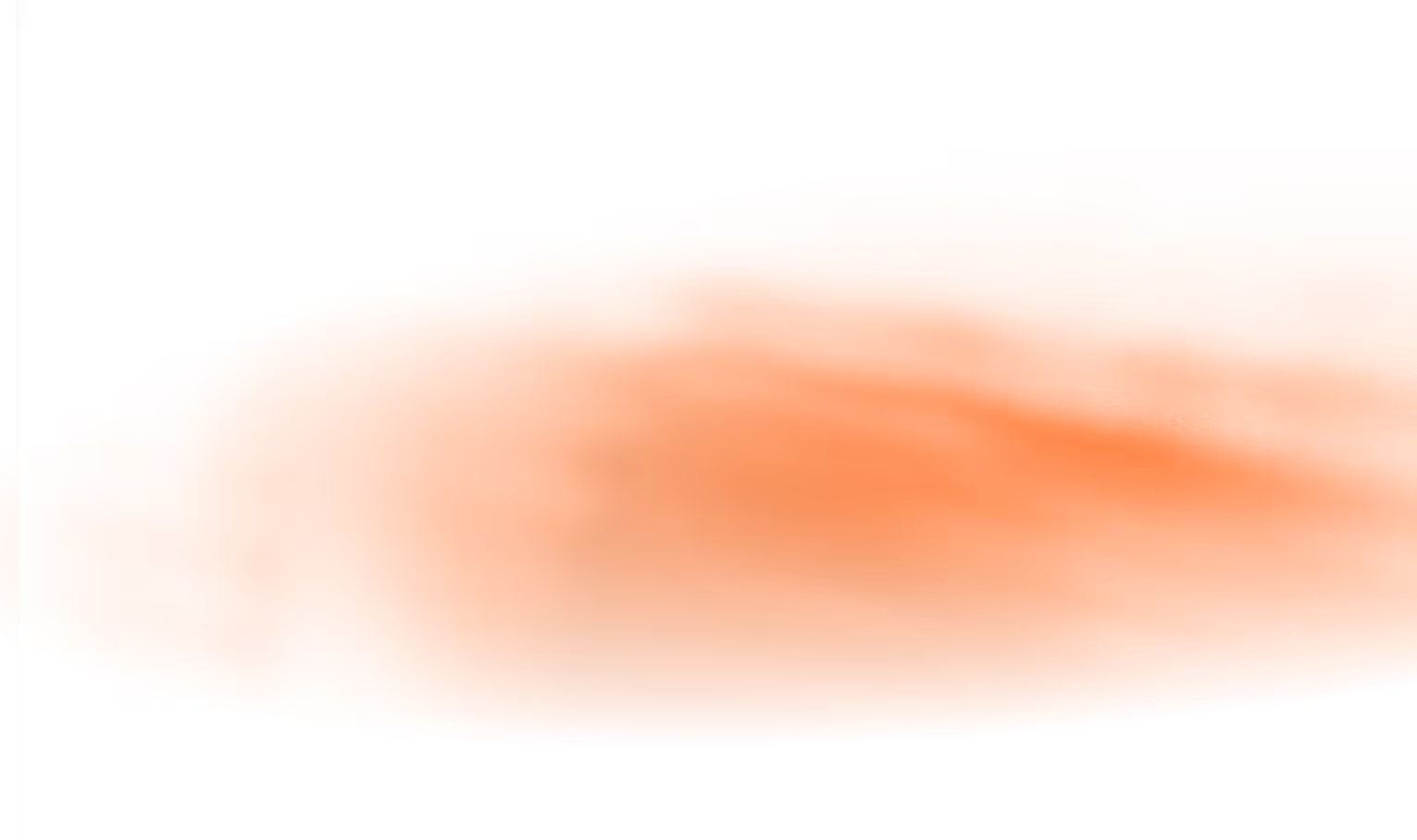
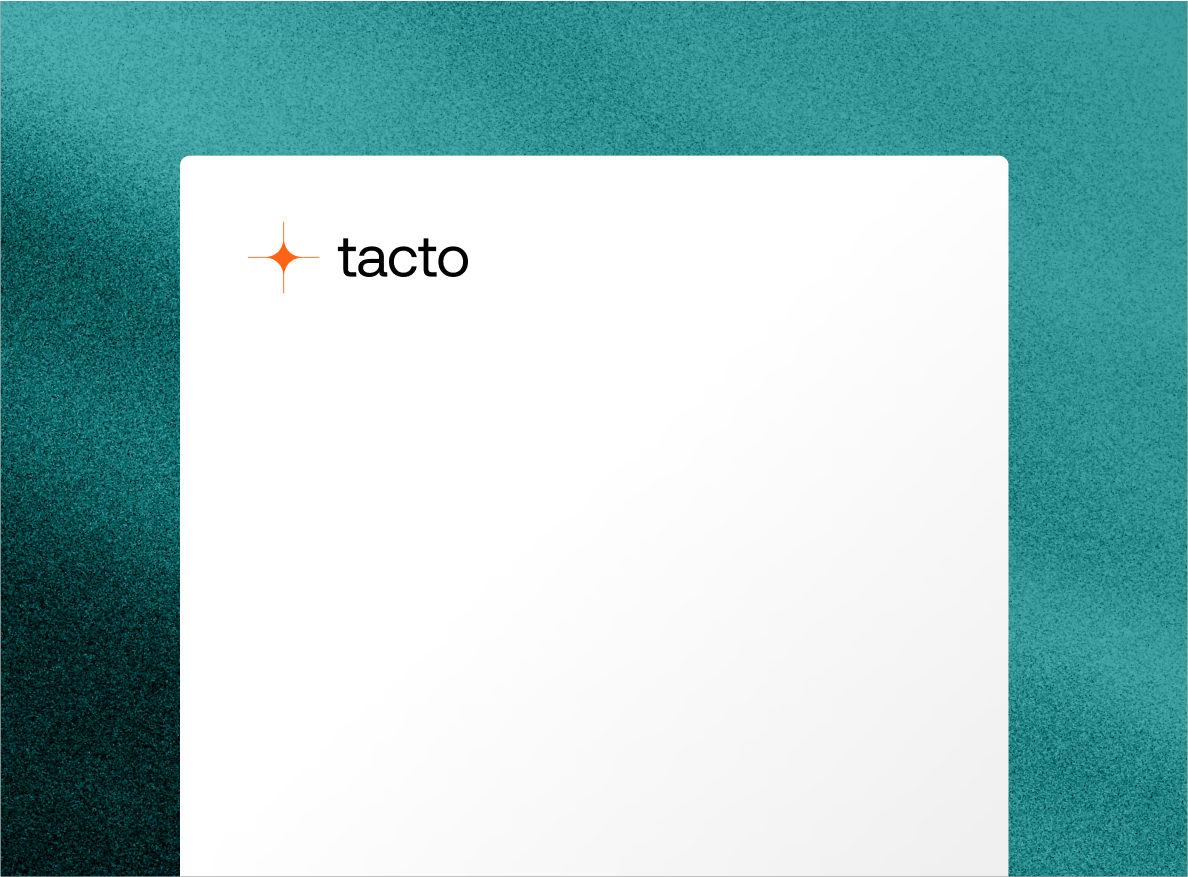