Procurement Glossary
Supplier portal: definition and important aspects for buyers
A supplier portal revolutionizes the collaboration between purchasing organizations and their suppliers through digital processes and central data management. This structured overview shows you how you can use a supplier portal to optimize your procurement processes and take supplier relationships to a new level.
Supplier portal in a nutshell:
A supplier portal is a web-based platform that serves as a central digital interface between companies and their suppliers. For Procurement , it enables the automated handling of processes such as orders, invoicing and document exchange, which leads to increased transparency and reduced process costs.
Example: A car manufacturer implements a supplier portal through which 500 suppliers post their delivery notifications, upload quality documents and submit invoices digitally every day, reducing the process costs per transaction from 15 to 3 euros.
Introduction to the supplier portal
A supplier portal is a digital platform that serves as a central interface between companies and their suppliers. In the increasingly digitalized business world, the supplier portal has established itself as an indispensable tool for efficient supplier management. It enables transparent, fast and effective communication as well as the structured exchange of documents and information. The integration of various processes such as order processing, quality management and invoicing in a single platform optimizes workflows and minimizes sources of error. In this guide, you will learn about the benefits of a supplier portal and how you can successfully implement it in your company.
What is a supplier portal?
A supplier portal is a web-based platform that serves as a central interface between a company and its suppliers. It enables the exchange of information, documents and data in real time and thus promotes more efficient and transparent collaboration. By integrating it into the internal purchasing systems, processes such as order management, supplier evaluation and communication can be digitized and automated.
Core elements of a supplier portal
- Supplier registration and qualification: digital onboarding process for new suppliers including document management
- Order and order management: access to orders, call-offs and order confirmations in real time
- Communication and collaboration: direct exchange via messages, notifications and shared calendars
- Performance monitoring: Insights into key figures on delivery punctuality, quality and compliance
Significance for modern Procurement
For Procurement , the supplier portal plays a decisive role in the digitalization and optimization of procurement processes. It enables improved collaboration with suppliers, reduces administrative effort and increases transparency along the supply chain. The central platform enables procurement departments to work more efficiently, minimize risks and save costs.
- Increased efficiency: automation of routine tasks and reduction of manual processes
- Improved supplier relationships: Transparent communication and faster response times
- Risk minimization: up-to-date information on supplier performance and compliance
Supplier portal: from manual communication to digital networking
Building on the theoretical importance of the supplier portal as a central digital platform for networking between companies and their supplier management, its practical implementation is becoming increasingly relevant. In a globalized economy where speed and efficiency are crucial, traditional communication channels are reaching their limits. The need for a transformation to digital solutions is evident in order to optimize processes and remain competitive.
Old: Manual supplier communication
Traditional approach: In traditional procurement processes, communication with suppliers was mainly via telephone, fax and e-mail. Orders were created manually and sent by fax, while order confirmations and shipping notifications were often obtained by telephone. These manual processes were time-consuming and prone to errors such as incorrect entries or transmission losses. There was also a lack of transparency and real-time information, which led to delays in the supply chain. The lack of system integration made it difficult to track orders and required a great deal of administrative effort.
New: Supplier Portal
Supplier Portal: These challenges have been overcome with the introduction of modern supplier portals. The digital platform allows companies and their suppliers to communicate directly and in real time. Orders are transmitted electronically and automatic notifications provide information on status changes. The integration of ERP systems enables seamless data exchange without media disruptions. Important documents such as contracts or quality assurance agreements are provided centrally. This innovative approach increases efficiency, reduces error rates by up to 60% and significantly shortens throughput times. It also promotes transparency and strengthens the strategic partnership with suppliers.
Practical example: Automotive supplier
A medium-sized automotive supplier implemented a supplier portal to digitize its procurement processes. By connecting over 150 suppliers to the portal, orders, shipping notifications and invoices could be processed electronically. Within the first year, the average processing time per order fell from 30 to 10 minutes. The error rate for orders was reduced by 70% and stock levels were reduced by 20% thanks to better planning. This led to cost savings of over 500,000 euros per year and strengthened the company's competitiveness in the long term.
Conclusion on supplier evaluation
Supplier portals are indispensable digital tools for modern companies that want to optimize their procurement processes. They not only increase efficiency through automated processes and improved communication, but also create more transparency in the supply chain. Successful implementation requires careful planning and change management, but pays off through reduced costs, minimized risks and strengthened supplier relationships. With a view to future developments such as AI and blockchain, supplier portals will continue to gain in strategic importance.
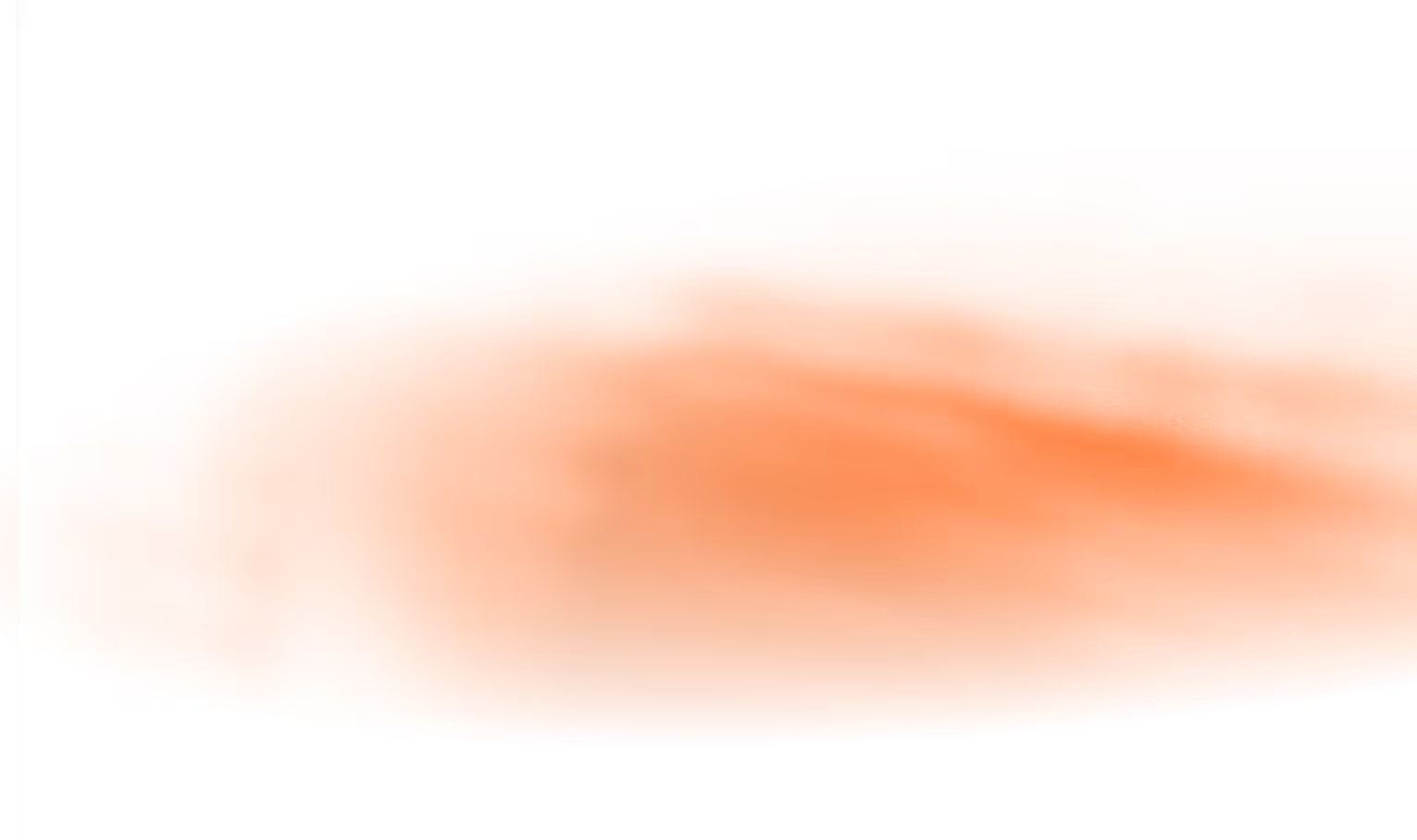
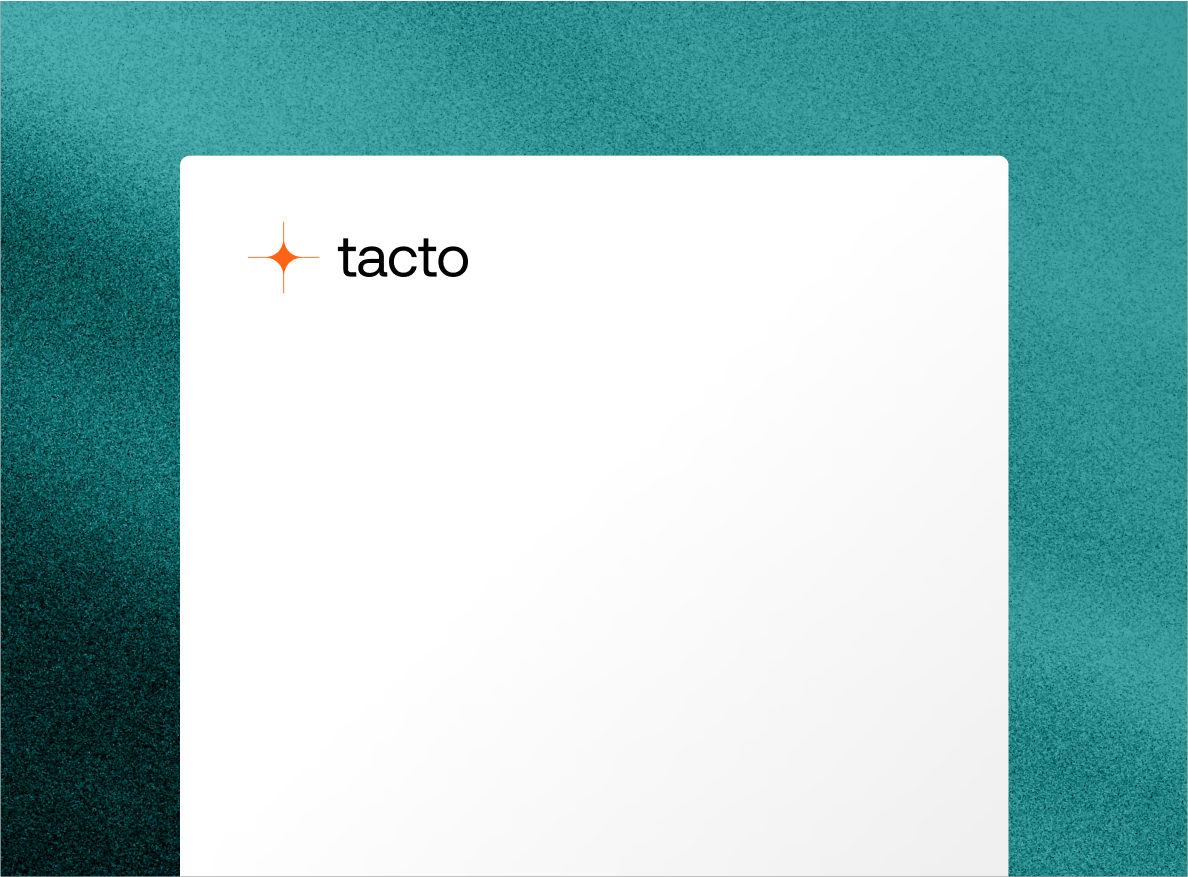